Feuerverzinken
Das Feuerverzinken ist ein Verfahren, um Stahl vor Korrosion (Rost) zu schützen. Durch Feuerverzinken wird ein metallischer Zinküberzug auf Eisen oder Stahl durch Eintauchen in geschmolzenes Zink oder eine Zinklegierung (bei etwa 450 °C) aufgebracht. Dabei bildet sich an der Berührungsfläche eine widerstandsfähige intermetallische Phase aus Eisen und Zink (und ggf. weiteren Legierungsbestandteilen der Zinkschmelze, z. B. Aluminium oder Magnesium) und darüber eine sehr fest haftende reine Zinkschicht. Feuerverzinken ist eine von mehreren Verzinkungsmethoden. Bei der Feuerverzinkung wird zwischen (diskontinuierlicher) Stückverzinkung und (kontinuierlicher) Bandverzinkung unterschieden. Sowohl das Stückverzinken als auch das Bandverzinken sind genormte Verfahren. Das Stückverzinken ist in EN ISO 1461 geregelt und das Bandverzinken von Blechen in EN 10143 und EN 10346.
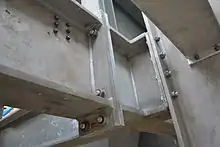
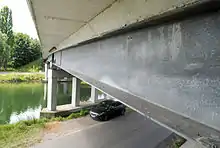
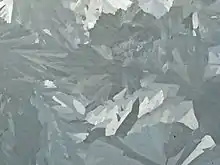
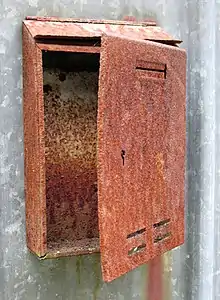
Kontinuierlich verzinkter Stahl ist ein Vorprodukt (Halbzeug), das nach dem Verzinken durch Umformen, Stanzen und Zuschneiden weiterverarbeitet wird. Hierdurch wird an den Schnitt- und Stanzkanten die schützende Zinkschicht zerstört. Im Gegensatz dazu werden bei den diskontinuierlichen Feuerverzinkungsverfahren des Stückverzinkens Bauteile wie zum Beispiel Treppenkonstruktionen oder Fahrwerkskomponenten erst gefertigt und anschließend feuerverzinkt. Hierdurch sind die Bauteile rundum vor Korrosion geschützt. Stück- und Bandverzinken unterscheiden sich zudem hinsichtlich der verwendeten Zusammensetzung der Zinkschmelze sowie der Zinkschichtdicke, wodurch sich unterschiedliche Schutzdauern ergeben können. Bei der Stückverzinkung wird gemäß EN ISO 1461 eine Zinkschmelze mit einem Mindest-Zinkgehalt von 98 % verwendet. Bei der kontinuierlichen Feuerverzinkung kommen sowohl Zink-, Zink-Aluminium- als auch Zink-Aluminium-Magnesium-Schmelzen zur Anwendung. Die Überzugsdicke von kontinuierlich feuerverzinkten Band und Blechen liegt zwischen 7 und 42 Mikrometer. Die Zinkschichtdicken von stückverzinkten Stahlteilen liegen üblicherweise zwischen 50 und 150 Mikrometern.
Eigenschaften
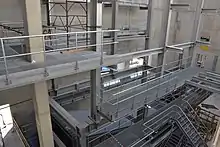
Die Zinkschicht ist im frischen Zustand in der Regel hellglänzend. Im Laufe der Zeit bildet sie infolge der Korrosion des Zinks eine Patina aus und wird in ihrem Erscheinungsbild dunkler und matter. Die Patina ist eine witterungsbeständige Schutzschicht aus Zinkoxid und Zinkcarbonat. Ist der Luft- und damit der Kohlendioxid-Zutritt beispielsweise durch nicht fachgerechte Verpackung, Lagerung oder nicht fachgerechten Transport eingeschränkt, entsteht an frisch verzinkten Bauteilen der unerwünschte Weißrost.
