Holzaufschluss
Als Holzaufschluss wird die mechanische oder chemische Zerlegung von Holz in Holzfasern bezeichnet. Durch mechanische Zerfaserung des Holzes werden Holzstoffe gewonnen, mit chemischen Aufschlussverfahren Zellstoff. Diese Faserstoffe werden von der Papierindustrie zu Papier, Karton und Pappe verarbeitet. In geringerem Maß wird besonders reiner Zellstoff (Chemiezellstoff) von der chemischen Industrie weiterverarbeitet.
Grundlagen
Holz besteht im Wesentlichen aus in Bündeln angeordneten Cellulosefasern, die in einer Matrix aus Ligninmolekülen eingelagert sind. Das Lignin ist als Stützmaterial und verhärtetes Polymer wesentlich für die Druckfestigkeit des Gewebes zuständig, während die eingelagerten Cellulosefasern die Zugfestigkeit gewährleisten. Es handelt sich also um eine Durchdringung von reißfesten, biegsamen Fasern (Cellulose) mit einem dichten und starren Polymer als Füllmaterial (Lignin).[1] Als Analogien sind auch technische Materialien wie Stahlbeton oder naturfaserverstärkte Kunststoffe entsprechend aufgebaut. Außerdem dient Lignin als Schutz gegen Eindringen von Wasser in das Zellwandmaterial und hält dieses somit in den Leitgefäßen (Xylem und Phloem) sowie im Innern der Zellen. Weitere Schutzwirkung besteht gegenüber UV-Licht sowie mechanischer Beschädigung und dem Eindringen von Schädlingen. Schließlich kann Lignin nur schwer von Bakterien bzw. Pilzen abgebaut werden und hemmt infolgedessen das Wachstum pathogener Mikroorganismen.[2]
Für die Nutzung von Cellulose als Zellstoff in der Papier- und Zellstoffindustrie muss die Ligninmatrix aufgelöst und die Cellulose entsprechend freigelegt werden. Dieser Auslösung des Zellstoffs dienen die chemischen Holzaufschlussverfahren.
Mechanischer Holzaufschluss
Bei mechanischem Aufschluss werden Holzschliff und andere Holzstoffe für sogenanntes holzhaltiges Papier erzeugt. Dabei wird unterschieden, ob die einzelnen Holzfasern aus dem Rundholz oder aus Hackschnitzeln herausgelöst werden.
Schliff-Verfahren
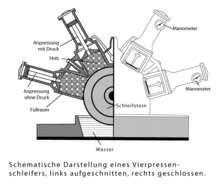
Mit dem Schliff-Verfahren werden Holzstoffe hergestellt, die unmittelbar aus dem Rundholz gewonnen werden. Dies erfolgt mit Hilfe eines rotierenden Schleifsteins, welches die Fasern schrittweise vom Holz ablöst. Dabei wird unterschieden, ob bei Normaldruck oder bei Überdruck geschliffen wurde. Ersteres wird als Stein-Holzschliff (stone groundwood pulp) bezeichnet, letzteres als Druckschliff (pressure groundwood pulp).
