Dispergierung (Lack)
Als Dispergierung oder Dispergieren bezeichnet man einen Verfahrensschritt bei der Herstellung von Formulierungen, wie sie unter anderem bei Lacken, Druckfarben, Kunststoffen oder Pigmentpräparationen üblich sind. Meist wird der Begriff bei der Einarbeitung von Pigmenten und Füllstoffen in einem solchen System verwendet. Dabei wird eine Suspension (eine spezielle Art einer Dispersion) hergestellt, also eine feste Phase in einer flüssigen verteilt. Neben der gleichmäßigen Verteilung im Trägermaterial umschreibt die Dispergierung auch die Benetzung des zu dispergierenden Stoffes mit dem Trägermaterial, sowie die Zerkleinerung des zu dispergierenden Stoffes und die anschließende Stabilisierung.
Die Eigenschaft, wie leicht sich ein Material einarbeiten lässt, bezeichnet man als Dispergierbarkeit. Eine quantifizierende Messgröße ist die Dispergierhärte.
Theorie der Dispergierung
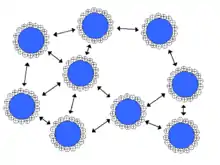
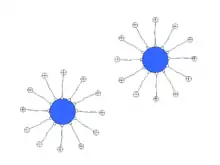
Pigmentpartikel liegen üblicherweise als Agglomerate, also lockere Zusammenballungen kleinerer Partikel (über die „Ecken“ der Primärteilchen) und Aggregate (über „Flächen“ der Primärteilchen) vor. Ziel des Prozesses ist die stabile Zerteilung der Agglomerate in Aggregat und Primärteilchen. Die Dispergierung umfasst die drei Teilprozesse Benetzung, Zerteilen und Stabilisieren. Diese Prozesse laufen in der Praxis parallel ab, da beispielsweise die Zerteilung von Agglomeraten zu einer Vergrößerung der Oberfläche führt und die zusätzliche Oberfläche ebenfalls benetzt werden muss.[1][2]
Benetzung
Im ersten Schritt werden die als Agglomerate vorliegenden Pigmentpartikel durch das Trägermaterial benetzt. Je nach Lacksystem erfolgt die Benetzung der Pigmente durch Lösemittel, Wasser oder das (gelöste oder geschmolzene) Bindemittel. Dabei unterscheidet man das Ausbreiten der flüssigen Phase auf der Agglomeratoberfläche und das Eindringen in Hohlräume und Poren, wobei Luft aus dem System verdrängt wird. Da die Benetzung häufig schwierig oder zu langsam abläuft, verwendet man Netzmittel, um den Vorgang zu beschleunigen.[3][4]
Zerteilen
Durch das jeweilige Dispergieraggregat werden Scherkräfte auf unterschiedliche Art und Weise in das System eingebracht, die für eine Zerteilung der Agglomerate (über Ecken und Kanten verbundene Aggregate und Primärteilchen) in Aggregate (über Flächen verbunden) und Primärteilchen sorgen. Im Idealfall könnten die Pigmentpartikel bis zum Primärkorn zerkleinert werden. In der Praxis reicht die eingebrachte Energie jedoch nicht zu einer Zerkleinerung bis zu Primärteilchen aus, so dass meist Aggregate und teilweise noch Agglomerate vorliegen.[3]
Stabilisierung
Die zerkleinerten Teilchen haben in der Regel die Tendenz, sich wieder zu Agglomeraten zusammenzuballen. Dieser Vorgang wird als Flokkulation bezeichnet, die entstandenen Zusammenballungen als Flokkulate. Da dies nicht erwünscht ist, werden Dispergiermittel zugesetzt, die diesem Prozess entgegenwirken. Die Abgrenzung dieser Additive zu den Netzmitteln ist dabei nicht eindeutig, da viele marktübliche Additive beide Eigenschaften (benetzend und stabilisierend) besitzen. Eine gebräuchliche Definition ist dabei die Aufteilung in niedrigmolekulare, amphiphile Substanzen (Netzmittel) und gegen Flokkulation stabilisierende Oligomere oder Polymere (Dispergiermittel).[3][5]
