Surface-mounted device
Surface-mounted device (SMD, deutsch: oberflächenmontiertes Bauelement) ist ein englischsprachiger Fachbegriff aus der Elektronik. SMD-Bauelemente haben im Gegensatz zu Bauelementen der Durchsteckmontage (englisch through hole technology, kurz THT), den bedrahteten Bauelementen, keine Drahtanschlüsse, sondern werden mittels lötfähiger Anschlussflächen oder -beinchen direkt auf eine Leiterplatte gelötet (Flachbaugruppe). Die dazugehörige Technik ist die Oberflächenmontage (englisch surface-mounting technology, kurz SMT).

Übersicht
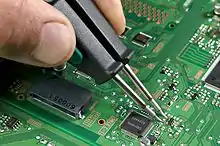
Während die Anschlussdrähte konventioneller Bauelemente durch Bestückungslöcher geführt werden und auf der Rückseite der Leiterplatte (oder über Innenlagen) verlötet werden müssen (Durchkontaktierung), entfällt dies bei SMD-Bauelementen. Dadurch werden sehr dichte Bestückungen und vor allem eine beidseitige Bestückung der Leiterplatte möglich. Die elektrischen Eigenschaften der Schaltungen werden speziell bei höheren Frequenzen positiv beeinflusst. Der Platzbedarf der Bauelemente verringert sich. Dadurch können die Geräte kleiner und zugleich wesentlich kostengünstiger hergestellt werden.
SMD-Bauteile werden nach der Herstellung in Gurten, Stangenmagazinen oder auf Blister-Trays transportiert und mit Automaten auf Leiterplatten bestückt. Eine manuelle Bestückung ist bei kleinen Stückzahlen möglich. Die Anschlussflächen für die SMD-Bauteile auf den Platinen werden vor dem Bestücken mittels Schablonendruck (lasergeschnittene Lotpastenmaske) oder mittels maschinellem Auftragen mit Lotpaste bedeckt. Anschließend werden die Bauteile aufgesetzt. Nach dem Bestücken werden die SMD-Bauteile mit Wärme gelötet. Für die Oberseite einer Platine hat sich dafür das Reflow-Verfahren durchgesetzt. SMD-Bauteile auf der Unterseite einer Leiterplatte werden aufgeklebt und im Wellen- oder Schwallbad gelötet.
Die Miniaturisierung der SMD-Bauteile macht es schwieriger, die Lötqualität von Leiterplatten mit SMD-Bauteilen mit dem bloßen Auge oder mit Hilfe eines Mikroskops zu kontrollieren. Es wird Bildverarbeitung (AOI-Systeme, englisch: automated optical inspection) eingesetzt, die nicht nur Bestückungsfehler, sondern teilweise auch Lötfehler erkennen kann. Nicht erkennbar für die AOI sind Lötfehler bei QFN, Ball Grid Array und ähnlichen Bauteilen, die keine sichtbaren konkaven Lotflächen zeigen.
Für Handbestücker ergibt sich durch die SMD-Technik der Nachteil, dass sich manche SMD-Bauteile nur sehr schwer ohne Maschinen oder entsprechendes Know-how verlöten lassen. Mit Pinzette, einer feinen Lötspitze und 0,5-mm-Lötzinn und einer Lupenbrille, eventuell einem Stereomikroskop, lassen sich jedoch viele Baugrößen verarbeiten. Die Bestückung ist teilweise sogar schneller als bei Handbestückung bedrahteter Bauteile, da die Bauteilvorbereitung jener (Ablängen, Biegen, Fixieren) entfällt. Die Verwendung klassischer Lochrasterkarten und Streifenrasterkarten ist für Versuchsaufbauten oder Prototypen nur eingeschränkt möglich. Geeignete Laborkarten und Adapter sind jedoch im Handel erhältlich oder selbst herstellbar.
Das Recycling von Bauelementen aus Altgeräten ist durch schwierige Entlötbarkeit und teilweise mehrdeutige Kennzeichnung bei SMT schwieriger.
Geschichte
Entwicklung der Oberflächenmontagetechnik (SMT)
Die Oberflächenmontagetechnik wurde in den 1960er-Jahren von IBM entwickelt und fand ihre erste Anwendungen in den Computern der Saturn- und Apollo-Missionen.[1] Begründet wurde diese Entwicklung mit den beengten Raum- und Platzverhältnissen in den Raumkapseln sowie mit der Reduzierung der Schaltungsimpedanz zur Erhöhung der Schaltfrequenzen.
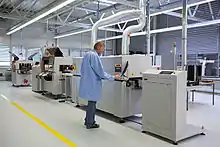
In den 1970er Jahren wurde die Digitaltechnik zur treibenden Kraft für die Lösungen von Konzepten für elektronische Schaltungen für völlig neue Geräte wie z. B. Taschenrechner oder auch für konventionelle Geräte der Rundfunk- und Fernsehtechnik. 1976 wurde beispielsweise der erste Homecomputer Apple 1 präsentiert[2] und einige Jahre später, 1983, wurde das erste digitale „one-chip IC“ für UKW-Radios von Philips entwickelt.[3] Parallel dazu begann die Industrie ab Mitte der 1970er Jahre die Bauelemente mit genormten Rastermaßen für Leiterplattenmontage anzubieten,[4] da der Leiterplattenentwurf mittels „Computer-Aided Designs“ (CAD) mit genormten, vorgegebenen Maßen für die Bauelemente großen Vorteil bot. (Das von IBM entwickelte Programmiersystem APT, welches der rechnerunterstützten Programmierung von NC-Maschinen diente, wurde in den 1950er Jahren entwickelt[5][6])
Gleichzeitig wurden die ersten Bestückungsautomaten zur automatischen Bestückung bedrahteter Bauelemente entwickelt. Anfang der 1980er Jahre standen im Grundig-Werk 16, Nürnberg-Langwasser, Bestückungsautomaten, die für 500.000 Farbfernsehgeräte pro Jahr ausgelegt waren.[7] In diesen Jahren wurden die ICs immer komplexer. Die Anzahl der Schaltungsfunktionen, die auf einem Halbleiterkristall integriert wurden, stieg von Jahr zu Jahr an (Mooresches Gesetz) Mit der ansteigenden Integration stiegen die Betriebsfrequenzen der Schaltungen an und es galt, mit kürzeren Leitungsführungen die Leitungsimpedanz zu verringern. Die von IBM entwickelte Oberflächenmontagetechnik bot hier die Möglichkeit, durch Fortfall der Bohrungen die Leitungsführungen zu verkürzen.