Eine Feuerverzinkung bietet sowohl einen aktiven als auch passiven Korrosionsschutz. Der passive Schutz erfolgt durch die Barrierewirkung des Zinküberzuges. Der aktive Korrosionsschutz entsteht aufgrund der kathodischen Wirkung des Zinküberzuges: Gegenüber edleren Metallen wie Eisen (siehe Spannungsreihe) dient Zink als Opferanode, die das darunter liegende Eisen solange vor Korrosion schützt, bis sie selbst vollständig korrodiert ist. Die anodische Wirkung schützt bis zu einer gewissen Entfernung von der angrenzenden Zinkfläche auch bloßliegende Schadstellen oder nicht verzinkte Schnittkanten. Hierdurch beschleunigen sich jedoch Korrosion und Abtrag der angrenzenden Zinkschicht selber.
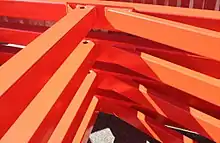
Abhängig von der Dicke des Zinküberzuges kann eine Feuerverzinkung eine unterschiedlich lange Schutzdauer erreichen. Im Stückverzinkungsverfahren hergestellte Zinküberzüge zeichnen sich durch dickere Zinkschichten als im Bandverzinkungsverfahren hergestellte Zinküberzüge aus, welche wiederum einen besseren Korrosionsschutz bieten, als galvanisch aufgetragene Zinkschichten. „Stückverzinkte“ Überzüge erreichen deshalb einen jahrzehntelangen wirtschaftlichen Korrosionsschutz ohne Wartungsaufwand. Laut der vom deutschen Bundesministerium für Verkehr, Bau und Stadtentwicklung herausgegebenen Tabelle „Nutzungsdauern von Bauteilen zur Lebenzyklusanalyse des Bewertungssystems Nachhaltiges Bauen (BNB)“[1] erreichen stückverzinkte Bauteile eine Nutzungsdauer von zumeist mehr als 50 Jahren. Hinweise zur Schutzdauer feuerverzinkter Überzüge in unterschiedlichen Korrosivitätskategorien gibt auch Tabelle 2 der EN ISO 14713-1.
Nach ISO 14713, Teil 1, Tabelle 2, Anmerkung 7 haben Zink-Aluminium-Überzüge eine höhere Korrosionsbeständigkeit als Zink-Überzüge, jedoch quantifiziert die Norm dies nicht. Die Fachliteratur zeigt, dass Zink-Aluminium-Überzüge lediglich in extrem Chlorid-reicher Umgebung, beispielsweise in Küstenbereichen mit Salzwasserkontakt, eine deutlich höhere Korrosionsbeständigkeit erreichen[2]. In ländlichen, städtischen oder industriellen Bereichen bestehen hingegen keine oder nur marginale Unterschiede zwischen den beiden Überzugsarten[3].
Die Schutzdauer einer Feuerverzinkung kann durch einen zusätzlichen Farbanstrich („Duplexsystem“) weiter verbessert werden.
Seit kurzem wird die Stückverzinkung auch unter Brandschutzaspekten eingesetzt. Ein 2019 abgeschlossenes Forschungsvorhaben der TU München hat belegt, dass durch Feuerverzinken die Feuerwiderstandsdauer von Stahl verbessert wird. Die Verbesserung des Feuerwiderstands basiert auf einer verringerten Emissivität von feuerverzinkten Stählen. Hierdurch ist eine Brandschutzdauer von 30 Minuten vielfach mit ungeschützten, feuerverzinkten Stahlkonstruktionen möglich.[4]
Stückverzinkung
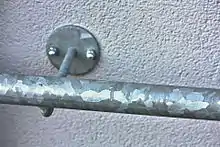
Unter Stückverzinken nach EN ISO 1461 versteht man das Feuerverzinken von (meist) größeren Stahlteilen und -konstruktionen. Dabei werden Rohlinge oder fertige Werkstücke nach einer Vorbehandlung einzeln in das Schmelzbad getaucht. Durch das Tauchen werden auch Innenflächen, Schweißnähte und unzugängliche Stellen gut erreicht.
Beispiele für Stückverzinken: Schutzplanken (Leitplanken), Geländer, Außentreppen, PKW-Anhänger, LKW-Auflieger, Teile für Stahlhallen, Stahl-Glas-Gebäude und Parkhäuser.
