Lift-off-Verfahren
Das Lift-off-Verfahren (englisch lift-off technique) ist in der Halbleiter- und Mikrosystemtechnik eine Prozessfolge zur Herstellung einer meist metallischen Mikrostruktur. In einem ersten Prozessschritt werden dabei strukturierte dünne Schichten auf der Oberfläche von Substraten wie beispielsweise Wafern erzeugt. Auf diese strukturierte Opferschicht wird dann das Zielmaterial ganzflächig abgeschieden. Jene Bereiche, in denen sich das Zielmaterial auf der Opferschicht befindet, werden anschließend durch einen weiteren Prozessschritt entfernt, und die verbliebenen Strukturen bilden die gewünschte Mikrostruktur. Die Größe der mit dem Lift-off-Verfahren herstellbaren Strukturen reicht von einigen zehn Nanometern[1] bis zu Zentimetern, wobei die typischen Strukturgrößen im Mikrometerbereich liegen. Eingesetzt wird das Verfahren unter anderem zur Herstellung von Leiterbahnebenen oder Kontaktflächen bei der Fertigung von integrierten Schaltungen (ICs) und Mikrosystemen. Im Gegensatz zu diesem additiven bzw. aufbauenden Verfahren stehen die subtraktiven Verfahren, bei denen zuerst ganzflächig eine homogene Schicht des Zielmaterials auf dem Substrat abgeschieden wird und die spätere Struktur durch Ätzen dieser Schicht entsteht.
Prozessbeschreibung
.svg.png.webp)
Das Lift-off-Verfahren ist eine relativ einfache und effiziente Folge aus verschiedenen Grundverfahren der Halbleitertechnik. Eine typische Prozessfolge besteht zum Beispiel aus der fotolithografischen Strukturierung, dem Schichtabscheiden und dem Entfernen der Fotolackschicht. Im Laufe der Zeit haben sich jedoch verschiedene Varianten entwickelt, wobei deren Möglichkeiten sehr von den verwendeten Prozessbedingungen bzw. -einstellungen abhängen. Im Folgenden werden daher nur die grundlegenden Prozessschritte beschrieben.
Der Lift-off-Prozess beginnt mit dem ganzflächigen Abscheiden der späteren Opferschicht (häufig Fotolack) auf einem vorbehandelten Substrat. Die Vorbehandlung umfasst in der Regel das Reinigen des Substrates und falls notwendig eine Planarisierung der Oberfläche (beispielsweise durch chemisch-mechanisches Polieren oder den Auftrag einer Haftvermittlerschicht). Anschließend erfolgt die fotolithografische Strukturierung der Opferschicht mit einem inversen Muster der späteren Struktur. Die Parameter der Opferschichtstrukturierung sollten dabei so eingestellt werden, dass sich hochgradig vertikale Seitenwände oder Seitenwände mit leichtem Unterschnitt (negativer Seitenwandwinkel) ergeben.
Nach der Strukturierung der Opferschicht folgt das ganzflächige Abscheiden des Zielmaterials, beispielsweise Aluminium, durch thermisches Verdampfen. Dabei sollte es zu keiner Verbindung zwischen dem abgeschiedenen Zielmaterial auf dem Substrat und dem Zielmaterial auf der Opferschicht kommen, damit zum einen diese Verbindung später nicht nachträglich aufgetrennt werden muss, zum anderen die Seitenflächen der Opferschicht weiterhin unbedeckt sind und somit die Entfernung der Opferschicht im letzten Prozessschritt nicht behindert wird. Eine Verbindung der beiden Bereiche kann durch zwei Rahmenbedingungen vermieden werden:
- Die Schichtdicke des Opfermaterials sollte mindestens dreimal so groß sein wie die des Zielmaterials, denn andernfalls wird die Opferschichtstruktur zu sehr gefüllt und blockiert spätere Prozessschritte.
