Tiefdruckverfahren
Das Tiefdruckverfahren ist eine Drucktechnik, bei der die abzubildenden Elemente als Vertiefungen in der Druckform vorliegen. Die gesamte Druckform wird vor dem Druck eingefärbt und die überschüssige Farbe danach mit einer Rakel oder einem Wischer entfernt, so dass sich die Druckfarbe nur noch in den Vertiefungen befindet. Ein hoher Anpressdruck und die Adhäsionskräfte zwischen Papier und Farbe bewirken die Farbübertragung. Das Verfahren wird sowohl im gewerblichen Tiefdruck als auch im künstlerischen Bereich eingesetzt.[1]
Die Tiefdruckform wird vor allem im Verpackungs-, Etiketten-, Dekor- und im Zeitschriftendruck eingesetzt. Die Lasergravur in Kombination mit dem Ätzprozess findet im Verpackungsdruck Anwendung.
Rakeltiefdruck
Im industriellen Bereich wird ausschließlich der Rakeltiefdruck eingesetzt. Die Druckformen im Rakeltiefdruck bestehen nicht aus Druckplatten, sondern aus Stahlzylindern. Bei einem Vierfarbendruck werden vier separate Druckzylinder pro Auftrag eingesetzt. Diese Tiefdruckzylinder besitzen formatbedingt ein beträchtliches Gewicht und müssen mit speziellen Transportsystemen ausgewechselt werden.[1]
Druckformherstellung
Die Druckformherstellung im Rakeltiefdruck unterlag im Verlauf der technischen Entwicklung erheblichen Veränderungen. Es gibt vorwiegend zwei Arten des Zylinderaufbaus. Den Stahlzylinder ummantelt eine rund 2 mm starke Kupferschicht, die Grundkupfer genannt wird. Auf diese innere Kupferschicht wird entweder gravierfähiges Kupfer in einer Schichtstärke von etwa 100 μm galvanisiert oder eine so genannte abziehbare Ballardhaut wird auf das Grundkupfer galvanisch aufgebracht. Zwischen dieser 100 μm dünnen Ballardhaut und dem Grundkupfer liegt eine Trennschicht. Dadurch lässt sich die Ballardhaut nach dem Druck einfach entfernen und durch eine neue ersetzen.
Die Rasterung im Tiefdruck zerlegt das Druckbild in winzige druckende Formelemente, die Näpfchen genannt werden, während die nichtdruckenden Elemente Stege heißen. Die Stege sind erforderlich, damit die Rakel die überschüssige Farbe vom Zylinder abstreifen kann. Die Rakel besteht aus einem der Länge des Druckzylinders entsprechenden Stahllineal.[1]
Konventionelle Ätzung oder Heliogravüre
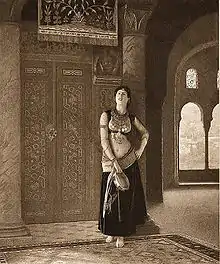
Als Erfinder der Heliogravüre gilt der Österreicher Karl Klietsch, der 1879 den Einsatz des Pigmentpapiers mit dem fotografischen Übertragungsprozess verband. Zunächst wurde von Kupferplatten gedruckt, bis die Verwendung von Schnellpressen im gewerblichen Bereich die Herstellung von Druckformzylindern erforderlich machte.[2]
Die konventionelle Ätzung des Druckzylinders, die bis Ende der 1970er Jahre praktiziert wurde, erfolgte über das Pigmentpapier. Auf das von einer lichtempfindlichen Chromgelatineschicht bedeckte Papier wird zunächst ein gleichmäßiger Raster kopiert. In einem zweiten Kopiervorgang belichtet man danach einen fotografischen Halbtonpositivfilm über den Raster. Danach wird das Pigmentpapier mit der Gelatineschicht auf den Druckzylinder geklebt. Mittels warmen Wassers wird das Papier vorsichtig gelöst und dann die unbelichtete Gelatine entfernt, bis auf dem Zylinder ein negatives, gerastertes Gelatinerelief zurückbleibt.[2]
