Koordinatenmessgerät
Ein Koordinatenmessgerät beruht auf dem Prinzip der Koordinatenmesstechnik und beinhaltet ein zur Messung räumlicher Koordinaten geeignetes Messsystem. Es besteht aus einem Messkopfsystem (schaltender oder messender Sensor), dessen Messbereich durch ein Verfahr- bzw. Positioniersystem mit inkrementeller Weg- oder Winkelsensorik erweitert wird. Darüber hinaus sind weitere Soft- und Hardwarekomponenten zur Auswertung der erfassten Koordinatenwerte, zur rechnerischen Korrektur systematischer Messabweichung und zur Steuerung der Verfahrachsen erforderlich.
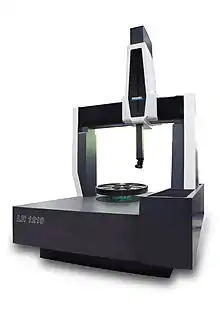
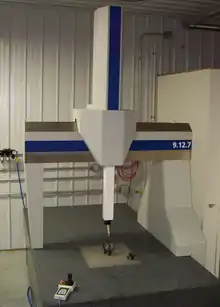
Ein rein mechanisch-analoger Vorläufer ist der Koordinatograf.
Grundprinzip und Anwendungsgebiete
Grundbauarten
Ein Koordinatenmesssystem verfügt über ein CNC-gesteuertes Positioniersystem oder ein handgeführtes Verfahrsystem, mit dem das Messkopfsystem (Sensor) und das Messobjekt in ihrer räumlichen Lage relativ zueinander bewegt werden, um die jeweiligen Messpunkte zu erfassen.[1] Jeder Verfahrachse des Positioniersystems ist mindestens ein Längenmesssystem zugeordnet, das die jeweilige Position mit feiner Auflösung misst. Einzelne Sensormesspunkte können aufgrund der bekannten Positionen der Positioniereinheit somit in ein gemeinsames Koordinatensystem transformiert und miteinander verknüpft werden.
Üblicherweise dienen als Längenmesssysteme zur relativen Positionsbestimmung der Achsen inkrementale Längenmesssysteme mit elektronischer Messwerterfassung und mit Maßverkörperungen auf materieller (z. B. Glasmaßstab) oder optischer (z. B. Laserinterferometer) Basis.
Der Messbereich und das Gerätekoordinatensystem werden durch die Verfahrachsen und deren Führungen, Antriebe und inkrementale Messsysteme festgelegt. Koordinatenmesssysteme konventioneller Bauart besitzen ein kartesisches Gerätekoordinatensystem. Koordinatenmesssysteme, deren Führungen ein Zylinder- oder Kugelkoordinatensystem aufspannen, sind aber ebenfalls verbreitet und arbeiten mit einer Kombination aus inkrementaler Weg- und Winkelsensorik.
Konventionelle Bauweise – kartesisches Gerätekoordinatensystem
Die am häufigsten eingesetzten „klassischen“ Geräte sind kartesisch rechtwinklige Koordinatenmesssysteme. Die orthogonalen Führungen spannen ein kartesisches Koordinatensystem auf. Wesentliche Bau- und Funktionsgruppen eines kartesischen Koordinatenmessgerätes sind:
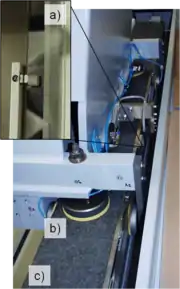
- Messtisch: meist Hartgestein
- Maßverkörperungen für die einzelnen Achsen: z. B. fotoelektrisches inkrementales Längenmesssystem mit Zerodur-Maßstäben (geringer thermischer Ausdehnungskoeffizient).
- Lagerung der einzelnen Achsen: z. B. aerostatische Lager (Luftlager) zur Realisierung einer geringen Reibung zwischen den einzelnen beweglichen Komponenten. Führungsbahnen aus Hartgestein (Granit).
- Antrieb: z. B. wird bei CNC-gesteuerten KMGs die Bewegung der Achsen durch elektrische Antriebe (inkl. Getriebe und schwingungsdämpfende Elemente) in einem geschlossenen Regelkreis realisiert. Aufgabe des Antriebssystems ist nur die Bewegung der Achsen, nicht das Bereitstellen der Information über die Position der Achsen. Diese Aufgabe wird vom Längenmesssystem übernommen, welches die aktuelle Position an den Steuer- (zur Positionierung) und Auswerterechner (zur Berechnung der angetasteten Koordinatenwerte) übermittelt.
- Mess- und Tastsysteme: siehe Abschnitt Sensoren
- Steuer- und Auswerterechner: Zur Steuerung des Messablaufs und der Verfahrbewegungen, zur Regelung der Position oder Trajektorie (z. B. Variation der Verfahrgeschwindigkeit), zur Manipulation der gemessenen Werte hinsichtlich einer rechnerischen Korrektur systematischer Messabweichungen (mit Hilfe zuvor bestimmter Kalibrierwerte) und hinsichtlich der Transformation der Koordinatenwerte sowie der Auswertung der Messpunkte gemäß dem zugeordneten Geometrieelement.

