Viskosefaser
Als Viskosefasern werden Chemiefasern (Regeneratfasern) aus regenerierter Cellulose bezeichnet, die sowohl als Filamentgarn als auch als Spinnfaser hergestellt werden können. Sie werden nach dem Viskoseverfahren, dem verbreitetsten Nassspinnverfahren, industriell ersponnen.
Früher wurden Viskose-Filamentgarne als Reyon (engl. Rayon) oder Kunstseide, die Spinnfasern als Zellwolle bezeichnet.[1] Diese Bezeichnungen dürfen laut Textilkennzeichnungsverordnung nicht mehr für die Kennzeichnung von Textilerzeugnissen verwendet werden.[2]
Allgemeines
Die regenerierte Cellulose ist chemisch identisch mit der nativen Fasercellulose, wie zum Beispiel der Baumwolle, weist aber ein anderes Elementargitter in den geordneten Bereichen auf, nämlich das der Cellulose II oder Hydratcellulose. Der Ordnungszustand ist etwa nur noch halb so groß wie in der nativen Cellulose.[3]
Die Herstellung erfolgt in drei Hauptstufen[4]:
- Erzeugung der Spinnlösung, der Viskose,
- Erspinnen der Filamente und
- Nachbehandlung der ersponnenen Fäden.
Durch Modifizierung der Herstellungsparameter und der Nachbehandlung können Viskosefasern sehr gut den vorgesehenen Verarbeitungs- und Verwendungszwecken angepasst werden. Als einfachste Anpassung an spätere Verarbeitungsstufen gilt das Schneiden oder Reißen der aus dem Spinnbad abgezogenen Filamentkabel zu Spinnfasern mit Längen überwiegend zwischen 2 und 130 Millimeter. Die Feinheit von Viskosefasern kann zwischen 0,5 und 30 dtex eingestellt werden, was unter der Voraussetzung eines runden Querschnitts einem Durchmesser von 6 bis 30 µm entspricht.[5]
Weitere Modifizierungen gegenüber der Normaltype sind z. B. hochgekräuselte, hochnassfeste, farbfeste spinngefärbte und schwer entflammbare Fasern.[6] Durch Variation der Faserlänge und der Kräuselung lassen sich die Viskosefasern der Baumwollfaser (B-Typen: 50–60 mm, wenig gekräuselt) und der Wolle (W-Typen: 30–150 mm, stark gekräuselt) anpassen, was für die Herstellung von Mischgarnen von Bedeutung ist.[7]
Herstellung (Viskoseverfahren)
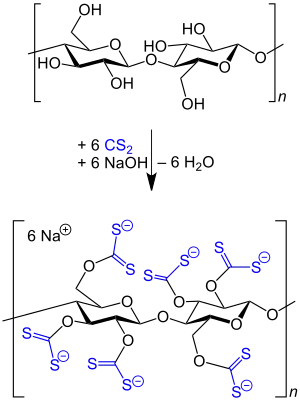
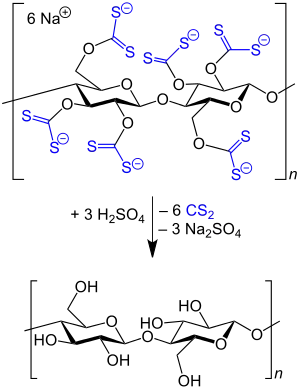
Die gegenwärtig existierenden Viskosefaser-Produktionsanlagen weisen einen sehr unterschiedlichen Aufbau auf. Eine umfassende Darstellung ist deshalb hier nicht möglich. An für alle Viskosefaser-Herstellungsverfahren gebräuchlichen Prozessen soll ein prinzipieller Überblick gegeben werden.
Erzeugung der Spinnlösung
Als Ausgangsmaterial für die Viskosefaserherstellung dient Chemiezellstoff, der durch chemische Aufschlussverfahren aus verschiedenen Holzsorten von Buchen, Fichten, Eukalyptus, Pinien, Bambus, einjährigen Faserpflanzen oder Baumwolllinters gewonnen wird. Diese Zellstoffqualität unterscheidet sich von dem Zellstoff für die Papierherstellung dadurch, dass die Kettenlänge der Cellulosepolymere kürzer und die Reinheit höher ist. Der Zellstoff für die Viskoseproduktion enthält weniger Restlignin und weniger Hemizellulosen, bzw. Pentosane. Er hat eine bessere Reaktivität gegenüber Natronlauge und Schwefelkohlenstoff und eine bessere Löslichkeit in Natronlauge nach erfolgter Xanthogenierungsreaktion.
Für die Herstellung der Viskosefasern[9][10][11] nach dem klassischen Viskoseverfahren muss eine Spinnlösung, die Viskose, erzeugt werden. Dazu werden die aus der Zellstoffherstellung gelieferten Zellstoffbögen zunächst in einer wässrigen Natronlauge (NaOH) eingeweicht. Dabei quillt die Cellulose (Mercerisierung) und wird in Alkalicellulose umgewandelt. Die aufgequollenen Alkalicellulosebögen werden abgepresst und anschließend mechanisch in feine Partikel zerfasert, um die Oberfläche zu vergrößern und damit die spätere Umsetzung der Alkalicellulose mit Schwefelkohlenstoff schneller und gleichmäßiger ablaufen zu lassen. Die zerkleinerte Alkalicellulose wird danach in einem speziellen Behälter einer sogenannten Vorreife (auch als Alterung bezeichnet) unterzogen. Bei konstanter Temperatur und Luftfeuchtigkeit wird unter Einfluss von Luftsauerstoff der Polymerisationsgrad der Cellulose herabgesetzt, um damit später eine spinnfähige Viskosität der Spinnlösung einstellen zu können.[12] Auf die vorgereiften Alkalicellulosepartikel lässt man Schwefelkohlenstoff (CS2) einwirken. Dabei entsteht Natriumxanthogenat (Xanthat). Das orangegelbe Xanthat bildet in wässriger, verdünnter Natriumhydroxid-Lösung eine viskose Lösung. Aus dieser Zustandsbeschreibung der Lösung in diesem Reaktionsstadium leiten sich die Bezeichnungen Viskose-Lösung, und letztendlich Viskosefaser ab. Die Spinnlösung mit einer Konsistenz ähnlich der von warmem Honig, wird zwei- bis dreimal filtriert. Bei den aufeinander folgenden Filtrationen werden immer sorgfältiger die festen Verunreinigungen und die gequollenen, nicht vollständig gelösten Polymerteilchen aus der Lösung entfernt. Die verbleibenden Teilchen dürfen nicht größer als die Spinndüsenlöcher sein, um die spätere Filamentbildung nicht zu gefährden. Ebenfalls werden durch Vakuumeinwirkung Luftbläschen beseitigt. Es folgt die Nachreife der Viskose-Lösung über einen längeren Zeitraum in speziellen Behältern. Im Gegensatz zur Vorreife verringert sich dabei der Polymerisationsgrad nur noch wenig. Ziel der Nachreife ist vielmehr eine vollkommen gleichmäßige Viskoselösung; um ein besseres Durchmischen zu erreichen, wird die Lösung im Reifebehälter oft bewegt. Während der Reife wird das Cellulosexanthogenat allmählich hydrolysiert, wodurch der Veresterungsgrad abnimmt. Es erfolgt meist eine weitere Filtration und Entlüftung der Spinnlösung. Gleichzeitig wird auch Schwefelkohlenstoff und Wasserdampf abgesaugt. Die fertige Spinnlösung wird über eine Rohrleitung dem Spinnkessel zugeführt.
