Durchstrahlungsprüfung
Die Durchstrahlungsprüfung ist ein bildgebendes Verfahren der zerstörungsfreien Werkstoffprüfung (ZFP) zur Darstellung von Materialunterschieden. Mit Röntgen- oder Gammastrahlung aus einer geeigneten Quelle (einer Röntgenröhre, einem Elektronenbeschleuniger mit Röntgentarget oder einem gammastrahlenden Radionuklid) wird die Dichte eines Bauteils auf einem Röntgenfilm abgebildet. Dort erscheint ein Projektionsbild des Bauteils. Am Grad der Schwärzung lässt sich die unterschiedliche Materialdicke oder -dichte erkennen. Je dicker oder dichter ein Bauteil, desto weniger Strahlung kann es durchdringen und desto heller erscheint die Stelle auf dem Röntgenbild.
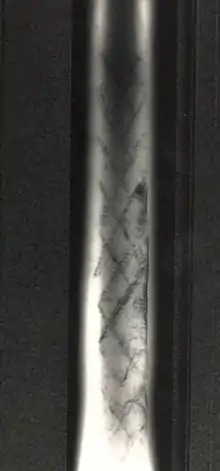
Anwendung
Die Röntgen- und Gammadurchstrahlung ist eine zerstörungsfreie Werkstoffprüfung zur Fehleraufdeckung im Inneren von Bauteilen, insbesondere an Schweißnähten von Blechen, Rohren und Behältern. Zur Prüfung sicherheitsrelevanter Bauteile bspw. von Schweißnähten (DIN EN ISO 10675-1) sowie sicherheitsrelevanter Gussteile (DIN EN 12681:2003-06 und DIN EN ISO 5579:2014-04) z. B. in Kraftwerken ist sie ein Standardverfahren.
Die häufigsten Fehler sind Lunker, Poren, Seigerungen und Risse. Damit diese gut erkennbar sind, müssen Strahlungsintensität, Wellenlänge der Strahlen, Dicke des Bauteils und Belichtungszeit aufeinander abgestimmt sein. Die Durchstrahlungsprüfung (Kürzel RT gem. DIN EN ISO 9712) ist geeignet zum Nachweis volumenhafter Fehler. Durch Unterschiede der Dichte zwischen Fehlstelle und Grundmaterial ist der Fehler nachweisbar. Auch feine Risse lassen sich bei geeignetem Einstrahlwinkel finden. Kontrast und Auflösung beeinflussen das Erkennen solcher Details. Der Kontrast ist abhängig von der Werkstoffdicke, der Dichte, dem Material, der Strahlerqualität/Energieintensität sowie dem Auflösungsvermögen und dem Typus des Films.
Zur Beurteilung der Bildgüte werden Karten (sog. Drahtsteg-Bildgüteprüfkörper nach DIN EN ISO 19232-1:2013-12) mit sieben Drahtstegen unterschiedlicher Durchmesser auf das belichtete Bauteil gelegt. Die Durchmesser der Drähte reichen von 0,05 mm bis 3,2 mm und sind nach Normvorgabe in 19 Einzeldurchmesser unterteilt. Anhand des dünnsten noch zu erkennenden Drahtes kann auf die kleinste erkennbare Fehlergröße geschlossen werden.
Eigenschaften
Röntgen- und Gammastrahlen sind elektromagnetische Wellen. Physikalisch gleichen sie dem Licht, haben aber wesentlich kleinere Wellenlängen und dadurch höhere Frequenzen. Auf den kleinen Wellenlängen beruht die Fähigkeit, zwischen den Atomen der Materie einzudringen und mit genügend hoher Energie (Frequenz) auch durchzudringen (Bedingung: Wellenlänge muss kleiner als der Abstand zwischen den Atomen im Kristallgitter sein). Beim Durchdringen werden sie dann verschieden stark durch Fehler abgeschwächt und dadurch zeigt die austretende Strahlung Intensitätsunterschiede. Sie durchdringen Stahl bis etwa 300 mm, Leichtmetall bis 400 mm und Kupfer bis 50 mm. Das Durchdringungsvermögen der Röntgen- und Gammastrahlen ist umso höher, je kleiner die Dichte des Bauteils, die Wellenlänge der Strahlen und je größer die Frequenz ist. Gammastrahlen haben i. A. größere Eindringtiefen, weil sie kurzwelliger sind.
