Thermoformen
Das Thermoformen oder Warmformen ist ein Verfahren zur Umformung thermoplastischer Kunststoffe unter Wärmeeinwirkung sowie mit Hilfe von Druckluft oder Vakuum. Wegen seiner oberflächlichen Ähnlichkeit zum Tiefziehen von Metallblechen wird es auch als „Vakuumtiefziehen“ oder einfach „Tiefziehen“ bezeichnet, ist aber in wesentlichen Punkten ein anderes Verfahren.
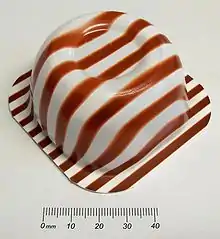
Man unterscheidet die Thermoformverfahren nach dem jeweils eingesetzten Halbzeug: Dünnere Halbzeuge werden Folien genannt, dickere (ab ca. 1,5 mm) Platten. Folien-Halbzeuge können auf großen (bis Ø 1,8 m) Rollen den Thermoformautomaten zugeführt werden.
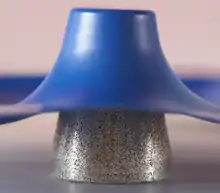
Daneben sind die Thermoformen die Werkzeuge für das Thermoformen.
Thermoformen „ab der Rolle“
Artikel aus Dünnfolien (0,2 bis 1 mm) wie Pralinenschachteleinlagen, Spielekartoneinsätze, Klappblister für Kleinartikel an Lochrasterwänden im Einzelhandel, Joghurtbecher sind weit verbreitet. Schiebekartenblister, Siegelhauben und die schwer zu öffnenden Klappblister, in denen oft Kleinteile verkauft werden und die mittels Hochfrequenz-HF-Elektroden verschweißt sind, gehören auch dazu.
Das Verfahren
Von großen Rollen wird die Folie an den Folienbahnkanten in sogenannten Stachelketten geführt. Die noch harte kalte Folie wird so dem Formautomaten zuerst zugeführt und dann taktweise hindurchgeleitet. In einer Aufwärmstation werden Heizstrahler über industrielle Heizungssteuerungen angesteuert und die Folie so ein- oder beidseitig erwärmt. Die warme, jetzt weichere Folie wird in den Stachelführungen dabei leicht auseinandergezogen, damit sie nicht so stark durchhängt. In der Werkzeugstation wird die Folie mittels Spannrahmen festgehalten, Vorstrecker und das Thermoformwerkzeug fahren durch die Folienebene hindurch und geben die fertige Kontur schon grob vor. Dann kommt Druckluft von der einen und Vakuum von der anderen Seite, um die Folie rasch und stark an die wassergekühlte Wandung (Kontur) des Aluminiumformwerkzeuges zu bringen. Durch 0,5 bis 0,8 mm kleine Löcher und/oder 0,2 bis 0,3 mm breite Schlitze entweicht die Luft zwischen Folie und Aluminiumwerkzeug. Die erkaltete, nun feste Folie wird von dem Formwerkzeug getrennt und im nächsten Arbeitstakt der Ausstanzstation zugeführt. Dort werden mittels Bandstahlschnitt die Außenmaße oder auch Löcher in das fertige Werkstück gestanzt.
Im nächsten Arbeitstakt wird der Artikel manuell der Thermoformmaschine entnommen oder mittels Stapelschacht, Klemmbrett, Ausheber und Rakel automatisiert gestapelt. Die fertigen Folienartikel werden dann stapelweise manuell entnommen, häufig in Polybeutel verpackt und in Kartons gelegt.
Daneben gibt es weitere, hier nur stichwortartig aufgeführte Arten des Thermoformens:
- Hochleistungsautomaten arbeiten mit gehärteten Stahlwerkzeugen und stanzen die Folienartikel im selben Moment der Formgebung aus.
- Mittelserienautomaten werden z. T. auch nur mit Vakuum oder Druckluft betrieben.
- Kleinserien werden fallweise von einer kleinen Rolle oder aus Folienplatten in Halbautomaten erzeugt und die Teile dann per Rollenstanze und Bandstahlschnitt abgetrennt.
Man unterscheidet zudem Positives Thermoformen und Negatives Thermoformen. Beim Positiven Thermoformen wird das Thermoformbauteil über das Werkzeug bzw. Maschine "gestülpt", während beim Negativen Thermoformen das Thermoformteil über eine Werkzeugkavität gelegt und "hineingesaugt".
Mit Schiebern, Klapp- und Drehkernen lassen sich auch komplexe Designs realisieren. Gestanzt werden kann auch in mehr als nur einer Ebene. Früher waren Verpackungen quaderförmig; heute sind sie fast immer den oft komplexen Geometrien der zu verpackenden Artikel angepasst oder nur deswegen mit geschwungenen Flächen und Kanten versehen, um individuelle "moderne" Verpackungen zu erhalten. Ein doppeltes Thermoform-Verfahren bezeichnet das TwinSheet-Verfahren, bei der nicht nur eine Halbschale geformt wird, sondern zwei Platten nacheinander oder gleichzeitig zu einem Hohlkörper verschmolzen werden.