Erspinnen der Filamente
Die alkalische Spinnmasse wird aus dem Spinnkessel mittels Zahnradpumpen durch Spinndüsen in ein Fällbad (Spinnbad) gepresst. Der Durchmesser eines Einzellochs der Spinndüse liegt je nach der Zielvorgabe für die später zu erreichende Faserfeinheit zwischen ca. 25 µm und 250 µm.[13] Die Anzahl der Bohrungen pro Spinndüse beträgt für Viskose-Filamente zwischen 15 und 120, je nachdem aus wie vielen Filamenten das Filamentgarn bestehen soll.[14] Für die Herstellung von Viskosespinnfasern werden Spinndüsen mit einer Bohrlochanzahl zwischen 3000 und 60.000, in Sonderfällen sogar bis 100.000 eingesetzt.[15]
Für die Viskosefasern im klassischen Herstellungsprozess wird ein Schwefelsäurespinnbad verwendet, das Natriumsulfat fast bis zur Sättigungsgrenze und eine geringe Menge Zinksulfat zur Verzögerung der Cellulose-Ausfällungsreaktion enthält. Durch Neutralisation bildet die Schwefelsäure aus dem Natriumxanthogenat sowohl Natriumsulfat als auch die unbeständige Cellulose-Xanthogensäure, die ihrerseits sofort zu Cellulose und Schwefelkohlenstoff zerfällt. Die zurückgebildete (regenerierte) Cellulose koaguliert dabei zu Filamenten, die aus dem Fällbad abgezogen werden. Die noch weichen und formbaren Filamente werden sofort in einem Streckwerk verstreckt (gereckt), d. h. bleibend gedehnt. Die Gesamtverstreckung beträgt für Standardfasern (Normaltyp) ca. 20 % und für hochfeste Fasern bis zu 200 % und mehr. Das Verstrecken führt zu einer erhöhten Orientierung der Kettenmoleküle der Faser, wodurch z. B. die Scheuer- und Zugfestigkeit erhöht werden. Bei dem Viskose-Normaltyp liegen im Kern der Faser die Kettenmoleküle noch relativ ungeordnet vor. Man spricht deshalb von einer Kern-Mantel-Struktur.[16][17][18]
Eine Regenerierung der Spinnbäder erfolgt zur sicheren Faserherstellung, wegen der notwendigen Chemikalieneinsparung und des Umweltschutzes.[19] Sehr wesentlich für die Regenerierung des Fällbades ist die Entfernung der geringen Mengen Kohlendioxid, und des übelriechenden Schwefelwasserstoffs, der in einer aufwendigen Gaswäsche entfernt werden muss. Alternativ kann das Biotrickling-Filter-Verfahren (Lenzing AG) angewendet werden, eine einfache und betriebssichere biologische Reinigungstechnik. Das Wasser und das Natriumsulfat werden in der Rückgewinnung für die Wiederaufbereitung des Spinnbades aus dem verbrauchten Bad entfernt. Natriumsulfat ist somit ein Koppelprodukt im klassischen Viskoseverfahren und wird größtenteils an die Waschmittelindustrie verkauft. Der im Spinnprozess freigesetzte Schwefelkohlenstoff wird zum einen aus den Spinnanlagen abgesaugt und entweder durch Absorption an Aktivkohle direkt zurückgewonnen oder zum anderen zur Herstellung von Schwefelsäure verbrannt.
Nachbehandlung der ersponnenen Filamente und Konfektionierung
Die Anzahl und die Reihenfolge der Nachbehandlungsschritte hängen von der gewünschten Produktqualität sowie von den vorhandenen Nachbehandlungsapparaturen ab. Unterschiede gibt es z. B. beim Schneiden der Filamentkabel in Spinnfasern, das bei manchen Anlagen unmittelbar nach dem Streckwerk, bei anderen erst am Ende der nassen Nachbehandlungsstufen nach dem Trocknen der Filamente erfolgt. Auch bei der Nachbehandlung von Filamentgarnen gibt es Varianten: Sowohl Zwischenspeicherung vor dem Nachbehandeln als auch kontinuierlicher Durchlauf der Filamentgarne durch die Nachbehandlungsanlagen sind in Gebrauch. Wesentliche Nachbehandlungsstufen zur Beseitigung von an den Fasern anhaftenden Verunreinigungen sind, bei unterschiedlicher Reihenfolge in den Herstellungsanlagen, erforderlich. Beim Verstrecken des frischen Spinnkabels wird das CS2 durch Austreibung aus den Fasern mittels Dampf und nachfolgender Kondensation der Brüden direkt wiedergewonnen und in den Prozess zurückgeführt; seine vollständige Rückgewinnung wird dabei angestrebt.
