Plasmanitrieren
Beim Plasmanitrieren und -nitrocarburieren wird in einer ionisierten Gasatmosphäre gezielt Stickstoff in die Randzone von Eisenbasislegierungen eindiffundiert. Das Plasmanitrierverfahren wird angewandt, um Funktionsflächen eine höhere Oberflächenhärte zu vermitteln, damit diese einen erhöhten Widerstand gegen abrasiven, adhäsiven und korrosiven Verschleiß bekommen.
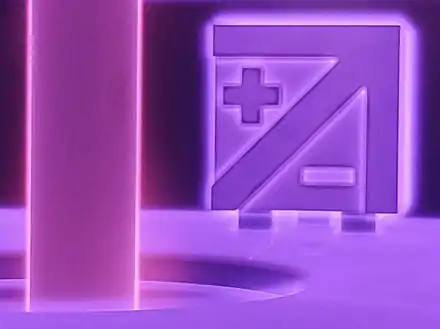
Geschichte
Historische Funde beweisen, dass bereits vor Christus (wenn auch nur auf natürlichem Wege) nitriert bzw. nitrocarburiert wurde:
In China wurden carbonitrierte Werkstücke aus der Zeit um 100 vor Christus gefunden. Eisensäule/-stäbe mit Stickstoffgradienten (natürliche Nitrierung) an der Oberfläche gibt es in Indien seit 415 nach Christus. Zu Beginn des 20. Jahrhunderts erstellte Adolph Machelet in den USA die ersten Arbeiten über die Gasnitrierung (erste Patente 1908). Es folgte Adolph Fry in Deutschland mit Untersuchungen über den Einfluss und die Rolle des Stickstoffs auf Legierungselemente (Patent aus 1921). Die Salzbadnitrierung erlangte in den 1920er Jahren immer mehr Anerkennung, nachdem Hermann Schlosser aus den USA erste Erfahrungen mit cyanidhaltigen Salzschmelzen für verschleißfeste Oberflächen nach Europa bringt. Klöckner Ionon GmbH startete 1932 mit ihren ersten Plasmanitrieranlagen. Im Jahr 1944/1945 fanden bereits militärische Anwendungen Gefallen daran (Nitrierung von Geschützrohren, …). Die industrielle Akzeptanz stieg in den 1970er Jahren in Europa. Die Warmwand-Technologie wurde in den 1980er Jahren entwickelt. Alternative Verfahren wie „plasma immersion ion implantation“ oder „Aktiv-Gitter“ wurden in den 1990er Jahren entwickelt. Heute wird die Plasmanitriertechnologie weltweit akzeptiert.
Funktionsweise
Das Verfahren arbeitet mit einem Stickstoff-Wasserstoff-Gasgemisch als Nitriermedium, das in einen Vakuumofen bei einem Unterdruck von 50 Pa bis 600 Pa mittels einer stromstarken Glimmentladung ionisiert wird. Wegen der hohen energetischen Wirkung des Plasmas kann die Arbeitstemperatur beim Plasmanitrieren gegenüber dem Salzbad- und dem Gasnitrieren erheblich abgesenkt werden, so dass dieses Verfahren auch bei verzugsempfindlichen Werkstoffen und Bauteilen eingesetzt werden kann. Der typische Arbeitsbereich beim Plasmanitrieren von Eisenlegierungen liegt zwischen 350 °C und 600 °C. Übersteigt nach Einschalten die Hochspannung, die zwischen Ofenwand und Charge angelegt wird, einen kritischen Wert, zündet eine Glimmentladung. Das Plasma bewirkt, dass an der Oberfläche diffusionsfähiger Stickstoff gebildet wird, der dann bei hinreichend hoher Bauteiltemperatur und einer entsprechend langen Behandlungszeit bei bestimmten Stählen bis zu 0,8 mm tief in die Randzone eindiffundieren kann. Je nach Prozessführung wird eine reine Diffusionsschicht oder bei Überschreiten der Löslichkeitsgrenze zusätzlich eine γ’(Fe4N) oder ε(Fe2-3CxNy) Eisennitridphase von 2 µm bis 20 µm Dicke aufgebaut. Während die erzielbare Randhärte im Wesentlichen von der Stahlsorte bestimmt wird, werden die Dicken der erzeugten Schichten zusätzlich durch die Behandlungstemperatur, die Behandlungszeiten und das Stickstoffangebot im Prozessgas beeinflusst.