Die Vorgänge beim Aufschluss der Holzfasern aus dem Rundholz lassen sich in drei Teile klassifizieren, wobei sich die einzelnen Einflüsse überschneiden. Zuerst kommt es zur Erweichung der Mittellamelle. Dies liegt an den hohen Temperaturen, die durch die starken Druckwechselbeanspruchungen entstehen, welche beim Schleifvorgang auf das Holz wirken. Weil nicht nur ein einzelner Stamm zurzeit geschliffen wird, sondern sich stets mehrere Rundholzstämme in der Nähe des Schleifsteins befinden, kann die durch die Reibung entstehende Wärme nicht entweichen, weswegen sie sich einige Millimeter über der Schleifzone staut. Das führt zur Plastifizierung des Lignins und der Hemicellulosen bereits vor dem Kontakt mit dem Schleifstein. Jedoch ist die Erweichungstemperatur abhängig vom Wassergehalt des Holzes. Je höher der Wassergehalt des Holzes ist, desto niedriger ist Plastifizierungstemperatur. Während trockenes Lignin zwischen 135 °C und 235 °C erweicht, plastifiziert es bei einem Wassergehalt im Bereich von 30 bis 40 % bereits zwischen 90 °C und 100 °C. Hemicellulosen erweichen bei einem Wasseranteil in dieser Höhe bereits bei 85 °C, statt bei 167 °C bis 217 °C als trockenes Substrat. Anschließend kommt es zur Abtrennung der Fasern. Die vom Schleifstein verursachten Druckwechselbeanspruchungen führen zunächst zur Verformung des Faserverbandes und schließlich zum Bruch der Bindungen zwischen und innerhalb der Fasern. Die entstandenen Verformungen erleichtern die Wasseraufnahme des Lignins, was wiederum die weitere Fibrillierung der herausgelösten Fasern begünstigt. Abschließend kommt es zum Herauslösen der Fasern. Je nachdem wie scharf die Oberfläche des Schleifsteins ist, führt ein stark geschärfter Stein zu einer ritzenden oder schneidenden Wirkung auf die Fasern. Ist der Schleifstein eher stumpf, übt er eine fibrillierende beziehungsweise quetschende Wirkung auf das Ausgangsmaterial aus.[3]
Die maßgebende Eigenschaft für die Oberflächenstruktur der Holzfasern ist bei dem Stein-Verfahren die Holzfeuchtigkeit. Eine höhere Holzfeuchte führt zu einem Faserstoff mit besseren Festigkeitseigenschaften, niedrigerem Entwässerungswiderstand, höherem Weißgrad und einem größeren Anteil an Faserlangstoff bei hochwertigerem Feinstoff. Der Feuchteanteil sollte nicht unter 33 Prozent liegen, da eine Fasersättigung des Holzes gewährleistet sein muss. Dieser stellt sich, je nach Holzart, zwischen 28 und 32 Prozent ein. Jedoch bringt ein Feuchteanteil von 50 bis 60 Prozent die besten Eigenschaften mit sich. Des Weiteren können bessere Ergebnisse beim Schleifen unter Überdruck erzielt werden. Das lässt sich damit erklären, dass bei einem erhöhten Druck die Sättigungstemperatur des Wassers sinkt, weshalb mit höheren Temperaturen in der Schleifzone gearbeitet werden kann. Außerdem kann kein Wasser aus dem System entweichen, weil bei Druckschleifern die gesamte Schleifzone dicht verschlossen ist. Somit kann die gesamte Wassermenge für die Plastifizierung von Lignin und den Hemicellulosen verwendet werden. Auf diese Weise können Faserstoffe mit besseren Eigenschaften als beim Steinschliff unter Normaldruck erzielt werden.[3]
Ein weiterer wichtiger Parameter stellt die Zunahme des Schleifdrucks dar, welche durch Erhöhung des Holzvorschubs erreicht wird. Das ergibt einen Groundwood-Faserstoff mit einer besseren Entwässerbarkeit, jedoch führt dies ebenfalls zur schlechteren Festigkeitseigenschaften. Weiterhin hat die Steinumfangsgeschwindigkeit auch eine signifikante Bedeutung für die Faserstoffeigenschaften. So führt eine Erhöhung der Geschwindigkeit zu einem kurzfaserigen und nur schwer entwässerbaren Faserstoff. Üblicherweise werden zur Steigerung der Produktivität in der Praxis die Erhöhung des Holzvorschubs und die Steinumfangsgeschwindigkeit in Kombination angehoben.[3]