Die Filamente müssen anschließend intensiv gewaschen werden. Von besonderer Bedeutung ist das Entfernen der Schwefelsäurereste, da sie die Zellulosefasern beim Trocknen zerstören würden. Infolge von Nebenreaktionen bei der Filamentbildung entstandener elementarer Schwefel kann sich an der Filamentoberfläche als gelbliche Verfärbung festsetzen und die weitere Verarbeitung erschweren. Zwar entfernt Heißwäsche einen großen Teil des Schwefels, es kann aber zusätzlich ein Behandeln mit Entschwefelungschemikalien wie Alkalisalzen notwendig werden. Um den Weißgrad der Filamente zu erhöhen, erfolgt eine Bleiche, die zumindest in Europa chlorfrei erfolgt. Als abschließende Nassbehandlung werden die Filamente mit ölhaltigen Substanzen überzogen, um sie sowohl gleitfähiger als auch geschmeidiger und länger lagerfähig zu machen.[20] Anschließend werden die getrockneten Viskosespinnfasern in Ballen von etwa 250 bis 350 Kilogramm mit einer Reprise (handelsübliche Restfeuchte) von etwa elf Prozent gesammelt. Viskosefilamentgarne werden mit Spulengewichten von etwa 1,5 bis 6,0 Kilogramm aufgewickelt. Die Feinheit liegt üblicherweise zwischen 40 und 660 dtex.
Modifizierte Viskosefasern
Die Normaltype der Viskosefaser besitzt Eigenschaften, die nicht für alle Anwendungszwecke optimal sind. Die Herstellung der Viskosefasern durch ein Nassspinnverfahren bietet aber gute Modifikationsmöglichkeiten. Um die Eigenschaften der Fasern dem Verwendungszweck besser anzupassen, können in die Spinnlösung feste und flüssige Zusätze eingemischt werden und zusätzlich können die Fällbäder (Regenerierungsbäder) sowie die Produktionsgeschwindigkeiten und Verstreckungen variiert werden.[21]
Hochgekräuselte Viskose-Spinnfasern
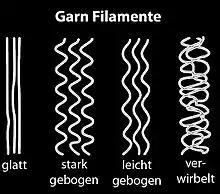
Die normalen Viskosefasern weisen eine zu geringe Kräuselung auf, um z. B. mit Wolle zu bauschigen Garnen verarbeitet werden zu können. Texturierverfahren, wie sie für thermoplastische Synthesefasern zum Erzeugen von Kräuselbögen genutzt werden, sind für Viskosefasern nicht anwendbar. Um hochgekräuselte Fasern zu erhalten, werden die Herstellungsbedingungen verändert: Zum Beispiel lässt man die Viskose länger reifen; die Koagulation der Filamente kann außerdem durch die Zusammensetzung des Spinnbades verändert werden, das beeinflusst die Gleichmäßigkeit und die Dicke des Fasermantels. Im Vergleich zum Faserkern verstärktes Schrumpfen des Mantels im heißen Waschbad und bei der anschließenden Trocknung verursacht dann eine beständige Kräuselung der Faserfilamente von 90–140 Bögen/10 cm. Die hochgekräuselten Filamente werden dann auf die gewünschte Länge zerschnitten.[22][23]
Querschnittsmodifizierte Viskosefasern
Mithilfe von profilierten Spinndüsenbohrungen lassen sich profilierte Viskosefasern herstellen. Der Faserquerschnitt weist gegenüber dem „runden“ (wolkenförmigen) des Normaltyps z. B. flache (Verhältnis Dicke D / Breite B 1:5), trilobale (dreigelappte)(D/B 1:5) oder ultraflache (D/B 1:20 bis 1:40) Formen auf, die die Faseroberfläche gegenüber dem Normaltyp auf 150 %, 240 % oder 260 bis 360 % erhöht, wodurch z. B. sich die Eigenschaften von den aus diesen Fasern hergestellten Filtern verändern.[24] Bei Verwendung von Viskosefasern mit sternförmigen und tri- bzw. multilobalen Profilen in Windeln und Tampons wird aufgrund ihrer Hohlraumstruktur bei gleichem Fasereinsatz eine um 30 bis 40 % vergrößerte Saugfähigkeit gegenüber Normaltyp- bzw. Baumwollfasern erreicht.[25] Werden in Vliesstoffen Viskosefasern mit einem flachen Querschnitt und gewellter Oberfläche eingesetzt, so können diese Fasern bei Kontakt mit größeren Mengen Wasser aufbrechen und damit die Spülbarkeit (Flushability) daraus hergestellter Disposables verbessern und deren umweltgerechte Entsorgung gewährleisten.[26][27]
Viskose-Hohlfasern
Wenn in die Viskoselösung Natriumcarbonat hinzugefügt wird, entwickelt sich beim Kontakt des Spinnstrahls mit dem sauren Spinnbad gasförmiges Kohlendioxid: Verbunden mit den normalen Gasen, die im Spinnprozess freigesetzt werden, entsteht genügend Druck, um den Mantel des sich bildenden Filaments aufzublähen. Es entsteht ein durchgehender Hohlraum in Längsrichtung des Filaments[28] Die so entstehenden Fasern sind weicher und fülliger als Normaltypen und haben eine verbesserte Wärmeisolation.[29] Es existieren auch Hohlfasern mit einer Segmentierung in Längsrichtung aufgrund von membranartigen Trennwänden. Die Querschnittsstruktur solcher Fasern liegt im trockenen Zustand kollabiert vor, aber bei Kontakt mit Flüssigkeit quellen diese Fasern auf. Die Flüssigkeit wird in den Hohlräumen gespeichert. Die Quellung ist reversibel. Eingelagertes Wasser wird als Luftfeuchtigkeit ausgetragen. Diese Art Hohlfasern werden in Filtermaterialien und in Hygieneprodukten eingesetzt.[30][31]
Schwerentflammbare Viskosefasern
Eine Schwerentflammbarkeit von Viskosefasern ist durch Zugabe von flammhemmenden Substanzen zur Viskoselösung relativ einfach möglich. Solche Flammschutzmittel sind z. B. Phosphorsäureester, Phosphate oder Phosphonate. Wenn sie als fein zerteilte Pulver oder polymere Flüssigkeiten zu 18 – 25 % in die Viskose (bezogen auf die Zellulosemasse) zugegeben werden, können ausreichende Flammschutzeigenschaften für die aus solchen Fasern hergestellten Gewebe gewährleistet werden.[32] Die schwerentflammbaren Viskosefasern weisen einen optimalen Tragekomfort auf. Rein oder in Mischung mit z, B. Aramid-, Kermel- oder PBI-Fasern können sie zu Flammschutzbekleidung, Vorhangstoffen oder Sitzbezügen in öffentlichen Verkehrsmitteln verarbeitet werden.[33] Die Einlagerung der Flammschutzmittel in der Faser hat den Vorteil, dass die Schwerentflammbarkeit der daraus hergestellten Textilien auch nach vielen Wäschen erhalten bleibt.[34]
Farbfeste spinngefärbte Viskosefasern
Die Veredlung von Textilien kann vereinfacht werden, wenn die Fasern bereits während der Herstellung gefärbt werden. Dazu können Farbstoffe der Viskosespinnmasse beigemischt werden. Als Farbstoffe eignen sich anorganische und organische Pigmente (z. B. Azopigmente), die in der Viskose und im Spinnbad sowie in den Wasch- und Bleichbädern unlöslich und beständig sein müssen. Mit den Pigmentfarbstoffen kann eine breite Palette leuchtender, kräftiger Farbtöne erzielt werden.[35]
Hochfeste Viskosefilamente
Hochfeste Viskosefilament werden durch ein modifiziertes Spinnverfahren mit „gebremster“ Koagulation im Fällbad und stärkerem Verstrecken der koagulierten Fäden erreicht. Es entsteht dadurch ein hoher Orientierungsgrad der Cellulosemoleküle längs der Faserachse.[36] Die Festigkeit liegt dadurch gegenüber normalen Viskosefilamenten zwei- bis dreifach höher, die Reißdehnung im trockenen Zustand mit 12 bis 17 % niedriger als die der Normalviskose. Die hochfesten Viskose–Filamentgarne sind beständig gegenüber Bremsflüssigkeiten und können deshalb für die Bremsschlauchherstellung verwendet werden.[37] Sehr bedeutend sind diese Filamente als Reifencord und als Verstärkungsfasern in PP-Compounds.