Verfahrensschritte beim Stückverzinken
Die nachstehend beschriebenen Verfahrensschritte stellen nur eine beispielhafte Erläuterung dar. Nach den jeweiligen betrieblichen Gegebenheiten können Abweichungen auftreten. Bei Anlagen zum Feuerverzinken von Kleinteilen können teilweise erhebliche Änderungen des Verfahrensablaufs auftreten. Das Verfahren des Dünnschichtverzinkens wird analog zum klassischen Stückverzinken, wie es den Zinküberzügen gemäß DIN EN ISO 1461 zugrunde liegt, betrieben.
Vorbereitende Arbeitsschritte
Außer in großen industriellen Anlagen (zum Beispiel Karosserieverzinkung) findet die Feuerverzinkung meist in Lohnverzinkereien statt. Hierfür muss eine grobe Oberflächenvorbehandlung durchgeführt worden sein. Die Teile müssen frei von losem Rost und alten Farben sein. Gegebenenfalls ist vorheriges Sandstrahlen erforderlich. Hohlprofile müssen angebohrt sein (10 mm und größer). Aus diesen Bohrungen müssen alle Flüssigkeiten restlos auslaufen können. Spitze Innenecken sollten ausgerundet sein.
Nach der Anlieferung der zu verzinkenden Teile in der Feuerverzinkerei und einer notwendigen Eingangsprüfung werden die Werkstücke zunächst zu Chargen möglichst gleichartiger oder ähnlicher Bauteile zusammengestellt, damit ein wirtschaftliches Verzinken möglich ist. Die Teile werden vorher oder nachher gewogen. Bei der sogenannten Schwarzverwiegung (vor der Verzinkung) wird ein vorher festgelegter Prozentsatz als Zinkannahme hinzu gerechnet. Das resultierende Gewicht geht dann in die Rechnungserstellung ein. Bei der sogenannten Weißverwiegung (nach dem Verzinkungsvorgang) wird das Endgewicht mit einem festgelegten Eckpreis (gemäß einer materialbezogenen Tarifgruppe) multipliziert. Das Produkt aus Gewicht und Tarifgruppe ergibt dann die Rechnungsendsumme zuzüglich der gültigen Mehrwertsteuer.
Eine Differenzverwiegung erfolgt meist nicht.
Entfetten/Spülen
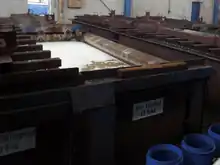
Teile, die Rückstände von Fetten und Ölen aufweisen, werden in einem Entfettungsbad gereinigt. Als Entfettungsmittel kommen üblicherweise wässrige alkalische oder saure Entfettungsmittel zur Anwendung. Nach einem alkalischen Entfettungsbad folgt ein kurzes Eintauchen in ein Wasserbad, um das Verschleppen von Entfettungsmitteln mit dem Verzinkungsgut zu vermeiden.
Bei einer sauren Entfettung wird meistens verdünnte Salzsäure als Basis verwendet. Hier kann auf das Spülen nach dem Entfetten verzichtet werden, wenn in der nachfolgenden Beize ebenfalls Salzsäure als Betriebsmedium verwendet wird.
Beizen
Der nächste Schritt ist eine Beizbehandlung zur Entfernung von arteigenen Verunreinigungen (zum Beispiel Rost und Zunder) von der Stahloberfläche. Das Beizen erfolgt üblicherweise in verdünnter Salzsäure. Die Dauer des Beizvorgangs richtet sich nach dem Verrostungsgrad des Verzinkungsgutes und der Arbeitskonzentration der Beize. Die Beizbäder werden im Regelfall bei Raumtemperatur betrieben, es können aber auch Badtemperaturen bis 40 °C vorkommen.
Spülen
Nach dem Beizen erfolgen zwei Spülvorgänge in Wasser, um die Verschleppung von Säure- und Salzresten mit dem Verzinkungsgut so weit wie möglich zu minimieren.
Beizen von verzinkten Teilen
Nach einer fehlerhaften Verzinkung oder nach einer Konstruktionsänderung an einem verzinkten Teil kann der Zinküberzug wieder entfernt werden. Dazu darf aber nicht das oben genannte Beizbad benutzt werden, sondern ein spezielles Beizbad mit verdünnter Salzsäure. Hierbei kommt es zu einer chemischen Reaktion, bei der sich Wasserstoff () bildet. Dieses Gas wird in einen Schaumfilm gebunden. Das Hantieren mit Zündquellen ist in der Nähe dieses Bades zu vermeiden, da es zur Explosion kommen kann. Die entzinkten Teile werden anschließend gefluxt und neu verzinkt.