Gemäß DIN EN ISO 10360-1:2003[1] unterscheidet man folgende Grundbauarten zur Realisierung von drei zueinander rechtwinklig beweglichen Führungen:
- Auslegerbauweise: Ein Auslegerarm, an dem das Messkopfsystem befestigt ist, ist in vertikaler Richtung beweglich. Zwei weitere Achsen sind jeweils senkrecht zueinander in horizontaler Richtung beweglich. Die horizontale Bewegung kann entweder durch einen beweglichen Tisch oder bei einem feststehenden Tisch durch bewegliche Aufbauelemente des Auslegers realisiert werden. Meist wird diese Bauweise für Messgeräte mit kleinem Messbereich, aber sehr guter Messgenauigkeit eingesetzt.
- Brückenbauweise: Die beweglichen Achsen und der Aufspannbereich sind voneinander getrennt. Die in horizontaler Richtung bewegliche Brücke trägt die Pinole mit dem Messkopfsystem, welche in horizontaler Richtung entlang der Brücke und in vertikaler Richtung bewegt werden kann. Koordinatenmessgeräte in Brückenbauweise ermöglichen einen großen Messbereich und damit das Erfassen sehr großer Werkstücke bis hin zu ganzen Fahrzeugen oder Komponenten aus dem Flugzeugbau.
- Portalbauweise: An dem Portalquerbalken ist die das Messkopfsystem tragende Pinole (vertikale Bewegung) angeordnet, welche in horizontaler Richtung entlang des Portalquerbalkens beweglich ist. Das Portal ist mit zwei Füßen an den Rändern des Gerätetisches gelagert und in horizontaler Richtung entlang des Gerätetisches beweglich. Ebenfalls sind Bauweisen mit feststehendem Portal und beweglichen Gerätetisch verbreitet. Koordinatenmesssysteme in Portalbauweise bieten geringe Messabweichungen bei gleichzeitig guter Zugänglichkeit und ausreichend großem Messbereich. Sie stellen daher die häufigste Bauweise dar. Üblich ist ein Messbereich von etwa 1 m³.
- Ständerbauweise: Bei einem Koordinatenmesssystem in Ständerbauweise mit Horizontalarm ist die Pinole mit dem Messkopfsystem in horizontaler Richtung beweglich, welche entlang eines Ständers (auch Säule genannt) in vertikaler Richtung bewegt werden kann. Die zweite horizontale Bewegung kann durch Verfahren des Ständers entlang des Messtisches oder durch einen beweglichen Tisch realisiert werden. Diese Bauweise wird häufig zur Messung von Karosserien und großen Blechbauteilen genutzt, da drei Seiten des Messbereichs frei zugänglich sind.
- Grundbauarten von Koordinatenmesssystemen gemäß DIN EN ISO 10360-1:2003
- Auslegerbauweise
- Brückenbauweise
- Portalbauweise
- Ständerbauweise mit beweglichem Horizontalarm
Unkonventionelle Bauart – Zylinder- oder Kugelkoordinatensystem
Koordinatenmesssysteme unkonventioneller Bauart messen in Zylinder- oder Kugelkoordinaten. Hierzu zählen Lasertracker, Gelenkarmmessgeräte[2] und Röntgen-Computertomographie.
Unkonventionelle Bauart – Mikro- und Nanokoordinatenmesssysteme
Zur Reduktion der Messabweichungen – verursacht durch zufällige und systematische rotatorische Führungsabweichungen – werden bei Mikro- und Nanokoordinatenmessgeräten unkonventionelle Anordnungen der Längenmess- und Antriebssysteme eingesetzt. Durch Realisierung des abbeschen Komparatorprinzips in mehreren Messachsen, den Einsatz von laserinterferometrischen Längenmesssystemen und einer Parallelmetrologie, welche alle Positionswerte direkt an dem in allen drei Achsen beweglichen Sensor oder der in allen drei Achsen beweglichen Plattform mit dem Messobjekt misst, lassen sich die Messabweichungen und Messunsicherheiten signifikant reduzieren.
Erweiterungen
Durch den Einsatz eines zusätzlichen Drehtisches oder einer Dreh-Schwenk-Einrichtung können auch ungünstig gelegene Messelemente angetastet werden. Mit derartigen Erweiterungen kann das Werkstück in ein oder mehreren Achsen rotiert werden. Die veränderte Position des Werkstücks wird bei der Berechnung und Transformation der gemessenen Koordinatenwerte in das Werkstückkoordinatensystem berücksichtigt. Alternativ oder zusätzlich werden auch Dreh-Schwenk-Einrichtungen für die Sensoren eingesetzt.