Nun wird der Druckzylinder nacheinander in mehreren Säurebädern aus Eisenchlorid und Wasser geätzt, wobei mit dem Bad mit der höchsten Konzentration begonnen wird. In der äußeren Kupferschicht entstehen unterschiedlich tiefe, jedoch gleich große Näpfchen. Je tiefer das Näpfchen ist, umso mehr Farbe kann es aufnehmen und beim Druck entsteht ein entsprechend dunkler Ton. Man spricht hier vom „tiefenvariablen Tiefdruck“. Schließlich wird die restliche Gelatineschicht vom Zylinder abgewaschen und der Andruck kann erfolgen.[2]
Elektromechanische Gravur
Die elektromechanische Gravur zählt zu den konventionellen Verfahren und wird seit etwa 1960 bis heute vereinzelt eingesetzt. Die Firma Hell in Kiel brachte 1966 die erste elektronisch gesteuerte Graviermaschine auf den Markt, den „Helio-Klischograph“. Der Abtastzylinder und der zu gravierende Druckformzylinder sind über eine Welle miteinander verbunden. Auf dem Abtastzylinder befindet sich ein so genannter Opalfilm mit allen Bildinformationen, Texten und Strichzeichnungen. Entsprechend der Helligkeit des abgetasteten Bildpunktes auf dem Opalfilm wird eine adäquate Lichtmenge reflektiert und in ein elektrisches Signal umgewandelt. Dieses Ausgangssignal des Abtastkopfes der Graviermaschine wird im Rechner aufbereitet und dient zur Steuerung des Gravierkopfes, der zwei Informationen erhält: Erstens das eigentliche Bildsignal nebst Position sowie zweitens das Signal zur Definition der Rasterfeinheit und des Rasterwinkels. Ein Diamantstichel schneidet daraufhin ein entsprechend großes und tiefes Näpfchen physisch in die Kupferschicht des Druckzylinders.[3]
Anstelle eines Halbtondiapositivs als Opalfilm werden auch gerasterte Opalfilme als Graviervorlage eingesetzt. Eine wirtschaftliche Methode ist die Übernahme von Offsetfilmen, also Druckvorlagen, die zuvor aus Kostengründen im Offsetandruck eingesetzt wurden. Dieses Verfahren wird Offset-Tiefdruck-Konversion oder OT-Konversion genannt. Der Abtastkopf wird so eingestellt, dass die gerasterten Offsetfilme integral abgetastet und in entsprechende Halbtonwerte umgewandelt werden. Wichtigste Voraussetzung bei der OT-Konversion ist die Entrasterung der Vorlagen, da sonst auf dem gravierten Tiefdruckzylinder ein Moiré entstehen würde.[3]
Elektronische Gravur
Ab 1995 wird der Tiefdruckzylinder überwiegend direkt, ohne Umweg über einen Opalfilm, graviert. Die Signale für den Gravierkopf kommen aus dem digitalen Datenbestand zur Druckformbeschreibung. Heute wird zunehmend mit dem Laserstrahl graviert, der höhere Gravurgeschwindigkeiten ermöglicht. Je nach Verfahren wird eine Zinkoberfläche oder eine dickere Chromschicht statt des Kupfers graviert. Versuche mit einer Kunststoffbeschichtung hatten keinen Erfolg.
