Duraluminium
Duralumin(ium), ist eine Aluminiumlegierung, die besonders im Vergleich mit Reinaluminium durch die erzielte hohe Festigkeit und Härte ein neues Zeitalter für Aluminium eröffnete.
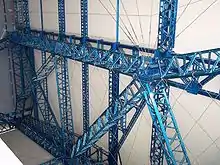
Entwicklung
1906 entwickelte Alfred Wilm im Rahmen von Untersuchungen zur Festigkeitssteigerung von Aluminiumlegierungen die erste ausschließliche Knetlegierung. Seine Entdeckung war, die Härte der Legierung dadurch zu steigern, dass man die in der Stahlherstellung gebräuchlichen Verfahren zur Festigkeitssteigerung auf eine Aluminiumlegierung übertrug. Es wurde zufällig festgestellt, dass Legierungsproben, die man nach dem Abschrecken noch einige Tage liegen ließ, tatsächlich eine erhöhte Festigkeit aufwiesen. Das zugrundeliegende Prinzip bezeichnet man als Ausscheidungshärtung.
Das neue Material wurde ab 1909 von den Dürener Metallwerken hergestellt und der Name Duralumin nebst einigen ähnlichen (DURAL) als eingetragene Warenzeichen geschützt. Wilms Legierung aus Aluminium, 3,5 bis 5,5 Prozent Kupfer, 0,5 bis 0,8 Prozent Magnesium und 0,6 Prozent Mangan sowie bis zu 1 Prozent Silizium und 1,2 Prozent Eisen wurde auch zum Patent angemeldet. Der Name wurde abgeleitet vom lateinischen durus für „hart“ (oder besser: „ausdauernd“ im Sinne von beständig, widerstandsfähig), wobei in der Literatur gelegentlich auch ein Zusammenhang zum Arbeitsort Düren beschrieben wird, sowie vom Hauptbestandteil der Legierung Aluminium. Inzwischen gibt es zahlreiche vergleichbare Legierungen, die den Herstellernamen in die Legierungsbezeichnung eingefügt haben.
Materialeigenschaften
Duraluminium gehört zu den Aluminiumlegierungen der Gruppe AlCuMg (Werkstoffnummer 2000 bis 2999) und wird vor allem kaltausgehärtet verwendet. Es ist nicht sehr korrosionsbeständig, nur bedingt anodisierbar und schweißbar.[1] Heute wird der Name Duraluminium vorwiegend zu lexikalischer Definition verwendet. Ähnliche Legierungen werden indessen weiterhin in der Luftfahrt verwendet.
Gegenüber reinem Aluminium hat Duraluminium eine geringfügig größere Dichte. Die Zugfestigkeit beträgt jedoch zwischen 180 und 450 N/mm² (laut anderer Quelle bis zu 800 N/mm²[2]) und damit bis zu dem zehnfachen von reinem Aluminium, das nur etwa 80 N/mm² aufweist.[3] Auch die technisch sehr wichtige Dehngrenze liegt bei über 250 N/mm² gegenüber 30 N/mm² bei reinem Aluminium.[3] Ähnlich verhält es sich bei der Brinellhärte, wo ein HB-Wert von etwa 125 gegenüber 22 bei Reinaluminium erreicht wird.[3] Die Bruchdehnung wird mit 22 Prozent als dreifach höherer Wert gegenüber 7 Prozent bei Reinaluminium angegeben. Ein weiterer wichtiger Punkt ist, dass Duraluminium durch Alterung an seiner Festigkeit nichts einbüßt.[2]
Die Grundlage für die Härtung gegenüber Reinaluminium liegt darin, dass nach schneller Abkühlung der Legierung nach einiger Zeit eine bei der Abschreckung zunächst unterdrückte Ausscheidung einer Zweitphase (der intermetallischen Verbindung CuAl2) im Grundgefüge der Legierung stattfindet, ein Vorgang, der eine deutliche Festigkeitssteigerung zur Folge hat. Diese Ausscheidung der festigkeitssteigernden Zweitphase kann bei sowohl Raumtemperatur als auch bei erhöhten Temperaturen erfolgen („Kaltauslagern“ – „Warmauslagern“) und erreicht ihr Optimum nach zwei Tagen.
