Anodisieren
Das Anodisieren, auch die Anodisierung oder die Anodisation genannt, bezeichnet in der Oberflächentechnik ein elektrolytisches Verfahren zur Herstellung oder Verstärkung von oxidischen Schichten auf Metallen.[1] Das Anodisieren ist ein Spezialfall einer anodischen Oxidation, bei der sich ein festhaftendes Oxid bildet.[2] Die Anodisierung dient insbesondere dazu, Metalle gegen Korrosion zu schützen. Das wichtigste Anodisierungsverfahren ist das Eloxal-Verfahren der Anodisierung von Aluminium.
Verfahren
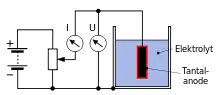
Bei der Anodisierung wird das Metall in eine geeignete wässrige Lösung (beispielsweise von Schwefel-, Oxal- oder Chromsäure) getaucht und es wird eine Elektrolyse durchgeführt, wobei das Metall als Pluspol dient. Durch den elektrischen Strom bildet sich auf der Anodenoberfläche eine Oxidschicht, während an der Kathode Wasser zersetzt wird, es wird zu Wasserstoff reduziert.[3]
Zur Elektrolyse wird in der Regel Gleichspannung verwendet, oft mit einer Spannung von 10 bis 25 Volt und einer Stromdichte von 50 bis 250 A/m2. Für dickere Schichten, z. B. in Schwefelsäure, können bis zu 120 V verwendet werden. Das Verfahren mit Gleichspannung und Schwefelsäure wird als GS-Verfahren, wenn zusätzlich neben Schwefelsäure noch Oxalsäure eingesetzt wird als GSX-Verfahren bezeichnet.[2] Verfahren mit nur Oxalsäure werden als GX- oder WGX-Verfahren und mit Chromsäure als GC-Verfahren oder Bengough-Stuart-Verfahren bezeichnet. Daneben gibt es für die Herstellung von Elektrolytkondensatoren noch Verfahren die Borax (50–500 Volt), Borsäure (230–250 Volt) oder Citronensäure verwenden.[2]
Anwendungsbereiche
Dazu werden Oxidschichten benutzt, die bei Aluminium zwischen 0,5 und 150 Mikrometern dick sein können. Dabei sind 5–25 Mikrometer dicke Schichten für den Korrosionsschutz üblich. Die Schichtdicken für dekorative Zwecke können bis zu 500 µm betragen.[3] Die so hergestellte Schicht dient vorwiegend als Schutzschicht für Metalle gegen Korrosion und Abrieb. Sie ist mikroporös und erreicht daher ihre optimale Beständigkeit erst durch eine Nachbehandlung – dem Verdichten –, die einen Porenverschluss bewirkt.[4] Bei Magnesium sind Schichtdicken bis zu 80 µm üblich.[1] Oxidschichten werden aber auch als elektrische Isolation (Dielektrikum) in Elektrolytkondensatoren eingesetzt (Tantal, Niob, Aluminium).[5] Für diesen Zweck müssen die Oxidschichten dünn genug sein, denn nur eine geringe Schichtdicke (kleiner 1 μm) ermöglicht die gewünschten hohen Kapazitäten, die einer der Hauptvorteile von Elektrolytkondensatoren sind.
Auch wenn die Anodisierung bei verschiedenen Metallen möglich ist, hat sie doch nur für Leichtmetalle größere technische Bedeutung erlangt, besonders bei Aluminium und seinen Legierungen. Dort wird das Verfahren auch Eloxal-Verfahren genannt. „Eloxiertes“ Aluminium wird in großem Umfang in der Architektur (Hausfassaden, Türen usw.) sowie im Fahrzeugbau verwendet.
Ein weiterer Vorteil des Verfahrens ist, dass von der Umwandlung nur die obersten Metallschichten (bis zu 40 μm Dicke) betroffen sind. Einige Metalle (z. B. Aluminium, Titan) neigen dabei zunächst dazu, mikroporös zu werden und sind so mit organischen Farbstoffen leicht anfärbbar.[6] Sie müssen danach noch einer Nachverdichtung unterzogen werden.[4]
In der Halbleitertechnik wird das Verfahren zur Herstellung von Gate-Oxiden verwendet.[5]
Historisches
Schon 1853 wurde über Experimente mit Aluminiumanoden berichtet: Wird durch eine äußere Spannung eine in Schwefelsäure tauchende Aluminiumelektrode positiv polarisiert, so tritt zunächst eine „ziemlich lebhafte Gasentwicklung“ auf, es entsteht Sauerstoff.[7] Diese Gasentwicklung lässt aber schnell nach.[7] Eine Passivität des Aluminiums kann auch „beim Eintauchen in Salpetersäure von jedem Concentrationsgrade“ erhalten werden.[7] 1923 wurde ein Patent zur Ausbildung einer korrosionsresistenten Schicht auf Aluminium und Aluminiumlegierungen eingereicht, das mit einer Chromatlösung und mit einer auf 50 Volt ansteigenden Spannung arbeitete.[8] Das Verfahren wurde zum Korrosionsschutz von Teilen aus Duraluminium bei Wasserflugzeugen angewandt.