Die Stabilisierung kann dabei elektrostatisch, sterisch oder elektrosterisch erfolgen. Bei der elektrostatischen Stabilisierung wird die Oberfläche der zu stabilisierenden Partikel so belegt, dass alle Partikel gleichnamige Ladungen aufweisen und sich somit abstoßen. Bei der sterischen oder entropischen Stabilisierung wird die Partikeloberfläche mit langkettigen Molekülen belegt. Bei Verringerung des Partikelabstands würde sich die Entropie des Systems verringern, was der Flokkulation entgegenwirkt. Bei der elektrosterischen Stabilisierung sind die langkettigen Moleküle zusätzlich geladen, so dass beide Effekte genutzt werden können.[3]
Prozessablauf
Einwaage
Vor Beginn der Dispergierung werden die verwendeten Rohstoffe (mit wenigen Ausnahmen) vorgelegt und vermischt bzw. vordispergiert. Dabei wird die flüssige Phase zuerst eingewogen und die feste Phase zum Schluss dazugegeben. Bei Systemen, wo ein Komplettieren möglich ist, wird in der Regel eine für die Zerkleinerung der Teilchen optimale Viskosität eingestellt. Diese ist in der Regel höher als die Verarbeitungsviskosität des Endproduktes, so dass dies durch Verringerung der Einwaagemengen des Lösemittels oder des Wassers erreicht wird. Bei besonders viskosen Gemischen wird die zu dispergierende Phase meist schrittweise zugegeben.[6]
Vordispergierung
Die Vordispergierung umfasst alle Schritte, die zu einer besseren Benetzung der dispersen Phase führen. Dies verbessert zum einen das Dispergierergebnis selbst (schnellere oder bessere Ausdispergierung), andererseits aber auch die Kostensituation, da Zeit beim energieintensiven Dispergierprozess gespart wird.[6] Bei schlecht benetzbaren Materialien ist der erste Schritt häufig das einfache Stehenlassen des Mahlguts nach dem Mischen, umgangssprachlich als Einsumpfen bezeichnet. Die verwendeten Netzmittel haben dadurch Zeit, die Oberfläche der festen Phase besser zu benetzen. Es folgt die Vordispergierung, die bei flüssigen Formulierungen meist mit einem Dissolver erfolgt. Dies dient ebenfalls der besseren Benetzung, führt aber auch zu einem ersten Zerteilen der Agglomerate.[6] Bei Materialien, die bei Raumtemperatur fest sind, beispielsweise Pulverlacke und Kunststoffe, ist bereits das Mischen der Rohstoffe als Teil der Vordispergierung zu betrachten, da bei der Mischung von Feststoffen bereits eine Zerteilung stattfindet. Bei diesen Materialien findet jedoch keine klassische Vordispergierung statt.[6][7]
Dispergierung
Nach dem Mischen und Vordispergieren wird das Mahlgut auf ein Dispergieraggregat, also eine Maschine zum Dispergieren gegeben. Dort wird das Mahlgut bis zur gewünschten Korngröße dispergiert, so dass es weiterverarbeitet werden kann.[6] Bei Verfahren, die mit der Zugabe von Mahlkörpern arbeiten, folgt ein Verfahrensschritt, bei dem die Mahlkörper vom Mahlgut abgetrennt werden. Bei Verfahren, bei denen die Dispergierung in der Schmelze stattfindet, folgt ein Kühlschritt und in der Regel auch eine Mahlung (Pulverlack) oder Granulierung (Kunststoff).[6]
Komplettieren
Zum Schluss erfolgt das Komplettieren (ugs. das Auflacken) des Dispergiergutes. Es bezeichnet das Zugeben der noch fehlenden Bestandteile der Formulierung, wobei auch die Viskosität des Endproduktes durch die Zugabe von Lösungsmittel bzw. Wasser eingestellt wird. Es handelt sich um einen kritischen Verfahrensteil, da an dieser Stelle Schockerscheinungen möglich sind, die das Dispergierergebnis teilweise aufheben können und im Extremfall zum Verwerfen des gesamten Ansatzes führen können.[6][8]
Bei Formulierungen, die bei Raumtemperatur fest sind, wie etwa bei Pulverlacken oder Kunststoffen, ist das Komplettieren nicht möglich.[6]
Einfluss der Dispergierung auf die Systemeigenschaften