Grundsätzlich werden auch bei der Lasergravur Näpfchen in die Zylinderoberfläche gebrannt, die abhängig von der Stärke des elektronischen Signals ein entsprechend größeres oder kleineres Volumen aufweisen. Die hohe Schreibauflösung von bis zu 2540 dpi (= 100 Punkte pro Millimeter) ermöglicht eine sehr hohe Konturenschärfe. Darum ist die Laserdirektgravur besonders für den Druck von Etiketten und Verpackungen, typisch zum Beispiel für Zigaretten, geeignet.[1]
Ein weiteres elektronisches Verfahren zur Druckformherstellung ist der moderne Ätzprozess. Hier wird der Zylinder zuerst mit einer Lack- oder säurefesten Schicht überzogen, die anschließend mit einem Laser weggebrannt wird. Dadurch wird die Schicht an den Stellen entfernt, an denen die Näpfchen später erscheinen sollen. Die anschließende computerüberwachte Ätzung oder elektrolytische Kupferabtragung generiert die endgültigen Näpfchen.[1]
Gravierte Tiefdruckformen neigen zu so genannten Missing Dots, das bedeutet fehlende Rasterpunkte, da einige Näpfchen wegen ihrer Formgebung zu wenig Farbe aufs Papier übertragen. Anhand der Zahl der Missing dots wird von Fachleuten die Qualität der Tiefdruckprodukte beurteilt. Diesem Problem wird mit elektrostatischen Druckhilfen begegnet.[1]
Tiefdruckmaschinen
Das Druckwerk einer Tiefdruckmaschine besteht im Wesentlichen aus dem Druckzylinder, der Farbwanne, der Rakel, dem Presseur und dem Trocknungssystem und arbeitet wie folgt: Der Druckzylinder taucht in die dünnflüssige Druckfarbe in der Farbwanne ein. Die Näpfchen im Druckformzylinder werden völlig mit Farbe überflutet. Die Rakel entfernt die überschüssige Farbe, so dass sich nur in den Näpfchen Druckfarbe befindet, die Stege zwischen den Näpfchen jedoch farbfrei sind. Die überschüssige Farbe fließt in die Farbwanne zurück. Dann erfolgt der Druckvorgang. Der Presseur sorgt für einen hohen Anpressdruck, um die Farbe aus den Näpfchen fast vollständig auf den Bedruckstoff zu übertragen. Der Presseur wird im Tiefdruck eingesetzt, um den notwendigen mechanischen Druck für das Heraussaugen der Druckfarbe aus den Näpfchen des Druckformzylinders durch das Papier zu erzeugen. Dazu drückt der Presseur die Bedruckstoffbahn gegen den Formzylinder und sorgt für den Transport des Papiers durch das gesamte Druckwerk. Im Mehrfarbentiefdruck muss nach jedem Druckvorgang getrocknet werden, weil ein Nass-in-Nass-Druck bei den dünnflüssigen oder niedrigviskosen Tiefdruckfarben nicht möglich ist.[1]
Es gibt im Tiefdruck sowohl Rotationsmaschinen als auch Bogendruckmaschinen. Im Rotationsdruck werden vor allem auflagenstarke Produkte hergestellt. Ihre Druckleistung liegt aktuell bei 60.000 Drucken pro Stunde, das entspricht einer Papierbahngeschwindigkeit von rund 16 m/s. Der weniger verbreitete Bogentiefdruck wird vor allem beim Druck von Leuchtstofffarben, Metallfarben und Lacken (zum Beispiel Metallic-, UV-aktivierbare, grobpigmentöse Farben) als Sonderfarbe auf fertige Druckbögen aus dem Offsetdruck genutzt.