Früher wurde der Effekt der Anodisierung mancher Metalle auch zur Gleichrichtung genutzt. Eine Bauart bestand aus einer Platinelektrode und einer Niobelektrode, welche in verdünnte Schwefelsäure getaucht sind. Sobald das Niobblech zur Anode wird, versiegt der Stromfluss, da sich nichtleitendes Nioboxid bildet, welches bei Umkehrung der Polarisation wieder zum Niobmetall reduziert wird, wodurch wieder ein Stromfluss möglich ist.[9]
Varianten
Eine Variante ist die anodische Oxidation unter Funkentladung (engl. anodic spark oxidation, ANOF). Bei diesem Prozess wird nicht mit Gleichstrom, sondern einer von null ansteigenden sägezahnähnlichen Spannungsrampe oxidiert, bis ein Funke vom Elektrolyten auf den zu behandelnden Werkstoff überspringt. Dieser Funke schmilzt den Werkstoff wie Titan, Magnesium oder Aluminium lokal auf und bildet durch die hohen Temperaturen der Entladung ein hartes Oxid. Im Fall von Aluminium kann ohne thermische Behandlung des Bauteils Alpha-Aluminiumoxid (Korund) abgeschieden werden. Diese Schichten eignen sich besonders als chemisch hochbeständige Verschleißschutzschichten.[10][11]
Bei einer anderen Methode, der Plasma-Anodisation, wird ein mit Aluminium bedampfter Halbleiter bei etwa 3•10−3 Torr (0,4 Pascal) einer Gleichspannungs-Glimmentladung in einer Sauerstoff-Atmosphäre ausgesetzt.[12]
Einzelnachweise
- Kirsten Bobzin: Oberflächentechnik für den Maschinenbau. John Wiley & Sons, 2013, ISBN 978-3-527-68149-5 (eingeschränkte Vorschau in der Google-Buchsuche).
- Horst Briehl: Chemie der Werkstoffe. Springer-Verlag, 2014, ISBN 978-3-658-06225-5, S. 121 (eingeschränkte Vorschau in der Google-Buchsuche).
- Andreas Kalweit, Christof Paul, Sascha Peters, Reiner Wallbaum: Handbuch für Technisches Produktdesign Material und Fertigung, Entscheidungsgrundlagen für Designer und Ingenieure. Springer Science & Business Media, 2006, ISBN 3-540-21416-X, S. 532 (eingeschränkte Vorschau in der Google-Buchsuche).
- Ulrike Kuhlmann: Stahlbau-Kalender 2016 Eurocode 3 - Grundnorm, Werkstoffe und Nachhaltigkeit. John Wiley & Sons, 2016, ISBN 978-3-433-60630-8, S. 299 (eingeschränkte Vorschau in der Google-Buchsuche).
- Eike Becker: Technologien für organische Feldeffekttransistoren in der Displaytechnik. Cuvillier Verlag, 2006, ISBN 3-86727-044-9, S. 41 (eingeschränkte Vorschau in der Google-Buchsuche).
- Hansgeorg Hofmann, Jürgen Spindler: Verfahren in der Beschichtungs- und Oberflächentechnik. Carl Hanser Verlag GmbH Co KG, 2014, ISBN 978-3-446-44183-5, S. 198 (eingeschränkte Vorschau in der Google-Buchsuche).
- H. Buff: Ueber das electrische Verhalten des Aluminiums. In: Justus Liebigs Annalen der Chemie. Band 102, Nr. 3, 1857, S. 102, doi:10.1002/jlac.18571020302.
- Patent GB223994A: Improved process of protecting surfaces of aluminium or aluminium alloys. Angemeldet am 2. August 1923, veröffentlicht am 3. November 1924, Erfinder: Guy Dunstan Bengough, John Mcarthur Stuart.
- Richard Wilhelm Heinrich Abegg, Friedrich Auerbach, Ivan Koppel: Handbuch der anorganischen Chemie, Band 3,Ausgabe 3. S. Hirzel, 1907, S. 811 (eingeschränkte Vorschau in der Google-Buchsuche).
- Hans-Ludwig Graf, Alexander Hemprich, Wolfram Knöfler: Entwicklung der Technologie der „Anodischen Oxidation unter Funkenentladung (ANOF)“ zur Konditionierung von Implantatoberflächen. In: Implantologie. Nr. 3, 2004, ISSN 0943-9692, S. 257–269.
- P. Kurze, W. Krysmann, H. G. Schneider: Application Fields of ANOF Layers and Composites. In: Crystal Research and Technology. Band 21, Nr. 12, 1986, S. 1603–1609, doi:10.1002/crat.2170211224 (Übersicht zur ANOF-Methode).
- Wolfgang Harth: Halbleitertechnologie. Springer-Verlag, 2013, ISBN 978-3-322-94051-3, S. 91 (eingeschränkte Vorschau in der Google-Buchsuche).