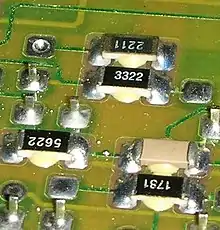
Allerdings waren die Investitionskosten für diese neue Montagetechnik sehr hoch. Es mussten für alle Fertigungsschritte neue Automaten entwickelt werden. Die erforderlichen hohen Investitionskosten konnten nur von Geräteherstellern mit großen Stückzahlen aufgebracht werden, die überwiegend in Japan und den USA ansässig waren. 1979 wurde die erste SMD-Fertigungslinie in Japan installiert, zwei Jahre später in den USA.[8] In Europa und in Deutschland war Philips mit seiner Bauelementetochter Valvo ab 1984 Vorreiter für die SMD-Technik mit ihren Bauelementen einschließlich der erforderlichen Bestückungsanlagen.[9] Die Bestückungsfrequenz dieser neuen SMD-Vollautomaten war deutlich höher als die der Automaten für bedrahtete Bauelemente. Es konnten mit diesen Automaten Bestückungsgeschwindigkeiten von 7000 bis zu 540.000 SMDs pro Stunde erreicht werden.[9]
Die Entwicklung der Automaten für die Oberflächenmontagetechnik Ende der 1970er Jahre war von den Herstellern von Anfang an in ein Gesamtkonzept mit hohen Qualitätsanforderungen eingebunden. Es umfasste die Standardisierung der Bauelemente über ihre gegurtete Anlieferweise bis hin zu ihren genormten Landeflächen und der Reflow-Lötfähigkeit bzw. der Fähigkeit der Wellen-Lötbarkeit, die Bestückungsautomaten mit hohen Anforderungen an die Reinheit und hohe Genauigkeit beim Kleben, hohe Präzision der Passgenauigkeit beim Bestücken sowie die präzise Temperatursteuerung bei der Lötung. Entscheidend für den Erfolg dieser Technik war, dass die Oberflächenmontagetechnik als ganzheitliches Konzept betrachtet und realisiert wurde. Mit dieser Technik konnte die Leitungsimpedanz und das Bauvolumen für die Gesamtschaltung deutlich reduziert werden, die Herstellungskosten sanken, da die Kosten für die Bohrungen in den Leiterplatten und die zusätzlicher Anschlüsse an den Bauelementen entfielen und die Qualität der Schaltungen stieg mit der größeren Sauberkeit bei der Herstellung an. Ab Mitte 1980 wurden bereits SMD-Schaltungen in vielen Bereichen der Industrie im großen Stil verwendet, wobei die Schaltung häufig als „Mixed Print“ ausgelegt war, d. h., die größeren Bauelemente weiterhin bedrahtet eingesetzt wurden.
Entwicklung der SMD-Bauelemente
Die anfänglich für die Raumfahrt benötigten Bauelemente kamen aus den USA von den seinerzeit führenden Herstellern wie IBM, Texas Instruments, Fairchild, Sprague u. a. Es waren die damals verfügbaren Bauelemente, wie Transistoren und Dioden, ICs, Kondensatoren und Widerstände, deren Anschlüsse für den Einsatz in der Oberflächen-Montagetechnik modifiziert waren oder durch lötbare Metallkappen ersetzt waren. Die treibende Kraft waren Integrierte Schaltungen, die die gewünschte Volumenverkleinerung der Geräte brachten, indem die Gehäuse kleiner werden konnten.
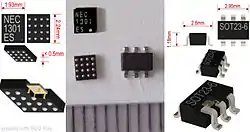
Es war oft einfach, aus dem jeweiligen bedrahteten Gehäuse ein SMD-Gehäuse zu machen, so wurden Dioden und Widerstände ohne Anschlussdrähte gefertigt, es entstanden die Bauformen MELF und Mini-MELF.
Hochintegrierte ICs bekamen immer mehr Anschlüsse. Hatte 1971 der 4-Bit-Prozessor Intel 4004 noch 16 Anschlüsse, so hatte 1978 der erste 16-Bit-Mikroprozessor Intel 8086 bereits 40 Anschlüsse. Die Geometrie der Halbleiter-Gehäuse wurde angepasst. In SMT konnten mehr Anschlüsse pro Länge an der Bauteilkante untergebracht werden. Das anfangs für THT übliche Rastermaß von 2,54 mm sank auf z. B. 0,5 mm.
Anfang 1970 begann die Entwicklung der Keramik-Vielschichtkondensatoren (MLCCs), die kennzeichnend für fast alle SMD-Schaltungen wurden.[10]
Mit der Oberflächenmontagetechnik nahm in den 1980er Jahren der Druck zu SMD-Bauformen auch für weitere Kondensator-Typen zu und Aluminium-Elektrolytkondensatoren und auch Folienkondensatoren wurden als SMD verfügbar. Das Kapazitäts-Volumen-Produkt dieser Kondensatoren nahm etwa um den Faktor 10 zu (siehe auch Kondensator (Elektrotechnik)#Weiterentwicklung).