In Kombination mit dem Offsetdruck sind im Bogentiefdruck hochqualitative und optisch sehr ansprechende Druckergebnisse möglich. Anwendungen sind vor allem in der Zigarettenindustrie, aber auch bei Parfüm-, Kosmetikverpackungen, Displays sowie im Sicherheits- und Wertpapierdruck zu finden. Im Rotationstiefdruck werden ausgezeichnete Ergebnisse beim Illustrationsdruck erzielt. Ein im Tiefdruck reproduziertes Bild kommt der Originalvorlage sehr nahe.[1]
Merkmale des Tiefdrucks
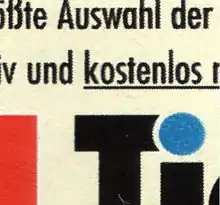
Wichtigstes Merkmal beim Tiefdrucken ist der Zackenrand oder Sägezahneffekt an Buchstaben und Strichzeichnungen, da nicht nur Bilder, sondern auch Texte und Strichzeichnungen gerastert werden. Beim tiefenvariablen Tiefdruck fallen unter der Lupe die gleich großen, quadratischen Rasterpunkte auf, die in den helleren Tonwerten häufig ausgehöhlt aussehen. Beim tiefen- und flächenvariablen Tiefdruck nach einer gravierten Druckform weisen die Rasterpunkte eine unterschiedliche Größe und Farbsättigung auf.[1]
Alle manuell hergestellten künstlerischen Tiefdrucke – üblicherweise im Bogendruckverfahren – haben als Erkennungszeichen einen durch den Druck in das gefeuchtete Papier entstandenen Plattenrand, die so genannte Facette, die sich in das Papier einprägt und auch auf der Rückseite des bedruckten Papiers eine Erhöhung bewirkt. Ein weiteres Merkmal ist, dass verschiedene Abzüge von einer Platte geringe Maßdifferenzen aufweisen. Grund ist die Feuchtigkeit fertiger Drucke, die bei anschließender Trocknung eine minimal unterschiedliche Schrumpfung der Bögen bewirkt.[1]
Wirtschaftliche Anwendung
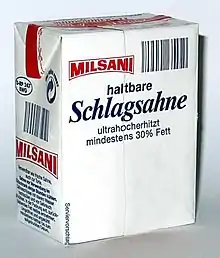
Das Tiefdruckverfahren wird heute für Druckaufträge mit hohen Auflagen von mehr als 300.000 Exemplaren wirtschaftlich eingesetzt. Die Wahl des Druckverfahrens ist abhängig von verschiedenen Kriterien, wie zum Beispiel dem Format oder der Anzahl der Druckformenwechsel. Im Illustrationstiefdruck werden in diesem Druckverfahren Zeitschriften wie stern, TV-Zeitschriften, Zeitungs- und Zeitschriftenbeilagen sowie Kataloge (früher zum Beispiel von IKEA) hergestellt. Ein anderes großes Marktsegment ist der Verpackungstiefdruck, zum Beispiel die Herstellung von Faltschachteln, Tetra Paks oder Folienverpackungen. Weitere Einsatzgebiete sind der Dekor-, Textil-, Banknoten- und Wertpapierdruck. Gedruckt wird vor allem auf saugfähigem Papier mit glatter, satinierter Oberfläche. Der Illustrationstiefdruck steht dabei in Konkurrenz zum Rollenoffsetdruck, während Verpackungen häufiger auch im etwas günstigeren Flexodruck-Verfahren hergestellt werden können.
Künstlerischer Tiefdruck
Als künstlerisches Medium verleiht der Tiefdruck dem Künstler große Souveränität, mit der sich sein Einfallsreichtum ungehindert verwirklichen kann. Insbesondere die Radierung ist seit Rembrandt immer wieder ein bevorzugtes Arbeitsgebiet bildender Künstler gewesen.
.jpg.webp)
Die künstlerischen Tiefdruckverfahren werden in zwei Gruppen unterteilt: Einmal die manuellen, trockenen Verfahren, die auf physikalischer Kaltverformung der Druckplatte beruhen, wie Kaltnadelradierung, Kupferstich, Mezzotinto (Schabtechnik), Steinradierung, und zum anderen die nassen Ätzverfahren, bei denen mit chemischen oder galvanischen Methoden Material entfernt wird, wie Ätzradierung, Aquatinta, Vernis Mou (Weichgrundätzung) und teilweise auch beim Stahlstich.[4]
Außerdem werden viele Mischtechniken verwendet, so dass die strikte Trennung zwischen trockenen und nassen Verfahren nicht mehr so eng begrenzt werden kann. Beim Prägedruck, auch Reliefdruck und ohne Farbe Blinddruck genannt, werden Metallplatten in Form geschnitten, zum Teil werden Bleche oder Drähte aufgelötet oder Teile der Platte ausgestanzt oder herausgesägt.
