Power to Liquid
Unter dem Begriff Power to Liquid (PtL) (deutsch etwa: „Elektrische Energie zu Flüssigkeit“),[1] versteht man die Umwandlung von elektrischem Strom in Flüssigkraftstoff. Bei dem PtL-Prozess handelt es sich um eine Aneinanderreihung verschiedener Teilprozesse. Dieses Verfahren wird noch nicht großtechnisch eingesetzt, ermöglicht aber potenziell die Kraftstoffversorgung aus regenerativ erzeugtem Strom für die Sektoren, die auf Flüssigkraftstoff nicht verzichten können (wie z. B. die Luftfahrt).
Die untenstehende Abbildung stellt die gängigste Kombination der Prozessschritte dar; es existieren aber auch abweichende Kombinationen.[1]
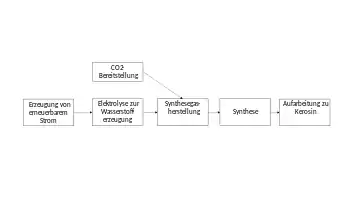
Prozessbeschreibung
Stromherstellung
Da elektrischer Strom ein homogenes Gut ist, kann grundsätzlich bei der Herstellung von PtL jede Art von Strom eingesetzt werden. Die Gewinnung von PtL aus fossilen Kraftstoffen wäre jedoch aufgrund der vielen Umwandlungsschritte und -verluste weder ökonomisch noch ökologisch sinnvoll. Gleiches gilt auch für die Gewinnung von PtL aus der Verstromung von Biomasse. Ökologisch sinnvoll ist lediglich die Gewinnung aus erneuerbaren Energien (Wind, Solar, Wasser), also aus elektrisch erzeugtem grünem Wasserstoff. Eine Gewinnung von PtL auf Basis des aktuellen Strommixes der Bundesrepublik Deutschland wäre im Vergleich mit der Gewinnung der gleichen Kraftstoffmenge aus fossilem Rohöl nur mit einer geringen Reduzierung des CO2-Ausstoßes verbunden.[2]
Bei der Stromversorgung des PtL-Prozesses ist zu beachten, dass die am Ende der Prozesskette ablaufenden Syntheseprozesse idealerweise kontinuierlich stattfinden, Wind- und Solarenergie aber nur in Abhängigkeit von der Tageszeit und den Wetterverhältnissen zur Verfügung stehen. Sofern die Stromerzeugung nicht ausschließlich durch Wasserkraft erfolgen kann, muss daher eine Abpufferung der Stromschwankungen stattfinden.
Elektrolyse
Elektrolyse ist die chemische Aufspaltung einer Substanz in ihre Komponenten durch Zuführung von Energie in Gestalt elektrischen Stroms. Die für den PtL-Prozess typische Elektrolyse ist die Wasserelektrolyse, bei der Wasser (H2O) in seine Komponenten Wasserstoff (H2) und Sauerstoff (O2) aufgespalten wird.
Hierbei gibt es drei wesentliche Elektrolyseformen:
- Alkalische Elektrolyse
- PEM-Elektrolyse
- Hochtemperaturelektrolyse
Alkalische Elektrolyseure nutzen einen porösen Separator, der die Gase Wasserstoff und Sauerstoff physikalisch trennt, aber den Austausch des flüssigen Elektrolyten weiterhin ermöglicht[3]. Dies ist die älteste Form der Elektrolyse, die bereits seit etwa einem Jahrhundert in industriellem Umfang eingesetzt wird. Gegenwärtig werden diese alkalischen Elektrolyseure hauptsächlich für die Chloralkali-Elektrolyse zur Gewinnung von Chlor und Natronlauge eingesetzt. Bei Einsatz zur Wasserstofferzeugung liegt ihre Konversionseffizienz bei ca. 66 %. Sie können in gewissem Umfang flexibel auf Schwankungen der Stromversorgung reagieren, aber sind in diesem Punkt begrenzt (Lastbereich zwischen 15 und 100 %, Reaktionszeit bei Kaltstart ca. 50 Minuten).[4]