Hochnassfeste Viskosefasern
Eine veränderte Spinnlösung (z. B. weniger gereift, Modifizierzusätze) und mehr Zinksulfat im Fällbad ermöglichen die Herstellung hochnassfester Fasern. Zudem werden die Filamente bei niedrigere Spinngeschwindigkeit ersponnen und stärker verstreckt als Normalviskosefilamente. Die dadurch entstandenen Vollmantelfasern besitzen eine höhere Festigkeit bei geringerem Quellwert. Eine Anwendung sind Verstärkungen in Fördergurten.[38] Diese hochnassfesten Viskosefaser–Typen waren auch die Vorläufer der Modalfasern.[39]
Verwandte Produkte
Ebenso wie die Viskosefasern zählen die Modal-, Lyocell- und Cuprofasern zu den Regeneratcellulosefasern. Sie bestehen zu 100 Prozent aus Cellulose II (siehe Einleitung).
Modalfaser
Modalfasern (Kurzzeichen: CMD)[40][41] sind strukturmodifizierte Viskosefasern mit einem höheren Polymerisationsgrad (über 400 bis 700) als die normale Viskosefaser. Die Modifizierung erfolgt durch veränderte Spinnbedingungen, veränderte Fällbäder und Zugabe von Spinnhilfsmitteln. Die Dehnung von Modalfasern muss bei einer Zugbelastung von 22,5 cN/tex im nassen Zustand unter 15 % bleiben, was von normalen und auch zahlreichen hochfesten Viskosefasern nicht erreicht wird.[42] Anders als andere Regeneratfasern wird der für die Herstellung verwendete Zellstoff hauptsächlich aus Buchenholz gewonnen.[43][44][45] Modalfasern wurden als PN-Typen (Polynosic) bzw. als HWM-Typen (High Wet Modulus) entwickelt.[46][47] Diese ähneln besonders der Baumwolle, im Gegensatz zu Normalviskosefasern, die geringere Haltbarkeit und höheres Schrumpfverhalten aufweisen.[48] Modalfasern geben damit Bekleidungs- und Heimtextilien, auch im nassen Zustand, eine hohe Dimensionsstabilität.[49] Während die HWM-Typen eine höhere Bruchdehnung und Querfestigkeit besitzen, sind Polynosic-Fasern alkalibeständiger, was ihre Merzerisation gemeinsam mit Baumwolle ermöglicht. Modalfasern weisen außerdem gegenüber Normalviskosefasern höhere Schlingen- und Scheuerfestigkeit auf. Polynosic-Fasern werden heute hauptsächlich in China, HWM-Typen meist in Europa produziert.[50]
Lyocellfaser
Die Fasern der Gattung Lyocell (Kurzzeichen: CLY)[51] (Handelsname z. B. TENCEL) werden durch ein Lösungsmittelspinnverfahren hergestellt, bei welchem die Cellulose direkt ohne Ausbildung eines Derivates in einem organischen Lösungsmittel aufgelöst und die Lösung versponnen wird. Als organisches Lösungsmittel im kommerziellen Maßstab wird NMMO (N-Methylmorpholin-N-oxid) eingesetzt,[52] das nicht toxisch ist. Der Herstellungsprozess für Lyocellfasern zeichnet sich im Vergleich zur Viskosefaser-Technologie durch eine hervorragende Umweltverträglichkeit aus. Als Cellulose wird meistens Holzzellstoff verwendet.[53]
Die Lyocellfasern übertreffen in den Festigkeiten (trocken und nass), im Nassmodul und damit in der Dimensionsstabilität daraus hergestellter Flächengebilde die Standardtypen aller anderen Cellulose-Regeneratfasern, weisen aber auch denen gegenüber eine geringere Dehnung aus. Die textilen Eigenschaften sind vergleichbar mit denen langstapeliger Baumwolle. Der NMMO-Prozess ermöglicht auch durch Zugabe von Additiven in die Spinnlösung, bioaktive, absorbierende oder thermoregulierende Lyocellfasern zu erzeugen.[54]
Cuprofasern
Als Ausgangsstoff für die Herstellung von Cuprofasern (Kurzzeichen: CUP)[55] werden in Cuoxam gelöste kurzfaserige Baumwolle, Baumwolllinters oder Edelcellulose (hoher Anteil Alphacellulose) verwendet. Die durch den Lösungsprozess entstehende viskose Masse (sog. Blaumasse) wird nach dem Nassspinnverfahren im Fällbad zu Cuprofilamenten ersponnen. Die Eigenschaften sind denen der Normalviskose ähnlich, nur die Nassbruchdehnung ist höher. Der seidige Glanz (Ursprung der Bezeichnung Kunstseide) ist im Bekleidungssektor, aber auch bei technischen Textilien gefordert. Die Cuprofasern haben trotzdem nur noch eine geringe wirtschaftliche Bedeutung.[56][57][58]
Gebrauchs- und Trageeigenschaften
Die Eigenschaften der Viskosefasern variieren aufgrund strukturändernder Maßnahmen (z. B. Modifizierzusätze, Querschnittsänderungen etc.) in einem breiten Bereich, so liegt die feinheitsbezogene Reißkraft im trockenen Zustand z. B. zwischen 16 und 70 cN/tex und die Wasserquellung zwischen 45 und >300 %.[59] Die Feuchtigkeitsaufnahme der Viskosefaser liegt zwischen 11 % bis 14 % im Normalklima und übertrifft damit die der Baumwolle, deshalb verfügt sie über gute hygienische Eigenschaften (z. B. Schweißaufnahmefähigkeit) und lässt sich hervorragend färben und bedrucken. Das hohe Wasserrückhaltevermögen führt allerdings zu relativ langen Trockenzeiten. Die Viskosefaser ist temperaturausgleichend und hautsympathisch. Risiken zur Hautirritation entstehen daher gegebenenfalls aufgrund des Färbens oder der Ausrüstung der Faser.