- Der Beschichtungsprozess sollte eine schlechte Kanten- bzw. Seitenwandbedeckung aufweisen, so dass an der Seitenwand der Opferschicht möglichst kein Material abgeschieden wird. Hierfür eignen sich beispielsweise das thermische Verdampfen oder bestimmte Varianten der Sputterdeposition.
Beim Abscheiden des Zielmaterials ist weiterhin darauf zu achten, dass die Opferschicht diesen Arbeitsschritt unbeschadet übersteht. Für den Einsatz von Fotolack als Opferschicht bedeutet dies, dass die Prozesstemperatur die Glastemperatur des Fotolacks nicht überschreiten darf. Aus diesem Grund wird die Zielschicht meist bei Raumtemperatur abgeschieden und ist daher häufig amorph oder polykristallin.
Im letzten Prozessschritt wird die Opferschicht nasschemisch entfernt. Dazu kann beispielsweise der Fotolack in einem Lösungsmittel (z. B. Aceton) aufgelöst werden, gegebenenfalls mit Ultraschallunterstützung. Die Opferschicht wird dabei von den Seitenwänden (Flanken) her aufgelöst. Das Zielmaterial auf der Oberseite der Opferschicht wird mit abgehoben (englisch lift off) und weggewaschen. Danach verbleibt das Zielmaterial nur mehr in solchen Regionen, wo es einen direkten Kontakt mit dem Substrat hatte.
Typische Prozessfehler
.svg.png.webp)
Die fertige Struktur kann nach dem Auflösen der Opferschicht drei prozessbedingte typische Fehler aufweisen:[2]
- Zurückbleibendes Material: Dabei handelt es sich in der Regel um nicht aufgelöstes Opferschichtmaterial und das darauf befindliche Zielmaterial. Dieses Problem tritt auf, wenn das Opfermaterial von Zielmaterial umschlossen wurde und vom Lösungsmittel daher nur schlecht oder gar nicht angreifbar war.
- Wiederabscheidung: Darunter versteht man die Anlagerung von abgelöstem Material, welches sich wieder an der Oberfläche anlagert. Diese Partikel sind nach dem Prozess nur schwer bis überhaupt nicht entfernbar, vor allem nach dem Trocknen des Wafers.
- Grate: Dabei handelt es sich um Zielmaterial, das an den Seitenwänden der Opferschicht abgeschieden wurde und nach dem Entfernen der Opferschicht stehen bleibt. Solche Grate haben negative Auswirkungen auf nachfolgende Herstellungsschritte, denn sie erzeugen zum einen eine unerwünschte Topografie auf dem Wafer, die beispielsweise eine gleichmäßige Abscheidung einer weiteren Schicht behindert. Zum anderen können sie auch „umfallen“ und so einen elektrischen Kurzschluss erzeugen.
Die drei Fehlerbilder sind mehr oder weniger stark die Folge einer Seitenwandbedeckung der strukturierten Opferschicht durch Zielmaterial. Daraus folgt, dass eine gute Strukturqualität entscheidend vom Profil der Opferschicht und der „Kantenbedeckung“ des Beschichtungsverfahrens abhängt. Günstig sind hierbei eine Kombination aus unterschnittenen (negativen) Flanken oder Opferschichtsystemen, bei denen die unterste Schicht zurückgeätzt wurde, und einem Beschichtungsverfahren mit schlechter Kantenbedeckung.
Prozessvarianten
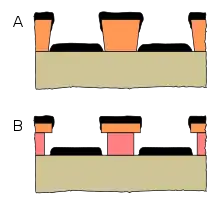
A) ein Einschichtsystem mit negativem Flankenwinkel, z. B. Fotolack mit Bildumkehrschritt
B) ein Zweischichtsystem, bei dem die untere Schicht nach der Strukturierung zurückgeätzt wurde.