Die PEM-Elektrolyse (Proton Exchange Membrane) geht auf Forschungen aus den 1970er Jahren zurück. Der Name leitet sich daraus ab, dass eine PEM-Elektrolysezelle eine protonenleitende Membran aufweist.[5] Dies ist ein gasdichter Feststoffelektrolyt, der die Anode von der Kathode isoliert, aber durch selektive Leitfähigkeit für Kationen den elektrischen Stromkreis schließt.[3] Die Konversionseffizienz ist ähnlich wie die der alkalischen Elektrolyse. Vorteil der PEM-Elektrolyse ist ihre größere Teillastflexibilität, die theoretisch von 0 bis 100 % geht, wobei in der Praxis von einer unteren Grenze von ca. 5 % der nominalen Leistung aufgrund des Eigenverbrauchs der Peripheriekomponenten auszugehen ist.[5] Die Startzeit bei einem Kaltstart beträgt rund 10 Minuten, die Zeit aus dem Stand-by bis zur Nennleistung nur 10 Sekunden.[5]
Die Hochtemperaturelektrolyse (HTES – High Temperature Electrolysis of Steam) wird gegenwärtig (ca. 2016) noch nicht in großem Maßstab eingesetzt, sondern ist eher Gegenstand der Grundlagenforschung. Bei der Hochtemperaturelektrolyse wird ein Teil der zur Spaltung von Wasser benötigten Energie thermisch zugeführt. Dieses Verfahren arbeitet mit einem Temperaturniveau von 800 bis 1000 °C.[5] Durch die hohen Temperaturen kommt die Hochtemperaturelektrolyse mit deutlich geringeren Zellspannungen aus als die anderen Elektrolyseverfahren und erreicht so hohe strombezogene Wirkungsgrade.[5] Diese hohe (elektrische) Konversionseffizienz (rund 80 %) ist der Hauptvorteil der Hochtemperaturelektrolyse – die Konversionsverluste sind nur etwa halb so hoch wie bei den anderen Elektrolyseverfahren. Diese elektrische Effizienz lässt sich allerdings in der Praxis nur erreichen, wenn die erforderliche hohe Temperatur nicht selber durch Strom erzeugt werden muss, sondern auf anderem Wege bereitgestellt wird.[4] Wenn die nachgelagerte Synthese am gleichen Standort wie die Elektrolyse erfolgt, kann die Abwärme des Syntheseprozesses als Wärmequelle verwendet werden[6], konkurriert dann allerdings im Falle einer CO2-Gewinnung aus der Umgebungsluft mit dem damit verbundenem Energiebedarf.[6]
Hauptnachteil der Hochtemperaturelektrolyse ist ihre geringe Flexibilität. An- und Abschalten der Elektrolyseure und die damit verbundenen Temperaturschwankungen führen zu hohen Belastungen der Zellen, die die Lebensdauer drastisch verkürzen und im Falle eines ungleichmäßigen Hochfahren des Elektrolysemoduls (Stacks) zu einer direkten Zerstörung der Zellen führen können.[7] Auch das Teillastverhalten der Hochtemperaturelektrolyse ist wenig dynamisch.[4] Sie eignet sich daher hauptsächlich für Situationen mit kontinuierlicher Stromversorgung, z. B. durch Wasserkraft.
CO2-Bereitstellung
Neben Energie und Wasser ist CO2 der dritte wesentliche Einsatzfaktor für den PtL-Prozess. CO2 ist praktisch überall in der Atmosphäre vorhanden, aber nur in einer sehr geringen Konzentration von 0,04 %. Deshalb erfordert eine direkte Gewinnung aus der Erdatmosphäre den Durchsatz sehr großer Mengen an Luft und ist daher entsprechend aufwändig. Eine grundsätzlich einfachere Art ist die Gewinnung aus den Abgasen stationärer Emitter, in denen das CO2 in ungleich größeren Anteilen enthalten ist.
Gewinnung von CO2 aus den Abgasen stationärer Emitter
Die wichtigsten stationären Emitter sind in Tabelle 1 zusammengestellt.