Die Schleifzonentemperatur ist eine weitere Eigenschaft, die Auswirkungen auf den Faserstoff hat. Allerdings ist diese in der Praxis nur schwierig zu ermitteln. Deshalb werden, um den Wert abschätzen zu können, die Temperatur des Trogstoffes, des Spritzwassers und die Temperaturverhältnisse am Schleifzonenaustritt ermittelt. Normalerweise wird bei Trogtemperaturen zwischen 60 °C und 75 °C produziert, da dies zu einem festen und langfaserigen Holzstoff führt, welcher sich gut entwässern lässt. Des Weiteren ist das Profil des Schleifsteins für das Produkt relevant. Während durch das Schärfen Einfluss auf die Makrostruktur des Steins genommen werden kann, entsteht die Mikrostruktur des Steins durch das Kornmaterial Steins. Welchen Einfluss die Struktur des Schleifsteins auf das Rundholz hat, wird mit Hilfe des spezifischen Schleifarbeitsbedarfs ermittelt. Er dient sowohl zur Beschreibung des Energiebedarfs und der Qualität des Groundwood-Faserstoffs, als auch zur Prozessregelung und Kontrolle. Herkömmlicherweise wird mit 90 bis 150 kWh/100 kg gearbeitet. Ein hoher spezifischer Schleifarbeitsbedarf ergibt einen feineren und festeren Holzstoff. Das folgende Diagramm demonstriert seinen Einfluss auf die Festigkeitseigenschaften des Faserstoffs.[3]
Refiner-Verfahren
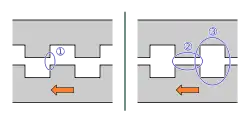
➀ Kante gegen Kante
➁ Fläche gegen Fläche
➂ Messerzelle gegen Messerzelle
Mit dem Refiner-Verfahren werden Holzstoffe aus Hackschnitzeln hergestellt. Je nach Vorbehandlung wird zwischen TMP- (thermo-mechanical pulp) und CTMP-Faserstoffen (chemo-thermo-mechanical pulp) unterschieden. Während TMP-Faserstoffe nur thermisch vorbehandelt werden, werden CTMP-Faserstoffe für den Aufschluss auch mit Chemikalien vorbehandelt. Dabei wird für Nadelhölzer bevorzugt Natriumsulfit verwendet, für Laubhölzer hingegen Natriumhydroxid.[4]
Der Aufschluss der Holzfasern im Refiner-Verfahren geschieht ebenso durch die Plastifizierung des Lignins. Dies erfolgt sowohl durch mechanische und thermische Beanspruchung während des Schleifprozesses, als auch durch chemische Vorbehandlung bei CTMP-Faserstoffen. Die Beschaffung des entstandenen Faserstoffes hängt dabei von mehreren Faktoren ab. Wie beim Stein-Verfahren hat die Defibrierungstemperatur eine wesentliche Bedeutung. Damit das Lignin erweicht, wird im Refiner eine Temperatur zwischen 120 °C und 135 °C benötigt. Diese sollte auch möglichst eingehalten werden, da nur so ein großer Teil der Fasern unbeschädigt aus dem Faserverband herausgelöst werden kann. Bereits eine leichte Überschreitung hat negative Auswirkungen auf die Qualität des Faserstoffs. Liegt die Defibrierungsstemperatur bei 140 °C, führt das zu einem sehr groben Produkt. Darüber hinaus verfestigt sich das erweichte Lignin nach dem Abkühlen auf der Faseroberfläche, was zu einem harten Faserstoff führt, welcher für die Papierherstellung gänzlich untauglich ist. Wird hingegen beim Zerfasern die Erweichungstemperatur nicht erreicht, ergibt das einen ebenso groben Faserstoff mit nur geringem Festigkeitsvermögen.[3] Nach Wenderdel und Krug kommt es bei einer Temperatur von über 170 °C sogar zur Ligninkondensation, wodurch der entstandene Faserstoff ebenfalls für die Produktion von Papier untauglich ist.[5]