Aus Viskosefasern hergestellte Stoffe besitzen einen weichen, fließenden Fall (Fall – vgl. Hinweis bei Drapierbarkeit). Die hohe Flüssigkeitsaufnahme bewirkt allerdings auch, dass die Nassreißfestigkeit nur 45 bis 65 % der Trockenreißfestigkeit (mittlerer Wert zwischen 20 und 24 cN/tex) erreicht. Hier liegt ein wesentlicher Unterschied zur Baumwolle vor, deren Nassreißfestigkeit höher als die Trockenreißfestigkeit ist. Ob es sich bei einer Faser um Viskose oder Baumwolle handelt, kann durch einen einfachen Handtest festgestellt werden. Man feuchtet dazu den zum Test herangezogenen Garnabschnitt in der Mitte an. Wenn bei Zug an den Enden das Garnstück im Bereich des feuchten Abschnittes reißt, handelt es sich um ein Viskosegarn.
Die mittlere Reißdehnung im trockenen Zustand beträgt 20 bis 25 %, im nassen Zustand sogar 25 bis 30 %. Da Viskose eine geringe Elastizität aufweist, knittert sie stark. Ihre Scheuerfestigkeit ist im trockenen Zustand gering und im nassen Zustand sehr gering, weshalb starke mechanische Beanspruchungen vermieden werden sollten. Die Säuren- und Laugenbeständigkeit ist relativ schlecht. Im feuchten Zustand ist sie empfindlich gegenüber Mikroorganismen, was zu Stockflecken führt.[60][61]
Verwendung
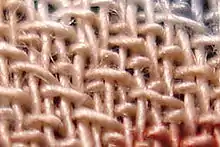
Die Verwendung von Viskosefasern ähnelt wegen der gemeinsamen Basis Cellulose und den damit verbunden bekleidungsphysiologischen Eigenschaften der von Baumwollfasern. Wegen viel größerer Variationsmöglichkeit der Fasergeometrie (Länge, Kräuselung, Feinheit, Querschnittsform) übertrifft sie aber in vielen Anwendungseigenschaften die von Baumwollfasern. Bedeutend für die Verarbeitung und damit für die Verwendung ist auch, dass aus Viskose nicht nur Spinnfasern wie bei Baumwolle zur Verfügung stehen, sondern Filamente (Endlosfasern) hergestellt werden können.
- Beispiele für die Verwendung im Bekleidungs- und Heimtextiliensektor sind:[62]
- Garne aus 100 % Viskose-Spinnfasern oder in Mischung mit Baumwoll-, Woll-, Polyester- oder Polyacrylnitrilfasern werden
- zu Stoffen für Oberbekleidung, wie Kleider, Blusen, Hemden, Anzüge und Mäntel,
- wegen ihrer hohen Saugfähigkeit auch zu Stoffen für Unterbekleidungsartikel,
- zu Deko- und Möbelstoffen sowie Stoffen für Bett- und Tischwäsche verarbeitet.
- Viskose-Filamentgarne werden insbesondere für Kleider-, Blusen- und Rockstoffe sowie für Futterstoffe verwendet, wobei die Stoffe vorrangig Gewebe, aber auch Strick- und Wirkwaren sind
- Viskose-Kurzfasern (Faserlänge 0,5 bis 1 mm) finden zum Beflocken von z. B. T-Shirts mit plastischen Motiven Anwendung
- In Mischung mit Polyesterfasern werden Viskosefasern auch im Bekleidungssektor für näh- und fixierbare Einlagevliesstoffe genutzt
- Garne aus 100 % Viskose-Spinnfasern oder in Mischung mit Baumwoll-, Woll-, Polyester- oder Polyacrylnitrilfasern werden
- Beispiele für die Verwendung in Medizin- und Hygieneprodukten sind:[63]
- Verbands- und Kompressionsmaterialien wie Verbandmull aus leinwandbindigen Viskosefasergarn-Geweben, Viskosefaser-Verbandwatte, Viskosefaservliesstoffe für Kompressions- und Saugkissenfertigung, Viskosefaservliesstoffe als Sekretverteilschicht (Acquisitionlayer) in mehrlagigen Saugkompressen, Mullbinden aus Viskosefasergarn-Geweben für Fixierbinden sowie rundgestrickte, quer- und längselastische Trikot-Schlauchverbände aus Viskosefasergarnen
- Krankenhaustextilien wie mehrlagige Matratzenauflagen mit Viskosefaser/Baumwollfaser-Frottiergewirken als Saugschicht, bindemittelverfestigte Viskosefaser-Vliesstoffe als Saugschicht in mehrlagigen OP-Abdecktüchern, wasserstrahlverfestigte Polyester-/Viskosefaser-Vliesstoffe als OP-Mäntel
- Hygiene- und Körperpflegeprodukte wie
- Trocken- und Feucht-Reinigungstücher aus unterschiedlich verfestigten Vliesstoffen (zunehmend durch Verfestigung mit Wasserstrahlen; auch als Spunlace-Vliesstoffe bezeichnet) auf Basis von 100 % Viskosefasern oder Mischungen mit Polyesterfasern oder defibrillierten Zellstoff
- Saugkerne von Tampons, die aus Streifen von Nadel- oder wasserstrahlverfestigten Vliesstoffen hergestellt werden, wobei zur Erhöhung der Saugkraft 100 % querschnittsmodifizierte (multilobale) Viskosefasern verwendet werden können
- Wattestäbchen
- Beispiele für technische Anwendungen sind:
- die aus nach einem Spezialspinnverfahren erzeugten Hochfest-Viskosefilamenten (Viscosecord) gefertigten Cordgewebe als Radialkarkassen im Reifenbau, Schläuche, wie für Kraftstoff- und Schmieröle in Autos, Gewebe für Förderbänder sowie Kordeln und Schnüre[64]
- Hochfest-Viskosefilamente, aber auch geschnitten als Kurzfasern zur Verstärkungfasern in PP-Compounds, die durch Spritzguss, Extrusion oder Fließpressen verarbeitet werden (z. B. für Bauteile im Kfz-Innenraum[65])
- bindemittelverfestigte Viskosfaservliesstoffe als Filtermaterialien in der Flüssigfiltration (Abwasser, Kühlschmierstoffe, Milch)
- Teebeutel und Papier für Banknoten
Hersteller
Das Xanthogenat-Verfahren zur Viskoseherstellung stammt von Edward John Bevan und Charles Frederick Cross (1892), die dies auch industriell umsetzten. Für die Umsetzung der Patente in Deutschland, Frankreich und den USA entstand das Viscose Spinning Syndicate, in Großbritannien übernahm Courtaulds die Verwertung.