Tabelle 1: Stationäre CO2-Quellen in der Bundesrepublik Deutschland, 2016[5]
Industrie | CO2-Menge im Jahr (Mio. Tonnen) | Anmerkungen |
Braunkohlekraftwerke | 159 | Annähernd kontinuierlicher Betrieb |
Steinkohlenkraftwerke | 96 | Diskontinierlicher Betrieb |
Stahlindustrie | 57 | |
Mineralölraffinerien | 23 | |
Zementindustrie gesamt | 23 | |
Zementindustrie energiebedingt | 11 | Hoher Anteil alternativer Brennstoffe |
Zementindustrie rohstoffbedingt | 12 | |
Kalkindustrie gesamt | 8 | |
Kalkindustrie energiebedingt | 5 | |
Kalkindustrie rohstoffbedingt | 3 | |
Ammoniakherstellung gesamt | 6 | Annähernd kontinuierlicher Betrieb |
Ammoniakherstellung CO2-Prozessgas | 4 | Reinheitsgrad 99,5 % |
Ammoniakherstellung energiebedingt (Rauchgas) | 2 | |
Glasindustrie | 4 | Annähernd kontinuierlicher Betrieb |
Biobasierte CO2-Quellen | ||
Biogasanlagen | 1 | Verteilt auf hunderte Anlagen |
Bioabfallvergärung | 0,3 | |
Klärgasanlagen | 0,8 | Verteilt auf hunderte Anlagen |
Bioethanolherstellung | 1 |
Der bei weitem größte Teil der industriellen CO2-Emissionen entsteht durch die Verbrennung zur Energiegewinnung, entweder zur Stromgewinnung im Kraftwerk oder zur Erzeugung von Prozesswärme (z. B. an Hochöfen oder bei der Glasherstellung). Diese Verbrennungsabgase haben unvermeidlich einen hohen Anteil von Verunreinigungen durch Ruß, Stickstoff oder andere Produkte unvollständiger Verbrennung. Bei Einsatz schwefelhaltiger fossiler Brennstoffe muss auch mit der Präsenz von Schwefel und Schwefelverbindungen im Abgas gerechnet werden.[5]
Nur ein relativ geringer Anteil der CO2-Emissionen ist rohstoffbedingter Natur, und damit unvermeidlich. Die größte Menge derartiger CO2-Emissionen findet in der Zementindustrie mit etwa 12 Millionen Tonnen im Jahr statt. Der Reinheitsgrad derartiger CO2-Emissionen ist tendenziell deutlich höher. Am größten ist er in der Ammoniakherstellung, wo das CO2 prozessbedingt fast rein anfällt (99,5 %).[5]
Als Produkt natürlicher biologischer Zersetzung fällt CO2 bei Biogasanlagen, der Bioabfallvergärung, Kläranlagen und bei der Bioethanolherstellung an. Auch dieses CO2 hat tendenziell einen sehr hohen Reinheitsgrad. Die absolut jährlich anfallende Menge ist allerdings mit insgesamt 3 Millionen Tonnen CO2 eher gering und entspricht stöchiometrisch nur etwa dem Kohlenstoffäquivalent einer Million Tonnen Kerosin. Darüber hinaus fällt dieses CO2 dezentral verteilt auf Hunderte von Anlagen an.[5]
Insgesamt liegen die rohstoff- oder zersetzungsbedingten CO2-Emissionen bei rund 22 Millionen Tonnen im Jahr, was stöchiometrisch etwa 7 Millionen Tonnen Kerosin oder Dieselkraftstoff entspricht. Die verbrennungsbedingten CO2-Emissionen betragen mehr als das Zehnfache.
