Ionenimplanter
Ionenimplanter sind Maschinen, die Werkstoffe mit geladenen Teilchen (Ionen) beschießen und diese in ein Substrat einbringen (Ionenimplantation), um die Materialeigenschaften zu ändern.
Aufbau & Funktionsweise
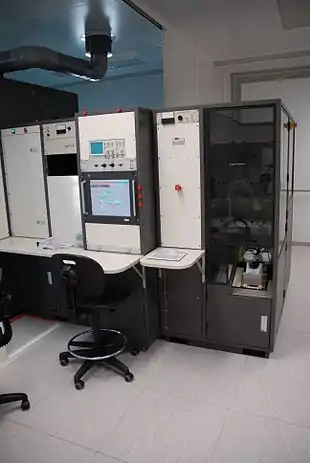
Alle Ionenimplanter bestehen aus einer Ionenquelle, einem Beschleunigungssystem (Ionenbeschleuniger), einer Extraktionsblende, einer Masse- und Energietrennung der Ionen, einem Abtastsystem, sowie einer Kammer zur Bearbeitung der Wafer.
Implantiert wird in Silizium und andere Halbleiter wie z. B. Gallium-Arsenid (GaAs), einem III-V-Verbindungshalbleiter.
In der Ionenquelle wird das Gas ionisiert. Die Ionenquelle besteht dabei aus einem Heizdraht der vom Dotantengas angeströmt wird. Zum Implantieren von Stoffen die als Festkörper vorkommen (z. B. Beryllium) kann in manchen Implantern auch ein sogenannter „Vaporizer“ eingesetzt werden, mit dem feste Dotanten verdampft werden können. Die ionisierten Dotanten werden dann vorbeschleunigt (meist einige 10 kV), bevor der Ionenstrahl den Magnet zur Massen-/Energietrennung erreicht. Nach dem Selektionsmagnet findet eine Nachbeschleunigung mit bis zu einigen Megavolt statt. Der gesamte Prozess findet im Ultrahochvakuum statt, das meist mit Turbomolekularpumpen oder Kryopumpen erzeugt wird.
Als Dotanten dienen Elemente, die als Akzeptoren, wie Bor und Indium, oder Donatoren, wie Phosphor und Arsen, wirken können. Die Beispiele beziehen sich dabei auf Silizium als zu dotierendes Material. Diese Elemente werden oft nicht in ihrer elementaren Form, sondern gebunden in gasförmiger oder fester Form (Pulver) eingesetzt:
- Bor: Bortrifluorid (BF3, gasförmig)
- Phosphor: Phosphin (PH3, gasförmig)
- Arsen: Arsin (AsH3, gasförmig)
- Indium: Indium(III)-chlorid (InCl3, fest)
- Kohlenstoff
- Germanium
Einteilung
Bei der Halbleiterherstellung unterscheidet man folgende Grundtypen von Implantern:[1]
- Mittelstromimplanter mit Implantströmen von 1 µA bis 5 mA bei Energien von 10 keV bis 200 keV
- Hochstromimplanter mit Implantströmen von 100 µA bis 30 mA bei Energien von 80 keV bis 200 keV
- Niedrigenergieimplanter mit Implantströmen von 1 mA bis 20 mA bei Energien von 0,2 keV bis 80 keV
- Hochenergieimplanter mit Implantströmen von 10 µA bis 1 mA bei Energien von 200 keV bis 5 MeV[2] und höher (bis zu 10 MeV[3])
wobei die hier genannten Grenzen nur eine grobe Orientierung darstellen und die Angaben von Literatur zu Literatur schwanken, vgl.[4][5][6] Zudem verfügen moderne kommerziell erhältliche Anlagen über einen nutzbaren Strom- bzw. Energiebereich, der zwei oder drei der zuvor genannten Bereiche überstreicht. Für eine spezifische Anwendung – basierend auf den allgemeinen Anforderung einer gegebenen Energie und Dosis (Ionen pro Fläche) – kommt daher öfter mehr als ein Anlagentyp in Frage. Ausgehend von vergleichbaren Implantationsprofilen bekommen dann auch wirtschaftliche Aspekte einen höheren Stellenwert, so dass ein Prozess mit hoher Dosis (> 5e14 Ionen pro Quadratzentimeter) bevorzugt auf Hochstromimplanter durchgeführt wird, da hier im Vergleich zu Mittelstromimplantern eine deutlich geringe Prozesszeit benötigt wird (näherungsweise lineare Steigerung mit der Abnahme des Ionenstroms).
Weiterhin kann man Implanter nach ihrem Handhabungseinrichtung einteilen:
- Batch-Maschinen (es werden mehrere Wafer gleichzeitig bearbeitet)
- Einzel-Wafer-Maschinen (die Wafer werden nacheinander bearbeitet)
Batch-Maschinen waren lange Zeit der gängige Typ. Dabei werden mehrere Wafer (oft 13) auf einem rotierenden Träger platziert und mir hohen Umdrehungsgeschwindigkeiten (bis zu 1200/min) durch den Ionenstrahl gefahren. Mit der Einführung von 200-mm-Wafern wurden Einzel-Wafer-Maschinen attraktiv, bei denen ein einzelner Wafer auf einem elektrostatischen Träger (engl. chuck) gehalten wird. Neben Prozesskostenersparnissen, ermöglichen Einzel-Wafer-Maschinen durch eine andere Führung durch den Ionenstrahl einen gleichmäßigere Dotierung über die Waferfläche und durch den geringeren Platzbedarf der Einzel-Wafer-Halterung höhere Verkippungen (bis zu 60°) sowie eine bessere Winkelgenauigkeit. Bei der Fertigung auf 300-mm-Wafern kommen fast keine Batch-Anlagen mehr zum Einsatz, da sie zum einen die notwendigen Toleranzanforderungen nur schwer erreichen können und die Anlagen auch schlicht zu groß (und zu teuer, Standfläche in einen Reinraum sind Kosten) wären.[3]
Siehe auch
Einzelnachweise
- Bernd Schmidt, Klaus Wetzig: Ion Beams in Materials Processing and Analysis. Springer, 2012, ISBN 3-211-99355-X, S. 74.
- Axcelis Celebrates Shipment of 300th GSD/HE Series Implanter Marking Over 15 Years. Axcelis Technologies, 22. Juni 2011, abgerufen am 22. Juli 2020 (Pressemeldung).
- Lis K. Nanver, Egbert J. G. Goudena: Ion Implantation. In: Wiley Encyclopedia of Electrical and Electronics Engineering. American Cancer Society, 1999, ISBN 978-0-471-34608-1, doi:10.1002/047134608X.W7021.
- Sami Franssila: Introduction to Microfabrication. John Wiley & Sons, 2010, ISBN 978-1-119-99189-2, S. 177.
- Mel Schwartz: New Materials, Processes, and Methods Technology. CRC Press, 2010, ISBN 978-1-4200-3934-4, S. 647–649.
- Michael Nastasi, James W. Mayer: Ion Implantation and Synthesis of Materials. Springer, 2006, ISBN 978-3-540-45298-0, S. 214.