Das Härten von Aluminiumlegierungen hat ansonsten nichts mit den bei der Stahlhärtung stattfindenden Prozessen zu tun. Dort sinkt die Festigkeit nach einer Wiedererwärmung des abgeschreckten Stahls, bei den Al-Legierungen steigt sie an.[2]
Material | Dichte in kg/dm³ | E-Modul in N/mm² | Zugfestigkeit in N/mm² | Bruchdehnung in % | Brinellhärte HB |
---|---|---|---|---|---|
Dural AlCu4Mg1 | 2,75–2,87 | 73.000 | 420– 500 | < 22 | 115–135 |
Reinaluminium Al99,5 | 2,7 | 70.000 | 75– 110 | < | 722– 35 |
Unlegierter Stahl (S355) | 7,9 | 200.000 | 510 | 19 | 120–140 |
Chrom-Nickel-Stahl | 7,9 | 200.000 | 500– 750 | 40 | 130–190 |
54SiCr6[4] (Federstahl) | 7,46 | 210.000 | 1450–1750 | 6 | 230–280 |
Durch das Aushärten erreicht Duraluminium also fast die Festigkeit weicher Stähle. Der gegenüber Reinaluminium höheren Anfälligkeit für Korrosion begegnet man durch eine Plattierung mit Reinaluminium, Eloxieren oder Lackierung.[5]
Anwendungen
Durch die verbesserten Materialeigenschaften wurde der Ersatz von Stahl durch eine Aluminiumlegierung in der Luftfahrt und Waffentechnik überhaupt erst sinnvoll. Frühere Legierungen wie die Zink-Aluminium-Legierungen waren bedeutend anfälliger für Spannungskorrosion und erreichten bei weitem nicht die erforderliche Festigkeit.[6][7]
Bereits 1911 fand Duraluminium eine großtechnische Anwendung für das Traggerüst des britischen Luftschiffs HMA No. 1 Mayfly.[8] Ab 1914 wurde es auch für den Bau der deutschen Zeppelin-Luftschiffe (erstmals beim LZ 16 / Z XII) eingesetzt.[9] 1929 wurde ein Ganzmetall-Luftschiff – das amerikanische ZMC-2 – gefertigt. Es bestand inklusive einer Blech-Gashülle vollständig aus Duraluminium.
Neben den Luftschiffbauern wurde auch Hugo Junkers angeregt, Duraluminium bei der Junkers J 7 (1917) einzusetzen. Eines der ersten Passagierflugzeuge, die Junkers F 13 (1919), war ein Vollmetall-Verkehrsflugzeug, bei dem Duralumin als Werkstoff für das Chassis verwendet wurde.[10][11] Duraluminium zeigte sich auch gut geeignet für die damals neue Monocoque-Konstruktion von Flugzeugzellen. Im modernen Flugzeugbau ist Duraluminium heute als Werkstoff 2017, 2117 oder 2024 bekannt.[12]
Der Einsatz im Kraftfahrzeugbau war anfangs durch den hohen Preis und die schwierigere Verarbeitung nur eingeschränkt möglich. Der Einsatz hochfester Aluminiumlegierungen im PKW-Bau hat aus Leichtbaugründen insbesondere seit den 2000er Jahren stark zugenommen, z. B. als Karosseriebeplankungsteile aus AlMgSi-Legierungen, als Strukturgussbauteile oder Versteifungsbleche aus AlMg-Legierungen. Kupferhaltige AlCuMg-Legierungen wie Duraluminium sind dagegen in Serienanwendungen aufgrund der geringen Korrosionsbeständigkeit unüblich[13].
Beispiele für den Einsatz sind besonders Karosserieteile. Motorhauben und Kofferraumklappen sind inzwischen weitgehend durch dünnwandigen Präzisionsdruckguss ersetzt (EVACAL- und PORAL-Verfahren).[14]
Literatur
- Paul Krais: Werkstoffe. Band 2, A. Barth, Leipzig 1921, S. 517–518.