Gewinnung von CO2 aus der Atmosphäre
Die Gewinnung von CO2 aus der Atmosphäre wurde bereits in den Neunziger Jahren im Rahmen eines Projektes des Landes Baden-Württemberg untersucht[8] und gegenwärtig von verschiedenen Lehrstühlen und Startups verfolgt. Ein Beispiel ist die Schweizer Firma Climeworks, die in Hinwil bereits zwei entsprechende Anlagen betreibt.[9] In diesen Anlagen wird die Luft durch Pumpen eingesaugt und durch einen Filter geleitet, in dem das CO2 chemisch gebunden wird. Ist der Filter voll, wird er auf etwa 100 °C aufgeheizt, wodurch das CO2 aus der chemischen Bindung gelöst wird und für die weiteren Prozessschritte zur Verfügung steht.[10] Diese erste dieser Anlagen läuft seit Mai 2017 mit einer Kapazität zur Gewinnung von 900 Tonnen CO2 pro Jahr.[11] Weitere auf diesem Gebiet arbeitende Unternehmen sind Carbon Engineering und Global Thermostat.[12]
Synthesegasherstellung
Beim typischen PtL-Prozess wird zunächst Wasserstoff erzeugt und dann mit CO2 zusammengeführt. CO2 ist aber inert und muss für die anschließenden Syntheseschritte in CO umgewandelt werden. Dieser Prozessschritt wird als reverse water gas shift reaction bezeichnet. Das Resultat ist dann ein Synthesegas aus Wasserstoff und CO, idealerweise in einem stöchiometrischen Verhältnis von 2:1.[13]
Abweichend hiervon erfolgen bei der Hochtemperaturelektrolyse sowie beim StL-Verfahren (Solar to Liquid) die Umwandlung von Wasser und CO2 in Wasserstoff und CO in einem einzigen Schritt. Im Falle der Hochtemperaturelektrolyse geschieht dies als Co-Elektrolyse unter Einsatz von Wasserdampf, und beim StL-Verfahren direkt durch die solarthermische Erhitzung von Wasser und CO2. Vorteile bei diesem Ansatz sind die geringeren Konversionsverluste verglichen mit dem sequenziellen Vorgehen sowie der Umstand, dass die beiden Reaktionen (Elektrolyse und reverse water gas shift reaction) in einem Reaktor erfolgen, wodurch sich der apparative Aufwand reduziert.[7]
Synthese und Aufarbeitung zu Kerosin
Für die Herstellung von Flüssigkraftstoffen aus Synthesegas sind drei alternative Ansätze bekannt.
Fischer-Tropsch-Synthese
Der bekannteste und am weitesten verbreitete Ansatz ist die Fischer-Tropsch-Synthese. Dieses Verfahren wurde bereits 1925 am Kaiser-Wilhelm-Institut für Kohleforschung als Verfahren zur Herstellung von Kraftstoffen aus Kohle entwickelt, und in darauffolgenden Jahrzehnten weiter entwickelt und in großem Maßstab eingesetzt. Von besonderer Bedeutung war es im Zweiten Weltkrieg, da ein Import von Rohöl zur Versorgung der deutschen Raffinerien kriegsbedingt nur begrenzt möglich war und die Treibstoffversorgung der deutschen Streitkräfte daher ein Ausweichen auf synthetische Kraftstoffe erforderte.
Mit der Verfügbarkeit von preisgünstigem Rohöl nach dem Ende des Zweiten Weltkriegs war die Raffination von Rohöl die kostengünstigere Alternative, so dass die Produktion synthetischer Kraftstoffe eingestellt wurde. Eine Ausnahme war Südafrika, wo beginnend in den 50er Jahren[13] mit dem Aufbau einer Industrie begonnen wurde, die südafrikanische Kohle in flüssige Kraftstoffe umwandelte. Ein wesentlicher Faktor für den Ausbau dieser Industrie waren das weltweite Embargo gegen das südafrikanische Apartheidsregime und die damit verbundenen Probleme beim Import von Rohöl in den 80er Jahren. In den hierfür durch die südafrikanische Firma Sasol (Suid Afrikaanse Steenkool en Olie) errichteten Fischer-Tropsch-Anlagen wurde erstmals auch Kerosin aus Kohle hergestellt.
Obwohl das Fischer-Tropsch-Verfahren ursprünglich für die Umwandlung von Kohle entwickelt wurde, wird es heutzutage vor allem für die Umwandlung von Erdgas verwendet, insbesondere in Qatar und in Malaysia. Der Einsatz des Verfahrens für die Konversion von Biomasse wurde verschiedentlich versucht, zuerst vor rund zehn Jahren durch die Firma Choren, ist aber bisher nicht geglückt. Zwei neuere Anläufe zur Gewinnung von FT-Kerosin aus Biomasse werden gegenwärtig durch Projekte der amerikanischen Firmen Fulcrum (Einsatzstoff: Haushaltsabfälle) und Red Rocks (Einsatzstoff: Holz) gemacht, deren Anlagen im Laufe des Jahres 2021 mit der Produktion von FT-Kerosin beginnen sollen.
