Hobeln und Stoßen
Das Hobeln und Stoßen sind zwei spanende Fertigungsverfahren der Gruppe Spanen mit geometrisch bestimmter Schneide, die mit einschneidigen Zerspanungswerkzeugen durchgeführt werden: Dem Hobelmeißel und dem Stoßmeißel oder -messer. Ein Hobel dagegen ist ein Werkzeug für ein verwandtes Verfahren der Holzbearbeitung. Sie werden nach DIN 8580 gemeinsam einer Gruppe zugeordnet, da sie kinematisch identisch sind; die Relativbewegung zwischen Werkzeug und Werkstück ist also dieselbe. Beim Stoßen wird die Schnittbewegung durch Bewegung des Werkzeuges erzeugt bei stehendem Werkstück; beim Hobeln ist es andersherum. Stoßen und Hobeln dienen zur Herstellung ebener Flächen wie Nuten und Einstiche; sie spielen jedoch in der industriellen Fertigung kaum noch eine Rolle, da sie weitgehend durch Fräsen ersetzt wurden, das produktiver und flexibler ist. Wichtige Ausnahmen sind das Wälzhobeln und Wälzstoßen zur Herstellung von Zahnrädern. Die zugehörigen Werkzeugmaschinen sind die Hobelmaschine und die Stoßmaschine. Vorteile des Stoßens und Hobelns gegenüber anderen Verfahren sind die niedrigen Einricht- und Werkzeugkosten sowie die geringere Erwärmung des Werkstücks. Nachteilig sind dagegen die hohen Fertigungszeiten (unwirtschaftlicher Leer-Rückhub und begrenzte Schnittgeschwindigkeit), beim Hobeln zusätzlich die Maschinengröße. Hobeln und Stoßen zählen gemeinsam mit dem Drehen und Bohren zu den ältesten Fertigungsverfahren. Siehe Geschichte der Produktionstechnik.
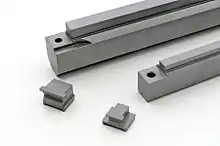
Definition nach DIN 8589
„Hobeln bzw. Stoßen ist Spanen mit schrittweiser, wiederholter, meist geradliniger Schnittbewegung und schrittweiser, zur Schnittrichtung senkrechter Vorschubbewegung.“[1]
Stoßen
Beim Stoßen führt das Werkzeug die hin- und hergehende Schnittbewegung aus. Sie besteht aus einem Arbeitshub, bei dem Material abgetragen wird, und einer Rückbewegung, die Leerhub genannt wird, bei der kein Material abgetragen wird. Nach dem Arbeitshub bewegt sich das Werkstück senkrecht zur Schnittbewegung (Vorschubbewegung), um den weiteren Materialabtrag zu gewährleisten. Beim Waagrechtstoßen bewegt sich das Werkzeug in waagrechter Richtung, das Werkstück kann sich entweder horizontal oder vertikal bewegen. Beim Senkrechtstoßen bewegt sich das Werkzeug senkrecht und das Werkstück innerhalb einer Ebene, die waagrecht zum Boden liegt.
Hobeln
Beim Hobeln ist das Werkzeug fest eingespannt, und das Werkstück vollführt die Schnittbewegung. Nach dem Rückhub bewegt sich das Werkzeug senkrecht zur Schnittrichtung weiter und vollführt somit die Vorschubbewegung. Die Schnittrichtung liegt praktisch immer in waagrechter Richtung. Der Vorschub kann auch nach oben oder unten erfolgen.
Einteilung der Verfahren
In der DIN 8589 werden alle spanenden Fertigungsverfahren nach einem einheitlichen Ordnungsschema eingeteilt. Das Hobeln und Stoßen trägt dort die Ordnungsnummer 3.2.4 (3. Hauptgruppe: Trennen, 2. Gruppe: Spanen mit geometrisch bestimmter Schneide, 4. Fertigungsverfahren).[2]
- 3.2.4.1: Planhobeln und -stoßen: Dient zur Erzeugung planer, also ebener Oberflächen.
- 3.2.4.2: Rundhobeln und -stoßen: Dient zur Herstellung von runden Oberflächen.
- 3.2.4.3: Schraubhobeln und -stoßen: Dient der Herstellung von schraubigen Oberflächen.
- 3.2.4.4: Wälzhobeln und Wälzstoßen: Dienen der Herstellung von Verzahnungen, z. B. Zahnräder oder Zahnstangen.
- 3.2.4.5 Profilhobeln und -stoßen: Dient zur Herstellung beliebiger Oberflächen mit einem profilierten Werkzeug, das die zu erzeugende Form als Negativ enthält.
- 3.2.4.6 Formhobeln- und -stoßen: Dient zur Herstellung beliebiger Oberflächen, die durch die gesteuerte Schnitt- und Vorschubbewegung erzeugt werden.
Oberflächen und Genauigkeiten
Die erzeugten Oberflächen weisen charakteristische parallele Linien auf, die von den Bearbeitungsspuren herrühren. Die erreichbaren Rauheiten gemessen als mittlere Rauheit liegen bei Ra = 2 bis 4 µm. Diese lassen sich erreichen durch Verwendung von Breitschlichtwerkzeugen, bei denen die Nebenschneide etwa eineinhalb bis doppelt so lang ist wie der Vorschub und der Werkzeug-Einstellwinkel der Nebenschneide sehr klein ist. Die erreichbaren Maßabweichungen gemessen als erreichbare ISO-Toleranzen liegen bei IT 8. In Sonderfällen sind auch IT 7 oder IT 6 möglich.