Seit 1908/09 produzierte Hugo Küttner in Pirna bei Dresden Kunstseide, zuerst nach dem Chardonnet-Verfahren und ab 1910 nach dem Viskose-Patent. 1911 gesellte sich dazu die 1899 von Max Fremery und Johann Urban gegründete Vereinigte Glanzstoff-Fabriken AG mit Sitz in Elberfeld (heute zu Wuppertal), die schon im Jahr davor die „Fürst Guido Donnersmarckschen Kunstseiden- und Acetatwerke“ in Sydowsaue bei Stettin und anschließend deren Viskose-Patente übernommen hatte, um sie weiter zu vervollkommnen.[66]
Der weltgrößte Viskose-Produzent ist heute die indische Grasim Industries, derweil die größten Viskose-Produktionsstraßen heute von der indonesischen South Pacific Viscose in Purwakarta (Indonesien) mit einer Tagesleistung von rund 150 Tonnen sowie von der österreichischen Lenzing AG mit fast 170 Tonnen täglich betrieben werden. Letztere kann dabei für sich beanspruchen, der weltgrößte Hersteller zellulosischer Fasern überhaupt, also von Viskose-, Modal- und Tencel- bzw. Lyocellfasern zusammengenommen, zu sein.
Weitere wichtige europäische Unternehmen auf dem Viskose-Sektor sind z. B. die deutsche Kelheim Fibres als weltgrößter Viskose-Spezialfaser-Hersteller, die ebenfalls deutsche Cordenka mit Sitz im Industrie Center Obernburg als weltgrößter Hersteller hochfester Viskose-Fasern zur Produktion u. a. von Karkassen und Reifencord sowie die deutsche Enka in Wuppertal als größter europäischer Hersteller textiler Viskose-Filament-Garne. Ein weiterer großer Hersteller von Filament-Viskose ist die Firma Glanzstoff Industries (vormals Glanzstoff Austria) mit Produktionsstandort Lovosice in der Tschechischen Republik.
Literatur zur Geschichte der Viskose
- Lars Bluma: „L'ersatz ist kein Ersatz“ – Das Schaffen von Vertrauen durch Technikvermittlung am Beispiel der deutschen Zellwolle. In: Lars Bluma, Karl Pichol, Wolfhard Weber (Hrsg.): Technikvermittlung und Technikpopularisierung. Historische und didaktische Perspektiven. Waxmann, Münster 2004, ISBN 3-8309-1361-3, S. 121–142.
- Lars Bluma: Stoffgeschichte: Zellwolle, Mode und Modernität 1920–1945. In: Elisabeth Hackspiel-Mikosch, Birgitt Borkopp-Restle (Hrsg.): Intelligente Verbindungen. Band 1: Wechselwirkungen zwischen Technik, Textildesign und Mode. (online auf: intelligente-verbindungen.de), abgerufen am 29. Dezember 2011.
- Hans Dominik: Vistra, das weiße Gold Deutschlands. Die Geschichte einer weltbewegenden Erfindung. Koehler & Amelang, Leipzig 1936, DNB 572897405.
- Kurt Götze: Kunstseide und Zellwolle nach dem Viskose-Verfahren. Springer, Berlin 1940, DNB 573503486.
- Jonas Scherner: Zwischen Staat und Markt. Die deutsche halbsynthetische Chemiefaserindustrie in den 1930er Jahren. In: Vierteljahrschrift für Sozial- und Wirtschaftsgeschichte. 89, Nr. 4, 2002, S. 427–448.
- Kurt Ramsthaler: Der Chemiewerker in der Zellwolle- und Kunstseidefabrik (Viskoseverfahren): Ein Hilfsbuch für Chemiewerker, Vormänner und Schichtmeister. Band 2: Von der Spinnlösung zum Fertigprodukt. Konradin-Verlag, Berlin 1941, DNB 453910629.
Weblinks
Einzelnachweise
- Hans-J. Koslowski: Chemiefaser–Lexikon. 12., erweiterte Auflage. Deutscher Fachverlag, Frankfurt am Main 2009, ISBN 978-3-87150-876-9, S. 242.
- Thomas Lange, Wolfgang Quednau: Kommentar zur europäischen Textilkennzeichnungsverordnung. Deutscher Fachverlag, Frankfurt am Main 2014, ISBN 978-3-86641-278-1, S. 59.
- W. Burchard: Polysaccharide – Eigenschaften und Nutzung. Springer-Verlag, 1985, ISBN 3-540-13931-1, S. 92.
- Thomas Gries, Dieter Veit, Burkhardt Wulfhorst: Textile Fertigungsverfahren – Eine Einführung. 2., überarbeitete und erweiterte Auflage. Carl Hanser Verlag, München 2014, ISBN 978-3-446-44057-9, S. 57.
- Walter Roggenstein: Viscose Fibres With New FunctionalsQualities. In: Lenzinger Berichte. 89, 2011, S. 72–75.
- Ursula Völker, Katrin Brückner: Von der Faser zum Stoff – Textile Werkstoff- und Warenkunde. 35., aktual. Auflage. Verlag Dr. Felix Büchner, Hamburg 2014, ISBN 978-3-582-05112-7, S. 61f.
- Walter Loy: Chemiefasern für technische Textilprodukte. 2., grundleg. überarb. und erweit. Auflage. Deutscher Fachverlag, Frankfurt am Main 2008, ISBN 978-3-86641-197-5, S. 25.