Erzeugung der Strahlen
Die Gammastrahler für die Werkstoffprüfung sind zum Beispiel 60Cobalt, 192Iridium, 75Selen und 137Cäsium.[1][2]
Die Isotope liegen in etwa 0,5 – 6 mm großen Präparaten vor. Die Präparate werden mechanisch aus der Schirmung bewegt, wenn sie Strahlung abgeben sollen. Sie sind gasdicht in der Strahlerkapsel mit Wolfram-Abschirmung (innen) und Blei- oder Uran-Abschirmung (außen) eingeschlossen, damit die Strahlung nicht allseitig austreten kann. Da die Strahlenquelle wesentlich kleiner als eine Röntgenröhre ist, lässt sie sich dichter an den Prüfling heranbringen, wie z. B. der Isotopenmolch, ein Gerät, das zur Schweißnahtprüfung auf Baustellen durch Rohre gezogen wird. Auch dass diese Prüfverfahren ohne Stromanschluss arbeiten, ist ein Vorteil.
Röntgenstrahlen werden mit Röntgenröhren oder bei hohen Energien mit Elektronenbeschleunigern[2] erzeugt, siehe Röntgenstrahlung. Die Quantenenergien sind wesentlich höher als im Medizinbereich, daher sind die Abschirm- und Sicherheitsmaßnahmen erheblich.
Durchführung
Die Strahlenquelle projiziert das Schattenbild des Prüfstückes auf eine strahlungsempfindliche Schicht. Die Anordnung besteht aus Strahlenquelle, durchstrahlter Probe und Registriereinrichtung. Ist ein Lunker oder ein Einschluss verringerter Dichte vorhanden, ist dahinter die Intensität der durchtretenden Strahlung höher als an anderen Stellen; hinter einem Einschluss mit höherer Dichte ist sie geringer. Es sind umfangreiche Strahlenschutzregeln (DIN 54113, DIN 54115) zu beachten.
Abbildungsverfahren
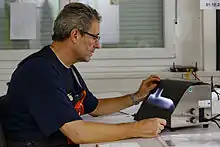
Röntgenfilm
Die aus dem Werkstoff austretenden Strahlen treffen auf eine doppelbeschichtete Filmfolie, die auf der Rückseite mit Bleifolien abgedeckt ist, um Streustrahlen fernzuhalten. Intensitätsunterschiede setzen sich in Schwärzungsunterschiede des Films um. Durch unterschiedlich starke Schwärzungen des Films sieht man die geometrische Form sowie die Lage des Fehlers. Die Filmaufnahme ist mit Röntgen- und Gammastrahlen möglich.
Anwendung: Kontrolle von Schweißnähten und Gussteilen mit Dicken bis zu 100 mm (Stahl) und 400 mm (Al); Revisionsuntersuchungen in Kessel-, Brücken- und Flugzeugbau.
Leuchtschirm
Röntgenstrahlen regen bestimmte Kristalle zur Abgabe grün-gelben Lichtes an. Eine mit entsprechendem Pulver beschichtete Platte dient als Leuchtschirm. Auf diesem erscheint ein Schattenbild des Prüflings, jedoch mit geringer Lichtstärke. Fehler mit geringer Dichte sind auf dem Schattenbild heller, Fehler mit höherer Dichte dunkler. Der Beobachter muss durch Bleiglas vor der Streustrahlung geschützt werden.
Die Durchleuchtung mit Röntgenstrahlen ist für Stahldicken bis zu 20 mm, für Leichtmetalle und Kunststoffe anwendbar.
Bildverstärker
Mit Hilfe von elektronischen Kameras oder Restlichtverstärker-Röhren kann das Röntgen-Leuchtschirmbild verkleinert und verstärkt werden, um die Strahlenbelastung des Untersuchungsobjektes zu verringern. Das Kamerabild kann mit Kabel übertragen werden, sodass der Beobachter in einem strahlengeschützten Raum sitzen kann.
Anwendung: Prüfung von Längs- und spiralgeschweißten Rohren
Sensorfolie
Statt eines Filmes können Sensor- oder Speicherfolien[1] verwendet werde, die das Bild wie ein Film aufnehmen, speichern und am Computer digital ausgelesen werden können.
Digitaler Röntgendetektor
Festkörperdetektoren mit analog-digital Wandlung (bspw. Flächendetektoren) können ebenfalls zur Durchstrahlungsprüfung verwendet werden. In diesem Zusammenhang spricht man auch von digitaler Radioskopie.