Durch die Verkleinerung der Partikel werden einige Eigenschaften pigmentierter Systeme deutlich verändert. Zunächst nimmt die Partikelgröße mit steigender Dispergierdauer ab. Die geht einher mit einer deutlichen Vergrößerung der zu benetzenden Lackoberfläche. Die Menge an Netzmittel bzw. Bindemittel, die zur vollständigen Benetzung nötig ist, nimmt demnach mit zunehmender Dispergierdauer zu. Die Verkleinerung der Partikel führt dazu, dass die Wirkung auf die Rauigkeit der Lackoberfläche abnimmt, was an einer Glanzzunahme zu sehen ist. Die offensichtlichste Änderung zeigt sich an der Zunahme der Farbstärke der enthaltenen Pigmente.[8]
Überprüfung der Dispergierwirkung
Diejenigen Eigenschaften, die sich während der Dispergierung am stärksten ändern, werden gleichzeitig auch für die Prüfung der Dispergierung verwendet. Die am weitesten verbreitete Methode zur Bestimmung des Dispergiergrades ist der Grindometer-Test, der eigentlich die Größe der größten Partikel (Überkorn) bestimmt, nicht jedoch die eigentliche (durchschnittliche) Partikelgröße. Die Prüfung kann direkt am Dispergiergut durchgeführt werden. Dabei wird die zu prüfende Substanz in einer keilförmigen Vertiefung eines Metallblocks aufgetragen und dann glattgestrichen. Die Partikel, die einen größeren Durchmesser besitzen als die Tiefe des Keils, bilden Streifen und können somit ausgewertet werden. An der Tiefe des Keils an dieser Stelle erkennt man die jeweilige Partikelgröße, die auch als Mahlfeinheit oder Körnigkeit bezeichnet wird.[8]
Messungen des Dispergierfortschritts, die sich an den Eigenschaften des entstandenen Lackes orientieren, sind die Messung der Farbstärke und des Glanzes. Beide Methoden nutzen die Tatsache aus, dass sich die Eigenschaften des Gesamtsystems in der Regel einem Grenzwert (oder zumindest einem Zielwert) annähern. Der Glanz nimmt während des Dispergierprozesses zu, der Einfluss der Dispergierung wird jedoch bei höherer Dispergierzeit immer kleiner. Die Farbstärke nimmt ebenfalls während der Dispergierung weiter zu und nähert sich einem Grenzwert, bei dessen (näherungsweisem) Erreichen das Pigment als ausdispergiert bezeichnet wird. Nachteilig bei diesen Methoden ist jedoch die notwendige Fertigstellung und Applikation des Lackes für jeden Prüfvorgang, was die Abprüfung aufwendiger macht.[8]
Dispergieraggregate
Dispergieraggregate (auch Dispergiermaschinen oder Dispergiergeräte) sind Geräte, die für die Dispergierung von festen Komponenten (Pigmente, Füllstoffe) in der flüssigen Phase von Lacken und Druckfarben verwendet.[9] Dispergieraggregate tragen Energie entweder durch Reiben des Mahlguts zwischen zwei Flächen oder Ausübung von Prall- und Scherkräften durch schnell rotierenden Scheiben in das Mahlgut ein. Je nach Viskosität des Mahlguts, Dispergierbarkeit der Pigmente und Füllstoffe und der geforderten Qualität des Beschichtungsstoffes sind verschiedene Dispergieraggregate gebräuchlich.[9]
Zur Vordispergierung und bei leicht zu dispergierenden Substanzen (oft anorganische Pigmente) sind Dissolver üblich. Bei schwieriger zu dispergierenden Substanzen (beispielsweise organische Pigmente) in wässrigen oder lösemittelhaltigen Lacksystemen kommen Kugelmühlen oder Rührwerkskugelmühlen zum Einsatz. Bei festen, aber aufschmelzbaren Trägermaterialien kommen Kneter oder Extruder zum Einsatz. Letztere sind vor allem bei der Herstellung von Pulverlacken üblich. Ein klassisches Dispergieraggregat für Druckfarben, das heute seltener zum Einsatz kommt, ist der Dreiwalzenstuhl (umgangssprachlich Dreiwalze), auf der pastöse Trägermaterialien benötigt werden.