Sensoren
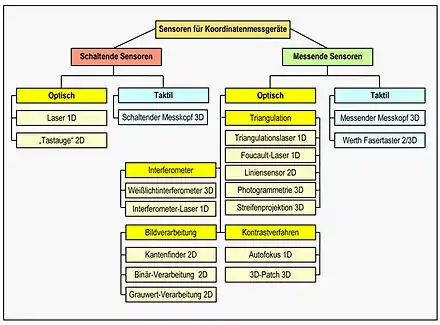
Koordinatenmesssysteme können mit schaltenden und messenden Sensoren ausgestattet sein. Schaltende Sensoren liefern beim Aufnehmen eines Messpunktes lediglich ein Triggersignal, welches das Auslesen der Längenmesssysteme initiiert. Messende Sensoren haben hingegen intern einen eigenen Messbereich von wenigen Millimetern. Der intern gemessene Sensorwert wird dabei mit der von den Längenmesssystemen bestimmten Position des Sensors überlagert.[3]
Sensoren für Koordinatenmesssysteme kann man ebenfalls hinsichtlich ihres physikalischen Prinzips unterteilen. Bis in die 90er Jahre waren taktile Sensoren die meist genutzten Antastsensoren bei Koordinatenmessgeräten. Mit verbesserter Sensortechnik, leistungsfähigerer Rechentechnik und gestiegenen Anforderungen werden heutzutage vermehrt auch optische, opto-taktile und Röntgen-Sensoren eingesetzt. Eine Übersicht über Sensoren in Koordinatenmesssystemen ist ebenfalls in[3] gegeben.
Um die Universalität von Koordinatenmesssystemen zu steigern, können auch mehrere unterschiedliche Sensorprinzipien in einem Koordinatenmesssystem vereint werden. Diese Koordinatenmesssysteme werden Multisensorkoordinatenmesssysteme genannt.
Da es mit einem einzigen Sensor bzw. Taster nicht möglich ist alle Messaufgaben zu lösen, ist es bei den meisten Koordinatenmesssystemen möglich diese auszutauschen. Mit Tasterwechseleinrichtungen kann der Wechsel in den automatischen Messablauf eingebunden werden.[4]
Mechanische (taktile) Antastung
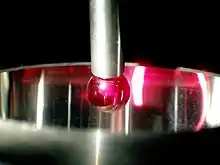
Messkopfsysteme mit taktilen Sensoren werden in schaltende Systeme (z. B. basierend auf dem elektro-mechanischen Prinzip) und messende Systeme (z. B. mit induktiv oder kapazitiv messenden Sensoren) unterteilt.
Die Antastung auf der Werkstückoberfläche wird durch Messtaster durchgeführt. Je nach Messaufgabe können hierfür unterschiedliche geometrische Formen des Tastelementes (meist Kugeln) und Materialien (oft Industrierubin, Hartmetall, Siliziumnitrid) eingesetzt werden. Die taktilen Sensorsysteme sind dem menschlichen Tastsinn nachempfunden, sodass nicht nur einzelne Berührungen, sondern auch großflächige Druckverteilungen erkannt werden können.[5]
Da bei der Antastung eine Messkraft in der Größenordnung von 0,01 N bis 0,2 N wirkt, biegt sich der Taststift, was bei der Messung berücksichtigt werden muss. Die Biegung des Taststiftes wird beim Einmessen der Taster (Taststiftkalibrierung, Tasterqualifikation) berücksichtigt und bei den folgenden Messungen automatisch korrigiert. Zusätzlich wird beim Einmessen des Tasters der Durchmesser bestimmt und bei mehreren Tastelementen der Bezug zueinander hergestellt (z. B. bei Sterntaster die Abstände der Mittelpunkte der Tastkugeln zueinander). Das Einmessen des Tasters erfolgt an einem sehr genauen Kugelnormal (Formabweichung < 0,2 µm), das mit jedem verwendeten Taster an mindestens fünf oder mehr Punkten entsprechend einer vom Gerätehersteller definierten Einmessstrategie angetastet wird.
Das punktweise Erfassen der Werkstückoberfläche ist ihrem Wesen nach vergleichbar mit dem Ziehen einer Stichprobe aus der unendlich großen Gesamtheit aller Oberflächenpunkte. Die Bereiche zwischen den aufgenommenen Messpunkten werden nicht erfasst und infolgedessen bei der Auswertung nicht berücksichtigt. Je mehr Messpunkte aufgenommen werden, desto mehr Informationen über die Oberfläche des Werkstückes werden erfasst und in die Auswertung einbezogen (der Umfang der Stichprobe wird größer). Das Antasten einzelner Punkte erfordert bei großen Messpunktzahlen erhebliche, meist nicht akzeptable Messzeiten.[6]
Beim Scannen wird die Tastkugel mit Hilfe besonderer Steuerfunktionen berührend entlang der Oberfläche des Werkstücks bewegt. Während der Bewegung werden laufend Messwerte übernommen. Neuere Geräte lassen hohe Scanning-Geschwindigkeiten zu, mit denen wie bei der Formmesstechnik sehr große Messpunktzahlen in geringer Messzeit erreicht werden können. Dies kann zu einer erhöhten Aussagesicherheit führen, obwohl die Einzelpunkt-Unsicherheit beim Scannen deutlich größer ist als beim Antasten einzelner Punkte. Das Scannen gewinnt daher gegenüber dem Einzelpunkt-Betrieb immer mehr an Bedeutung.[6]
Normen und Richtlinien, welche direkt auf die taktile Antastung bei Koordinatenmessungen eingehen, sind DIN EN ISO 10360-4:2002,[7] DIN EN ISO 10360-5:2010[8] und VDI/VDE 2617 Blatt 12.1.[9]
Berührungslose Antastung
Zur berührungslosen Antastung können optische, elektrische und röntgentomographische Sensoren eingesetzt werden. Prinzipiell kann jeder elektrische oder optische Sensor in Koordinatenmesssystemen eingesetzt werden, um dessen Messbereich mit Hilfe des Positioniersystems zu erweitern.