- Eintrag zu Duralumin. In: Römpp Online. Georg Thieme Verlag, abgerufen am 2. Januar 2015.
- A. von Zeerleder: Technologie der Leichtmetalle. Rascher, Zürich 1947.
- Stephan Hasse. Gießerei-Lexikon. 19. Auflage. Schiele und Schön, Berlin 2007, ISBN 978-3-7949-0753-3, siehe: Duraluminium.
Weblinks
Einzelnachweise
- J. Gobrecht: Werkstofftechnik – Metalle. ISBN 978-3-486-57903-1.
- Nasser Kanani: Werkstoffkunde für Oberflächentechniker und Galvaniseure. ISBN 978-3-446-40741-1.
- Niels Klußmann, Arnim Malik: Lexikon der Luftfahrt. ISBN 978-3-540-49095-1.
- 1.7102. 54SiCr6. Cr-Si-legierter Federstahl (PDF; 1,1 MB).
- Wolfgang Bergmann: Werkstofftechnik, Teil 2. ISBN 978-3-446-41711-3.
- Helmut Maier: Rüstungsforschung im Nationalsozialismus Organisation, Mobilisierung und Entgrenzung der Technikwissenschaften. Wallstein Verlag, 2002, ISBN 978-3-89244-497-8, S. 378 (eingeschränkte Vorschau in der Google-Buchsuche).
- Otto Brandt, H. Dubbel, W. Franz, R. Hänchen, O. Heinrich, Otto Kienzle, R. Kühnel, H. Lux, K. Meller, W. Mitan, W. Quack, E. Sachsenberg: Taschenbuch für den Fabrikbetrieb. Springer-Verlag, 2013, ISBN 978-3-642-99589-7, S. 422 (eingeschränkte Vorschau in der Google-Buchsuche).
- The Naval Airship. (PDF) In: FLIGHT, May 27, 1911. Flightglobal.com, 27. Mai 1911, S. 461–462, abgerufen am 28. Juli 2017 (englisch): „THE NAVY AIRSHIP NO. 1.—The "Mayfly," built by Messrs. Vickers, Ltd., which was successfully launched at Barrow on Monday last.“
- Klaus Hentschel: Duralumin. Verwendung von Duralumin. In: 220 Tonnen – leichter als Luft, Materialgeschichte der Hindenburg. Universität Stuttgart, Historisches Institut, Abteilung für Geschichte der Naturwissenschaften und Technik, 2010, abgerufen am 10. November 2017 (Website zur Ausstellung im Zeppelinmuseum Friedrichshafen): „Ab 1914 (LZ 26) wurde Duralumin im Luftschiffbau benutzt.“
- Philipp Hassinger: Zwischen Evolution und Revolution - Der Werkstoffwandel im Flugzeugbau. KIT Scientific Publishing, 2013, ISBN 978-3-86644-998-5, S. 145 (eingeschränkte Vorschau in der Google-Buchsuche).
- Hans Otto Frøland, Mats Ingulstad, Jonas Scherner: Industrial Collaboration in Nazi-Occupied Europe Norway in Context. Springer, 2016, ISBN 978-1-137-53423-1, S. 43 (eingeschränkte Vorschau in der Google-Buchsuche).
- Rambabu, P & Eswara Prasad, N & V. Kutumbarao, V & Wanhill, Russell. (2017). Aluminium Alloys for Aerospace Applications. 29-52. 10.1007/978-981-10-2134-3_2.
- Friedrich Ostermann: Anwendungstechnologie Aluminium, 3. Auflage. Springer Verlag, Berlin 2014, ISBN 978-3-662-43807-7, S. 23 ff.
- Friedrich Ostermann: Anwendungstechnologie Aluminium. Springer-Verlag, 2015, ISBN 978-3-662-43807-7, S. 24 (eingeschränkte Vorschau in der Google-Buchsuche).