Während Tantalkondensatoren von Anfang an auch in SMD-Bauformen angeboten wurden, waren Aluminium-Elkos erst Ende der 1980er Jahre als SMD verfügbar. Die Problematik ist, dass der flüssige Elektrolyt einen Siedepunkt hat, der unter der Temperaturspitze der Reflow-Lötung liegt. Erst durch Verstärkung der Materialien konnte der interne Gasdruck aufgefangen werden, der sich dann nach geraumer Zeit wieder zum Elektrolyten zurückbildet.[11][12] Um Folienkondensatoren in SMD zu erhalten, sind temperaturstabile Folien erforderlich.
Im Bereich der Widerstände wurden zunächst die Kappen der axialen Bauformen statt mit Drähten lötfähig gestaltet und als MELF angeboten.[9] Später wurden die bereits bekannten Dickschicht-Widerstände auf Keramik-Substraten weiterentwickelt, indem sie rechteckige Formen erhielten und beidseitig lötfähig metallisiert wurden.
Auch elektromechanische Bauelemente wie beispielsweise Steckverbinder, Schwingquarze oder Relais sind als SMD entwickelt worden – fast alle der in der Liste elektrischer Bauelemente genannten Teile sind auch als SMD verfügbar.
Vor- und Nachteile bei der Verwendung von SMDs
SMD-Bauelemente haben in vielen Anwendungsfällen Bauelemente mit durchkontaktierten Anschlussdrähten abgelöst. Sie besitzen gegenüber jenen unter anderem folgende Vor- und Nachteile:
Vorteile:
- Miniaturisierung, deutliche Verkleinerung von Schaltungen und Geräten durch kleinere Bauteilabmessungen (ergibt höhere Bauteildichte), engeren Leiterbahnabstand und dünnere Leiterbahnen auf der SMD-Platine.
- Eignung für flexible Leiterplatten, etwa in Fotoapparaten oder auf LED-Lichtbändern.
- Kostenreduzierung, Bohrungen in der Leiterplatte entfallen, die Leiterplatte wird kostengünstiger, insbesondere wenn durch die SMD-Technik auf einlagige Leiterplatten ohne Bohrungen zurückgegriffen werden kann.
- Gewichtsreduzierung durch Wegfall von Anschlussdrähten und Verwendung kleinerer Bauelemente.
- Verbesserung von Hochfrequenzeigenschaften durch geringeren Bauteilabstand zueinander und Verkürzung von Leiterbahnen (kleinere ohmsche Verluste, geringere Induktivität der kürzeren Leiterbahnen). Bauelemente können auf beiden Seiten der Leiterkarte auch direkt übereinander bestückt werden (wichtig bei Hochfrequenzbaugruppen).
- Schnellere Gerätefertigung durch schnelle Automatenbestückung (Collect & Place / Pick & Place / Chip-Shooter), dadurch ergeben sich geringere Fertigungskosten.
- Steigerung der Fertigungsqualität bei automatischer Bestückung.
- Steigerung der Fertigungsqualität durch Wegfall von Verschmutzungsquellen (Schneiden und Biegen der Anschlussdrähte)
- Steigerung der Fertigungsqualität durch automatische optische Inspektion (AOI) aller kritischen, optisch prüfbaren Faktoren bei den meisten SMD-Bauformen möglich.
- Kleine Positionierungsfehler bei der Bestückung werden beim Löten automatisch durch die Oberflächenspannung des flüssigen Lots korrigiert.
- Platinen mit glatter Rückseite herstellbar, bspw. für Fernbedienungen und Tastaturen – oder hobbymäßig als Gehäuseteil.
Nachteile:
- Bei Bauelementen mit Anschlüssen an der Unterseite (wie BGAs) können die Lötstellen nur noch mittels Röntgen überprüft werden.
- Durch das Reflow-Löten werden die kompletten Bauteile kurz einer hohen Temperatur ausgesetzt (> 200–250 °C). Beispielsweise Aluminium-Elektrolytkondensatoren, Superkondensatoren oder Akkumulatoren führen zu Problemen. Änderungen der Kennwerte sind auch bei weiteren Bauteilen nur bei genauer Einhaltung des Temperaturprofiles zu vermeiden.
- Festigkeitsprobleme treten bei großen, schweren Bauelementen auf.
- Biegebeanspruchung der Leiterplatte kann zu Kontaktierfehlern und Bauteilrissen führen.
SMD-Anschlussformen
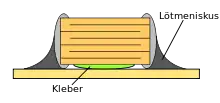
Passive Bauelemente wie Widerstände, Kondensatoren, Quarze oder induktive Bauelemente wie Drosseln werden oft in quaderförmigen Bauformen hergestellt. Zwei oder mehr Seitenflächen sind zur elektrischen Kontaktierung lötfähig ausgebildet. Eine einwandfreie Lötung dieser Bauteile kann am Lötmeniskus erkannt werden.
Transistoren und auch integrierte Schaltungen entstanden zu Beginn der SMD-Technik aus dem (bedrahteten) Dual-In-Line-Gehäuse (DIL-Gehäuse), einem Gehäuse, bei dem an den beiden Seitenflächen die Lötanschlüsse des Bauelementes herausgeführt sind. Die senkrechten Lötanschlüsse dieses Gehäuses wurden dann für die SMD-Lötung einfach entweder seitlich nach außen (englisch Gull-Wing) oder nach innen (englisch J-Leads) abgebogen. Die fortschreitende Integrationsdichte führte zur Entwicklung der Grid-Arrays. Hier befinden sich die Lötanschlüsse als kleine metallisierte Anschlussflächen unter dem Gehäuse. Beim Ball Grid Array (BGA) sind bereits Lotperlen auf den Kontaktflächen des Bauteils angebracht, die während des Lötprozesses nur noch aufgeschmolzen werden. Beim Land Grid Array (LGA) muss dagegen Lot auf der zu bestückenden Platine aufgebracht sein, weswegen LGA-Bauteile selten zum Verlöten verwendet werden – sie werden oft auf einem dazu passenden Pin-Array betrieben und können so leicht ausgewechselt werden.