Normen für die Durchstrahlungsprüfung
- DIN EN ISO 5579:2014-04 Zerstörungsfreie Prüfung – Durchstrahlungsprüfung von metallischen Werkstoffen mit Film und Röntgen- oder Gammastrahlen – Grundlagen
- DIN EN ISO 19232-1:2013-12 Zerstörungsfreie Prüfung – Bildgüte von Durchstrahlungsaufnahmen – Teil 1: Ermittlung der Bildgütezahl mit Draht-Typ-Bildgüteprüfkörper
- DIN EN ISO 19232-2:2013-12 Zerstörungsfreie Prüfung – Bildgüte von Durchstrahlungsaufnahmen – Teil 2: Ermittlung der Bildgütezahl mit Stufe/Loch-Typ Bildgüteprüfkörper
- DIN EN ISO 19232-3:2014-02 Zerstörungsfreie Prüfung – Bildgüte von Durchstrahlungsaufnahmen – Teil 3: Bildgüteklassen
- DIN EN ISO 19232-4:2013-12 Zerstörungsfreie Prüfung – Bildgüte von Durchstrahlungsaufnahmen – Teil 4: Experimentelle Ermittlung von Bildgütezahlen und Bildgütetabellen
- DIN EN ISO 19232-5:2018-12 Zerstörungsfreie Prüfung – Bildgüte von Durchstrahlungsaufnahmen – Teil 5: Bestimmung der Bildunschärfezahl mit Doppeldraht-Typ-Bildgüteprüfkörpern
- DIN EN ISO 11699-1:2012-01 Zerstörungsfreie Prüfung – Industrielle Filme für die Durchstrahlungsprüfung – Teil 1: Klassifizierung von Filmsystemen für die industrielle Durchstrahlungsprüfung
- DIN EN ISO 11699-2:2018-12 Zerstörungsfreie Prüfung – Industrielle Filme für die Durchstrahlungsprüfung – Teil 2: Kontrolle der Filmverarbeitung mit Hilfe von Referenzwerten
- DIN EN 1330-1:2015-05 Zerstörungsfreie Prüfung – Terminologie – Teil 1: Allgemeine Begriffe
- DIN EN 1330-2:1998-12 Zerstörungsfreie Prüfung – Terminologie – Teil 2: Begriffe, die von allen zerstörungsfreien Prüfverfahren benutzt werden
- DIN EN 1330-3:1997-10 Zerstörungsfreie Prüfung – Terminologie – Teil 3: Begriffe der industriellen Durchstrahlungsprüfung
- DIN EN 1330-9:2017-10 Zerstörungsfreie Prüfung – Terminologie – Teil 9: Begriffe der Schallemissionsprüfung
- DIN EN 1330-10:2003-05 Zerstörungsfreie Prüfung – Terminologie – Teil 10: Begriffe für Sichtprüfung
- DIN EN 1330-11:2007-09 Zerstörungsfreie Prüfung – Terminologie – Teil 11: Begriffe der Röntgendiffraktometrie von polykristallinen und amporphen Metallen
- DIN EN ISO 17636-1:2013-05 Zerstörungsfreie Prüfung von Schweißverbindungen – Durchstrahlungsprüfung – Teil 1: Röntgen- und Gammastrahlungstechniken mit Filmen
- DIN EN ISO 17636-2:2013-05 Zerstörungsfreie Prüfung von Schweißverbindungen – Durchstrahlungsprüfung – Teil 2: Röntgen- und Gammastrahlungstechniken mit digitalen Detektoren
- DIN EN ISO 10675-1:2017-04 Zerstörungsfreie Prüfung von Schweißverbindungen – Zulässigkeitsgrenzen für die Durchstrahlungsprüfung – Teil 1: Stahl, Nickel, Titan und deren Legierungen
- DIN EN ISO 10675-2:2018-02 Zerstörungsfreie Prüfung von Schweißverbindungen – Zulässigkeitsgrenzen für die Durchstrahlungsprüfung – Teil 1: Aluminium und seine Legierungen
- DIN EN 12681-1:2018-02, Gießereiwesen – Durchstrahlungsprüfung – Teil 1: Filmtechniken
- DIN EN 12681-2:2018-02, Gießereiwesen – Durchstrahlungsprüfung – Teil 2: Technik mit digitalen Detektoren
Weblinks
Einzelnachweise
- https://www.zfp-muenchen.de/werkstoffpruefung/gammagraphie/ wbsite der Fa. ZFP-München - zerstörungsfreie Werkstoffprüfung GmbH zum Verfahren der Durchstrahlungsprüfung, abgerufen am 27. Juli 2018
- https://www.gfr-hattingen.de/de/technologie-normen/strahlenquellen website der Firma Gesellschaft für Radiographie mbH zu Strahlenquellen, abgerufen am 27. Juli 2018