Das Fischer-Tropsch-Verfahren ist ein etabliertes, bereits in sehr großem Maßstab industriell eingesetztes Verfahren. Die gegenwärtig weltweit größten Fischer-Tropsch-Anlagen sind die des Pearl-Konsortiums in Qatar mit einer jährlichen Produktion von Flüssigkraftstoffen von 95 Millionen Tonnen, zu deren Bau Investitionen in Höhe von 24 Milliarden USD erforderlich waren. Es existieren mehrere große Marktteilnehmer mit Kenntnissen im Bau von Fischer-Tropsch-Anlagen, insbesondere Shell (Partner im Pearl-Konsortium) und Sasol. Diese Art von Anlagen ist allerdings mit sehr hohen Fixkosten verbunden und lässt sich daher nur im sehr großen Maßstab wirtschaftlich betreiben. Um auch Feedstock aus kleineren Quellen (z. B. einzelnen Biogasanlagen) nutzen zu können, haben einzelne Forschungseinrichtungen in Zusammenarbeit mit Startups Verfahren entwickelt, die auf die Nutzung kleiner Quellen ausgelegt sind. Wesentliche Akteure sind hierbei die englische Firma Velocys sowie die deutsche Firma Ineratec, eine Ausgründung aus dem Karlsruher Institut für Technologie.
Beim Fischer-Tropsch-Verfahren wird das Synthesegas mit Hilfe von Eisen- oder Kobaltkatalysatoren[14] in Wachse mit sehr unterschiedlicher Kettenlänge umgewandelt, wobei die Verteilung der Länge der Kohlenwasserstoffketten in gewissem Umfang eingestellt werden kann.[13] Die weitere Aufarbeitung der Wachse zu Flüssigkraftstoffen erfolgt dann durch Isomerisierung und Hydrocracking.[15]
Methanolsynthese
Bei der Methanolsynthese wird das Synthesegas mittels kupfer-, zink- oder aluminiumoxidbasierten Katalysatoren in Methanol umgewandelt.[16] Dieser Prozessschritt wurde bereits vor mehreren Jahrzehnten von der Firma Mobil erprobt und kann als grundsätzlich gut bekannt angesehen werden.[17] Es existiert bereits eine von der Firma Carbon Recycling International betriebene Anlage zur Umwandlung von CO2 und Wasser zu Methanol. Diese Anlage wurde 2012 in Betrieb genommen und hat eine Jahreskapazität von 4.000 Tonnen[17] und damit eher Democharakter. Die Firma bietet jedoch Technologielösungen für Anlagen zur Produktion von Methanol mit einer Jahreskapazität von 50.000 bis 100.000 Tonnen Methanol an.[18] Weitere Akteure in diesem Bereich sind Thyssenkrupp und Mitsubishi Hitachi. Vorteil der Methanolsynthese gegenüber der Fischer-Tropsch-Synthese ist die Vermeidung des reverse water gas shift-Schrittes und der damit verbundenen Energieverluste.[8]
Alkoholsynthese
Bei der Alkoholsynthese wird als erster Prozessschritt das Synthesegas katalytisch in höhere Alkohole wie Ethanol, Propanol oder Butanol umgewandelt.[13] Dieser Ansatz wird gegenwärtig von der Firma Swedish Biofuels erforscht.[19]
Ammoniak
Die Herstellung von Ammoniak im strombasierten Power-to-Ammonia-Verfahren statt aus Erdgas kann ebenfalls zu den Power-to-Liquid-Verfahren im weiteren Sinne gezählt werden, auch wenn Ammoniak bei Normalbedingungen gasförmig ist und nur bei hohem Druck oder niedrigen Temperaturen flüssig vorliegt.
Verwechslungsgefahr mit anderen Prozessen
Nicht mit dem PtL-Ansatz zu verwechseln sind Ansätze, bei denen eine direkte Nutzung der Sonneneinstrahlung zur Produktion von Flüssigkraftstoffen erfolgt, ohne dass vorher eine Erzeugung von Strom stattfindet. Insbesondere der englischsprachige Begriff "Solar Power" (Sonnenenergie) kann zu Verwechslungen mit der Erzeugung aus "Power" (Strom) führen. Eine Schilderung eines derartigen Prozesses, die ebenfalls im Zusammenhang mit erneuerbaren Energien steht, findet man beispielsweise im Scientific American, wo Ende März 2012 ein Artikel mit dem Titel "Mikroben helfen bei der Umwandlung von Solarenergie in flüssigen Treibstoff" (Solar Power to Liquid Fuel) erschienen ist. Darin wird ein integrated electro-microbial bioreactor, zu Deutsch etwa integrierter elektro-mikrobieller Bioreaktor beschrieben, der in der Lage sein soll, mit Hilfe von gentechnisch veränderten Ralstonia eutropha verschiedene flüssige Butanole wie beispielsweise 1-Butanol zu erzeugen, die sich als Kraftstoff eignen[20]. Hierbei handelt es sich um einen völlig andersartigen Prozess als bei der Produktion von PtL.