Dissolver
Dissolver sind schnelllaufende Rührscheibengeräte, die aus einem Rührbehälter und einem (meist gezahnten) Scheibenrührer bestehen. Sie kommen bei der Dispergierung von leicht benetzbaren Materialien oder dort, wo keine hohen Feinheitsansprüche bestehen, zum Einsatz, beispielsweise bei Dispersionsfarben. Der wichtigste Einsatzzweck von Dissolvern ist jedoch die Vordispergierung bei der Verarbeitung schwer dispergierbarer Pigmente und bei der Herstellung hochwertiger Lacke.[10]
Dissolver zerteilen Agglomerate durch Scherung im Nahbereich der Scheibe und Druckwechsel beim Wechsel zwischen Zonen mit hohem Drucks und Unterdruck. Am Rande der Dissolverscheibe befinden sich häufig Prallvorrichtungen wie Zähne oder Stifte. Möglich ist auch die Verwendung mehrerer Rührscheiben. Das Dispergierergebnis ist im Wesentlichen von der richtigen Einstellung der Viskosität des Mahlguts, der Abstimmung der Größen von Rührscheibe und Rührbehälter und der Umfangsgeschwindigkeit der Scheibe abhängig. Wichtig ist die Ausbildung eines bis auf die Scheibe herabreichenden Sogkegels (Doughnut-Effekt).[10]
Rührwerksmühlen
Rührwerksmühlen sind die wichtigsten Dispergiergeräte bei der Herstellung von Lacken und Druckfarben. Sie haben andere Dispergiergeräte aufgrund ihrer Vielseitigkeit und ihres Leistungspotentials weitgehend verdrängt. Rührwerksmühlen arbeiten in der Regel kontinuierlich und existieren als offene oder geschlossene Ausführung. Nach der Art der Mahlkörper unterscheidet man zwischen Perlmühlen und Sandmühlen.[11] Rührwerksmühlen bestehen aus einem zu etwa zwei Dritteln mit Mahlkörpern befüllten zylindrischen Mahltopf. In der Längsachse dieses Zylinders verläuft eine Welle, auf der parallel zueinander angeordnete, durchlöcherte Scheiben zum Rühren montiert sind. Das Dispergiergut wird in den Mahlzylinder gepumpt. Die Agglomerate werden zwischen den Füllkörpern geschert, wenn die Welle rotiert. Neben der klassischen vertikalen Anordnung sind auch häufig horizontal angeordnete Mühlen im Einsatz.[11]
Eine Mehrfachdispergierung ist durch Mehrkammermühlen, die aus mehreren hintereinander liegenden Rührwerksmühlen besteht, möglich. Vorteilhaft ist die Möglichkeit der kontinuierlichen Fertigung, eine schnelle Arbeitsweise und fast keine Lösemittelemission (bei geschlossenen Varianten). Nachteilig ist der hohe Reinigungsaufwand.
Sandmühlen
Sandmühlen sind Rührwerksmühlen, bei denen Ottawa-Sand als Mahlkörper eingesetzt wurde. Sie waren über Jahre die üblichen Dispergiergeräte in der Lackindustrie. Die häufig offen betriebenen Sandmühlen wurden jedoch durch die geschlossenen Perlmühlen ersetzt.[12]
Perlmühlen
Perlmühlen sind geschlossene Rührwerksmühlen, bei denen keramische Perlen oder Hartglasperlen als Mahlkörper verwendet werden. Sie sind heute die meistverwendeten Dispergiergeräte in der Lackindustrie.[13] Je höher die Dichte der Perlen, umso größer die Dispergierintensität. Gebräuchliche Mahlkörper bestehen aus Glas, Keramik, Zirkoniumdioxid oder Stahl. Glasperlen sind preiswert und weniger abrasiv zur Mühle. ZrO2-Perlen sind hart und haben eine hohe Dichte. Sie sind cerstabilisiert und yttriumstabilisiert erhältlich. Besonders hartnäckige Pigmente, wie Nano-Zinkoxid, können nur mit Zirkonperlen vollständig dispergiert werden. Ein Nachteil bei der Verwendung harter Perlen ist verstärkter abrasiven Verschleiß an der Wandung der Mühle.
