Kohlenstoffbasierte Selektive Katalytische Reduktion
Die kohlenstoffbasierte selektive katalytische Reduktion (kurz CSCR, aus dem englischen carbon selective catalytic reduction) bezeichnet ein trockenes Abgasreinigungsverfahren zur Reduzierung von Schadstoffen in Abgasen von großtechnischen Anlagen wie zum Beispiel in Müllverbrennungsanlagen für Hausmüll und Industriemüll, Stahlwerken, Kohlekraftwerken, LCD-Glasherstellung[2] sowie in der Munitionsverwertung.[3]
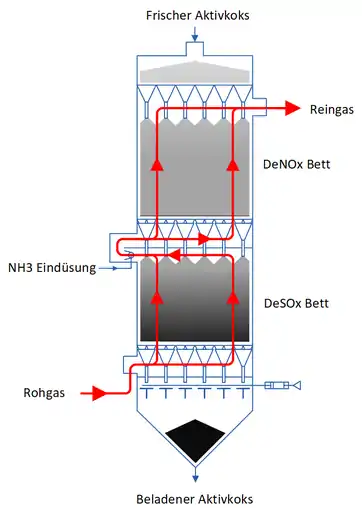
Das Verfahren zeichnet sich durch einen ein- oder mehrstufigen Aktivkoks-Wanderbettreaktor aus, welcher im Gegenstrom betrieben wird. Aktivkoks dient dabei sowohl als Katalysator für die Oxidation bestimmter Abgasbestandteile, wie auch als „Speicher“ für adsorbiertes Schwefeldioxid (SO2) in Form von Schwefelsäure (H2SO4) oder anderen Schadstoffe. Der beladene Aktivkoks wird ausgetragen und kann, je nach Anwendung, regeneriert werden oder wird in Kohlekraftwerken verbrannt.
Zur Entstickung wird nach vorheriger SO2-Abscheidung ein Stickoxid (NOx) reduzierendes Gas, zumeist Ammoniak (NH3), dem Abgas beigemischt. Anschließend wird NOx in einem weiteren Aktivkoksbett in Gegenwart von Aktivkoks als Katalysator zusammen mit NH3 zu Stickstoff (N2) und Wasser (H2O) umgesetzt.
Neben Stick- und Schwefeloxiden werden aufgrund der vielfältigen Eigenschaften[4] von Aktivkoks auch andere Schadstoffe wie etwa Dioxine und Furane, Staub, Schwermetalle wie zum Beispiel Quecksilber und Halogene wie Fluorwasserstoff und Chlorwasserstoff abgeschieden.
Aufbau und Funktionsweise eines CSCR Reaktors
Bei der CSCR-Technologie handelt es sich um ein adsorptives und absorptives trockenes Wanderbettverfahren. Die Rauchgasführung erfolgt entgegengesetzt dem Adsorptionsmittelfluss im Gegenstromprinzip.[5]
Das Rauchgas wird mit einer Temperatur von 90 °C bis 140 °C in den Rauchgassammelraum unterhalb der Aktivkoksschüttung geführt. Von dort aus gelangt das Gas in ein Aktivkoksbett. Falls erforderlich ist dem ersten Aktivkoksbett ein zweites nachgeschaltet.
Das erste Bett dient meist zur Abscheidung von Schwefeloxiden (SOx) und Staub. Der im Abgas enthaltene Staub wird aufgrund der Filterwirkung des Aktivkoksbettes abgeschieden. Im Abgas enthaltenes Schwefeldioxid (SO2) wird an der Aktivkoksoberfläche katalytisch zu Schwefeltrioxid (SO3) oxidiert und mit Wasserdampf (H2O) zu Schwefelsäure (H2SO4) umgesetzt, welche im Porensystem des Aktivkokses chemisch absorbiert wird. Neben SO2 und Staub werden auch andere Schadstoffe von dem Aktivkoks adsorbiert.