Fluxen
Dem Spülbad schließt sich ein Flussmittelbad an. Aufgabe des Flussmittels ist es, bei der Reaktion mit dem schmelzflüssigen Zink eine letzte intensive Feinstreinigung der Stahloberfläche vorzunehmen und die Oxidhaut der Zinkoberfläche aufzulösen, sowie eine erneute Oxidation der Stahloberfläche während der Wartezeit bis zum Verzinkungsvorgang kurzzeitig zu verhindern. Ähnlich wie zum Beispiel bei Lötverbindungen, bei denen in der Regel auch Flussmittel eingesetzt werden, erhöht das Flussmittel die Benetzungsfähigkeit zwischen der Stahloberfläche und dem schmelzflüssigen Zink. Das Flussmittel besteht meistens aus einer wässrigen Lösung von Chloriden, am häufigsten einer Mischung aus Zinkchlorid (ZnCl2) und Ammoniumchlorid (NH4Cl).
Trocknen
In den meisten Fällen folgt eine Trockenstation, in der der Flussmittelfilm mittels Wärme aufgetrocknet wird. Zur Erwärmung von Entfettungsbädern und Trockenöfen wird in vielen Feuerverzinkereien die Abwärme aus der Beheizung des Verzinkungskessels mitgenutzt. Die Erwärmung / Trocknung der Bauteile hat einzig den Sinn, anhaftendes Wasser (Feuchtigkeit) zu verdunsten, so dass unerwünschte Reaktionen (Bildung von Wasserdampf) im 450 °C heißen Zink vermieden werden. Ein Entspannen der Bauteile (Vermeiden von thermischem Verzug) kann bei der vorherrschenden Trockentemperatur von max. 90 °C technisch und physikalisch nicht erfolgen.
Verzinken
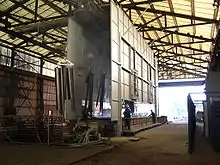
Nach der Flussmittelbehandlung bzw. dem Trocknen wird das Verzinkungsgut in die flüssige Zinkschmelze getaucht. Zink hat eine Schmelztemperatur von etwa 419 °C; die Betriebstemperatur eines Verzinkungsbades liegt in den meisten Betrieben zwischen 440 und 460 °C, in besonderen Fällen auch bei mehr als 530 °C (Hochtemperaturverzinkung). Der Zinkgehalt der Schmelze liegt gemäß EN ISO 1461 bei mindestens 98,5 %.
Nach dem Eintauchen des Verzinkungsgutes in das geschmolzene Zink verbleiben die Teile im Zinkbad, bis sie dessen Temperatur angenommen haben. Nachdem das Flussmittel nun „abgekocht“ ist, wird die Oberfläche des Zinkbades von Oxiden und Flussmittelresten gereinigt, bevor dann das Verzinkungsgut wieder aus der Zinkschmelze herausgezogen wird.
Beim Verzinkungsvorgang bildet sich als Folge einer wechselseitigen Diffusion des flüssigen Zinks mit der Stahloberfläche auf dem Stahlteil ein Überzug verschiedenartig zusammengesetzter Eisen-Zink-Legierungsschichten. Beim Herausziehen der feuerverzinkten Gegenstände bleibt auf der obersten Legierungsschicht noch eine – auch als Reinzinkschicht bezeichnete – Schicht aus Zink haften, die in ihrer Zusammensetzung der Zinkschmelze entspricht.
Abkühlen
Die Teile werden an der Luft oder im Wasserbad abgekühlt.
Verputzen oder Entgraten
Nun werden die Anschlagmittel oder auch Anbindedrähte entfernt und die sich ergebenen Klebestellen normgerecht nachgearbeitet. Sollten sich unverzinkte Stellen an den Bauteilen zeigen, so dürfen diese in engen Grenzen und nach festgelegten Regeln nachgearbeitet werden. Als maximal zulässige Größe pro Einzelfehlstelle gelten 10 cm², wobei alle an einem Bauteil befindlichen Fehlstellen in Gesamtheit der Fläche 0,5 % der Bauteiloberfläche nicht überschreiten dürfen. Die Nacharbeit kann durch Spritzverzinken oder durch eine Zinkstaubbeschichtung erfolgen. Welches der vorgenannten Verfahren zum Einsatz kommt, ist vom Bauteil und den technischen Gegebenheiten in der Verzinkerei abhängig.