Ebenfalls ein anderer Ansatz ist der StL-Ansatz (Solar to Liquid). Der Solar to Liquid-Ansatz wird gegenwärtig hauptsächlich an der ETH Zürich (Lehrstuhl Professor Steinfeld) erforscht. Konzeptionell besteht der Ansatz darin, Sonnenlicht über Parabolspiegel an einem Punkt zu bündeln und so an diesem Punkt eine Temperatur von 1.500 °C zu erreichen, bei der Wasser und CO2 direkt in ein Synthesegas aus Wasserstoff und CO umgewandelt werden.[21] Vorteil dieses Verfahrens ist die Vermeidung der Konversionsverluste, die beim PtL-Verfahren zunächst bei der Stromerzeugung und anschließend bei der Elektrolyse entstehen. Diese Umwandlungsverluste sind erheblich, da gängige Solarkollektoren weniger als 20 % der eintreffenden Sonnenenergie in Strom verwandeln und bei der anschließenden Elektrolyse des gewonnenen Stroms weitere Umwandlungsverluste von bis zu 33 % entstehen. Im Gegensatz dazu ist die Bündelung des Sonnenlichts durch Spiegel mit nur geringen Verlusten verbunden; die Masse der eingestreuten Sonnenenergie kann dazu verwendet werden, die gewünschten hohen Temperaturen zu erreichen.[22] Nachteil des Verfahrens ist die aufwändige Mechanik zum ständigen Nachführen der Spiegel, die erforderlich ist, um trotz des ständig wechselnden Sonnenstandes kontinuierlich eine Bündelung aufrechtzuerhalten. Ebenfalls nachteilig ist, dass dieses Verfahren ausschließlich auf Sonnenenergie beruht; eine Kompensation sonnenschwacher Perioden durch Windenergie ist bei diesem Verfahren, anders als bei Strom, nicht möglich.
Eine Laboranlage für das StL-Konzept existiert auf dem Dach der ETH Zürich. Diese Anlage wird laufend betrieben und erzeugt Flüssigkraftstoff im Milliliterbereich (ca. 100 ml täglich).[23] Eine zehnmal so große Anlage befindet sich in Móstoles in Spanien.[21] Noch deutlich größere Anlagen, insbesondere eine Großanlage in Spanien[21] sind konzipiert, aber sind bisher nicht über den Status von Papierstudien hinausgekommen.
Anlagen
- In Island wurde im April 2012 eine acht Millionen Euro teure Power-to-Liquid-Anlage von der Firma Carbon Recycling International (CRI) mit einer Kapazität von 1,3 Millionen Litern pro Jahr in Betrieb genommen. 2015 erweiterte CRI die Anlage auf mehr als 5 Millionen Liter pro Jahr. Die nach George Olah benannte Anlage sollte anfangs jährlich 4.500 Tonnen CO2 nutzen und damit Methanol erzeugen. Sowohl das CO2 als auch die elektrische Energie stammen aus dem benachbarten Kraftwerk Svartsengi.[24]
- In Werlte in Niedersachsen ging am 4. Oktober 2021 eine Pilot-Anlage zur Gewinnung eines synthetischen Kraftstoffes, „Syncrude“, auf Basis des oben beschriebenen Fischer-Tropsch-Verfahrens in Betrieb.[25] Vorgeschaltet ist ein Zwischenschritt zur Gewinnung von Synthesegas. Über einen weiteren Schritt wird anschließend in der Raffinerie Heide (Schleswig-Holstein) Kerosin der Marke „Jet A1“ gewonnen.[26] Gebaut wurde die Anlage von atmosfair.[27] Das Pilotprojekt trägt den Namen „FairFuel“.[28] Die Anlage verfügt über eine Herstellungsleistung von 44 kg/h synthetischen Kohlenwasserstoff.[29] Es handelt sich um die erste Anlage weltweit, in der hier als E-Kerosin bezeichnetes Kerosin aus Windkraft produziert wird. Der Regelbetrieb soll im ersten Quartal 2022 starten. Dann sollen in Werlte acht Fässer Rohkerosin pro Woche produziert werden.[30]
Literatur
- Kompetenzzentrum Klima- und Lärmschutz im Luftverkehr (2020): Betrachtung und Ausblick der Technologien zur Herstellung von "Power-to-Liquid" (PtL)
- Michael Sterner, Ingo Stadler (Hrsg.): Energiespeicher. Bedarf, Technologien, Integration. 2. Auflage. Berlin Heidelberg 2017, ISBN 978-3-662-48893-5.