Im zweiten Bett findet die Entstickung statt. Bevor das Rauchgas in das zweite Bett gelangt, wird es in eine Mischkammer geführt, in der gasförmiges Ammoniakwasser beigemischt wird. Mit dem zugegebenen Ammoniak (NH3) reagieren die Stickoxide des Rauchgases an der katalytischen Oberfläche des Aktivkokses zu den unschädlichen Produkten Stickstoff (N2) und Wasser.[6] Das Rauchgas verlässt das zweite Bett und kann gereinigt in die Umgebungsluft über einen Kamin abgegeben werden.
Der konstruktive Aufbau des Adsorberanströmbodens sichert einerseits eine gleichmäßige Verteilung des Rauchgases beim Eintritt in die Aktivkoksschüttung und sorgt andererseits gleichzeitig dafür, dass sich die Schüttung beim Austragen des beladenen Aktivkoks planparallel absenkt.[7]
Bei Betätigung der Austragsvorrichtung gelangt der Aktivkoks in den Austragstrichter. Dabei senkt sich das Aktivkoksbett um einige Millimeter ab und frischer Aktivkoks rutscht selbsttätig aus dem Vorratsbunker in den Adsorptionsbereich des Adsorbers nach.
Durch das Gegenstromprinzip ist im Vergleich mit anderen Reaktoren eine gleichmäßige Beladung des Aktivkokses über die gesamte Anströmfläche sichergestellt. Ein weiterer Vorteil des Gegenstromprinzip ist die bessere Aktivkoksbeladefähigkeit und somit die Minimierung des Aktivkoksverbrauchs. Letzteres wird dadurch erreicht, dass über den einfachen, geregelten Abzug nur die am höchsten beladene Aktivkoksschicht in nahezu beliebig einstellbaren Chargen abgezogen wird.
Aktivkoks kann mit thermischer Behandlung regeneriert werden. Man erhält auf diesem Wege ein hoch konzentriertes SO2-Reichgas, welches verwendet werden kann, um beispielsweise elementaren Schwefel oder Schwefelsäure herzustellen.
Chemische Reaktionen
Im Abgas enthaltenes SO2 wird gemäß der aufgezeigten Reaktionsgleichung auf der Aktivkoksoberfläche im Temperaturbereich von etwa 20 – 150 °C katalytisch zu SO3 oxidiert, welches mit dem Wasserdampf im Abgas zu Schwefelsäure umgesetzt wird.
Ein geringer Teil der gebildeten Schwefelsäure wird mit den basischen Aschebestandteilen zu den entsprechenden Sulfaten umgesetzt.
Erst nach dem DeSOx-Bett wird dem Rauchgas NH3 als Reduktionsmittel hinzugegeben, da NH3 aufgrund seiner Affinität zuerst mit SO2 reagieren würde. Dabei entstehen Sulfate und Bisulfate, welche am Aktivkoks abgeschieden werden und dessen katalytische Eigenschaften hemmen. Deswegen wird im ersten Aktivkoksbett ein Großteil des SO2 ohne NH3 abgeschieden.
Im zweiten Aktivkoksbett, welches für die Entstickung (DeNOx) gedacht ist, reagiert dann das restliche SO2, welches nicht im DeSOx-Bett abgeschieden wurde, zusammen mit Ammoniak und Wasserdampf zu Ammoniumsulfit und wird im Porensystem absorbiert.
Die Zusammensetzung des Rauchgases wird zwar von dem eingesetzten Brennstoff und den Verbrennungsparametern bestimmt, jedoch gilt die Regel, dass Stickoxide aus 5 - 10 %-Vol. NO2 und 90 - 95 %-Vol. NO bestehen. Sauerstoffgehalt von Abgasen variiert zwischen 1 %-Vol. für Gasfeuerungen und etwa 15 %-Vol. für Müllverbrennungsanlagen. Stickstoff und Kohlenstoffdioxid (CO2) sind Residuen und nehmen an der Abscheidereaktion nicht teil.[8]
Stickstoffmonoxid oxidiert katalytisch an der Oberfläche des Aktivkokses und mithilfe des Sauerstoffs im Abgas zu Stickstoffdioxid.
NO2 wird dann durch das in der Mischkammer zugegebene Ammoniak reduziert und die Produkte Stickstoff und Wasserdampf verlassen zusammen mit dem gereinigten Rauchgas die Anlage.[9]
Stickstoffmonoxid kann auch direkt katalytisch umgesetzt werden.[10]
Die Hauptreaktion für Stickoxidabscheidung lautet wie folgt.