In einem letzten Schritt wird das fertig verzinkte Material gewogen, da im Regelfall das verzinkte Gewicht die Basis für die Preisermittlung des Unternehmens bildet. Vor der Auslieferung wird die Güte der Feuerverzinkung kontrolliert. Bei Bedarf erfolgt noch ein Verputzen der Teile, das heißt Zinkspitzen und Unsauberkeiten auf dem Zinküberzug werden beseitigt.
Nachbehandeln
Die Anforderungen an das Aussehen der Feuerverzinkung nehmen zu. Die frisch feuerverzinkte Oberfläche soll möglichst lange den Glanz halten und nur langsam und gleichmäßig Weißrost bilden und somit länger eine hohe optische Qualität der Verzinkung bewahren. Es sind Nachbehandlungen im Sinne der DIN EN ISO 1461:1999-03 „Durch Feuerverzinken auf Stahl aufgebrachte Zinküberzüge (Stückverzinken); Anforderungen und Prüfungen“, und dem nationalen Beiblatt I, erhältlich, die den Glanz einer frisch feuerverzinkten Oberflächen länger erhalten und die Weißrostbildung verzögern. Dies verlängert den hervorragenden Qualitätseindruck einer frisch feuerverzinkten Oberfläche, erhöht die Werthaltigkeit der Oberfläche und reduziert Kundenreklamationen, die auf Weißrost und verminderten Glanz zurückzuführen sind. Vorteilhaft sind chromfreie an der Luft trocknende, wasserlösliche Tauchlacke, die in einer Tauchapplikation aufgebracht werden können. Meist sind die Nachbehandlungen auch ein ausgezeichneter Haftgrund für eine anschließende Pulverbeschichtung bzw. Nasslackierung.
Ergebnis
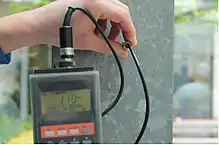
| |||
Bereich | Korrosionsschutz | ||
Titel | Durch Feuerverzinken auf Stahl aufgebrachte Zinküberzüge (Stückverzinken) – Anforderungen und Prüfungen | ||
Letzte Ausgabe | Oktober 2009 | ||
Übernahme von | ISO 1461 |
Ein wesentliches Kriterium für die Güte einer Feuerverzinkung ist die Dicke des Zinküberzuges in µm (Mikrometer, ein tausendstel Millimeter). In der Norm EN ISO 1461 „Durch Feuerverzinken auf Stahl aufgebrachte Zinküberzüge (Stückverzinken)“ (früher in Deutschland in der DIN-Norm DIN 50976 genormt) sind die Mindestwerte der geforderten Überzugsdicken angegeben, wie sie je nach Materialdicke beim Stückverzinken zu liefern sind.
Mindestschichtdicke von Zinküberzügen gemäß EN ISO 1461:
- Materialdicke 0 bis 1,5 mm: Überzugsdicke > 45 µm
- Materialdicke 1,5 bis 3,0 mm: Überzugsdicke > 55 µm
- Materialdicke 3,0 bis 6,0 mm: Überzugsdicke > 70 µm
- Materialdicke > 6,0 mm: Überzugsdicke > 85 µm
In der Praxis liegen die Schichtdicken deutlich über den in EN ISO 1461 angegebenen Mindestschichtdicken. In der Regel haben durch Stückverzinken hergestellte Zinküberzüge eine Dicke von 50 bis 150 µm.
Für Verbindungsmittel ist unabhängig von der Gewindeabmessung eine mittlere Mindestschichtdicke von 50 μm vorgesehen.[5]
Für das Dünnschichtverzinken sind folgende Werte gemäß DIN 50997 festgelegt: Als mindestens einzuhaltender Wert wird die örtliche Schichtdicke des Zink-Aluminiumüberzugs, die sich als arithmetisches Mittel mehrerer, in der Regel fünf, Einzelmessungen in einem Messbereich ergibt, auf 5 µm festgelegt. Die über das Bauteil gemittelte Schichtdicke (durchschnittliche Schichtdicke) muss mindestens 6 µm betragen.