Optische Abstandssensoren
- Triangulationssensoren (z. B. Lasertriangulation, Liniensensor, Photogrammetrie, Streifenprojektion)
- Bilderverarbeitungssensoren (z. B. Kantenfinder, Binär-Verarbeitung, Grauwert-Verarbeitung)
- Fokusvariation (Kontrastverfahren, z. B. Autofokus)
- Konfokalsensoren (z. B. chromatischer Konfokalsensor, Foucault-Sensor bzw. Laserfokusverfahren)
- Interferometer (z. B. Laserinterferometer, Weißlichtinterferometer)
Elektrische Abstandssensoren
- Tunnelstromsensoren (z. B. schaltend oder Tunnelstrommessung)
Röntgentomographische Sensoren
- Bestehend aus einer Röntgenröhre und einem Detektor (die durch ein Messobjekt, welches sich zwischen Röntgenröhre und Detektor befindet und durchstrahlt wird, abgeschwächte Röntgenstrahlung wird gemessen)
Normen und Richtlinien, welche auf die berührungslose Antastung bei Koordinatenmessungen eingehen, sind DIN EN ISO 10360-7:2011,[10] DIN EN ISO 10360-8:2012,[11] VDI/VDE 2617 Blatt 6.1[12] und VDI/VDE 2617 Blatt 6.2.[13]
Weiterentwickelte Gerätetechnik
Multisensorkoordinatenmessgeräte – Messen mit mehreren Sensoren
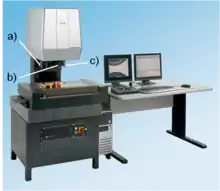
Eine besonders hohe Universalität wird durch die Kombination mehrerer unterschiedlicher Sensoren in einem Koordinatenmessgerät erreicht. Für jedes zu messende Merkmal kann der optimale Sensor ausgewählt werden. Die Messergebnisse der unterschiedlichen Sensoren liegen in einem gemeinsamen Koordinatensystem vor. Hierfür wird die Position der Sensoren vorab zueinander eingemessen. Dies ermöglicht es, die Ergebnisse verschiedener Sensoren zu kombinieren, um Merkmale zu messen, die mit einem Sensor allein nicht oder nur schlecht messbar sind.
Die verschiedenen Sensoren werden entweder an einer Wechselschnittstelle an der Pinole des Koordinatenmessgerätes befestigt und im Messablauf nacheinander automatisch eingewechselt (Sensorwechsler), oder sind dauerhaft an der vertikal positionierbaren Pinole nebeneinander angeordnet. Durch Geräte mit mehreren Pinolen, die eine getrennte vertikale Positionierung der einzelnen Sensoren zulassen, ist das Kollisionsrisiko verringert. Ebenso werden Sensoren auch mittels Rückzugsachsen an der Pinole befestigt und nur bei Bedarf ausgefahren, wodurch sich Kollisionen vermeiden lassen.
Normen und Richtlinien mit direktem Bezug zu Koordinatenmesssystemen mit Multisensorik sind DIN EN ISO 10360-9:2011[14] und VDI/VDE 2617 Blatt 6.3.[15]
Portable Koordinatenmessgeräte
Während herkömmliche Koordinatenmessgeräte (KMG) eine Sonde verwenden, die sich auf drei kartesischen Achsen bewegt, um physikalische Eigenschaften eines Objekts zu messen, nutzen tragbare KMGs entweder Gelenkarme oder, im Fall von optischen Koordinatenmessgeräten, messarmfreie Scansysteme, die optische Triangulationsmethoden verwenden und eine uneingeschränkte Bewegungsfreiheit um das Objekt herum ermöglichen. Tragbare KMGs mit Gelenkarmen haben sechs oder sieben Achsen, die anstelle von Linearachsen mit Drehgebern ausgestattet sind. Tragbare Messarme sind leicht (in der Regel weniger als 20 Pfund) und können fast überall hin transportiert und eingesetzt werden. Allerdings werden in der Industrie zunehmend optische Koordinatenmessgeräte verwendet. Sie sind mit kompakten linearen oder Matrix-Array-Kameras (wie der Microsoft Kinect) ausgestattet und sind kleiner als portable KMG mit Armen. Sie funktionieren kabellos und erlauben Anwendern schnell und einfach 3D-Messungen aller Arten von Objekten praktisch überall durchzuführen. Tragbare KMG eignen sich insbesondere für bestimmte, sich nicht wiederholende Anwendungen im Bereich Reverse Engineering, Rapid Prototyping und für die Inspektion großer Bauteile. Die Vorteile tragbarer KMG sind vielfältig. Nutzer können jede Art von Teilen selbst in den entferntesten und schwierigsten Umgebungen in 3D messen. Die optischen Messsysteme sind benutzerfreundlich und erfordern keine kontrollierte Umgebung für genaue Messungen. Hinzu kommt, dass tragbare Koordinatenmessgeräte weniger kosten als herkömmliche KMG.