Außerdem hat der Mahlscheibenabstand Auswirkungen auf die Fasermorphologie. Dieser lässt sich jedoch nur schwer steuern aufgrund der sich ändernden Druck- und Temperaturverhältnisse während des Schleifens, weshalb eine häufige Nachjustierung notwendig ist. Denn durch einen geringeren Mahlscheibenabstand wirken stärkere physikalische Kräfte auf die Hackschnitzel, wodurch die Fasern eher aus dem Faserverbund herausgebrochen, anstatt fibrilliert zu werden.[5]
TMP- und CTMP-Faserstoffe unterscheiden sich hinsichtlich ihrer Beschaffenheit in einigen Merkmalen. Im Wesentlichen liegt der Unterschied in der mittleren Faserlänge der beiden Holzstoffe. CTMP-Faserstoffe haben einen höheren Langfasergehalt und einen geringeren Feinstoffanteil, was durch die chemische Vorbehandlung bedingt ist. Dabei wird, je nach Holzart, nur Natriumsulfit oder eine Mischung aus Natronlauge und Natriumsulfit verwendet. Dieser Vorgang wird als Sulfonierung bezeichnet. Er bewirkt, dass sich die Fasern an der Mittellamelle leicht trennen lassen, da der Schwefel in Wechselwirkung mit dem dort hauptsächlich vorhandenen Lignin tritt. Des Weiteren werden so die Holzfasern leichter zugänglich für Wassermoleküle. Als Reaktionsprodukt entsteht Ligninsulfonsäure, welche bei der Papierherstellung weniger störend ist als das Lignin. Darüber hinaus sind chemisch vorbehandelte Faserstoffe flexibler und bindungsfreudiger als nur thermisch vorbehandelte.[6]
Chemischer Holzaufschluss
Dominierende Verfahren
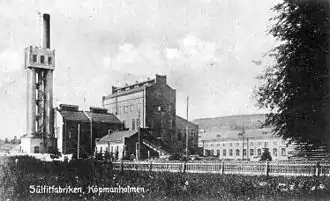
Zur Gewinnung von Zellstoff wird das Holz chemisch aufgeschlossen. Die Papierindustrie verwendet vor allem folgende Verfahren:
- Sulfatverfahren
- Sulfitverfahren
- Sodaverfahren
Bei der Produktion von Zellstoff für die Papierherstellung findet aktuell (2009) hauptsächlich das Sulfatverfahren Verwendung. Rund 85 Prozent des in Deutschland verbrauchten Zellstoffs werden im Sulfatverfahren gewonnen, im Jahr 2008 waren dies 3,7 Millionen Tonnen Sulfatzellstoff.[7] Das Sulfitverfahren wird für lediglich ca. 15 Prozent bzw. 723.000 Tonnen des in Deutschland verbrauchten Zellstoffs angewendet.[7] Weltweit stammen etwa 80 Prozent des Zellstoffs aus Anlagen mit einem konventionellen oder modifizierten Sulfatverfahren während nur etwa 6 Prozent aus dem Sulfitverfahren stammen (vor allem Chemiezellstoff). Die restlichen etwa 14 Prozent werden über das Sodaverfahren oder andere Aufschlussprozesse vor allem aus einjährigen Nutzpflanzen (Bambus u. ä.) hergestellt.[8]
Alternative Verfahren
Eine Reihe weiterer Aufschlussverfahren sind darauf ausgerichtet, das bindende Lignin mit Hilfe von Lösungsmitteln, Säuren oder Enzymen aus dem Holz zu entfernen und damit den Zellstoff auszulösen. Zu diesen Verfahren zählen folgende:[9]
- Acetocell-Verfahren: Aufschluß mit Essigsäure bei hohem Druck und hoher Temperatur[10]
- Acetosolv-Verfahren: Aufschluss mit Essigsäure und einem geringen Anteil an Salzsäure[10]
- ASAM-Verfahren (ASAM = Alkali-Sulfit, Anthrachinon, Methanol): Aufschluss mit Natriumsulfit und Methanol
- Formacell-Verfahren: Aufschluss mit Essigsäure und Ameisensäure[10]
- Milox-Verfahren (Milox = „Milieu“ und „oxidativ“): Aufschluss mit Perameisensäure (hergestellt aus Ameisensäure und Wasserstoffperoxid)[10]
- Organocell-Verfahren: Aufschluss mit Ethanol und Natronlauge
- Organosolv-Verfahren: enzymatischer Aufschluss
Belege
- Sekundärwände von Faser- und Holzzellen. In: Peter Sitte, Elmar Weiler, Joachim W. Kadereit, Andreas Bresinsky, Christian Körner: Strasburger – Lehrbuch der Botanik für Hochschulen. 35. Auflage. Spektrum Akademischer Verlag, Heidelberg 2002, ISBN 3-8274-1010-X. S. 95–96.