Kleinteileverzinken
Bei kleinen Stahlteilen ist das Stückverzinken oft zu teuer. In diesem Fall werden die Kleinteile als Schüttgut in einen Metallkorb gefüllt und der Metallkorb wird komplett in das schmelzflüssige Zink eingetaucht. Gegenüber dem Stückverzinken bestehen folgende Unterschiede:
- Die Bad-Temperatur wird hierbei über 530 °C eingestellt.
- Als zusätzlicher Verfahrensschritt nach dem Verzinken werden die Kleinteile meistens durch Rotation des Metallkorbes zentrifugiert. Man spricht dann von Schleuderware.
- Durch das Zentrifugieren wird die Zink-Schichtdicke vermindert. Die Verminderung der Zink-Schichtdicke ist besonders wichtig bei Teilen mit Gewinde oder bei Teilen mit genauen Maßtoleranzen. Gewinde wären ohne das Zentrifugieren oft nicht mehr gängig.
- Die Farbe von fertig verzinkter Schleuderware ist meistens weniger hell glänzend als die Farbe von stückverzinkten Teilen, sondern eher grau. Dies ist eine Folge des Zentrifugierens, weil das Reinzink von der Oberfläche abgeschleudert wird.
Beispiele für das Kleinteileverzinken: Schrauben, Muttern und Verbindungselemente.
Wirtschaftliche Bedeutung des Stückverzinkens
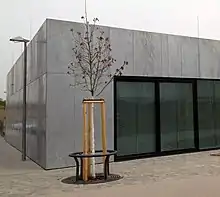
Durch Stückverzinken werden in Deutschland pro Jahr rund 1,9 Mio. Tonnen Stahl gegen Korrosion geschützt. Dies entspricht einem Umsatz von ca. 700 Mio. Euro. Rund 85 Prozent der Tonnage wird im Lohnauftrag veredelt. Zu den Kunden von Feuerverzinkereien zählen vor allem Stahl- und Metallbauunternehmen, Serienteilehersteller und der Stahlhandel. Rund die Hälfte der feuerverzinkten Tonnage wird im Bauwesen verwendet. Weitere wichtige Verwendungsbereiche sind Industrieausrüstungen, Transportwesen, Fahrzeugbau, Landwirtschaft, Straßenausrüstung, Ver- und Entsorgung sowie Kleinteile. Typische Produkte sind Schutzplanken (Leitplanken), Balkongeländer, Treppenanlagen mit Gitterrosten, PKW-Anhänger, LKW-Auflieger, Stahlbaukonstruktionen (z. B. Stahlhallen, Moderne Stahl-Glas-Architektur, Parkhäuser).
Kontinuierliche Bandverzinkung (Sendzimirverfahren)
Die kontinuierliche Bandverzinkung ist auch unter der Bezeichnung Sendzimirverfahren (benannt nach Tadeusz Sendzimir) bekannt. Bandverzinkungsanlagen kombinieren den Prozess des Feuerverzinkens mit dem des Glühens. Sie bestehen aus einer Einlaufzone, einer Behandlungszone und einer Kühlzone.
Ausgangsmaterial ist in der Regel ungeglühtes kaltgewalztes Stahlband (0,4 bis 4 mm dick, 400 bis 1800 mm breit), das zu einem Coil (Bund) aufgewickelt ist. Die Bandlänge eines solchen Coils kann bis zu 3000 m betragen. Im Einlaufteil wird das Stahlband vom Coil abgewickelt. Zwei Abwickelhaspeln und eine Schweißmaschine ermöglichen die Herstellung von Endlosbändern, so dass die Anlage kontinuierlich gefahren werden kann.