Letztere Reaktion findet nur in Gegenwart von Sauerstoff statt, welches im Abgas enthalten ist. Eine Erhöhung der Sauerstoffkonzentration im Rauchgas über 5 %-Vol. hinaus führt jedoch nicht zu einer weiteren Erhöhung der NO-Reduktion. Des Weiteren erhöht überstöchiometrische NH3-Zugabe zwar die Konversion, führt aber häufig zu NH3-Schlupf, der im Reingas zu messen ist.
CSCR in der Stahlindustrie
Abgase von Sinterbandprozessen stellen einen erheblichen Anteil der Verunreinigungen dar, die bei der Stahlerzeugung insgesamt anfallen. Aufgrund der sehr hohen Abgasmengen, die bei Sinterbandanlagen anfallen, ist eine zufriedenstellende Abgasreinigung mit hohen Kosten und großem Aufwand verbunden, da bei herkömmlichen Reinigungsverfahren mehrere Reinigungsschritte hintereinandergeschaltet werden müssen.
Insbesondere, wenn Stickoxide aus dem Rauchgas entfernt werden sollen, stellt man sich der Herausforderung, dass andere Schadstoffkomponenten, wie SO2 und HCl auf den Aktivkoks wie ein Katalysatorgift wirken.
Bei der CSCR Technologie wird dieses Problem vermindert oder weitgehend beseitigt. SO2 und NOx kann mit diesem Verfahren gleichzeitig oder Katalysatorschädigung abgeschieden werden, indem der Sinterabgasreinigungsprozess als zweistufiger Wanderbettreaktor ausgeführt wird. Auch wenn das Sinterabgas nach einem Vorreinigungsprozess bspw. Mit einem Nasswäscher immer noch deutliche Konzentrationen an SO2 und/oder HCl vorweist, werden diese Stoffe im ersten Verfahrensschritt des CSCR-Prozesses abgeschieden, ohne die Reinigung für NOx zu belasten und den dafür verwendeten Katalysator nennenswert zu schädigen.[11]
Bevorzugte Verfahren zur Vorreinigung des Sinterabgases, bevor es zur CSCR übergeben wird, sind Schlauch- oder Elektrofilter, Abgaswäscher oder Flugstromabsorber bspw. mit Kalkstaub.
Mit diesem Gegenstrom Wanderbettverfahren werden Restwerte im gereinigten Sinterabgas von 10 mg/Nm3 SO2, 50 mg/Nm3 NOx und 10 mg/Nm3 Staub erreicht.
Aufgrund der Vorteile die CSCR bietet ist dieses Verfahren von einer Nischentechnologie mehr und mehr in die Mitte gerutscht und findet Einsatz in vielen Stahlwerken im asiatischen Raum, zum Beispiel bei Anlagen der Jiangsu Shagang Group, der Anshan Iron and Steel Group und der Masteel Group.
CSCR in Müllverbrennungsanlagen
Müllverbrennungsanlagen zur Energie- und Wärmegewinnung gerieten in den 1990er Jahren in Bedrängnis, da bekannt wurde, dass die Verbrennung von Haus- und Industrieabfällen eine Quelle für polychlorierte Dibenzodioxine und Dibenzofurane (PCDD/F) darstellen. Viele Menschen, die in der Nähe von Müllverbrennungsanlagen wohnen, waren besorgt, dass sie hohen Konzentrationen dieser krebserregender Schadstoffe ausgesetzt wurden.
Die CSCR-Technologie ist eine wirtschaftliche Möglichkeit Dioxine und Furane fast bis zur Nachweisgrenze (0,001 ngTE/Nm³) abzuscheiden. Neben PCDD/F werden in Müllverbrennungsanlagen auch Staub, Schwermetalle und Quecksilber, Schwefeloxide und Halogene, wie HF und HCl abgeschieden. Typischerweise wird in thermischen Abfallbehandlungsanlagen Braunkohleaktivkoks eingesetzt, der nicht wieder regeneriert wird. In vielen Anwendungen wird dieser Herdofenkoks in Kohlekraftwerken mitverbrannt. Dioxine und Furane zersetzen sich dabei.