Das Lift-off-Prinzip zur Herstellung von Metallstrukturen wurde bereits in den 1940er-Jahren vor den Anfängen der Mikroelektronik beschrieben.[3] Seitdem wurden in der Literatur zahlreiche Varianten entwickelt, die sich im Hinblick auf die abgeschiedene Schicht, die Opferschicht und die eingesetzte Chemie sowie zahlreiche Prozessparameter und die Anwendungsbereiche voneinander unterscheiden. Wie bereits erwähnt, nutzen einfache Verfahren eine Schicht aus Fotolack oder einem Polymer wie Polymethylmethacrylat (PMMA), wobei diese Opferschicht mittels konventioneller Fotolithografie strukturiert werden kann – erstmals 1969 durch Hatzakis[4] für die Herstellung von Leiterbahnen und Source/Drain-Kontakten aus Aluminium vorgestellt. Es wurden aber auch Prozessvarianten beschrieben, die Elektronenstrahl- oder Imprintlithografie nutzen. Weiter entwickelte Varianten nutzen mehr oder weniger komplexe Schichtstapel als Opferschicht, beispielsweise Fotolack/Aluminium/Fotolack-, Polyimid/Molybdän- oder Polyimid/Polysulfon/Siliziumdioxid-Stapel etc.[5] Der Einsatz eines zusätzlichen Ätzschritts[6], mit dem die Seitenkante der untersten Opferschicht zurückgeätzt wird, wirkt hierbei wie ein unterschnittenes Kantenprofil und verhindert die Ausbildung einer geschlossenen Schicht an den Seitenwänden.
Neben Prozessvarianten mit unterschiedlichen Opferschichten bzw. -schichtsystemen wurden auch Verfahren beschrieben, bei denen der Lift-off-Effekt nicht durch chemische Auflösung erfolgt, sondern durch Abheben der beschichteten Opferschicht mithilfe eines Klebebandes (tape-assisted lift off) oder durch eingebrachte Spannungen im Material (vgl. Carbon-Dioxide-Snow-Technik).[7]
Im Folgenden werden einige Prozessvarianten beispielhaft beschrieben.
Fotolithografie mit Bildumkehrschritt
.svg.png.webp)
Bei der Verwendung einer Fotolackopferschicht wird häufig ein sogenannter Umkehrschritt (engl. image reversal process) genutzt, mit dessen Hilfe ein unterschnittenes Kantenprofil erzeugt werden kann.[8][9][10] Dies ist mit einer einfachen fotolithografischen Strukturierung nur schwer möglich, da in den oberen Bereichen der Lackschicht Licht stets stärker absorbiert wird und sich so nach der Entwicklung ein Profil mit steilen Flanken oder Überschnitt ergibt, vgl. Schritt 2. in der nebenstehenden Abbildung. Umkehrfotolacke (engl. image-reversal resists) bieten die Möglichkeit der Bildumkehr (engl. image reversal) der Maske. Je nach eingesetztem Umkehrfotolack wird zwischen einem direkten (sauer-katalytischen) und einem indirekten (basischen) Umkehrprozess unterschieden, sie ergeben je nach Prozessführung ein negatives oder ein positives Abbild der Maske.