- Siegfried Hauptmann: Organische Chemie. 2., durchgesehene Auflage. Deutscher Verlag für Grundstoffindustrie, Leipzig 1985, ISBN 3-342-00280-8, S. 652.
- W. Burchard: Polysaccharide – Eigenschaften und Nutzung. Springer-Verlag, 1985, ISBN 3-540-13931-1, S. 91–93.
- Dong Zhang (edit.): Advances in Filament yarn spinning of textiles and polymers. Woodhead Publishing, Cambridge 2014, ISBN 978-0-85709-499-5, S. 177f.
- Zakhar Aleksandrovič Rogowin: Chemiefasern: Chemie – Technologie. Georg Thieme Verlag, Stuttgart/ New York 1982, ISBN 3-13-609501-4, S. 80f.
- Zakhar Aleksandrovič Rogowin: Chemiefasern: Chemie – Technologie. Georg Thieme Verlag, Stuttgart/ New York 1982, ISBN 3-13-609501-4, S. 90.
- Menachem Lewin (Hrsg.): Handbook of Fiber Chemistry. 3. Auflage. Taylor & Francis Group, Boca Raton 2007, ISBN 978-0-8247-2565-5, S. 741.
- Alfons Hofer: Stoffe. Teil 1: Rohstoffe: Fasern, Garne und Effekte. 8., vollst. überarb. und erweit. Auflage. Deutscher Fachverlag, Frankfurt am Main 2000, ISBN 3-87150-671-0, S. 151.
- Alfons Hofer: Stoffe. Teil 1: Rohstoffe: Fasern, Garne und Effekte. 8., vollst. überarb. und erweit. Auflage. Deutscher Fachverlag, Frankfurt am Main 2000, ISBN 3-87150-671-0, S. 172.
- Ursula Völker, Katrin Brückner: Von der Faser zum Stoff – Textile Werkstoff- und Warenkunde. 35., aktualisiert Auflage. Verlag Dr. Felix Büchner, Hamburg 2014, ISBN 978-3-582-05112-7, S. 60.
- Thomas Gries, Dieter Veit, Burkhardt Wulfhorst: Textile Fertigungsverfahren – Eine Einführung. 2., überarb. und erweit. Auflage. Carl Hanser Verlag, München 2014, ISBN 978-3-446-44057-9, S. 59.
- Menachem Lewin (Hrsg.): Handbook of Fiber Chemistry. 3. Auflage. Taylor & Francis Group, Boca Raton 2007, ISBN 978-0-8247-2565-5, S. 742.
- Rogowin, Zakhar Aleksandrovič: Chemiefasern: Chemie – Technologie. Georg Thieme Verlag, Stuttgart/ New York 1982, ISBN 3-13-609501-4, S. 145.
- Ursula Völker, Katrin Brückner: Von der Faser zum Stoff – Textile Werkstoff- und Warenkunde ,35., aktualisiert Auflage. Verlag Dr. Felix Büchner. Hamburg 2014, ISBN 978-3-582-05112-7, S. 60.
- Hans-Karl Rouette: Handbuch Textilveredlung – Technologie, Verfahren und Maschinen. Band I, Deutscher Fachverlag, Frankfurt am Main 2003, ISBN 3-87150-728-8, S. 414.
- Zakhar Aleksandrovič Rogowin: Chemiefasern: Chemie – Technologie. Georg Thieme Verlag, Stuttgart/ New York 1982, ISBN 3-13-609501-4, S. 140.
- Menachem Lewin (Hrsg.): Handbook of Fiber Chemistry. 3. Auflage. Taylor & Francis Group, Boca Raton 2007, ISBN 978-0-8247-2565-5, S. 746.
- Philipp Wimmer: Viskose-Spezialfasern für Filtrationsanwendungen. In: F & S Filtrieren und Separieren. Jahrgang 28, Nr. 1, 2014, S. 14–21, Abgerufen am 9. Februar 2018].
- Walter Loy: Textile Produkte für Medizin, Hygiene und Wellness. Deutscher Fachverlag, Frankfurt am Main 2006, ISBN 3-87150-913-2, S. 106 f.
- Walter Loy: Chemiefasern für technische Textilprodukte. 2., grundl. überarb. und erweit. Auflage. Deutscher Fachverlag, Frankfurt am Main 2008, ISBN 978-3-86641-197-5, S. 26.
- Calvin Woodings (edit.): Regenerated cellulose fibres. Woodhead Publishing, Cambridge 2001, ISBN 1-85573-459-1, S. 252.
- V. B. Gupta, V. K. Kothari: Manufactured Fibre Technology. Chapman & Hall, London 1997, ISBN 0-412-54030-4, S. 499.
- Fabia Denninger, Elke Giese: Textil- und Modelexikon. Band 1: A –K. 8., vollst. überarb. und erweit. Auflage. Deutscher Fachverlag, Frankfurt am Main 2006, ISBN 3-87150-848-9, S. 316.
- Philipp Wimmer: Viskose-Spezialfasern für Filtrationsanwendungen. In: F & S Filtrieren und Separieren. Jahrgang 28, Nr. 1, 2014, S. 14–21, Abgerufen am 31. März 2018.
- depatisnet.dpma.de „EP 2 459 782A Regenerierte Cellulosefaser“ (angemeldet am 9. Juli 2010)
- Menachem Lewin (Hrsg.): Handbook of Fiber Chemistry. 3. Auflage. Taylor & Francis Group, Boca Raton 2007, ISBN 978-0-8247-2565-5, S. 762.
- Walter Loy: Chemiefasern für technische Textilprodukte. 2., grundleg. überarb. und erweit. Auflage. Deutscher Fachverlag, Frankfurt am Main 2008, ISBN 978-3-86641-197-5, S. 26.
- Ursula Völker, Katrin Brückner: Von der Faser zum Stoff – Textile Werkstoff- und Warenkunde. 35., aktualisiert Auflage. Verlag Dr. Felix Büchner. Hamburg 2014, ISBN 978-3-582-05112-7, S. 62.
- Zakhar Aleksandrovič Rogowin: Chemiefasern: Chemie – Technologie. Georg Thieme Verlag, Stuttgart/ New York 1982, ISBN 3-13-609501-4, S. 141.
- Walter Loy: Chemiefasern für technische Textilprodukte. 2., grundleg. überarb. und erweit. Auflage. Deutscher Fachverlag, Frankfurt am Main 2008, ISBN 978-3-86641-197-5, S. 27.