Je feiner die Perlen sind, desto mehr Fläche steht zum Zerreiben von Agglomeraten zur Verfügung. Daher kann mit feineren Perlen die gewünschte Kornfeinheit schneller bzw. in derselben Zeit größere Feinheiten erreicht werden. Zu kleine Perlen können große Agglomerate nicht einziehen und benötigen deshalb eine gewissenhafte Vordispergierung mit einem Dissolver. Die Mahlintensität steigt analog zum Dissolver auch mit der Umfangsgeschwindigkeit der Rührscheibenenden.
Kugelmühle
Kugelmühlen sind zylinderförmige Behälter, der mit Kugeln unterschiedlicher Größe (10 mm bis 30 mm) gefüllt werden kann. Die Kugeln bestehen aus Metall, Steatit, Korund oder Porzellan und machen die Hälfte des Füllvolumens aus. Die Agglomerate werden durch Rutsch- und Rollbewegungen der Kugeln zerkleinert. Vorteile sind die einfache Bedienbarkeit, der geringe Lösemittelverlust (geschlossenes System) und keine Notwendigkeit einer stetigen Überwachung. Nachteilig ist die lange Laufzeit, die diskontinuierliche Arbeitsweise, ein großer Reinigungsaufwand, die geringe Flexibilität bei der Chargengröße und der daraus folgende größere Maschinenpark. Hinzu kommt die große Lautstärke von Kugelmühlen.
Dreiwalzenstuhl
Der Dreiwalzenstuhl, auch Dreiwalze, Walzenstuhl oder Walzwerk ist ein offenes Dispergiergerät, das ebenfalls zur Dispergierung von pastösen Materialien verwendet. Es arbeitet kontinuierlich und besteht aus Aufgabe-, Mittel- und Abnahmewalze, wobei die Aufgabe- und Abnahmewalze an die feststehende Mittelwalze gepresst werden. Dabei entstehen Spalten der Breite 10 µm bis 20 µm, in denen die Zerteilung der Agglomerate durch Druck- und Scherkräfte erfolgt. Die Walzen drehen sich üblicherweise im Verhältnis 1:3:9 (Aufgabewalze : Mittelwalze: Abnahmewalze), da dies in der Regel zu den besten und wirtschaftlichsten Dispergierergebnissen führt.[14][15]
Das Dispergiergut kommt in den Aufgabespalt zwischen Aufgabe und Mittelwalze. Es wandert auf der Mittelwalze in den Abnahmespalt zwischen Mittel- und Abnahmewalze. Die Abnahmewalze übernimmt das Dispergiergut, welches dann mit einem Abstreifmesser abgenommen wird. Durch das Quetschen und Scheren zwischen den Walzen werden die Agglomerate zerkleinert. Die Walzen werden aufgrund der Temperaturerhöhung des Dispergiergutes von innen gekühlt. Wegen des hohen Lösemittelverlustes ist der Dreiwalzenstuhl nur für pastöse, also lösemittelarme Systeme verwendbar.[14] Maßgebliche Vorteile von Dreiwalzenstühlen sind geringe Festkörperverluste, schonende Dispergierwirkung und gute Reinigungsmöglichkeiten. Nachteilig wirken sich die hohen Lösemittelverluste, die Notwendigkeit einer stetigen Überwachung der Walze, sowie geringe Durchsätze und schlechte Reproduzierbarkeit aus.[14]
Extruder
Extruder sind Maschinen, die feste bis flüssige Materialien aufnehmen und das sogenannte Extrudat kontinuierlich aus einer Öffnung presst. Üblich sind Einschnecken-Extruder, die eine Knetschnecke im Inneren besitzen. Seltener sind Doppelschnecken-Extruder und Planetwalzen-Extruder (Kleinere Schnecken umlaufen eine Zentralschnecke). Extruder finden Anwendung bei der Dispergierung von Pulverlacken, wobei die schmelzbaren Rohstoffe (Bindemittel, Additive) aufgeschmolzen werden und die zu dispergierenden Bestandteile zwischen den Schnecke(n) bzw. zwischen Schnecke und Wand geschert werden.[16]
Kneter
Dieses Aggregat, das auch als Mischkneter bezeichnet wird, wird ebenfalls hauptsächlich zum Herstellen von pastösen bzw. teigartigen Systemen, meist Spachtelmassen angewendet. Kneter bestehen aus sich gegeneinander oder gegen eine feststehende Fläche bewegenden Knetwerkzeugen. Der Dispergiereffekt wird durch die starke Stauchung und Scherung des Materials erreicht.[17]
Literatur
- G. Bentzing et al.: Pigmente und Farbstoffe für die Lackindustrie. 2. Auflage, expert Verlag, 1992, ISBN 3-8169-0752-0.