Bei sauer-katalytischen Umkehrfotolacken, beispielsweise einem Diazonaphtoquinon (DNQ)/Novolak-Fotolack in Kombination mit einem beigemischten säureaktivierbaren Polymerisator (z. B. Hexamethoxymethylmelamin, HMMM), entspricht die Prozessführung bis zur Belichtung weitgehend einer normalen fotolithografischen Strukturierung (Lackauftrag, soft bake etc.). Eine Entwicklung des Fotolacks (Positivlack) unmittelbar nach dieser Belichtung würde daher ein positives Abbild der Maskenstruktur ergeben. Durch einen zusätzlichen Umkehrprozess vor der Entwicklung werden die Löslichkeitsverhältnisse jedoch umgekehrt. Das heißt, nach der Belichtung werden unlösliche Bereiche löslich und umgekehrt. Erreicht wird dies im Wesentlichen durch zwei Teilschritte. Zunächst folgt auf die Belichtung ein sogenanntes Umkehrausheizen (engl. image reversal bake). Durch die Temperatureinwirkung werden in den belichteten Bereichen des Fotolacks Quervernetzungsreaktionen bewirkt und nach einer Ruhephase, in der eine ausreichende Rehydrierung sichergestellt wird (eine längere Lagerung an Luft ist dafür ausreichend), folgt der zweite Zusatzschritt. Eine Flutbelichtung des gesamten Wafers bewirkt in den noch unbelichteten Bereichen die Bildung von 3-Indencarbonsäure und macht diese Bereiche löslich gegenüber dem alkalischen Entwickler. Nach der Entwicklung entsteht so ein Negativbild der Maskenstruktur mit einem unterschnittenen Flankenprofil.[8]
Bei basischen Umkehrfotolacken wird die Fotolackschicht nach der Belichtung zunächst einem Amin-Dampf oder einer Ammoniak-Lösung ausgesetzt. Dabei diffundiert ein basischer Katalysator in die Schicht, der beim anschließenden Umkehrheizen zur Zersetzung der in den belichteten Bereichen gebildeten 3-Indencarbonsäure führt. Die so entstandenen Inden-Derivate sind sehr wirksame Löslichkeitshemmer. Vor der Entwicklung des Lacks erfolgt wie beim direkten Prozess eine Flutbelichtung, bei der die zunächst unbelichteten Bereiche belichtet und somit löslich werden.[8]
Bei beiden Prozessvarianten kann bei der ersten Belichtung durch die Variation der Belichtungszeit der Flankenwinkel des Fotolackprofils beeinflusst werden. Wie bereits erwähnt, geschieht dies aufgrund des tiefenabhängigen Absorptionsverhaltens des Lichts und des daraus resultierenden Vernetzungsgrades nach dem Umkehrheizen. Eine hohe Belichtungsdosis führt hierbei zu steilen Flanken und eine geringe Belichtungsdosis zu stark unterschnittenen Flanken. Mit einem solchen Profil kann beim Lift-off-Prozess das Risiko von undefinierten Abrisskanten an den Seitenwänden vermieden werden. Darüber hinaus erhält die entstehende Opferschicht eine erhöhte thermische Stabilität bis zu 200 °C.[8]
Elektronenstrahllithografie
Eine weitere Möglichkeit, ein unterschnittenes Fotolackprofil herzustellen, ist die Strukturierung der Opferschicht mittels Elektronenstrahllithografie.[11] Bei dieser Prozessvariante wird das Streuverhalten von Elektronen bzw. deren Energieverteilung in der Fotolackschicht ausgenutzt. Je nach Ausgangsenergie ergibt sich eine mehr oder weniger langgezogene, birnenförmige Energieverteilung. Für die Herstellung eines hinterschnittenen Profils kann der obere Bereich dieser Verteilung genutzt werden. Hier nimmt der Verteilungsquerschnitt mit zunehmender Tiefe ebenfalls zu. Um dieses Profil in einer nur wenige hundert Nanometer dicken Opferschicht zu erreichen, sind jedoch relativ geringe Energien notwendig, was wiederum das Auflösungsvermögen negativ beeinflusst. Dies gilt vor allem bei dichten Strukturen. Für die Fertigung von dichten Strukturen mit Linienbreiten im Bereich unterhalb 100 nm werden daher dennoch hohe Energien eingesetzt, auch wenn es damit schwieriger wird, die notwendige Profilhinterschneidung zu erreichen.