Weblinks
- Kompetenzzentrum für Klima- und Lärmschutz im Luftverkehr, CENA Hessen
- Strategieplattform Power to Gas
- Deutscher Bundestag – Wissenschaftliche Dienste: Der Aktuelle Begriff: Power to Gas (PDF; 69 kB)
- M. Specht (Projektleitung) und Andere: „CO2-Recycling zur Herstellung von Methanol“ Zentrum für Sonnenenergie- und Wasserstoff-Forschung Baden-Württemberg (ZSW), Institut für Technische Thermodynamik und Kältetechnik (ITTK), Universität Karlsruhe Institut für Physikalische Elektronik (IPE), Universität Stuttgart, Juli 2000
Einzelnachweise
- Kompetenzzentrum Klima- und Lärmschutz im Luftverkehr, CENA Hessen: Betrachtung und Ausblick der Technologien zur Herstellung von "Power-to-Liquid" (PtL). 2020 (cena-hessen.de).
- Bullerdiek, N.; Buse, J.; Dögnitz, N.; Feige, A.; Halling, A.-M.; Hauschild, S.; Hawighorst, P.; Kaltschmitt, M.; Kuchling, T.; Kureti, S.; Majer, S.; Marquardt, C.; Müller-Langer, F.; Neuling, U; Oehmichen, K.; Pechstein, J.; Posselt, D.; Scheuermann, S.; Schripp, T.; Stein, H.; Zschocke, A.: Einsatz von Multiblend-JET-A-1 in der Praxis. Zusammenfassung der Ergebnisse aus dem Modellvorhaben der Mobilitäts- und Kraftstoffstrategie. DBFZ Deutsches Biomasseforschungszentrum gemeinnützige GmbH, Leipzig., 2019, S. Kapitel 9.2.
- Philipp Lettenmeier: Wirkungsgrad – Elektrolyse. In: Siemens Whitepaper. Januar 2019, S. 5.
- Smolinka / Wiebe, Sterchele / Palzer / Lehner / Jansen / Kiemel / Miehe / Wahren / Zimmermann.: Studie IndWEDe: Industrialisierung der Wasserelektrolyse in Deutschland: Chancen und Herausforderungen für nachhaltigen Wasserstoff für Verkehr, Strom und Wärme. Berlin 2018.
- Simon Lechleitner: Ganzheitliche Betrachtung der Kraftstofferzeugung aus Strom unter Einbeziehung von CO2-Quellen am Fallbeispiel Deutschland. Mittweida 2016, S. 16.
- Agora Verkehrswende, Agora Energiewende and Frontier Economics: The Future Cost of Electricity-Based Synthetic Fuels. 2018, S. 61–62.
- Florian Ausfelder und Hanna Dura (Hrsg.): Optionen für ein nachhaltiges Energiesystem mit Power-to-X-Technologien – 2. Roadmap des Kopernikus-Projektes "Power-to-X". Abschnitt 7.2. Auflage. Frankfurt am Main 31. August 2019, S. 131 (Betrachtet wurde der Fall von Temperaturdifferenzen vorne und hinten am Stack von 50 bis 100°C.).
- Specht / Bandi / Elser / Heberle / Maier / Schaber / Weimer: CO2-Recycling zur Herstellung von Methanol; Endbericht an das Land Baden-Württemberg. Juli 2020, S. 74.
- Climeworks eröffnet erste kommerzielle CO2-Filteranlage der Welt. 27. Juni 2017, abgerufen am 11. Januar 2021 (deutsch).
- Reverse climate change by removing CO2 from the air. Abgerufen am 11. Januar 2021.