Kompromisse müssen bei tragbaren KMG eingegangen werden: Es wird ein Anwender für die manuelle Handhabung benötigt. Darüber hinaus kann die Gesamtgenauigkeit etwas ungenauer sein als bei einer fest installierten Portalmessmaschine. Zudem ist das portable KMG für einige Anwendungen weniger geeignet.
Röntgen-Computertomographie
Neben taktilen und optischen Sensoren, welche abgesehen von der Schichtdickenmessung stets die Außengeometrie erfassen, kann das Verfahren der Röntgen-Computertomografie angewendet werden, um zusätzlich zur Außengeometrie auch die Innengeometrie eines Werkstücks zu messen. Beim Messen mit diesen Sensoren wirken zahlreiche Einflüsse (Ringartefakte, Taumelartefakte, Kegelstrahl-/Feldkamp-Artefakte, Strahlaufhärtung, Teil- oder Partialvolumenartefakte[16]), welche die Genauigkeit des Messergebnisses beeinflussen. Durch den Einsatz zusätzlicher taktiler Sensoren, können systematische Messabweichungen der Tomografie teilweise korrigiert werden.[17] Da während der Tomographie ein Bauteil immer vollständig durchstrahlt werden muss, ist der Einsatz für massive Bauteile oder für Bauteile mit stark unterschiedlichen Absorptionskoeffizienten (wegen nichtdurchstrahlte und überstrahlte Bereiche) eingeschränkt.
Richtlinien mit direktem Bezug zu Röntgen-Computertomographie für Koordinatenmessungen sind VDI/VDE 2617 Blatt 13[18] und VDI/VDE 2630 Blatt 1.1,[19] 1.2,[20] 1.4[21] und 2.1.[22]
Während Koordinatenmesssysteme basierend auf der Röntgen-Computertomografie für den industriellen Einsatz kommerziell verfügbar sind, befinden sich industrielle Koordinatenmesssysteme basierend auf Ultraschall-Computertomografie (USCT) und Neutronen-Computertomografie (NCT) noch im Forschungsstadium.
Lasertracker
Siehe Tracking-Interferometer. Normen und Richtlinien mit direktem Bezug zu Lasertrackern für Koordinatenmessungen sind DIN EN ISO 10360-10:2012,[23] VDI/VDE 2617 Blatt 10[24] und VDI/VDE 2617 Blatt 10.1.[25]
Maschinenintegrierte Messtechnik
Werkzeugmessgeräte sind spezialisierte Messgeräte für die Prüfung, Einstellung, Ausrichtung und Justage von spanenden Werkzeugen. Es gibt verschiedene Varianten, deren Auslegung den Anforderungen der Spezialisierung entsprechen.
Für das Fertigungsverfahren Fräsen, also für rotierende Werkzeuge wie Spiralbohrer oder Messerköpfe sind nur zwei Längsachsen (Werkzeughöhe und -breite) und eine Drehachse zur Prüfung der Werkzeuglänge, des Werkzeugdurchmessers und des Rundlaufs erforderlich.
Anstelle eines Messsensors für eine Kontaktmessung an einer Oberfläche tritt bei Werkzeugmessgeräten meist ein in zwei Achsen verfahrbarer Tageslichtprojektor, der auf einem großen Projektionsschirm mit Fadenkreuz den Schattenwurf oder das Profil des Werkzeuges abbildet. Bei der Messung wird die Projektionseinheit so verfahren das der Rand oder eine Ecke des Werkzeugs im Fadenkreuz liegt. Aus dem Verfahrweg ergibt sich die Werkzeuglänge oder der -durchmesser. Durch Ausrichtung auf dem Fadenkreuz und anschließende Drehung kann weiter der Rundlauf geprüft und so lange korrigiert werden, bis die Drehung keine Abweichung des Schattenrands auf dem Fadenkreuz zeigt.
Werkzeugmessgeräte für spanende Werkzeuge für das Fertigungsverfahren Drehen kommen formal mit zwei Achsen aus, besitzen aber meist drei, um auch die Höhe der Werkzeugschneide (für das sogenannte "Drehen über oder unter Mitte") in Bezug der Werkzeugaufnahmeebene zur Drehachse an der Drehmaschine prüfen zu können.