Abhilfe kann die Verwendung eines Doppelschicht-Fotolacksystems schaffen. Hierbei hat die untere Schicht eine wesentlich höhere Empfindlichkeit (z. B. 50-mal höher) als die obere Schicht, und es kann eine Profilhinterschneidung auch bei hoher Strahlungsenergie erreicht werden. Häufig verwendete Materialkombination für ein solches System ist ein Schichtstapel aus einer Deckschicht aus Polymethylmethacrylat (PMMA; mit hoher molarer Masse und geringerer Elektronenempfindlichkeit) und einer darunterliegenden Schicht aus einem seiner Copolymere (z. B. P(MMA-MAA) mit niedriger molarer Masse und höherer Elektronenempfindlichkeit).[11] Vorteilhaft an einer solchen Materialkombination ist, dass beide Schichten mit derselben Lösung entwickelt werden können.
Carbon-Dioxide-Snow-Technik
Eine neuere Lift-off-Variante nutzt gefrorene Kohlendioxid-Partikel (engl. carbon dioxide snow) zur Entfernung einer Metallschicht (Zielmaterial) auf der Fotolack-Opferschicht. Festes Kohlendioxid bildet sich bei Temperaturen unterhalb von −60 °C und damit deutlich unterhalb typischer Prozesstemperaturen bei der Beschichtung. Beim Abkühlen der Metall- und der Fotolackschicht kommt es aufgrund unterschiedlicher thermischer Ausdehnungskoeffizienten zu mechanischen Spannungen an der Grenzfläche der beiden Materialien, die zum Bruch bzw. zur Ablösung des Metallfilms führen. Das abgelöste Metall wird anschließend durch einen Kohlendioxid-Strahl mit Geschwindigkeiten von bis zu 40 m/s abgenommen. Üblicherweise wird dabei die Rückseite des Substrats auf bis zu +60 °C erwärmt, was die mechanische Spannung an den Grenzflächen nochmals erhöht und gleichzeitig die mechanischen Spannungen zwischen den gewünschten Metallstrukturen auf dem Substrat reduziert. Nach dem Ablösen der Metallschicht von der Opferschicht kann diese leicht nasschemisch oder durch Plasmaveraschung entfernt werden. Der Vorteil dieser Methode ist, dass die metallischen Partikel sofort abgeführt werden und die Probenoberfläche somit besser gegen eine wiederholte Abscheidung geschützt ist.[12]
Anwendung
Das Lift-off-Verfahren ist eine sehr allgemeine Herstellungsmethode, mit der sich prinzipiell alle Metalle und ihre Legierung sowie Mehrfachschichten strukturieren lassen. Da hierbei, anders als bei einer subtraktiven Strukturierung durch Ätzen, keine auf die zuätzenden Materialien abgestimmten Ätzprozesse bzw. Ätzchemie benötigt werden, kann hierbei immer annähernd der gleiche Lift-off-Prozess genutzt werden. Es muss nur eine ähnliche Abscheidung des Zielmaterials gewährleistet sein.
Das Verfahren bietet beispielsweise in folgenden Fällen Vorteile:
- In Fällen, bei denen kein direktes Ätzen mit genügend hoher Selektivität für die bereits abgeschiedenen Materialien zur Verfügung steht.
- Bei Mehrfachschichten, bei denen zunächst die Einzelschichten nacheinander aufgebracht und anschließend gemeinsam strukturiert werden.
- Bei Materialien wie Aluminium-Kupfer-Legierungen, die schwer entfernbare Rückstände bilden, wenn sie durch das Trockenätzen strukturiert werden.
Des Weiteren bieten die geneigten Seitenwände Vorteile bei der Abscheidung von Schichten in nachfolgenden Prozessebenen, etwa eine höhere Leiterbahnebene bei der Metallisierung des ICs. Denn anders als bei den steilen Seitenwänden, wie sie typischerweise beim Trockenätzen entstehen, können die Seitenflächen des mit Lift-off strukturierten Materials mit einer breiteren Auswahl von Verfahren beschichtet werden. Auch zeigt die Oberfläche deutlich weniger Sprünge in der Topografie, so dass unter anderem mit Rotationsbeschichtung hergestellte Schichten (z. B. Fotolackschichten für nachfolgende Prozesse) homogener aufgetragen werden können. Angewendet wird das Verfahren daher vor allem für die Strukturierung von metallischen Schichten.[13] Es ermöglicht die Herstellung von Leiterbahnen mit Strukturen im Mikrometerbereich für die Fertigung von diskreten Bauelementen und auch von (für heutige Verhältnisse) relativ einfachen integrierten Schaltkreisen mit bis zu vier[14] Leiterbahnebenen.