Prozesstechnik
Um eine kontrollierte und gezielte Oberflächenveredelung mit Hilfe einer Plasmabehandlung gewährleisten zu können, ist es erforderlich, den Behandlungsprozess unter definierten Bedingungen durchzuführen. Die Prozessabläufe werden durch den Einsatz modernster Prozess- und Regeltechnik vollautomatisch abgearbeitet, so dass an den Operator keine besonderen Anforderungen gestellt werden. Moderne Anlagen werden mit PC-Steuerung und Feldbussystemen ausgerüstet. Ist- und Sollwerte werden in schematischen Darstellungen visualisiert und dokumentiert. Ebenso werden die Funktionsstellungen relevanter Stellgrößen übersichtlich dargestellt. Wichtige Funktionen der Plasmaöfen, wie Druckschalter, Ventilstellungen für Evakuieren und Behandeln, Bereitstellung von Kühlwasser als auch Betrieb des Vakuumpumpstands werden überwacht und visualisiert. Die Prozessgaszusammensetzung wird über elektronisch geregelte Massflow-Controller gesteuert. Der Druck im Reaktionsraum wird über Druckmessgeräte erfasst und die Druckeinstellung erfolgt über Regelventile in der Saugleitung oder durch drehzahlgeregelte Wälzkolbenpumpen. Die Plasmaparameter Pulshöhe, Dauer und Taktfrequenz sind in den Behandlungsabläufen frei einstellbar. Zur Unterdrückung der Lichtbögen werden Ausschaltzeiten von unter zwei Mikrosekunden und Pulswiederholzeiten von bis zu 20 kHz realisiert.
Das Warmwand- bzw. Heißwandofenkonzept mit zusätzlicher Luftkühlung gestattet ein definiertes, beschleunigtes Aufheizen und Abkühlen der Charge. Standardbetriebsarten erlauben die Behandlung mit konstanten Plasmaleistungsdichten. Dadurch wird beispielsweise beim Plasmanitrieren sichergestellt, dass die Behandlungsergebnisse unabhängig von Ofengröße und der zu behandelnden Oberfläche sind. Durch die Pulstechnologie ist der Energieeintrag in die zu behandelnde Charge wesentlich geringer als bei einer reinen Gleichspannung. Daher können sehr enge Temperaturtoleranzen innerhalb der Charge eingehalten werden. Auch bei hohen Chargierdichten sind mit Hilfe der Pulstechnologie minimale Streuungen im Behandlungsergebnis möglich. Bei konstanter Plasmaleistung wird üblicherweise die Temperatur der Charge durch die Ofenheizung geregelt, womit die thermische Prozessführung von der chemischen weitgehend entkoppelt wird.
Prozessbeschreibung
Das Werkzeug wird in einem evakuierten Behälter als Kathode geschaltet, die Behälterwand als Anode. Ein stickstoffhaltiges Gas wird in geringen Mengen zugeführt. Nach Anlegen einer Hochspannung werden die Stickstoffatome in der Nähe der Kathode ionisiert. Die positiv geladenen Stickstoffionen werden zum Werkstück hin beschleunigt, treffen dort mit hoher kinetischer Energie auf und lagern sich in die Oberfläche ein. Die Auftreffenergie wird teilweise in Wärme umgesetzt. Durch exakte Steuerung der elektrischen Größen und der Gaszufuhr kann der Schichtaufbau optimal beeinflusst werden. Bei niedrigem Stickstoffangebot ist es sogar möglich, die Verbindungsschichtbildung zu unterdrücken.