- Kittel: Lehrbuch der Lacke und Beschichtungen. 2. Auflage, Band 8, S. Hirzel, 2004, ISBN 3-7776-1018-6.
Einzelnachweise
- G. Buxbaum, G. Pfaff: Industrial Inorganic Pigments. 3. Auflage, Wiley-VCH, Weinheim 2005, ISBN 3527303634, Seite 43.
- DIN 53 206
- A. Goldschmidt, H. Streitberger: BASF Handbuch Lackiertechnik. Vincentz Network, Hannover 2002, ISBN 3878703244, Seite 205ff.
- B. Müller, U. Poth: Lackformulierung und Lackrezeptur: Das Lehrbuch für Ausbildung und Praxis. Vincentz Network, Hannover 2006, ISBN 3878701705, Seite 59.
- B. Müller, U. Poth: Lackformulierung und Lackrezeptur: Das Lehrbuch für Ausbildung und Praxis.Vincentz Network, Hannover 2006, ISBN 3878701705, Seite 50.
- A. Goldschmidt, H. Streitberger: BASF Handbuch Lackiertechnik. Vincentz Network, Hannover 2002, ISBN 3878703244, Seite 226ff.
- DIN 55607:2007-06 Pigmente und Füllstoffe - Dispergierung von Pigmenten in Pulverlacken und deren farbmetrischen Beurteilung nach der Applikation
- G. Meichsner, T. Mezger, J. Schröder: Lackeigenschaften messen und steuern. Vincentz Network, Hannover 2003, ISBN 3878707398, Seite 191.
- H. Römpp: Römpp Lexikon Lacke und Druckfarben. Thieme, Stuttgart 1998, ISBN 9783137760016, Seite 147.
- H. Römpp: Römpp Lexikon Lacke und Druckfarben. Thieme, Stuttgart 1998, ISBN 9783137760016, Seite 150f.
- H. Römpp: Römpp Lexikon Lacke und Druckfarben. Thieme, Stuttgart 1998, ISBN 9783137760016.
- H. Römpp: Römpp Lexikon Lacke und Druckfarben. Thieme, Stuttgart 1998, ISBN 9783137760016, Seite 506.
- H. Römpp: Römpp Lexikon Lacke und Druckfarben. Thieme, Stuttgart 1998, ISBN 9783137760016, Seite 438.
- H. Römpp: Römpp Lexikon Lacke und Druckfarben. Thieme, Stuttgart 1998, ISBN 9783137760016, Seite 156.
- A. Goldschmidt, H. Streitberger: BASF Handbuch Lackiertechnik. Vincentz Network, Hannover 2002, ISBN 3878703244, Seite 234ff.
- H. Römpp: Römpp Lexikon Lacke und Druckfarben. Thieme, Stuttgart 1998, ISBN 9783137760016, Seite 214.
- H. Römpp: Römpp Lexikon Lacke und Druckfarben. Thieme, Stuttgart 1998, ISBN 9783137760016, Seite 325.