Trotz der genannten Vorteile hat sich das Lift-off-Verfahren für die Herstellung der Verdrahtungsebenen von integrierten Schaltkreisen nicht gegenüber der Strukturierung mittels Trockenätzen durchsetzen können; aktuell wird in diesem Bereich der Damascene- und Dual-Damascene-Prozess in größerem Umfang eingesetzt. Gründe hierfür sind unter anderem die verhältnismäßig geringe Auflösung sowie die aufwendigere Herstellung der strukturierten Opferschicht, da hier auf die Kompatibilität der chemischen und physikalischen Eigenschaften der Opfer- und Zielschicht beim Abscheidungs- und Auflösungsprozess geachtet werden muss.[15]
Analog zur Herstellung von Leiterbahnen kann Lift-off auch zur Herstellung von Bumps eingesetzt werden. Dabei handelt es sich um metallische (meist eine Blei-Zinn-Legierung) Kontaktelemente zur Direktmontage der Chips, beispielsweise für das Tape-Automated Bonding oder die Flip-Chip-Montage. Auch hier gibt es mehrere Prozessvarianten, die auch mit dem Lift-off-Verfahren hergestellte Kupferkontaktflächen inklusive Kupferdiffusionsbarrieren umfassen können. Für weitere Informationen sei hier auf die Literatur[16] verwiesen.
Heutzutage wird Lift-off als ein gängiges Verfahren bei der Fertigung von Bauelementen im Nanometerbereich (z. B. Einzelelektronentransistoren oder Mikro-SQUIDs) eingesetzt. Hierbei wird meistens eine Elektronenstrahllithografie in Kombination mit einem Positivfotolack, in der Regel Polymethylmethacrylat (PMMA), verwendet. Begrenzt wird das Verfahren vor allem durch die begrenzte Auflösung der lithografischen Strukturierung und durch die Korngröße des abgeschiedenen Materials. So kann eine Linienstruktur unterbrochen sein, wenn die Korngröße im Bereich der Linienbreite liegt.[17]
Literatur
- Zheng Cui: Nanofabrication: principles, capabilities and limits. Springer, 2008, ISBN 978-0-387-75576-2, S. 218–225 (eingeschränkte Vorschau in der Google-Buchsuche – Hauptquelle für die Prozessvarianten).
- Friedemann Völklein, Thomas Zetterer: Praxiswissen Mikrosystemtechnik. Grundlagen – Technologien – Anwendungen; mit 55 Tabellen. 2., vollst. überarb. u. erw. Auflage. Vieweg+Teubner, 2006, ISBN 3-528-13891-2.
- Kenneth A. Jackson, Wolfgang Schröter (Hrsg.): Handbook of Semiconductor Technology: Electronic structures and properties of semiconductors. Wiley-VCH, 2000, ISBN 3-527-29834-7, S. 587–590.
Weblinks
- Gary E. McGuire: Development of liftoff processes for patterning of magnetic and other materials. Abgerufen am 5. Februar 2012.
- Liftoff Processes. Stanford Nanofabrication Facility, 29. August 2003, archiviert vom Original am 25. Februar 2001; abgerufen am 5. Februar 2012.
Einzelnachweise
- Zheng Cui: Nanofabrication: principles, capabilities and limits. Springer, 2008, ISBN 978-0-387-75576-2, S. 219.
- Kenneth A. Jackson, Wolfgang Schröter (Hrsg.): Handbook of Semiconductor Technology: Electronic structures and properties of semiconductors. Wiley-VCH, 2000, ISBN 3-527-29834-7, S. 587–590.