- Hans W. Heldt und Birgit Piechulla: Pflanzenbiochemie. 4. Auflage. Spektrum Akademischer Verlag, 2008, ISBN 978-3-8274-1961-3, S. 420–422.
- Blechschmidt. 2010, S. 67–79.
- Blechschmidt. 2010, S. 84.
- Wenderdel et al. 2012, S. 88.
- Roffael 1994. S. 243–244.
- Verband deutscher Papierfabriken e.V.: Papierkompass 2009 ([https://de.wikipedia.org/w/index.php?title=Wikipedia:Defekte_Weblinks&dwl=http://www.vdp-online.de/pdf/Kompassdeutsch(1).pdf Seite nicht mehr abrufbar], Suche in Webarchiven: [http://timetravel.mementoweb.org/list/2010/http://www.vdp-online.de/pdf/Kompassdeutsch(1).pdf PDF] (Seite nicht mehr abrufbar, Suche in Webarchiven) Info: Der Link wurde automatisch als defekt markiert. Bitte prüfe den Link gemäß Anleitung und entferne dann diesen Hinweis. ).
- Akonen et al. 1997; S. 34.
- E. Gruber: Alternative Aufschlussverfahren, Baustein 14 aus dem Vorlesungsskriptum „Grundlagen der Zellstofftechnologie“ im Lehrgang „Papiertechnik“ an der Berufsakademie Karlsruhe, Stand 2011 (PDF). Mit Detailangaben zu den einzelnen Verfahren.
- Patentanmeldung DE19962411A1: Verfahren zur Gewinnung/Rückgewinnung von Carbonsäuren aus Ablaugen der Zellstoffherstellung. Angemeldet am 22. Dezember 1999, veröffentlicht am 5. Juli 2001, Anmelder: Natural Pulping AG (Angaben zum damaligen Stand der Technik unter Beschreibung, Seite 1 Zeile 11 ff).
Literatur
- Aki Ahonen, Ludwig Lehner: Umweltverträgliche Holzaufschlußverfahren. Wissenschaftliche Studie zum Thema „Umsetzung der neu entwickelten umweltverträglichen Holzaufschlußverfahren“. Landwirtschaftsverlag, Münster 1997, ISBN 3-7843-2877-6 (Schriftenreihe nachwachsende Rohstoffe 8).
- J. Blechschmidt: Taschenbuch der Papiertechnik. Carl Hanser Verlag, München 2010.
- E. Roffael, B. Dix, G. Bär, R. Bayer: Über die Eignung von thermo-mechanischem und chemo-thermo-mechanischem Holzstoff (TMP und CTMP) aus Buchen- und Kiefernholz für die Herstellung von mitteldichten Faserplatten (MDF). In: Holz als Roh- und Werkstoff. Band 52, Nr. 4, 1994, S. 239–246, doi:10.1007/BF02619102.
- C. Wenderdel, D. Krug: Untersuchung zum Einfluss der Aufschlussbedingungen auf die morphologische Ausprägung von aus Kiefernholz hergestelltem TMP-Faserstoff. In: European Journal of Wood and Wood Products. Band 70, Nr. 1–3, 2012, S. 85–89, doi:10.1007/s00107-010-0487-x.