Ursachen und Maßnahmen zur Reduzierung von Messabweichungen
Bei jeder Messung bestehen Abweichungen zwischen dem vom Messgerät angezeigten Messwert und dem tatsächlichen Wert der geometrischen Größe (Referenzwert). Diese Messabweichungen können unterschieden werden in zufällige und systematische Messabweichungen. Bei Koordinatenmesssystemen werden viele konstruktive und rechnerische Maßnahmen angewendet, um Messabweichungen gering zu halten. Während man systematische Messabweichungen rechnerisch korrigieren kann, machen zufällige Messabweichungen das Messergebnis unsicher. Genormte Verfahren zur Ermittlung der Mess- und Testunsicherheit von Koordinatenmesssystemen werden in DIN EN ISO 15530-3:2011,[26] VDI/VDE 2617 Blatt 7,[27] VDI/VDE 2617 Blatt 11[28] und in DIN ISO/TS 23165:2008[29] vorgestellt.
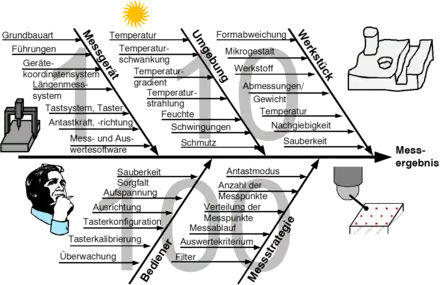
Wichtige Ursachen von Messabweichungen bei Koordinatenmessgeräten sind:
- Umgebungsbedingungen: Temperatur (Temperaturschwankungen, -gradienten, -strahlung), Schwingungen, Feuchte, Schmutz
- Werkstück , Messobjekt: Formabweichungen, Mikrogestalt (Rauheit), Werkstoff (E-Modul bei taktiler Antastung), Reflexionsgrad (bei optischer Antastung), Abmessungen / Gewicht, Temperatur, Nachgiebigkeit (z. B. filigrane Strukturen), Sauberkeit
- Messgerät: Konstruktiver Aufbau, Führungsabweichungen, Tastsystem, Antastkraft und -richtung, Mess- und Auswertesoftware
- Messstrategie: Antastmodus, Anzahl und Verteilung der Messpunkte, Messablauf, Auswertekriterien, Filter
- Bediener: Sorgfalt, Aufspannung, Tasterkonfiguration, Tasterkalibrierung, Überwachung des KMG
Konstruktive Maßnahmen gegen temperaturbedingte Messabweichungen
- Präzise gefertigte Führungskörper mit guten thermischen Eigenschaften.
- Pinole und Traverse des Portals aus Materialien mit hoher Wärmeleitfähigkeit (z. B. Aluminium). Die hohe Wärmeleitfähigkeit verkürzt die Anpassungszeit zur Wiederherstellung der Genauigkeit nach Temperaturschwankungen.
- Einhalten der international vereinbarten Bezugstemperatur von 20 °C durch klimatisierten Messraum, Temperieren der Messobjekte und Vermeidung einer Temperaturänderung am Messgerät (thermische Isolation des Geräteaufbaus; Vermeidung direkter Handwärme durch Thermohandschuhe, Vermeidung von Strahlung durch Beleuchtung und Sonne usw.)
- Maßstäbe aus Materialien mit minimalem thermischem Ausdehnungskoeffizient
- Temperaturüberwachung des Messraumes, des Messbereichs, des Messobjektes und von Messsystemelementen
Konstruktive Maßnahmen gegen Vibrationen
- Um den Schwingungseintrag aus der Umgebung auf die messtechnischen Einrichtungen zu reduzieren, kann als Fundament, auf dem alle messtechnisch relevanten Einrichtungen stehen, eine massive Betonplatte dienen, die ihrerseits durch ein Kiesbett und eine isolierende Dämpfungsschicht (spezielles Polymer) vom Boden getrennt ist. Eine umlaufende Trennfuge entkoppelt die Bodenplatte vom restlichen Gebäude. Durch diese Maßnahmen können die maximal zulässigen Schwingungsamplituden nach VDI/VDE 2627 eingehalten werden.
- Ein im Koordinatenmesssystem integriertes System zur passiven (oder aktiven) pneumatischen Schwingungsdämpfung minimiert das Übertragen von Bodenschwingungen und nivelliert den Gerätetisch bei unsymmetrischer Belastung durch das Werkstückgewicht.
Rechnerische Maßnahmen
- Rechnerische Korrektur statischer und dynamischer Einflüsse aller 21 Führungsabweichungen (regelmäßige Überwachung und ggf. Rekalibrierung zur Vermeidung von Drift)
- Vorhandene Plattendeformationen des Messtisches – verursacht durch Temperaturgradienten – werden durch Messen der Temperaturdifferenz zwischen Plattenober- und -unterseite kompensiert.