- SMD-Anschlussformen
- SMD-Lötflächen an den Seitenflächen des Bauteils wie z. B. bei SMD-Keramik-Vielschichtkondensatoren (MLCC)
- Gull-Wing-Lötanschlüsse an den Gehäuseseiten einer Integrierten Schaltung
- J-Lead-Lötanschlüsse an den Gehäuseseiten einer Integrierten Schaltung (veraltend)
- Lotperlen unter einem Mikroprozessor mit BGA
- Schachbrettartig angeordnetes LGA unter dem Gehäuse eines Mikroprozessors
SMD-Bauformen, SMD-Gehäuse
Passive SMD (Widerstände, Kondensatoren, Induktivitäten, Quarze usw.) unterscheiden sich durch ihre Bauform (englisch style)[13], während sich aktive Bauelemente (Transistoren oder IC) durch ihr Gehäuse (Chipgehäuse) unterscheiden. Das Die muss zur Löt-Kontaktierung in einem Gehäuse untergebracht sein.
Jedes Gehäuse hat einen eigenen Namen, der sich aus den ersten Buchstaben der englischen Beschreibung ergibt. Abweichungen innerhalb gleicher Gehäusebezeichnungen, die sich durch die Anzahl und der Anordnung der Anschlüsse und der Form der Anschlüsse ergeben, werden durch an den Namen angehängte Zahlen gekennzeichnet.
SMD-Bauformen passiver Bauelemente, Dioden und Transistoren
Passive Bauelemente und gegebenenfalls auch Dioden und Transistoren werden in folgenden Bauformen hergestellt, geliefert und verarbeitet:
- SMD-Bauformen
- „Chip“, quaderförmige SMD-Chip-Bauform für Kondensatoren und Widerstände mit Lötanschlussflächen an den Seitenflächen des Gehäuses
- V-Chip, vertikal-zylindrische SMD-Bauform für Aluminium-Elektrolytkondensatoren
- horizontal liegende SMD-Bauform für Widerstände (Melf) und Dioden (SOD)
- SMD-Transistor (BC817-40); Typische Anschlussbelegung: Basis / Kollektor / Emitter.
Chip, eine quaderförmige Bauform, ist die typische Bauform für MLCC- und Tantal-Kondensatoren, Induktivitäten sowie nichtlineare und lineare Widerstände (R-Chips). Der Begriff „Chip“ kann leicht mit dem gleichlautenden Begriff aus der Halbleitertechnik, dem „Chip“ (englisch „Die“) eines Halbleiter-Bauelementes verwechselt werden. Quaderförmigen Sonderbauformen für z. B. Quarze oder Oszillatoren können am Gehäuse auch noch zusätzliche Lötflächen, entweder für Verpolungsschutz oder zur besseren und vibrationsfesteren mechanischen Befestigung enthalten.
Die Chip-Bauform passiver Bauelemente unterscheidet sich im Wesentlichen durch die Baugröße, die mit einem Code wie „1206“ angegeben wird. Dabei steht „12“ für die Länge und „06“ für die Breite des Bauteils in der Einheit Zoll/100. Die Abmessungen sind dabei metrisch standardisiert worden, bei der Umrechnung in den Zoll-Code werden jedoch nur zwei Stellen benutzt, was zu entsprechenden Rundungsfehlern führt. So beträgt die Länge eines mit dem Code „1206“ bezeichneten Bauteils 3,2 mm oder 0,12598 Zoll, aber nur die „12“ wird zur Bezeichnung benutzt. Rechnet man diese zurück, käme man nur auf 3,048 mm.
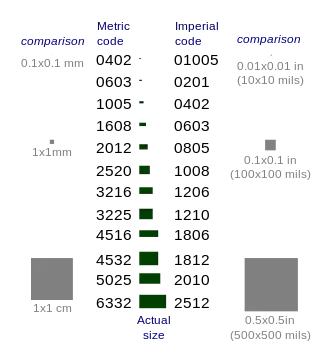
Gehäusegröße, Zoll-Code |
Gehäusegröße, metrischer Code |
Gehäuselänge L in mm (± 0,2 mm) |
Gehäusebreite B in mm (± 0,2 mm) |
SMD-C-Chip (MLCC) |
SMD-Ta-Chips1) | SMD-R-Chip |
---|---|---|---|---|---|---|
008004 | 0201[14] | 0,25 | 0,13 | X | ||
009005[15] | 03015[16] | 0,30 | 0,15 | X | – | X |
01005 | 0402 | 0,4 | 0,2 | X | – | X |
0201 | 0603 | 0,6 | 0,3 | X | – | X |
0402 | 1005 | 1,0 | 0,5 | X | – | X |
0603 | 1608 | 1,6 | 0,8 | X | – | X |
0805 | 2012 | 2,0 | 1,2 | X | R | X |
1020 | 2550 | 2,5 | 5,0 | – | – | X |
1206 | 3216 | 3,2 | 1,6 | X | A | X |
1210 | 3225 | 3,2 | 2,5 | X | – | X |
1218 | 3146 | 3,1 | 4,6 | – | – | X |
1225 | 3164 | 3,1 | 6,4 | – | – | X |
1411 | 3528 | 3,5 | 2,8 | – | B | – |
1808 | 4520 | 4,5 | 2,0 | X | – | – |
1812 | 4532 | 4,5 | 3,2 | X | – | – |
2010 | 5025 | 5,0 | 2,5 | – | – | X |
2220 | 5750 | 5,7 | 5,0 | X | – | – |
2312 | 6032 | 6,0 | 3,2 | – | C | – |
2512 | 6330 | 6,3 | 3,0 | – | – | X |
2917 | 7343 | 7,3 | 4,3 | – | D | – |
2924 | 7361 | 7,3 | 6,1 | X | – | – |
1) Ta-Chips werden mit einem Buchstabencode gekennzeichnet. Sie werden in unterschiedlichen Bauhöhen gefertigt |
Erweiterte Tabellen der verfügbaren Chip-Baugrößen und deren Abmessungen finden sich auch bei den Fachartikeln der Bauelemente Keramikkondensatoren, Tantal-Elektrolytkondensatoren und Widerstände.