Thermoformen von Plattenware
Platten zwischen 1 und 2 mm Dicke werden verarbeitet für Sortiertabletts, Transporttabletts, einfache technische Teile u. v. a. m. Materialstärken von 2 bis 10 mm finden Anwendung bei Kühlschrankwänden, Badewannen, Armaturenbrettern, Leuchten, Teichfertigbecken usw. Dieses Verfahren funktioniert ähnlich dem oben beschriebenen, mit der Einschränkung, dass mit Plattenware (Verschnitt) nicht so rationell produziert werden kann. Kunststofftafeln können in einer Größe von 2.200 × 3.300 mm verarbeitet werden. Die Höhe der Teile kann bis zu 1.500 mm betragen. Für spezielle Anwendungen kann die Formgröße auch noch größer sein. Allerdings gibt es in größeren Dimensionen nur wenige Halbzeuge (Platten). Zu beachten bei der Fertigung von Thermoformteilen ist immer die Verstreckung des Materials, also wie sehr sich das Material dehnt und um wie viel sich dadurch die Wandstärke des verformten Teils reduziert. Außerdem ist bei den Geometrien auch der Hinterschnitt zu beachten. Dieser ist materialabhängig begrenzt oder macht aufwändige Mechaniken nötig.
Die Materialien
Monofolien waren früher aus PVC, sind heute überwiegend aus PET, PS und PP hergestellt. Auch mehrschichtige Folien (PSEVOHPE / PPEVOHPE…) mit besseren Heißsiegeleigenschaften oder Dampfsperren für bessere Haltbarkeit von Lebensmitteln usw. finden oft Anwendung. Beflockte Folien: Zirkelkasteneinsätze, Besteckkasteneinsätze u. a.
Grundsätzlich lassen sich aber sämtliche Thermoplaste in diesem Verfahren verarbeiten. Die häufigsten sind hierbei: ABS, ASA, HD-PE, PC, PET-A, PET-G, PMMA, PP, PS und PVC[1]. Für jede Anwendung gibt es den passenden Kunststoff. Aus Talkum verstärktem PE können großdimensionierte Kotflügel hergestellt werden. ABS mit Acryldeckschicht wird für Verkleidungen verwendet, die starken Witterungseinflüssen ausgesetzt sind oder mit Chemikalien in Verbindung kommen. Eine gewisse elektrische Leitfähigkeit von Kleinladungsträgern (wegen halbleiterzerstörender elektrostatischer Entladung im Elektronikbereich) wird durch Zugabe von Rußpartikeln bewirkt. Auch das Verformen von Hochleistungskunststoffen wie PEEK ist mittlerweile möglich.
Anwendungen
Neben dem klassischen Anwendungsbereich Verpackungen hat das Thermoforming vermehrt Anwendungen im industriellen Bereich gefunden. Als Alternative zum Spritzguss zeichnet es sich durch günstige Werkzeugkosten aus und ist besonders bei kleinen und mittleren Serien besonders wirtschaftlich. Beispiele für Thermoformteile sind Hauben und Verkleidungen aller Art für den Maschinen- und Anlagenbau, für Agrar- und Baumaschinen, Flurförderzeuge und dem Nutzfahrzeugbau. Des Weiteren werden Kotflügel gefertigt, Armaturen uvm. Im Konsumgüterbereich ist die Anwendung u. a. bei der Herstellung von Kühl- und Gefriergeräten zu erwähnen. Hier werden die Innenbehälter und die Innenverkleidung der Türen durch Thermoformen hergestellt. Auch zur Herstellung von Zubehör in der Kfz-Branche wird heutzutage dieses Verfahren (auch Tiefziehverfahren genannt) angewandt, wie z. B. bei der Produktion von Kofferraumwannen. Aus Materialien wie z. B. Polyurethanschaum oder Glasfasermatten, werden akustisch und thermisch isolierende Bauelemente z. B. für die Automobilindustrie hergestellt. Ein weiterer Einsatzbereich ist die Medizintechnik für Werkzeugverkleidungen, Geräte- und sowie Maschinenverkleidungen.
Insbesondere die Kombination aus Formgebung, Farbigkeit und Funktion lässt Industriedesigner vermehrt auf dieses Verfahren zurückgreifen.
Literatur
- Adolf Illig (Hrsg.): Thermoformen in der Praxis. Hanser, München 2008, ISBN 3-446-40794-4.
- Adolf Illig (Hrsg.): Thermoformen in der Praxis. Hanser, München 1997, ISBN 3-446-19153-4.
- James L. Throne, Joachim Beine: Thermoformen. Hanser, München 1999, ISBN 3-446-21020-2.
Weblinks
- Positives/Negatives Thermoformen Thermoformen
Einzelnachweise
- formary: Tiefziehfähige Thermoplaste. Abgerufen am 5. September 2021 (deutsch).