Schichtaufbau
Verbindungsschicht
Der Aufbau des äußeren Randschichtbereichs aus Nitriden, den bei Kohlenstoffstählen vorhandenen Carbonitriden, Nitrocarbiden sowie Primärcarbiden bei den übereutektoidischen Stählen, hat zu der Bezeichnung Verbindungsschicht (engl. compound layer) geführt. Diese ist je nach den Behandlungsbedingungen und je nach Werkstoffzusammensetzung einige Mikrometer dick. Die Porosität in der Verbindungsschicht ist im Prinzip nicht zu vermeiden. Es wird angenommen, dass sie wegen der Metastabilität der Fe-N(-C)-Carbonitridphasen entsteht. Diese führt zum Ausscheiden von Stickstoff, der zu Molekülen rekombiniert. Dadurch entstehen Poren, bevorzugt an energetisch begünstigten Stellen wie z. B. Korngrenzen innerhalb der Verbindungsschicht.
Diffusionsschicht
Der Randschichtbereich unterhalb der Verbindungsschicht wird als Diffusionsschicht, manchmal auch als Ausscheidungs- oder Mischkristallschicht bezeichnet. Im Unterschied zur Dicke der Verbindungsschicht, kann die gesamte Nitrierschicht bis in eine Tiefe von einigen Zehntel Millimetern reichen. Der Gehalt an Legierungselementen wirkt sich auf das Wachstum der Diffusionsschicht aus. Mit zunehmendem Legierungsgehalt nimmt unter sonst gleichen Bedingungen die erreichbare Nitriertiefe ab.
Ergänzende Prozessschritte
Je nach Bedarf und Bauteilanforderungen können auf eine plasmanitrierte Oberfläche zusätzliche Schichten aufgebracht werden.
Eine Möglichkeit ist die Oxidation. Hierbei wird eine vor Korrosion schützende Eisenoxidschicht (Magnetit) auf der Verbindungsschicht erzeugt. Die Oxidation findet direkt im Anschluss an das Plasmanitrieren statt. Das Verfahren stellt einen zusätzlichen Schritt vor der Abkühlung der Charge dar und kann innerhalb eines Prozesses angewendet werden ohne die Prozessdauer nennenswert zu verlängern. Daher ist dieses Verfahren in der Praxis sehr kosteneffizient.
Weiterhin lässt sich alternativ auch eine zusätzliche Beschichtung auf eine plasmanitrierte Oberfläche aufbringen. Dies sind beispielsweise Schichten und Schichtkombinationen aus Diamond-like Carbon oder Titannitrid. Voraussetzung ist eine geeignete Wahl der Parameter beim Plasmanitrieren um eine optimale Schichthaftung zu gewährleisten und Delaminationseffekte zu vermeiden. Das Plasmanitrieren und Beschichten lässt sich ebenfalls in einer Anlage als Kombinationsprozess durchführen. Aus wirtschaftlichen Gesichtspunkten können hierbei jedoch nur sehr dünne Nitrierschichten erzeugt werden.
Anlagenaufbau
Ein wichtiges Merkmal einer sogenannten Warmwandanlage ist, dass die Erwärmung des Werkstücks im Wesentlichen durch die Wandheizung und nicht durch das Plasma erfolgt. Hierdurch können die Plasmaprozessparameter unabhängig von der Prozesstemperatur in optimaler Weise angepasst werden. Die Plasmaspannung wird in Form von Rechteckpulsen mit einer Folgefrequenz von bis zu 50 kHz angelegt. Pulse positiver und negativer Polarität sind möglich, was die Abscheidung isolierender Schichten erlaubt. Thermoelemente sorgen für eine akkurate Temperaturmessung und -anpassung. Gemessen wird diese entweder nahe dem oder direkt im Werkstück.
Eigenschaften
Verzüge
Das Nitrieren ist aufgrund der niedrigen Prozesstemperaturen das geeignete Diffusionsverfahren, wenn es um geringen Verzug geht. Die durch die Einlagerung von Stickstoff veränderte Gitterstruktur des Stahls vermindert zusätzlich noch die Gefahr der Adhäsion, die zum Fressen von Gleit- und Wälzpaarungen führt. Das Nitrieren bietet somit gewisse Notlaufeigenschaften.