- V-Chip (vertical Chip) ist eine zylindrische Bauform mit Unterlegplättchen, stehend montiert. Insbesondere Aluminium-Elektrolytkondensatoren werden in dieser Bauform geliefert und verarbeitet. Die Baugrößen dieser Bauform sind nicht genormt. V-Chip-Aluminium-Elektrolytkondensatoren können recht große Abmessungen erreichen; es sind die Exoten unter den SMD-Bauelementen.
- MELF (Metal Electrode Faces), ist die Bezeichnung für eine zylindrische Bauform passiver Bauelemente, die liegend montiert werden. Sie ist die typische Bauform für Metallschichtwiderstände und nichtlineare Widerstände.
- SOD (Small Outline Diode), wird das zylindrische Gehäuse für das Halbleiterbauelement Diode, das wie die MELF-Bauform ebenfalls liegend montiert wird, genannt. Auch das SOD-Gehäuse wird in unterschiedlichen Baugrößen geliefert.
Bauelemente wie Potentiometer, Trimmer, Transformatoren, Übertrager, Quarze, Oszillatoren, Taster, Sockel, Stecker und Buchsen haben oft spezielle Bauformen.
Lötanschlüsse an zwei Seiten des Gehäuses
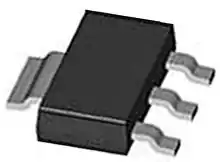
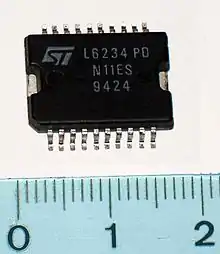
SMD-Transistorgehäuse mit Lötanschlüssen an zwei Seiten des Gehäuses werden mit den folgenden Gehäusenamen gekennzeichnet:
- SOT (small outline transistor): Bauform mit drei oder vier Anschlüssen für Transistoren, der vierte Anschluss ist oft als Wärmeableitelement (englisch heatsink) ausgeführt, Anschlussabstand typisch 1,27 mm
IC-Gehäuse mit Lötanschlüssen an zwei Seiten des Gehäuses werden mit den folgenden Gehäusenamen gekennzeichnet:
- SOIC (small-outline integrated circuit): IC-SMD-Gehäuse mit dem gleichen Reihenabstand wie die Durchsteck-Version, der Anschlussabstand ist typisch 1,27 mm
- SOP (small outline package): kleinere Version des SOIC-Gehäuses, bildet die Grundlage für eine ganze Reihe von Abwandlungen, die zum Teil herstellerspezifisch sind, beispielsweise:
- PSOP (plastic small-outline package)
- TSOP (thin small-outline package): Anschlüsse auf der Schmalseite des Gehäuses,
- SSOP (shrink small-outline package)
- TSSOP (thin shrink small-outline package)
- QSOP (quarter-size small-Outline package)
- VSOP (very small outline package)
Lötanschlüsse an vier Seiten des Gehäuses
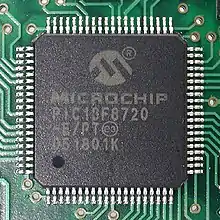
IC-Gehäuse mit Lötanschlüssen an den vier Seiten des Gehäuses werden mit den folgenden Gehäusenamen gekennzeichnet:
- PLCC (plastic leaded chip carrier): IC-SMD-Gehäuse mit 20 bis 84 „J-Lead“-Anschlüssen, Gehäuse mit Anschlussabstand von typisch 1,27 mm.
- QFP (quad flat package): IC-SMD-Gehäuse mit 32 bis 200 Anschlüssen, bildet die Grundlage für eine ganze Reihe von Abwandlungen, die zum Teil herstellerspezifisch sind, beispielsweise:
- LQFP (low-profile quad flat package): IC-SMD-Gehäuse mit 1,4 mm Bauhöhe
- PQFP (plastic quad flat package): IC-SMD-Gehäuse das im Allgemeinen durch das dünnere TQFP-Gehäuse ersetzt wurde.
- CQFP (ceramic quad flat package): IC-SMD-Gehäuse vergleichbar mit dem PQFP-Gehäuse jedoch mit Keramikumhüllung.
- MQFP (metric quad flat package): IC-SMD-Gehäuse vergleichbar mit dem QFP-Gehäuse jedoch mit metrischem Abstand der Anschlüsse voneinander.
- TQFP (thin quad flat package): Eine dünnere IC-SMD-Gehäuse-Version des PQFP-Gehäuses mit einer Bauhöhe von entweder 1,0 mm oder 1,4 mm.
Lötanschlussflächen unter dem Gehäuse, „Leadframe“ und „Grid-Arrays“
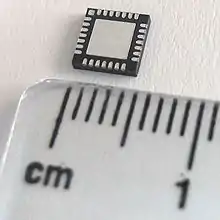
- quad flat no leads package (QFN), micro leadframe package (MLP), auch micro lead frame, MLF: Die Bezeichnungen umfassen eine ganze Familie von IC-Gehäusen, deren elektrische Anschlüsse rahmenartig um die Seitenflächen des Gehäuses angeordnet sind und sich als metallisierte Kontaktflächen unter dem Gehäuse befinden. Diese Gehäuse haben manchmal eine weitere metallisierte Kontaktfläche unter dem Gehäuse, die mit dem Die verbunden ist, um eine bessere Wärmeableitung zu ermöglichen. Eine Variante MLPD („D“ steht für „dual“) ist Pinkompatibel mit dem DIL-SOIC-Gehäuse, mit MLPD (Dual) und MLPQ (Quad) werden die Anschlusskonfigurationen unterschieden, MLPM (Micro) steht für eine miniaturisierte Version des Gehäuses. Das QFN-IC-SMD-Gehäuse ist ein spezielles MLPQ-Gehäuse, dessen Anschlussbelegung und Anschlussabstände dem bedrahteten QFP-Gehäuse entsprechen, deren metallisierte Anschlussflächen jedoch als Kontaktflächen unter dem Gehäuse angebracht sind.
