Druckplattenmessung
Die Druckplattenmessung ist ein Prüfverfahren zur Qualitätssicherung in der filmlosen Druckvorstufe des Offsetdruckverfahrens. Nach anfänglichen Behelfsmethoden wird dieses Prüfverfahren heute mit der elektrooptischen Methode der digitalen Bildanalyse realisiert.
.jpg.webp)
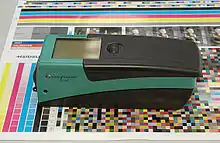
Analysiert werden die auf eine Druckplatte belichteten und entwickelten Druckraster unter dem Aspekt des Tonwertverhaltens im Auflagendruck. Als Resultat werden Kennlinien erstellt, die den kompletten Ist-Umfang des Rastertonwerts von 0 % bis 100 % darstellen. Zweck der Kennlinien ist die Kalibrierung des Druckplattenbelichters über die mit ihm konfigurierte RIP-Software, um Druckergebnisse mit einer jederzeit wiederholbaren Qualität zu erzielen. Diese Kalibrierung trägt zu standardisierten Bedingungen in der Druckvorstufe bei und ist somit eine der Voraussetzungen für ein erfolgreiches Anwenden des Colormanagement im Rahmen der Umsetzung der ISO 12647-2 bzw. des Prozessstandard Offsetdruck.
Verfahrensgeschichte
Solange transparente Kopiervorlagenfilme zum fotomechanischen Übertragen der Text- und Bildinformationen, also der Farbauszüge auf die Druckplatte verwendet wurden, genügten Durchlicht-Densitometer, um die Tonwerte zu bestimmen. Der Wegfall der Filmkopie bei der Umstellung der Druckindustrie auf Computer to Plate in den 1990er Jahren erforderte plötzlich neue Messmethoden. In Ermangelung geeigneter Messprinzipien und -geräte wurden hierfür zunächst Auflicht-Densitometer verwendet. Der bisweilen zu geringe Hell-Dunkel-Kontrast auf den verschieden eingefärbten Druckplattentypen war jedoch der Grund, dass die Densitometer nicht hinreichend zuverlässige Messergebnisse liefern konnten.
Als Alternative zur densitometrischen Integralmessung der Graustufen auf der Druckplatte kam nur die Bildanalyse in Frage, genauer gesagt das automatische Vermessen der geometrischen Form der Rasterelemente. Erst Ende 1998 gelang es, die ursprünglich sehr aufwändige Labormessmethode der planimetrischen Auswertung von Videobildern in Handmessgeräten zu implementieren. Dieser Erfolg war an Bildsensoren gebunden, die erst mit der aufstrebenden Digitalkamera-Technik verfügbar wurden.
Die Geräteklasse der ersten Generation wurde als Dotmeter (Centurfax ccDot) oder Plate Reader (ACME) bezeichnet, weil sie den „dot“ (Rasterpunkt) auf der Druckplatte „messen“ bzw. „lesen“ konnten. Sie wiesen aber noch das Manko auf, lediglich mit einem Graustufen-Bildsensor zu arbeiten, wodurch sie zumindest in puncto Hell-Dunkel-Kontrast sogar einem Farbdensitometer unterlegen waren. Dieses Problem löste schon Anfang 2000 das Techkon Digital Microscope DMS 910[1] unter Verwendung eines CCD-Matrixsensors, wie er in Farbvideokameras zu finden ist.
Die zweite Gerätegeneration ab Mitte der 2010er Jahre zeichnet sich durch zwei entscheidende Verbesserungen aus, die zu einer höheren Messgenauigkeit des Verfahrens führten.
- An Stelle einer Glühlampe, die im blauen und grünen Spektralbereich weniger zur Kontrastbildung beiträgt als im roten Bereich, werden zur Probenbeleuchtung nunmehr Leuchtdioden eingesetzt. Die verwendeten LEDs strahlen besonders breitbandig ab, das heißt, es entsteht ein so kontinuierlich wie möglich spektralverteiltes Weißlicht, indem ein weißes Mischlicht möglichst ohne Lücken zwischen den spektralen Komponenten Rot, Grün und Blau erzeugt wird. Nur so lassen sich die Hell-Dunkel-Kontraste aller Plattenfärbungen verlässlich abbilden.
- Mit dem weiteren Fortschritt in der Digitalkameratechnik werden Matrixsensoren verfügbar, die eine deutlich höhere optische Auflösung des Digitalkameramoduls erlauben, ohne dass dafür höhere Bauteilkosten anfallen, würde man hierfür noch immer CCDs verwenden. Es handelt sich um den in der CMOS-Technologie gefertigten Active Pixel Sensor. Neben der gewachsenen Auslesegeschwindigkeit steht er heute auch in seiner breiten spektralen Empfindlichkeit dem CCD nicht mehr nach und ist daher allen Kontrastproblemen gewachsen. Darüber hinaus ist er weniger als das CCD für Blooming anfällig – ein unerwünschtes Überstrahlen, das gerade beim Messen auf den metallischen Druckplatten-Oberflächen durch Reflexion gelegentlich entstehen kann, obwohl die Geometrie der Messoptik glanzfrei (45° zwischen Lichtquelle und Probe sowie 0° zwischen Probe und Sensor) aufgebaut ist.