Manche Radierer prägen unterhalb der eigentlichen farbigen Darstellung ihr Künstlerzeichen als farblosen Blinddruck in das Kupferdruckbüttenpapier. Das Carborundum ist eine Kombination aus Radierung und Prägedruck, bei der (auch zusätzlich zur Radierung) auf Teile der Druckplatte eine Mischung aus Carborundum (Schleifmittel) oder Marmormehl mit Acrylharz aufgetragen wird. Die Druckfarbe haftet in den Kornzwischenräumen und ergibt beim Abdruck Farbflächen hoher Intensität. Joan Miró hat solche Arbeiten geschaffen.
Die Heliogravüre entstand Ende des 19. Jahrhunderts als mit den Edeldruckverfahren lichtempfindliche Beschichtungen aufkamen. Sie erlaubt fotografische Wiedergaben. Ende des 20. Jahrhunderts kamen neue Verfahren hinzu, die mit einer auf einer glatten Oberfläche kaschierten (meist lichtempfindlichen) Polymerfolie hergestellt werden. Cerataryt ist ein Druck mittels Wachsplatten oder gewachsten Stoffen.
Siehe auch
Literatur
- Wolfgang Autenrieth: Neue und alte Techniken der Radierung und Edeldruckverfahren – Ein alchemistisches Werkstattbuch für Radierer: Vom 'Hexenmehl und Drachenblut' zur Fotopolymerschicht. Tipps, Tricks, Anleitungen und Rezepte aus fünf Jahrhunderten. Ein alchemistisches Werkstattbuch für Radierer. 232 Seiten, 7. Auflage, Krauchenwies 2020, ISBN 978-3-9821765-0-5 (→ Auszüge und Inhaltsverzeichnis online)
- Eckhard Bremenfeld, Ralf Kapalla, Holger Knapp: Fachwissen Zeitungs- und Zeitschriftenverlage. Leitfaden für Verlagsberufe und Quereinsteiger. 4. Auflage. Springer-VDI, Düsseldorf 2001, ISBN 3-935065-03-5.
- Walter Koschatzky: Die Kunst der Graphik. DTV, München 1985, ISBN 3-423-02868-8.
- Lothar Lang: Der Graphikensammler. Henschelverlag Kunst und Gesellschaft, Berlin 1979.
- Bernd Ollech: Tiefdruck, Grundlagen und Verfahrensschritte der modernen Tiefdrucktechnik. Polygraph, Bielefeld 1999.
- Hans Jürgen Scheper: Prüfungswissen Drucktechnik. Verlag Beruf und Schule, Itzehoe 2005, ISBN 3-88013-623-8.
Weblinks
- Umfangreiche Linksammlung zu Tiefdruckverfahren / Radiertechniken
- Online - Werkstattbuch über Tiefdruck / Radierung
- Künstlerische Tiefdrucktechniken
- Literatur zu Tiefdruckverfahren im Katalog der Deutschen Nationalbibliothek
Einzelnachweise
- Helmut Kipphan (Hrsg.): Handbuch der Printmedien, Seite 49ff. Springer-Verlag, November 2000. ISBN 3-540-66941-8
- Photogravure. Abgerufen am 24. August 2009.
- Elektronische Zylindergravur. (Nicht mehr online verfügbar.) Archiviert vom Original am 7. November 2009; abgerufen am 25. August 2009. Info: Der Archivlink wurde automatisch eingesetzt und noch nicht geprüft. Bitte prüfe Original- und Archivlink gemäß Anleitung und entferne dann diesen Hinweis.
- Tiefdruckverfahren in der Kunst. Abgerufen am 28. August 2009.