Zu den in Deutschland mit CSCR-Abgasreinigungstechnologie ausgerüsteten zählen unter anderen:
Weitere Anwendungen für CSCR
Da die CSCR-Technologie von den vielfältigen Eigenschaften von Aktivkoks getragen wird, so ist auch der Anwendungsbereich dieser Technologie ebenso vielseitig. Die modulare Bauweise der CSCR-Reaktoren erlaubt den Betrieb von Anlagen für beliebige Rauchgasmengen. Typische Anwendungen liegen zwischen 3.000 Nm³/h und 2.000.000 Nm³/h.[1]
Anwendungsfelder für CSCR-Technologie:
- Stahlerzeugung
- Pelletierung
- Kokerei
- Sinteranlagen
- Abfallverbrennung (Industrie- und Haushaltsmüll)
- Klärschlammverbrennung
- Kohlekraftwerke
- Glasschmelzprozesse
- Munitionszerstörung
- Zementherstellung
- Chemische Prozesse
Einzelnachweise
- WKV – Dr. Grochowski Anlagentechnik GmbH. Abgerufen am 26. März 2020 (deutsch).
- Patent EP1838419B1: Verfahren zum Reinigen von Abgasen eines Glasschmelzprozesses, insbesondere für Gläser für LCD-Bildschirme. Angemeldet am 12. Januar 2006, veröffentlicht am 11. Mai 2011, Erfinder: Horst Grochowski.
- Isao Mochida, Yozo Korai, Masuaki Shirahama, Shizuo Kawano, Tomohiro Hada: Removal of SOx and NOx over activated carbon fibers. In: Carbon. Band 38, Nr. 2, 1. Januar 2000, ISSN 0008-6223, S. 227–239, doi:10.1016/S0008-6223(99)00179-7 (sciencedirect.com [abgerufen am 17. März 2020]).
- CarboTech GmbH | Ihr Spezialist für Aktivkohle. Abgerufen am 17. März 2020.
- Margit Löschau: Reinigung von Abgasen. TK-Verlag, Nietwerder 2014, ISBN 978-3-944310-13-8, S. 220–222.
- Patentanmeldung DE2635063A1: Katalysator für die Reduktion von Stickstoffoxiden in Anwesenheit von Ammoniak. Angemeldet am 4. August 1976, veröffentlicht am 24. Februar 1977, Anmelder: Kurashiki Boseki KK, Erfinder: Masumi Saito et al.
- Patent EP0357653B1: Anströmboden für Wanderbettreaktoren. Angemeldet am 5. Mai 1988, veröffentlicht am 19. Januar 1994, Erfinder: Horst Grochowski.
- Ekkehard Richter, Hans-Jürgen Schmidt, Hans-Georg Schecker: Adsorption and catalytic reactions of NO and NH3 on activated carbon. In: Chemical Engineering & Technology. Band 13, Nr. 1, 1990, ISSN 1521-4125, S. 332–340, doi:10.1002/ceat.270130146.
- Gomi, Kenichi; Komuro, Takeo; Arashi, Norio; Hishinuma, Yukio; Kanda, Osamu; Kuroda, Hiroshi: Reduction of nitrogen monoxide(NO) with ammonia in sulfur dioxide-containing gas on activated carbon and vanadium pentaoxide-loaded activated carbon. Hrsg.: Chemical Society of Japan. 4. Auflage. 1986, S. 527—531.
- Karl Knoblauch, Ekkehard Richter, Harald Jüntgen: Application of active coke in processes of SO2- and NOx-removal from flue gases. In: Fuel (= Industrial Conversion of Coal and Carbon to Gas, Liquid and High-Value Solid Products). Band 60, Nr. 9, 1. September 1981, ISSN 0016-2361, S. 832–838, doi:10.1016/0016-2361(81)90146-0.
- Patentanmeldung WO2006084671A1: Verfahren zum Reinigen von Abgasen eines Sinterprozesses von Erzen und/oder anderen metallhaltigen Materialien in der Metallerzeugung. Angemeldet am 8. Februar 2006, veröffentlicht am 17. August 2006, Erfinder: Horst Grochowski.