Der eigentliche Behandlungsteil besteht aus dem Durchlaufofen, dem Schmelzbad, einer Vorrichtung zur Einstellung der Zinkauflage und der Kühlung. Dem Durchlaufofen ist bei moderneren Anlagen meist eine Reinigungssektion vorgeschaltet, die Rückstände des Kaltwalzens bzw. Korrosionsschutzöl entfernt. Der Durchlaufofen ist unterteilt in die direkte beheizte Vorwärmzone, die indirekt beheizten Reduktions- und Haltezonen, sowie die Kühlzone. In der Vorwärmzone wird das Band schnell auf etwa 450–650 °C erwärmt. Dieser Teil wird auch Oxidationszone genannt. Hier erfolgte eine oxidative Reinigung des Bandes, beispielsweise durch Abbrennen von Emulsionsrückständen aus dem Kaltwalzen. In der Reduktions- und Haltezone wird das Band weiter in einer reduzierenden Schutzgasatmosphäre (Formiergas: etwa 25 bis 28 % Wasserstoff in Stickstoff) auf etwa 800 °C erwärmt und bei dieser Temperatur gehalten. Das Band wird kontinuierlich geglüht, dabei werden durch Rekristallisation des Stahls die gewünschten mechanischen Eigenschaften des Grundwerkstoffs eingestellt. Daneben werden in der Vorwärmzone gebildete Eisenoxide reduziert. Die nachfolgende Kühlzone ist durch eine Schleuse (Rüssel) mit dem Schmelzbad verbunden. In der Kühlzone wird das Band unter Schutzgas auf eine Temperatur nahe der Schmelzbadtemperatur abgekühlt.
Das Band taucht schräg nach unten in das Schmelzbad (Badtemperatur bei Zink etwa 460 °C) ein, wird durch eine Rolle im Bad nach oben umgelenkt und verlässt das Schmelzbad wieder. Beim Austritt aus dem Bad reißt das Band eine von der Bandgeschwindigkeit abhängige Metallmenge mit sich, die weit über der gewünschten Überzugsdicke (Auflage) liegt. Das noch flüssige überschüssige Überzugsmetall wird im sogenannten Düsenabstreifverfahren mit einem gerichteten Luftstrahl aus einer breiten Flachdüse auf der Vorder- und Rückseite abgestreift. Die so einstell- und regelbare Überzugsdicke hängt von der Bandgeschwindigkeit, dem Abblasdruck und dem Düsenabstand vom Band ab (Hierzu siehe auch: Elektromagnetische Bandstabilisierung). Danach wird das Band durch Jetkühler mit Luft abgekühlt, wobei der metallische Überzug auf der Bandoberfläche erstarrt. Die dabei gebildete Kristallstruktur und deren Aussehen hängt von der Art des Überzugs und den Bedingungen des Erstarrungsvorgangs ab.
Das schmelztauchveredelte Stahlband kann bei Bedarf noch in der Feuerverzinkungsanlage nachgewalzt (dressiert), gerichtet und eventuell chemisch nachbehandelt (phosphatiert, passiviert) werden. Danach wird das Band wieder zu einem Coil aufgewickelt.
Die Bandgeschwindigkeiten in kontinuierlichen Feuerverzinkungsanlagen liegen je nach Banddicke bei bis zu 220 m/min., somit erreichen Feuerverzinkungsanlagen eine Tonnenleistung von über 2000 t verzinktem Stahlband pro Tag. Vom Aufheizen des Bandes bis zum Austauchen des Bandes aus dem flüssigen Zink muss darauf geachtet werden, dass nicht die geringsten Spuren von Sauerstoff auf das Stahlband gelangen, ansonsten benetzt das Zink die Stahloberfläche nicht und ein Verzinken ist nicht mehr möglich (Zink perlt ab). Stahlbänder können in so guter Qualität feuerverzinkt werden, dass diese sogar in Automobilen für Außenhautteile (Dach, Kotflügel, …) eingesetzt werden. Dazu wird das beschichtete Band zu einer Platine geschnitten und in mehreren Schritten tiefgezogen. Das Zink haftet so gut, dass es bei diesem Tiefziehen nicht abblättert. Das so geformte Bauteil (Kotflügel, Motorhaube, Kühlschranktüre, …) wird lackiert und verbaut.
Zinkbäder für die kontinuierliche Bandverzinkung enthalten (neben Zink) ca. 0,2 % Aluminium, um die Ausbildung einer ZnFe-Phase zu unterbinden und die Bildung von Zinkblumen zu fördern. Da ZnFe-Phasen spröde sind, würden diese beim folgenden Umformen eines verzinkten Blechs brechen, das Zink würde die Haftung verlieren und sich ablösen. Auch wird durch Aluminium die Oxidation der Oberfläche der Zinkschmelze durch Luft verlangsamt, wodurch weniger Oberflächenschlacke auf der Zinkschmelze entsteht. Zusätzlich wird durch die geringe Menge von Aluminium im Zinkbad die spätere Zink-Schicht heller und glänzender.