Aufgrund des geringen Verzuges ist die Nacharbeit die Ausnahme. Das Flächenwachstum beträgt je nach Nitriertiefe 10–25 µm. Dünnwandige Körper oder poröse Materialien wachsen jedoch insgesamt mehr, aber auch reproduzierbar. Durch geeignetes Vorhalten von Maßabweichungen kann hier effektiv gegengesteuert werden.
Umweltaspekt
Das Plasmanitrierverfahren ist aufgrund der Tatsache, dass keine giftigen Gase verwendet werden mitunter eine der umweltfreundlichsten Methoden der Oberflächenhärtung. Vergleicht man sie beispielsweise mit Gasnitrieranlagen, so erzeugen letztere 2.700-mal so viel CO/CO2, und 5.500-mal so viel NOx wie Plasmanitrieranlagen.
Maskierung
Neben dem geringen Verzug und der Umweltfreundlichkeit bietet die Plasmanitriertechnologie außerdem die Möglichkeit, anstelle von Abdeckpasten mechanische Maskierungen zu verwenden. Diese können ganz einfach aufgesetzt und wieder abgenommen werden. Geht es um Spalten, Bohrungen o. Ä., so kann sogar ganz auf sämtliche Abdeckungen verzichtet werden, da man die Nitrierwirkung mittels des Drucks variieren kann. Bei korrekter Einstellung werden die Bohrungen nicht nitriert, um eine Aufhärtung oder Versprödung zu verhindern.
Investitionskosten
In der Regel sind die Investitionskosten von Plasmanitrieranlagen um 20 Prozent bis 30 Prozent höher als die vergleichbarer Gasnitrieranlagen. Aufgrund der niedrigeren Prozesskosten (infolge der Gaszusammenstellung) relativiert sich diese Zahl allerdings schnell.
Materialien und Anwendungsgebiete
Ein breites Spektrum an Materialien kann problemlos im Plasma nitriert werden:
- Einsatzstahl, Vergütungsstahl, Nitrierstahl, Werkzeugstahl
- Austenitische und martensitische hochchromhältige Stähle
- Sintermaterial
- Gusseisen
- Titanlegierungen
Die Plasmanitriertechnologie findet in vielen Branchen Anwendung:
- Getriebeindustrie und deren Kunden wie Motion Control, Windkraft oder Hersteller von Automobilen, LKWs, Traktoren oder Baumaschinen
- Waffenindustrie
- Luftfahrt (z. B. Zentralwelle, Lager usw.)
- Automobilzulieferindustrie (z. B. Sinterbauteile, Wellen, Exzenterwellen, Schlepphebel, Grundwellen, Ventile, Kurbelwelle, Kolben, Gasfedern usw.)
- Hydraulikindustrie (z. B. Zylinder, Kolben usw.)
- Öl- und Gasindustrie (z. B. Offshore Komponenten, Ventile, Verschraubungen usw.)
- Werkzeugbau (z. B. Schmiedeteile, Aluminiumdruckguss- oder Extrusionsformen usw.)
Siehe auch
Quellen
- T. Bell, Y. Sun, A. Suhadi: Environmental and technical aspects of plasma nitrocarburising. In: VACUUM Surface Engineering, Surface Instrumentation & Vacuum Technology. Volume 59, 2000.
- KC. Kramer, A. Mühlbauer: Praxishandbuch Thermoprozess-Technik: Grundlagen – Verfahren. Vulkan, Essen 2002, ISBN 3-8027-2922-6.
- K. Lange: Umformtechnik: Handbuch für Industrie und Wissenschaft. Band 4: Sonderverfahren, Prozeßsimulation, Werkzeugtechnik, Produktion. Springer, Berlin/Heidelberg 1993, ISBN 978-3-540-55939-9.
- D. Liedtke: Wärmebehandlung von Eisenwerkstoffen I: Grundlagen und Anwendungen. 7. Auflage, expert verlag, Renningen 2007.