- Rechnerische Korrektur der Tasterbiegung bedingt durch Antastkräfte (bei taktilen Sensoren)
- Rechnerische Korrektur von Temperaturabweichungen des Werkstücks und einzelner Komponenten (z. B. der Maßstäbe) des Koordinatenmesssystems
Annahme- und Bestätigungsprüfungen
Zur Bestätigung der vom Hersteller festgelegten Leistungsfähigkeit eines Messsystems werden Annahmeprüfungen und nach wiederkehrenden Zeitabständen Bestätigungsprüfungen durchgeführt. Mit Hilfe kalibrierter Prüfkörper (Stufenendmaß, Kugelplatte, Lochplatte etc.) können dabei Längenmessabweichungen gemäß DIN EN ISO 10360-2:2010[30] und VDI/VDE 2617 Blatt 2.1[31] und Antastabweichungen gemäß DIN EN ISO 10360-5:2010[8] überprüft werden. VDI/VDE 2617 Blatt 5[32] und Blatt 5.1[33] gehen hierbei noch gezielt auf einzelne Prüfkörper ein.
Begrifflichkeiten
Der Begriff „Messmaschine“ (bzw. „Koordinatenmessmaschine“) ist stets zu vermeiden. Korrekt ist die Bezeichnung „Messgerät“ (bzw. „Koordinatenmessgerät“), da in der Technik ein „Gerät“ als ein signalumsetzendes bzw. informationsverarbeitendes System zur Steigerung der sensorischen oder geistigen Leistung eines Menschen definiert wird, während eine „Maschine“ ein energie- oder stoffumsetzendes System zur Steigerung der körperlichen Leistung eines Menschen beschreibt.
Da Geräte für Koordinatenmessungen mittlerweile komplexe Systeme sind, d. h. einen Verbund mehrerer Geräte darstellen, hat man sich international im Rahmen des ISO/TC 213 WG10 im Jahr 2013 darauf geeinigt, zukünftig nur noch den Begriff „Koordinatenmesssystem“ in Normen zu verwenden (Englisch: „Coordinate Measuring System“).
Normen und Richtlinien
- DIN EN ISO 10360-Reihe: Geometrische Produktspezifikation (GPS) – Annahmeprüfung und Bestätigungsprüfung für Koordinatenmessgeräte (KMG). Eine Übersicht ist auf der Homepage des ISO/TC 213[34] gegeben.
- VDI/VDE 2617-Reihe: Genauigkeit von Koordinatenmessgeräten – Kenngrößen und deren Prüfung. Eine Übersicht ist auf der Homepage des GMA FA „3.31 Koordinatenmessgeräte“[35] gegeben.
Literatur
- Albert Weckenmann (Hrsg.): Koordinatenmesstechnik: Flexible Strategien für funktions- und fertigungsgerechtes Prüfen. 2. Auflage. Hanser, 2012.
- Robert J. Hocken, Paulo H. Pereira (Hrsg.): Coordinate Measuring Machines and Systems (Manufacturing, Engineering and Materials Processing). CRC Press, 2011.
- Wolfgang Dutschke, Claus P. Keferstein: Fertigungsmesstechnik: Praxisorientierte Grundlagen, moderne Messverfahren. 5. Auflage. Vieweg+Teubner, 2005.
- Ralf Christoph, Hans J. Neumann: Multisensor-Koordinatenmesstechnik – Produktionsnahe optisch-taktile Maß-, Form- und Lagebestimmung. (= Die Bibliothek der Technik. Band 248). Verlag Moderne Industrie, 2006.
Weblinks
Einzelnachweise
- DIN EN ISO 10360-1:2003: Geometrische Produktspezifikation (GPS) - Annahmeprüfung und Bestätigungsprüfung für Koordinatenmessgeräte (KMG) - Teil 1: Begriffe
- VDI/VDE 2617 Blatt 9: Genauigkeit von Koordinatenmessgeräten - Kenngrößen und deren Prüfung - Annahme- und Bestätigungsprüfung von Gelenkarm-Koordinatenmessgeräten, 2009.
- koordinatenmesstechnik.de
- Sensoren - Tasterwechseleinrichtung. (Memento vom 12. November 2013 im Internet Archive) aukom-ev.de
- Taktile Sensorik - Fraunhofer IFF. Abgerufen am 8. Dezember 2021.
- Albert Weckenmann (Hrsg.): Koordinatenmesstechnik: Flexible Strategien für funktions- und fertigungsgerechtes Prüfen. 2. Auflage. Hanser, 2012.
- DIN EN ISO 10360-4:2002: Geometrische Produktspezifikation (GPS) - Annahmeprüfung und Bestätigungsprüfung für Koordinatenmessgeräte (KMG) - Teil 4: KMG im Scanningmodus
- DIN EN ISO 10360-5:2010: Geometrische Produktspezifikation (GPS) - Annahmeprüfung und Bestätigungsprüfung für Koordinatenmessgeräte (KMG) - Prüfung der Antastabweichungen von KMG mit berührendem Messkopfsystem
- VDI/VDE 2617 Blatt 12.1: Genauigkeit von Koordinatenmessgeräten - Kenngrößen und deren Prüfung - Annahme- und Bestätigungsprüfungen für Koordinatenmessgeräte zum taktilen Messen von Mikrogeometrien
- DIN EN ISO 10360-7:2011: Geometrische Produktspezifikation (GPS) - Annahmeprüfung und Bestätigungsprüfung für Koordinatenmessgeräte (KMG) - KMG mit Bildverarbeitungssystemen
- DIN EN ISO 10360-8:2012: Geometrische Produktspezifikation (GPS) - Annahmeprüfung und Bestätigungsprüfung für Koordinatenmessgeräte (KMG) - KMG mit optischen Abstandssensoren
- VDI/VDE 2617 Blatt 6.1: Genauigkeit von Koordinatenmessgeräten - Kenngrößen und deren Prüfung - Leitfaden zur Anwendung von DIN EN ISO 10360 für Koordinatenmessgeräte mit optischen Sensoren für laterale Strukturen, 2007.