Galfanbäder enthalten (neben dem Zink) noch 4 bis 5 % Aluminium und geringe Mengen an Lanthan und Cer. Galfan wird heute nur mehr wenig verwendet.
Neben den obengenannten, weitgehend auf Zink basierenden Überzügen werden auch Legierungsüberzüge aus Zink, Aluminium und Magnesium, sowie stark aluminiumhaltige Überzüge die mit Zink ("Galvalume") oder Silizium ("Feueraluminiert") legiert sind, verwendet. Blei, das verhindert, dass sich eine Hartzinkschicht auf dem Boden der Wanne bildet, wird wegen der Stoffverbote in diversen EU-Richtlinien nicht mehr zulegiert.[6]
Emissionen
Durch das Feuerverzinken (Stückverzinkung) und etwaige nachgeschaltete Prozesse können Staub und Chlorwasserstoff emittiert werden.[7] Die Beschäftigten werden zum Teil erheblich mit ultrafeinen Partikeln belastet.[8]
Siehe auch
- Verzinkung
- Feuervergoldung
- Sherardisieren (Diffusionsverzinken)
- Industrieverband Feuerverzinken
Literatur
- Stahl-Informations-Zentrum (Hrsg.): Charakteristische Merkmale 094 - Feuerverzinkter Bandstahl. 1. Auflage, 2001, ISSN 0175-2006, (PDF; 1,49 MB).
- Stahl-Informations-Zentrum (Hrsg.): Charakteristische Merkmale 095 - Schmelztauchveredeltes Band und Blech. Ausgabe 2016, ISSN 0175-2006, (PDF; 2,01 MB).
- Institut Feuerverzinken (Hrsg.): Korrosionsschutz durch Feuerverzinken (Stückverzinken). Ausgabe 2020, (PDF; 3,74 MB).
- Hansgeorg Hofmann und Jürgen Spindler: Verfahren in der Beschichtungs- und Oberflächentechnik. Carl Hanser Verlag, 2. Auflage, 7. Oktober 2010, S. 110 u. 111, ISBN 978-3446423787.
- DIN EN 10240:1998-02 (Vorgängernorn DIN 2444, zuletzt Ausgabe 1.1984) Zinküberzüge auf Stahlrohren; Qualitätsnorm für die Feuerverzinkung von Stahlrohren für Installationszwecke. Beuth Verlag, Berlin.
Weblinks
Einzelnachweise
- Informationsportal Nachhaltiges Bauen des BMVBS: Informationsportal Nachhaltiges Bauen: Baustoff- und Gebäudedaten - Nutzungsdauern von Bauteilen. Bundesinstitut für Bau-, Stadt- und Raumforschung, 24. Februar 2017, abgerufen am 4. November 2019.
- Xian Zhang, Christofer Leygraf, Inger Odnevall Wallinder: Atmospheric corrosion of Galfancoatings on steel in chloride-rich environments, Corrosion Science 73 (2013)
- B. Schuhmacher, D. Wolfhard: Korrosionsbeständigkeit metallisch und organisch veredelter Stahlfeinbleche in der Freibewitterung, in Materials and Corrosion 49, 725–735 (1998)
- Gaigl, Ch., Mensinger, M.: Feuerwiderstand von feuerverzinkten, tragenden Stahlkonstruktionen im Brandfall. Abgerufen am 12. Juni 2020.
- Verbindungselemente – Feuerverzinkung (ISO 10684:2004 + Cor. 1:2008); Deutsche Fassung EN ISO 10684:2004 + AC:2009, Seite 12
- Charakteristische Merkmale 095: Schmelztauchveredeltes Band und Blech. In: Webseite der Wirtschaftsvereinigung Stahl. Abgerufen am 11. Oktober 2019.
- VDI 2579 2008-05 Emissionsminderung; Feuerverzinkungsanlagen (Emission control; Hot-dip zinc galvanizing plants). Beuth Verlag, Berlin, S. 11.
- Marnix Poppe, Roman Weiß: Messtechnische Bestimmung von ultrafeinen Partikeln (UFP) beim Feuerverzinken. In: Gefahrstoffe – Reinhalt. Luft. 77, Nr. 1/2, 2017, ISSN 0949-8036, S. 7–11.