- Walter Loy: Chemiefasern für technische Textilprodukte. 2., grundleg. überarb. und erweit. Auflage. Deutscher Fachverlag, Frankfurt am Main 2008, ISBN 978-3-86641-197-5, S. 84/85.
- Ursula Völker, Katrin Brückner: Von der Faser zum Stoff – Textile Werkstoff- und Warenkunde. 35., aktualisiert Auflage. Verlag Dr. Felix Büchner. Hamburg 2014, ISBN 978-3-582-05112-7, S. 61.
- Hans-J. Koslowski: Chemiefaser – Lexikon. 12., erweiterte Auflage. Deutscher Fachverlag, Frankfurt am Main 2009, ISBN 978-3-87150-876-9, S. 142.
- DIN EN ISO 2076, Ausgabe März 2014: Textilien – Chemiefaser – Gattungsnamen, S. 8.
- Modalfasern auf materialarchiv.ch, abgerufen am 3. März 2017.
- Hans-J. Koslowski: Chemiefaser – Lexikon . 12., erweiterte Auflage. Deutscher Fachverlag, Frankfurt am Main 2009, ISBN 978-3-87150-876-9, S. 142.
- Modal – alle Fakten zu der modernen Wohlfühlfaser. (bonprix.de [abgerufen am 26. Juli 2017]).
- Menachem Lewin 1918-, Eli M. Pearce: Handbook of fiber chemistry. 2., überarbeitete und erweiterte Auflage. Marcel Dekker, New York 1998, ISBN 978-0-8247-9471-2.
- Technische Universität Graz - Faserarten. (PDF) 22. Februar 2016, abgerufen am 26. Juli 2017.
- Herbert M. Ulrich: Handbuch der chemischen Untersuchung der Textilfaserstoffe. Springer, 1968, ISBN 978-3-7091-7968-0, S. 816.
- A. Ernst: Die verschiedenen Einsatzmöglichkeiten von Modalfasern. In: Lenzinger Berichte. 52, 1982, online (PDF; 865 kB), auf lenzing.com, abgerufen am 3. März 2017.
- Calvin Woodings (Hrsg.): Regenerated cellulose fibres. Woodhead Publishing Ltd., Cambridge 2001, ISBN 1-85573-459-1, S. 248.
- Walter Loy: Chemiefasern für technische Textilprodukte. 2., grundlegend überarbeitete und erweiterte Auflage. Deutscher Fachverlag, Frankfurt am Main 2008, ISBN 978-3-86641-197-5, S. 27.
- Hans-J. Koslowski: Chemiefaser – Lexikon. 12., erweiterte Auflage. Deutscher Fachverlag, Frankfurt am Main 2009, ISBN 978-3-87150-876-9, S. 142.
- DIN EN ISO 2076 , Ausgabe März 2014: Textilien – Chemiefaser - Gattungsnamen, S. 7.
- Österreichische Gebrauchsmusterschrift AT 006 807 U1: Cellulosische Faser der Gattung Lyocell. Gebrauchsmusterinhaber: Lenzing Aktiengesellschaft, Ausgabetag: 26. April 2004, S. 2.
- Hans-J. Koslowski: Chemiefaser – Lexikon. 12., erweiterte Auflage. Deutscher Fachverlag, Frankfurt am Main 2009, ISBN 978-3-87150-876-9, S. 127 f.
- Walter Loy: Chemiefasern für technische Textilprodukte. 2., grundlegende überarbeitet und erweiterte Auflage. Deutscher Fachverlag, Frankfurt am Main 2008, ISBN 978-3-86641-197-5, S. 28 f.
- DIN EN ISO 2076 , Ausgabe März 2014: Textilien – Chemiefaser - Gattungsnamen, S. 7.
- Walter Loy: Chemiefasern für technische Textilprodukte. 2., grundlegende überarbeitet und erweiterte Auflage. Deutscher Fachverlag, Frankfurt am Main 2008, ISBN 978-3-86641-197-5, S. 30.
- Hans-J. Koslowski: Chemiefaser – Lexikon. 12., erweiterte Auflage. Deutscher Fachverlag, Frankfurt am Main 2009, ISBN 978-3-87150-876-9, S. 57.
- Menachem Lewin (Hrsg.): Handbook of Fiber Chemistry. 3. Auflage. Taylor & Francis Group, Boca Raton 2007, ISBN 978-0-8247-2565-5, S. 708.
- Hans-J. Koslowski: Chemiefaser – Lexikon . 12., erweiterte Auflage. Deutscher Fachverlag, Frankfurt am Main 2009, ISBN 978-3-87150-876-9, S. 242.
- Ursula Völker, Katrin Brückner: Von der Faser zum Stoff – Textile Werkstoff- und Warenkunde ,35., aktualisiert Auflage. Verlag Dr. Felix Büchner. Hamburg 2014, ISBN 978-3-582-05112-7, S. 67 f.
- Fabia Denninger, Elke Giese: Textil- und Modelexikon. 8., vollständig überarbeitete und erweiterte Auflage. Deutscher Fachverlag GmbH, Frankfurt am Main 2006, Bd. L – Z, ISBN 3-87150-848-9, S. 762.
- Walter Loy: Die Chemiefasern – ihr Leistungsprofil in Bekleidungs- und Heimtextilien. Fachverlag Schiele & Schön, Berlin 1997, ISBN 3-7949-0618-7, S. 37–41.
- Walter Loy: Textile Produkte für Medizin, Hygiene und Wellness. Deutscher Fachverlag, Frankfurt am Main 2006, ISBN 3-87150-913-2.
- Walter Loy: Chemiefasern für technische Textilprodukte. 2., grundleg. überarbeit. und erweit. Auflage. Deutscher Fachverlag, Frankfurt am Main 2008, ISBN 978-3-86641-197-5, S. 84 f.
- Walter Loy: Chemiefasern für technische Textilprodukte. 2., grundleg. überarbeit. und erweit. Auflage. Deutscher Fachverlag, Frankfurt am Main 2008, ISBN 978-3-86641-197-5, S. 182.
- deutsches-strumpfmuseum.de: Kunstseide (Memento des Originals vom 29. August 2010 im Internet Archive) Info: Der Archivlink wurde automatisch eingesetzt und noch nicht geprüft. Bitte prüfe Original- und Archivlink gemäß Anleitung und entferne dann diesen Hinweis.