- VDI/VDE 2617 Blatt 6.2: Genauigkeit von Koordinatenmessgeräten - Kenngrößen und deren Prüfung - Leitfaden zur Anwendung von DIN EN ISO 10360 für Koordinatenmessgeräte mit optischen Abstandssensoren, 2005.
- DIN EN ISO 10360-9:2011: Geometrische Produktspezifikation (GPS) - Annahmeprüfung und Bestätigungsprüfung für Koordinatenmessgeräte (KMG) - KMG mit Multisensoren
- VDI/VDE 2617 Blatt 6.3: Genauigkeit von Koordinatenmessgeräten - Kenngrößen und deren Prüfung - Koordinatenmessgeräte mit Multisensorik, 2008.
- Philipp Krämer: Simulationsgestützte Abschätzung der Genauigkeit von Messungen mit Röntgen-Computertomographie. Dissertation Friedrich-Alexander-Universität Erlangen-Nürnberg, Shaker, 2012.
- koordinatenmesstechnik.de
- VDI/VDE 2617 Blatt 13: Genauigkeit von Koordinatenmessgeräten - Kenngrößen und deren Prüfung - Leitfaden zur Anwendung von DIN EN ISO 10360 für Koordinatenmessgeräte mit CT-Sensoren, 2011.
- VDI/VDE 2630 Blatt 1.1: Computertomografie in der dimensionellen Messtechnik - Grundlagen und Definitionen, 2009.
- VDI/VDE 2630 Blatt 1.2: Computertomografie in der dimensionellen Messtechnik - Einflussgrößen auf das Messergebnis und Empfehlungen für dimensionelle Computertomografie-Messungen, 2010.
- VDI/VDE 2630 Blatt 1.4: Computertomografie in der dimensionellen Messtechnik - Gegenüberstellung verschiedener dimensioneller Messverfahren, 2010.
- VDI/VDE 2630 Blatt 2.1: Computertomografie in der dimensionellen Messtechnik - Bestimmung der Messunsicherheit und der Prüfprozesseignung von Koordinatenmessgeräten mit CT-Sensoren, 2013.
- DIN EN ISO 10360-10:2012: Geometrische Produktspezifikation (GPS) - Annahmeprüfung und Bestätigungsprüfung für Koordinatenmessgeräte (KMG) - Teil 10: Lasertracker
- VDI/VDE 2617 Blatt 10: Genauigkeit von Koordinatenmessgeräten - Kenngrößen und deren Prüfung - Annahme- und Bestätigungsprüfung von Lasertrackern, 2011.
- VDI/VDE 2617 Blatt 10.1: Genauigkeit von Koordinatenmessgeräten - Kenngrößen und deren Prüfung - Lasertracker mit Multisensorik, 2012.
- DIN EN ISO 15530-3:2011: Geometrische Produktspezifikation und -prüfung (GPS) - Verfahren zur Ermittlung der Messunsicherheit von Koordinatenmessgeräten (KMG) - Teil 3: Anwendung von kalibrierten Werkstücken oder Normalen
- VDI/VDE 2617 Blatt 7: Ermittlung der Unsicherheit von Messungen auf Koordinatenmessgeräten durch Simulation, 2008.
- VDI/VDE 2617 Blatt 11: Ermittlung der Unsicherheit von Messungen auf Koordinatenmessgeräten durch Messunsicherheitsbilanzen, 2011.
- DIN ISO/TS 23165:2008: Geometrische Produktspezifikation (GPS) - Leitfaden zur Ermittlung der Testunsicherheit von Koordinatenmessgeräten
- DIN EN ISO 10360-2:2010: Geometrische Produktspezifikation (GPS) - Annahmeprüfung und Bestätigungsprüfung für Koordinatenmessgeräte (KMG) - Teil 2: KMG angewendet für Längenmessungen
- VDI/VDE 2617 Blatt 2.1: Genauigkeit von Koordinatenmessgeräten - Kenngrößen und deren Prüfung - Leitfaden zur Anwendung von DIN EN ISO 10360-2 zur Messung von Längenmaßen
- VDI/VDE 2617 Blatt 5: Genauigkeit von Koordinatenmessgeräten - Kenngrößen und deren Prüfung - Überwachung durch Prüfkörper, 2010.
- VDI/VDE 2617 Blatt 5.1: Genauigkeit von Koordinatenmessgeräten - Kenngrößen und deren Prüfung - Überwachung mit Kugelplatten, 2011.
- iso.org
- vdi.de