Hochintegrierte Halbleiterbauelemente wie Mikroprozessoren haben so viele elektrische Anschlüsse, dass sie nicht mehr um den Umfang des Gehäuses herum unterzubringen sind. Deshalb werden diese Anschlüsse in Form von metallisierten Anschlussflächen schachbrett- oder gitterartig (engl. grid array) unter dem Gehäuse angebracht. Diese Halbleitergehäuse mit Lötanschlussflächen schachbrettartig unter dem Gehäuse werden mit den folgenden Gehäusenamen gekennzeichnet:
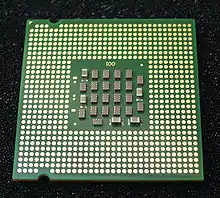
- LGA (land grid array): Ein LGA ist eine schachbrett- oder gitterartige Anordnung von elektrischen Anschlussflächen (englisch land) auf der Unterseite eines Gehäuses für ICs mit sehr vielen Anschlüssen wie z. B. Mikroprozessoren. Beim Löten dieser vielen Kontakte unter dem LGA-Gehäuse können allerdings vereinzelt Lötfehler auftreten, die nur recht schwierig zu erkennen sind (Röntgen). Da eine Reparatur kostenaufwendig und fehlerbehaftet ist, werden LGA-ICs häufig auf Sockel gesetzt. Diese Sockel mit der gleichen Pinbelegung wie das IC, werden im SMD-Prozess auf die Platine gelötet und können recht einfach auf Kontaktsicherheit getestet werden. Der Prozessor wird für den elektrischen Anschluss dann mit Hilfe einer Klammer mit seinen Anschlussflächen auf die oben liegenden Kontakte des Sockels gedrückt. Der Sockel hat federnde Kontaktstifte, so dass ein sicherer elektrischer Kontakt hergestellt werden kann.

- BGA (ball grid array, dt. Kugelgitteranordnung): Ein BGA ist wie das LGA-Gehäuse eine Gehäuseform von Integrierten Schaltungen, bei der die elektrischen Anschlüsse schachbrett- oder gitterartige Anordnung der Unterseite angebracht sind. Die Anschlüsse sind jedoch in Form kleiner Lotperlen (engl. balls) ausgeführt. Diese Perlen werden beim Reflow-Löten in einem Lötofen aufgeschmolzen und verbinden sich mit dem Kupfer der Leiterplatte.
Verarbeitung
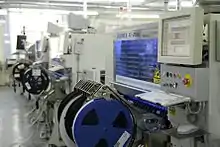
Da die SMD-Bauteile auf eine Leiterplatte bestückt werden, nennt man diese Verarbeitung Bestückung, obwohl die Bestückung auch andere Arbeitsschritte umfasst als nur das Platzieren der Bauteile auf der Leiterkarte. Diese Schritte sind:
- Aufbringen von Lotpaste (eine Mischung von Zinnkügelchen und Flussmittel) oder Kleber auf die Leiterkarte
- Bestücken der Bauteile
- Löten der Leiterkarte oder Aushärten des Klebers
Nach jedem Schritt wird die Qualität des Produktes optisch geprüft, bevor es zum nächsten Schritt weitergereicht wird. Die Fertigungsschritte werden in der Regel maschinell ausgeführt, bei Einzelstücken oder im Prototypenbau wird jedoch gelegentlich auf Maschinen verzichtet oder einzelne Schritte werden manuell ausgeführt. Die für die Verarbeitung benötigten Maschinen und Verfahren werden als Oberflächenmontagetechnik bezeichnet. Der Bereich eines Elektronikwerkes der sich mit der Verarbeitung von SMDs befasst wird daher als SMT-Bereich oder SMT-Abteilung bezeichnet.
Fertigungslinien für SMD-Bestückung (Prinzip)
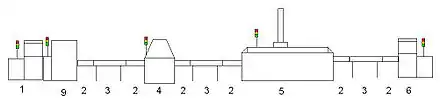
1: Magazinstation mit unbestückten Leiterkarten
2: Stauband
3: Inspektions- und Korrekturplatz
4: SMD-Bestückungsautomat
5: SMD-Ofen
6: Magazinstation zum Abstapeln des Endprodukts
9: Pastendrucker
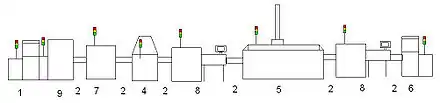
1: Magazinstation mit unbestückten Leiterkarten
2: Stauband
4: SMD-Bestückungsautomat
5: SMD-Ofen
6: Magazinstation zum Abstapeln des Endprodukts
7: automatische optische Inspektion (AOI)
8: AOI mit Reparaturplatz
9: Pastendrucker
Die gezeigten Varianten können auch miteinander gemischt werden, sodass bestimmte Prozesse manuell kontrolliert werden, andere mit automatischer optischer Inspektion. Prüfschritte werden weggelassen, wenn das Produkt sehr einfach ist. Oftmals sind einzelne Prüfungen bereits in den Produktionsschritt integriert. Manche Pastendrucker kontrollieren zum Beispiel optisch den Druck sowie die Sauberkeit der Schablone.