- Valentin Batteiger / Christoph Falter / Andreas Sizmann: Prospects and sustainability of large‐scale CO2 provision for synthetic jet fuel production. Vortrag auf dem 9th Carbon Dioxide Utilization Summit. Reykjavík 19. Oktober 2017, S. 19.
- Direct Air Capture Technology. Abgerufen am 11. Januar 2021 (englisch).
- Reinhard Rauch / Hermann Hofbauer / Ulf Neuling / Martin Kaltschmitt: Biokerosene Production from Bio-Chemical and Thermo-Chemical Biomass Conversion and Subsequent Fischer-Tropsch Synthesis. In: Martin Kaltschmitt / Ulf Neuling (Hrsg.): Biokerosene – Status and Prospects. Heidelberg 2018, S. 505.
- ASTM D7566, Annex 1.
- Bullerdiek, N.; Buse, J.; Dögnitz, N.; Feige, A.; Halling, A.-M.; Hauschild, S.; Hawighorst, P.; Kaltschmitt, M.; Kuchling, T.; Kureti, S.; Majer, S.; Marquardt, C.; Müller-Langer, F.; Neuling, U; Oehmichen, K.; Pechstein, J.; Posselt, D.; Scheuermann, S.; Schripp, T.; Stein, H.; Zschocke, A.: Einsatz von Multiblend-JET-A-1 in der Praxis. In: Zusammenfassung der Ergebnisse aus dem Modellvorhaben der Mobilitäts- und Kraftstoffstrategie. DBFZ Deutsches Biomasseforschungszentrum gemeinnützige GmbH. Leipzig, S. Kapitel 11.1.
- ASTM Subcommittee D.02.J on Aviation Fuels, February 24 ballot, ballot item 45, WK69614.
- Schmidt, Patrick / Batteiger, Valentin / Roth, Arne / Weindorf, Werner / Raksha, Tetyana: Power-to-Liquids as Renewable Fuel Option for Aviation: A Review. In: Chemie Ingenieur Technik. Band 90 (1-2), 2018, S. 127–140.
- Technology and Services. Abgerufen am 11. Januar 2021 (amerikanisches Englisch).
- Telefonische Auskunft von Swedish Biofuels
- Fossil Free: Microbe Helps Convert Solar Power to Liquid Fuel. Abgerufen am 11. Januar 2021.
- Aus Sonnenlicht und Luft entsteht Benzin. Abgerufen am 11. Januar 2021.
- Angaben der ETH Zürich
- Angaben der ETH Zürich
- chemicals-technology.com: George Olah CO2 to Renewable Methanol Plant, Reykjanes, Iceland, abgerufen am 15. Oktober 2013.
- Newsletter Oktober 2021. In: www.atmosfair.de. atmosfair, 1. Oktober 2021, abgerufen am 4. Oktober 2021.
- CO₂-neutrales E-Kerosin - der Einstieg in einen klimaverträglichen Luftverkehr schon heute. In: www.atmosfair.de. atmosfair, Oktober 2021, abgerufen am 4. Oktober 2021.
- Bernhard Pötter: Klimaschutz in der Luftfahrt: Nur grünes Fliegen ist schöner. An diesem Montag startet die erste Produktion von CO2-neutralem Flugbenzin in Deutschland. Zurück geht die Anlage auf eine Klimaschutzorganisation. In: taz.de. Die Tageszeitung, 3. Oktober 2021, abgerufen am 4. Oktober 2021.
- atmosfair fairfuel - Kriterienkatalog. (PDF; 1,5 MB) Gütesiegel für grünes, synthetisches Kerosin. In: www.atmosfair.de. atmosfair, 1. Oktober 2021, S. 34, abgerufen am 4. Oktober 2021.
- Feststellung gemäß § 5 UVPG Solarbelt FairFuel GmbH Werlte. (PDF; 35 kB) GAA v. 13.10.2020 ― Akz.: 31.12-40211/1-4.1.1 OL 19-113-01+02―. In: uvp.niedersachsen.de. Niedersächsisches Ministerium für Umwelt, Energie, Bauen und Klimaschutz, Referat 14: Umweltinformation, Digitalisierung, eGovernment, 16. Oktober 2020, abgerufen am 4. Oktober 2021.
- Joachim Ille: E-Kerosin: Grün durchstarten. Frankfurter Rundschau, 4. Oktober 2021, abgerufen am selben Tage.