Die Rauheit hängt ab vom Vorschub, dem Werkstoff, der Schneidengeometrie und der Schnitttiefe.
Berechnung von Kräften und Leistungen
Die benötigte Leistung ergibt sich aus der Schnittkraft , der Reibungskraft an der Tischführung der Maschine , der Schnittgeschwindigkeit und dem Wirkungsgrad des Antriebs zu
- .
Die Schnittkraft lässt sich mit der Kienzle-Formel berechnen. In diese gehen ein die Schnitttiefe , der Vorschub und die Spezifische Schnittkraft :
Die Reibungskraft ergibt sich aus der Gewichtskraft des Maschinentisches und der Gewichtskraft des größten Werkstücks sowie dem Reibungskoeffizient zu:
Richtwerte
Die Schnittgeschwindigkeit hängt von mehreren Faktoren ab. Unter anderem vom Schneidstoff, von den Standkriterien und der erwünschten Standzeit.
Richtwerte für Schnellarbeitsstahl
Für Werkzeuge aus Schnellarbeitsstahl und Standzeiten von 60 Minuten gelten folgende Werte:
Werkstoff | Vorschub [mm] | Schnittgeschwindigkeit [m/min] | Schneitteilgeometrie | |||
---|---|---|---|---|---|---|
Bezeichnung | Zugfestigkeit [N/mm²] bzw. Brinellhärte | Freiwinkel | Spanwinkel | Neigungswinkel | ||
Grauguss | bis 200 HB | 0,4 bis 1,0 | 18 bis 13 | 8° | 8° | 8° |
1,0 bis 2,5 | 13 bis 10 | 8° | 8° | 8° | ||
200 bis 250 HB | 0,4 bis 1,0 | 12 bis 9 | 8° | 6° | 8° | |
1,0 bis 2,5 | 9 bis 7 | 8° | 6° | 8° | ||
legierter Grauguss | 250 bis 450 HB | 0,4 bis 1,0 | 11 bis 9 | 8° | 6° | 8° |
1,0 bis 2,5 | 9 bis 7 | 8° | 6° | 8° | ||
Baustahl/ Einsatzstahl/ Vergütungsstahl | 500 | 0,4 bis 1,0 | 18 bis 12 | 8° | 14° | 8° |
1,0 bis 2,5 | 12 bis 8 | 8° | 14° | 8° | ||
600 | 0,4 bis 1,0 | 12 bis 8 | 8° | 12° | 8° | |
1,0 bis 2,5 | 8 bis 6 | 8° | 12° | 8° | ||
700 | 0,4 bis 1,0 | 11 bis 7 | 8° | 10° | 8° | |
1,0 bis 2,5 | 7 bis 5 | 8° | 10° | 8° | ||
Stahlguss | 700 | 0,4 bis 1,0 | 11 bis 7 | 8° | 10° | 8° |
1,0 bis 2,5 | 7 bis 5 | 8° | 10° | 8° |
Richtwerte für Hartmetall
Für Werkzeuge mit eingelöteten Schneiden aus Hartmetall und einer Standzeit von 240 Minuten gelten folgende Werte:
Werkstoff | Vorschub [mm] | Anwendungsgruppe | Schnittgeschwindigkeit [m/min] | Schneitteilgeometrie | |||
---|---|---|---|---|---|---|---|
Bezeichnung | Zugfestigkeit [N/mm²] bzw. Brinellhärte | Freiwinkel | Spanwinkel | Neigungswinkel | |||
Grauguss | bis 180 HB | 0,4 bis 1,0 | K20 | 45 bis 30 | 8° | 15° bis 20° | −10° |
1,0 bis 1,6 | K20 | 30 bis 25 | 8° | 15° bis 20° | −10° | ||
K30 | 25 bis 20 | 8° | 20° | −10° | |||
1,6 bis 2,5 | P40 | 30 bis 25 | 8° | 20° | −10° | ||
K30 | 20 bis 15 | 8° | 20° | −10° | |||
180 bis 220 HB | 0,4 bis 1,0 | P30 | 60 bis 45 | 8° | 20° | −10° | |
M20 | 50 bis 35 | 8° | 10° | −10° | |||
K10 | 50 bis 35 | 8° | 10° | −10° | |||
K20 | 40 bis 30 | 8° | 10° | −10° | |||
1,0 bis 1,6 | P30 | 45 bis 35 | 8° | 20° | −10° | ||
K20 | 30 bis 25 | 8° | 10° bis 15° | −10° | |||
1,6 bis 2,5 | P40 | 25 bis 20 | 8° | 20° | −10° |
Siehe auch
- Liste der spanenden Fertigungsverfahren: Überblick über die Fertigungsverfahren mitsamt Definition nach DIN 8589 und die zugehörigen Werkzeuge, Werkzeugmaschinen und erreichbaren Genauigkeiten
- Spanbildung
- Zerspanbarkeit
- Hochgeschwindigkeitszerspanen
- Energieumwandlung und Wärme beim Spanen
Einzelnachweise
- Uwe Heisel, Fritz Klocke, Eckart Uhlmann, Günter Spur: Handbuch Spanen. Hanser, 2014, S. 23.
- Alfred Herbert Fritz, Günter Schulze (Hrsg.): Fertigungstechnik. 11. Auflage. Springer Vieweg, Berlin/Heidelberg 2015, S. 328.
Literatur
- Fritz Klocke, Martin Arft: Hobeln, Stoßen in: Uwe Heisel, Fritz Klocke, Eckart Uhlmann, Günter Spur: Handbuch Spanen. Hanser, 2014, S. 453–463.