Aufbringen der Lotpaste bzw. des Klebers
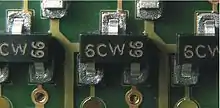
Lotpaste oder Kleber können entweder per Siebdruck (veraltet), per Schablone aufgebracht oder in kleinen Portionen maschinell oder von Hand appliziert werden. Kleber bzw. Paste werden durch Röhrchen auf die gewünschte Stelle aufgebracht oder berührungslos aufgespritzt.
Beim Aufbringen der Lotpaste wird eine Schablone verwendet. Dort, wo später Bauteilanschlüsse auf der Leiterkarte sind (auf den Pads) muss Lotpaste aufgebracht werden. Die Schablone wird so über der Leiterkarte positioniert, dass deren Löcher über den Pads zu liegen kommen. Meist sind die Öffnungen der Schablone einige hundertstel Millimeter kleiner, um zu verhindern, dass Paste neben das Pad gedruckt wird. Die Positionierung kann von Hand erfolgen oder automatisch anhand von Markierungen auf der Schablone und der Leiterplatte.
Leiterkarte und Schablone werden gegeneinander gepresst und ein Rakel drückt die Lotpaste durch die Öffnungen, sodass sie auf die Pads gelangt. Die Dicke der Schablone bestimmt die Lotpastenmenge pro Fläche.
Die Schablonen werden üblicherweise mittels Laserschneiden aus Stahlblech hergestellt.
Bestücken der Bauteile
Die kleineren Bauteile sind in Gurten aus Karton oder Kunststoff verpackt. In den Gurten befinden sich Taschen, in welchen die Bauteile liegen. Die Oberseite der Tasche ist durch eine Folie verschlossen, welche abgezogen wird, um das Bauteil zu entnehmen, ähnlich einer Blisterverpackung. Die Gurte selbst werden auf einer Rolle aufgewickelt. Auf zumindest einer Seite des Gurtes befinden sich Transport-Löcher im Abstand von 4 mm, über die der Gurt vom Bestückungsautomaten bewegt wird. Diese Rollen werden mit Hilfe von Zuführmodulen, sogenannten Feedern, dem Bestückungsautomaten zugeführt.
ICs und andere große Bauteile werden oft auch in Kunststoffstangen (englisch sticks) oder in kleinen Paletten, den so genannten Trays, verpackt. Während die Trays direkt in die Maschine eingelegt werden können, sind für die Stangen ebenfalls Feeder (englisch stickfeeder) erforderlich. Durch die Vibration der Stickfeeder gelangen nach der Entnahme die Bauteile weiter nach vorne, sodass der Bestückungskopf das nächste Bauteil entnehmen kann.
Die Bauteile werden mit Vakuumpipetten (englisch nozzle) oder Greifern entnommen und dann auf der Sollposition (X-,Y-Koordinaten) der Leiterplatte aufgesetzt. Dieser Vorgang wird für alle Bauteile wiederholt. Bei der Bestückung der Oberseite der Platine ist ein Kleben der Bauteile meist nicht erforderlich, da die Haftwirkung der Lotpaste für die notwendige Haftung des Bauteils während des Weitertransportes der Platine zur nächsten Station sorgt. Nachdem die Leiterkarte vollständig bestückt ist, wird sie zur nächsten Bearbeitungsstation transportiert und eine neue Platine kann zur Bestückung übernommen werden.
Härten des Klebstoffs und Löten
Bei aufgeklebten SMD-Bauteilen wird der Klebstoff durch Hitze ausgehärtet. Dies erfolgt in einem Ofen, der auch für das Reflow-Löten geeignet ist. Im Unterschied zum Reflow-Löten erfolgt das Aushärten des Klebstoffs bei niedrigerer Temperatur. Nach dem Aushärten müssen die Baugruppen noch schwallgelötet werden. Dies geschieht jedoch nach der THT-Bestückung, sofern diese THT-Bauelemente zusätzlich vorhanden sind.
Ist die Baugruppe zum Reflowlöten vorgesehen, wird sie in einem entsprechenden Reflowofen auf die erforderliche Prozesstemperatur gebracht. Die Lotkügelchen in der Lotpaste schmelzen dabei auf und sorgen sowohl für eine mechanische als auch elektrische Verbindung zwischen dem Bauelement und der Leiterplatte.
Typische Fehler
Einige der folgenden Fehler treten nur beim Reflow-Löten auf, andere nur beim Schwalllöten. Neben den klassischen Lötfehlern, wie Nichtbenetzung und Zinnbrücken, die auch bei Durchsteckbauteilen auftreten, sind hier zu nennen:
Grabsteineffekt
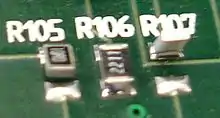
Der Grabsteineffekt (englisch tombstoning) tritt vermehrt bei Bauteilen mit zwei Anschlüssen auf. Das Bauteil hebt sich auf der einen Seite von der Platine ab, wodurch es wie ein kleiner Grabstein aussieht. Es ist jetzt nur noch an einer Stelle angelötet und die gewünschte Funktion ist nicht gegeben. Wenn möglich, muss hier nun manuell nachgearbeitet werden. Neben ungünstigen Lötparametern ist die zu lange Lagerung von Bauteilen eine Ursache, wenn die Anschlussflächen (unterschiedlich) oxidiert sind. Bereits ausgelötete SMD-Bauteile neigen ganz besonders zum Grabsteineffekt und sind für Reflow nicht geeignet.
