Rotationsformen
Rotationsformen ist ein Kunststoff-Bearbeitungsverfahren für Hohlkörper, bei dem eine Schmelze in einem rotierenden Werkzeug an der Wandung erstarrt.
Verfahren
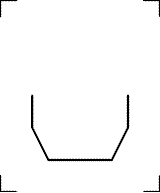
Mittels biaxialer Rotation und durch Erwärmung wird in dünnwandigen Hohlkörperformen pulverförmiges Thermoplast Schicht um Schicht an den Innenflächen der Form abgelagert. Dadurch können relativ gleichmäßige Wandstärken von 2 bis 15 mm erreicht werden.
Das Rotationsformen weist gegenüber dem Blasformen oder Spritzgussverfahren folgende Vorteile auf:
- einfache Werkzeuge und niedrige Werkzeugkosten
- Wirtschaftlichkeit für kleine und mittlere Serien von 20 bis 2.000 Stück/Jahr
- große mögliche Volumina bis 6.000 Liter
- mögliche komplizierte Formgebung mit Öffnungen, durchgehenden Verbindungen, Gewinden, Einlageteilen usw.
- gleichmäßige Wandstärken
- nahtlose Hohlkörper
Anlagen
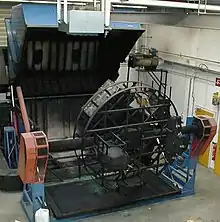
Die für das Rotationsformen verwendeten Anlagen lassen sich wie folgt einteilen:
- Einzelschussmaschinen, bei denen der gesamte Prozess vom Beschicken der Formen, Vorheizen, Heizen, Kühlen bis zum Ausformen, Schritt für Schritt geschieht. Auch als mehrarmige Karussellanlagen möglich, bei denen das Beschicken und Ausformen gleichzeitig mit dem sich im Ofen befindlichen Träger geschieht. Die Vorteile bei diesen Anlagen liegen in der besseren Ausnutzung der Prozesszeit, nachteilig aber ist die geringere Flexibilität in der Zusammenstellung von verschiedenen Teilegrößen, wie auch der wesentlich erhöhte Platzbedarf.
- Rock n‘ Roll-Anlagen sind Einzelschussanlagen, die sich nur in der Hauptachse drehen, in der Nebenachse jedoch nur eine Kippbewegung ausführen. Solche Anlagen werden hauptsächlich für zylindrische, längliche Teile verwendet.
Alle Anlagentypen lassen sich je nach Hersteller mit Infrarot oder mit Gas beheizen. Die Prozessverläufe und Temperaturen sind abhängig von der Teilegeometrie, dem verwendeten Kunststoff, der geforderten Wandstärke und dem Formenmaterial. Das Kühlen erfolgt meistens mittels Luftgebläsen und unter bestimmten Voraussetzungen auch mit gesprühtem Wassernebel.
Formen zum Rotieren
Die Erfahrungen beim Rotieren zeigen, dass sich verschiedene Formmaterialien verwenden lassen. Für einfache, kantige Behältnisse werden Formen kostengünstig aus Stahlblech oder Aluminiumblech hergestellt. Für komplizierte, gerundete und geschweifte Formteile werden jedoch die Rotationsformen einfacher in Aluminium gegossen. Die dazu notwendigen Urmodelle können aus Holz, Metall, Kunststoff, Gips oder anderen beliebigen festen Materialien hergestellt sein. Der Formgebung, sowie den Trennlinien sind somit keine Grenzen gesetzt. Idealerweise sollten Rotationsteile gut ab- und ausgerundet sein. Durch das Variieren der Formenwandstärke kann auch die Teilewandstärke beeinflusst werden.
Zum besseren Entformen, aber auch zum Erhalt einer konstanten Teilequalität können die Rotationsformen in verschiedenen Verfahren beschichtet oder behandelt werden. Die dazu verwendeten Silikone oder Kunstharze mit Tefloneinlagerungen werden je nach Anforderung an das Fertigteil ermittelt, aufgesprüht, einmassiert oder eingebrannt.
Sämtliche Formen werden mit Stahlkäfigen für den Maschinenaufbau ausgerüstet, für das rationelle Handling beim Entformen und Beschicken finden spezielle Schnellverschlüsse Anwendung.
Grenzen des Verfahrens
Wie jedes Produktionsverfahren kennt auch das Rotationsformen Verfahrensgrenzen. Das teilweise unberechenbare Schwindungsverhalten kann mit Erfahrung für konstruktive Details in engen Toleranzen gehalten werden. Eng tolerierte Maße von Öffnungen, Gewinden und Ausfräsungen müssen jedoch auf konventionelle Art hergestellt werden.
Kunststoffe für das Rotationsformen
Hauptsächlich finden die Thermoplaste Polyethylen (PE, auch elektrisch leitend) und Polypropylen (PP) Anwendung. Mit speziellen Einrichtungen an den Anlagen lassen sich auch fast alle weiteren Thermoplast-Produkte wie Polyamid (PA), Polycarbonat (PC) und Polystyrol (PS) für das Rotationssintern verwenden. In Ausnahmefällen eignen sich auch wärmehärtende 2-Komponenten-Duroplaste.
Je nach Kunststoff, werden die bekannten Festigkeitswerte erreicht, auch die weiteren mechanischen oder chemischen Merkmale (z. B. UV-Stabilität, Säurebeständigkeiten usw.) bleiben erhalten oder können bis zu Extremwerten eingestellt werden.
Die meisten Rohmaterialien lassen sich mittels Hochgeschwindigkeitsmischanlagen in jedem gewünschten Farbton einfärben (Turboblend). Ein weiteres Einfärbeverfahren (jedoch das teurere) ist das Compoundieren im Extruder. Der höhere Preis ist jedoch durch die bessere Durchmischung, die intensivere Deckkraft und die höheren Festigkeitswerte des Werkstoffes gerechtfertigt.
Die in der Nachbearbeitung anfallenden Materialabschnitte lassen sich in Mühlen fein granulieren und bis zu 30 % Anteil der Neuware zumischen. Größere Mengen Recyclingmaterial (bis zu 100 %) darf nur den speziell bezeichneten, nicht hoch belastbaren Regeneratteilen beigemischt werden.
- 1. Beispiel
- 2. Beispiel
Anwendungen
Überall, wo Kunststoffprodukte ausgehend von einem Hohlkörperteil, benötigt werden, kommt dieses Verfahren in Frage. Dieses können Tanks aller Art, Gehäuse für Maschinen, Transportbehälter für empfindliche Güter, Freizeit- und Wassersportartikel, etwa Kajaks, Möbel- und Spielzeugteile, Sicherheitsbehältnisse usw., sein.
Wegen der verhältnismäßig günstigen Formkosten eignet sich das Sinterrotieren besonders auch für kleine Serien.