- Patent US2559389: Method of Producing Precision Images. Angemeldet am 2. April 1942, Erfinder: Allan R. A. Beeber, David D. Jacobus, Carl W. Keuffel.
- M. Hatzakis: Electron Resists for Microcircuit and Mask Production. In: Journal of The Electrochemical Society. Band 116, Nr. 7, 1. Juli 1969, S. 1033–1037, doi:10.1149/1.2412145.
- Stanley Wolf, Richard N. Tauber: Silicon Processing for the VLSI Era. Volume 1: Process Technology. 2. Auflage. Lattice Press, 2000, ISBN 0-9616721-6-1, S. 535–536.
- vgl. u. a. Patent US3849136: Aluminum Gap. Angemeldet am 31. Juli 1973.
- Helbert Helbert: Handbook of VLSI Microlithography, 2nd Edition: Principles, Tools, Technology and Applications. 2. Auflage. William Andrew Inc, 2001, ISBN 0-8155-1444-1, S. 730–733.
- Friedemann Völklein, Thomas Zetterer: Praxiswissen Mikrosystemtechnik. 2., vollst. überarb. u. erw. Auflage. Vieweg+Teubner, 2006, ISBN 3-528-13891-2, S. 96–97.
- Kenneth A. Jackson, Wolfgang Schröter (Hrsg.): Handbook of Semiconductor Technology: Electronic structures and properties of semiconductors. Wiley-VCH, 2000, ISBN 3-527-29834-7, S. 234–235.
- William B. Glendinning, John N. Helbert: Handbook of VLSI microlithography: principles, technology, and applications. William Andrew, 1991, ISBN 0-8155-1281-3, S. 117–122.
- Zheng Cui: Nanofabrication: principles, capabilities and limits. Springer, 2008, ISBN 978-0-387-75576-2, S. 220–221 (eingeschränkte Vorschau in der Google-Buchsuche).
- F. Radulescu u. a.: Introduction of Complete Sputtering Metallization in Conjunction with CO2 Snow Lift-Off for High Volume GaAs Manufacturing. In: Proc. GaAs MANTECH Conference. 2002 (PDF). PDF (Memento des Originals vom 13. Mai 2015 im Internet Archive) Info: Der Archivlink wurde automatisch eingesetzt und noch nicht geprüft. Bitte prüfe Original- und Archivlink gemäß Anleitung und entferne dann diesen Hinweis. Zitiert nach: Zheng Cui: Nanofabrication: principles, capabilities and limits. Springer, 2008, ISBN 978-0-387-75576-2, S. 223 (eingeschränkte Vorschau in der Google-Buchsuche).
- Kenneth A. Jackson, Wolfgang Schröter (Hrsg.): Handbook of Semiconductor Technology: Electronic structures and properties of semiconductors. Wiley-VCH, 2000, ISBN 3-527-29834-7, Metallization and Liftoff Processes, S. 581–590.
- Stanley Wolf: Silicon Processing for the VLSI Era. Volume 2: Process Integration. Lattice Press, 1990, ISBN 0-9616721-4-5, S. 285.
- L. J. Fried, J. Havas, J. S. Lechaton, J. S. Logan, G. Paal, P. A. Totta: A VLSI Bipolar Metallization Design with Three-Level Wiring and Area Array Solder Connections. In: IBM Journal of Research and Development. Band 26, Nr. 3, 1. Mai 1982, S. 362–371, doi:10.1147/rd.263.0362.
- Herbert Reichl: Direktmontage. Gabler Wissenschaftsverlage, 1998, ISBN 3-540-64203-X, S. 18–45.
- Zheng Cui: Nanofabrication: principles, capabilities and limits. Springer, 2008, ISBN 978-0-387-75576-2, S. 219 (eingeschränkte Vorschau in der Google-Buchsuche).