Popcorn-Effekt
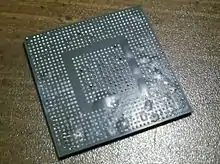
Der Popcorn-Effekt (englisch popcorning) kann entstehen, wenn feuchtigkeitsempfindliche elektronische Bauelemente zu lange außerhalb der vor Feuchte schützenden Verpackung gelagert werden; sie nehmen langsam Feuchtigkeit aus der Umgebungsluft auf. Die Lagerung solcher feuchteempfindlichen Bauelemente ist in IPC/JEDEC J-STD-020D geregelt (MSL-Klassen, englisch Moisture Sensitive Level). Durch die Hygroskopie der Kunststoffgehäuse der Bauelemente reichert sich Wasser vorwiegend an der Gehäusevergussmasse und den zu schützenden Strukturen (Leitbahnen, Substrat usw.) an (bis zu 0,5 Gewichtsprozent). Im Reflowofen verdampft die Feuchtigkeit aufgrund des raschen Temperaturanstiegs, dies führt zu einer Volumenausdehnung. Folgen sind u. a. Risse im Gehäuse und die Delaminierung des Substrates. Der kostenintensive Punkt am Popcorn-Effekt ist, dass er erst nach der Fertigung diagnostiziert werden kann, wenn z. B. Geräte mit solchen Bauteilen bereits in Kundenhände verkauft wurden. Zu lange gelagerte bzw. feucht gewordene Bauelemente lassen sich durch sogenanntes „Backen“ bei ca. 110 °C in 24 Stunden wieder im Innern trocknen, sodass diese zum Bestücken oder zerstörungsfreien Auslöten geeignet sind.
Verschwimmen beim Lötprozess
Als Verschwimmen wird eine Verschiebung in X- und/oder Y-Richtung des SMD-Bauelements bezeichnet. Gleichzeitig kann ein zusätzliches Verdrehen des Bauelements auftreten. Ein Verschwimmen kann unterschiedliche Ursachen haben. Aufgrund der Oberflächenspannung des flüssigen Lotes verändert das Bauteil seine Lage. Es besteht eine nahe Verwandtschaft zum Grabsteineffekt.
Abschwemmen von geklebten Bauelementen
Wenn Baugruppen mit geklebten SMD-Bauelementen schwallgelötet werden, besteht das Risiko, dass sich durch das flüssige Lot der Wellenlötanlage Klebeverbindungen zwischen der Leiterplatte und dem Bauelement lösen und somit das Bauelement von der Leiterplatte abgeschwemmt wird und im Lottopf der Wellenlötanlage landet.
Nichtbenetzen bei geklebten Bauelementen
Wenn Baugruppen mit geklebten SMD-Bauelementen schwallgelötet werden, besteht zusätzlich das Risiko, dass einzelne Pins oder einzelne Bauelemente durch das flüssige Lot der Wellenlötanlage nicht gelötet werden. Als mögliche Ursache hierzu kann die Abschattung durch größere benachbarte Bauelemente angesehen werden. Diese benachbarten Bauelemente können beim Wellenlöten den Lotfluss so verdrängen, dass einzelne Lötstellen nicht durch das Lot benetzt werden und somit nicht gelötet werden. Nach dem Lötvorgang haben die betroffenen Bauelemente offene Lötstellen. Durch eine geeignete Platzierung der Bauelemente bereits beim Leiterplattenentwurf wird das Problem vermieden. Das Design legt auch die Durchlaufrichtung durch die Lötanlage fest.
Siehe auch
Weblinks
- Peter Zenker: SMD-Löten leicht gemacht. (PDF; 1 MB)
- Detaillierte Beschreibung für SMD-Löten und -Entlöten bei mikrocontroller.net
- Suche nach SMD Code
Einzelnachweise
- spaceaholic.com, Artifact: Digital Computer Memory and Circuit Boards, LVDC, Saturn IB/V Guidance, Navigation and Control, spaceaholic.com
- Computerposter, computerposter.ch
- „one chip“ UKW-Radio-IC, Philips-Datenblatt TDA 7010, 1983
- Valvo GmbH, Hamburg, Am Puls der Zeit, 1974, Jubiläumsschrift zum 50-jährigen Jubiläum der Valvo GmbH
- Günter Spur, Frank-Lothar Krause: Das virtuelle Produkt. Management der CAD-Technik. Carl Hanser Verlag, München/Wien 1997, ISBN 3-446-19176-3.
- IBM 1966: Computer Aided Design Tools Developed for ICs, computerhistory.org
- Egon Fein, Grundig heute, Portrait eines Weltunternehmens, 1983, Druck Europrint GmbH
- Elektronik 13/2002, WEKA-Fachzeitschriften-Verlag, Sonderheft 50 Jahre Elektronik, Elektronik-Geschichte, Seiten 84–88.
- SMD Technologie, Bauelemente, Bestückung, Verarbeitung. Firmen-Druckschrift, bearbeitet durch H. H. Warnke, Valvo, 1987, S. 5.
- J. Ho, T. R. Jow, S. Boggs: Historical introduction to capacitor technology. In: IEEE Electrical Insulation Magazine. Band 26, Nr. 1, Januar 2010, S. 20–25, doi:10.1109/MEI.2010.5383924.
- C. Wiest, N. Blattau, J. Wright, R. Schatz, C. Hillman: Robustness of Surface Mount Aluminum Electrolytic Capacitors When Subjected to Lead Free Reflow. In: Passive Component Industry. November/Dezember, 2006, S. 6–11 ( [PDF; abgerufen am 10. Dezember 2020]).
- J. Both: The modern era of aluminum electrolytic capacitors. In: IEEE Electrical Insulation Magazine. Band 31, Nr. 4, Juli 2015, S. 24–34, doi:10.1109/MEI.2015.7126071.
- IEC-DIN-EN 60384-1, Festkondensatoren zur Verwendung in Geräten der Elektronik – Teil 1: Fachgrundspezifikation
- Miniaturisierung der Bauteile kann mehr Ausschuss nach sich ziehen. Abgerufen am 13. Juni 2019.
- Datenblatt Rohm Ultra Compact Chip Resistors. (PDF) Rohm Semiconductor, abgerufen am 13. Juni 2019 (englisch).
- Kommt 2013 die erste Bestückungsmaschine für 03015? Die kleinsten Bauteile der Welt