Darüber hinaus erfolgt die Datenübertragung zu einem angeschlossenen PC heute nicht mehr über eine serielle Schnittstelle, sondern über USB. Dies hat zwar keinen Einfluss auf Messgenauigkeit noch Analysegeschwindigkeit, erleichtert aber die heute allgemein erwartete automatische Geräteerkennung.
Auch in der zweiten Gerätegeneration ist der deutsche Hersteller Techkon mit dem SpectroPlate der einzige Anbieter, der zur Bildanalyse ein Farbkameramodul einsetzt. Der amerikanische Hersteller X-Rite nutzt eine Farbkamera lediglich zur Echtzeitanzeige beim Positionieren des Geräts, während der Sensor der Graustufenkamera gegebenenfalls durch einfärbungsbezogene Look-up-Tabellen für kontrastarm erscheinende Druckplattenfabrikate unterstützt werden muss. Unabhängig davon sind solche Lookup-Tabellen sinnvoll, wenn auf so genannten chemiefreien Druckplatten gemessen werden muss; weil diese Platten keinem chemischen Entwicklungsprozess und somit auch keiner Einfärbung unterzogen werden, stellt sich das zu messende Sujet extrem kontrastarm, nahe einem fotografischen Latenzbildes, dar.
In einem Ausnahmefall haben Auflicht-Densitometer trotzdem nach wie vor ihre Berechtigung bei der Druckplattenmessung, weshalb sogar einige Fabrikate der nachgefolgten Geräteklasse der Spektraldensitometer diese Funktion unterstützen. Dieser Ausnahmefall besteht im Messen auf Druckplatten, deren Trägermaterial aus Polyester oder gar Papier besteht und die deshalb als preisgünstige Alternative zu Aluminiumdruckplatten zur Anwendung kommen – natürlich nur im mittleren Qualitätssegment und in kleineren Druckmaschinenformaten. Die gute densitometrische Messbarkeit begründet sich in der fotografischen Schwärzung der Silberhalogenid-Kopierschicht, mit der die Druckfolien verfahrensbedingt ausgestattet sind, denn schwarze Raster auf weißem Grund kommen dem hohen Kontrastbedarf des Densitometers entgegen. In diesem Fall muss der Drucker nicht zusätzlich ein Druckplattenmessgerät erwerben.
Verfahrensbeschreibung
Systemkomponenten
Ein System für die Druckplattenmessung umfasst immer ein Druckplattenmessgerät und eine PC-Software für die Kennlinien-Berechnung. Nur über die Software ist eine Weitergabe der Kennlinien an den RIP möglich. In der Praxis sind die Kennlinien-Software, die RIP-Software und das Job-Management der Plattenbebilderungsanlage (Belichter) oft auf ein und demselben Rechner installiert; zumindest aber muss eine Vernetzung vorhanden sein. Die Kennlinienwerte werden in geeigneter Weise als Korrekturwerte für die Bebilderung der einzelnen Tonwertstufen auf die Druckplatte verarbeitet.
Das eigentliche Druckplattenmessgerät besteht aus folgenden grundlegenden physischen Komponenten:
- einem Gehäuse, das auch mit nur einer Hand sicher positioniert werden kann und das ergonomisch einfach, etwa mit einer großen Auslösetaste, bedienbar ist;
- einem auf der Gehäuseoberseite angebrachten grafikfähigen Display, das 1. mit dem Live-Vorschaubild als Positionierhilfe, 2. als Anzeige für das Funktionsmenü, die ausgewählten Funktionen und Einstellungen, 3. als Anzeige für das analysierte Bild und die Messwerte dient;
- einem Prozessormodul, das die Gerätefunktionen in Verbindung mit der installierten Grafikdisplay-Bedienoberfläche und der Bildanalyse-Software sicherstellt;
- einer glanzfreien Probenbeleuchtung, die in Abstimmung auf die spektrale Empfindlichkeit des Bildsensors einen hohen Hell-Dunkel-Kontrast erzeugt;
- einer hochwertigen, hochauflösenden Mikroskop-Optik, die einen zweckgebunden optimalen Vergrößerungsmaßstab bietet;
- einem Videokamera-Bildsensor, der 1. das Live-Vorschaubild liefert, 2. bei Auslösen der Messtaste die augenblicklichen Hell-Dunkel-Informationen, die von der Optik projiziert werden, „einfriert“ und zur sofortigen Bildanalyse an den Prozessor weitergibt;
- einem Speicher, der die Analysebilder übernimmt und zusammen mit den errechneten geometrischen Werten („Messwerten“) speichert;
- einem USB-Anschluss für die Datenübertragung an den PC;
- einem Akkumulator, der das Gerät mit Gleichstrom versorgt;
- einer Abstellkonsole, die mit Hilfe eines elektrischen Netzanschlusses den Akkumulator des Messgeräts wiederauflädt.
Herstellerabhängig sind bei den Komponenten Unterschiede festzustellen. So verwendet ein amerikanischer Anbieter zwei separate Bildsensoren: einen Farbbildsensor als Positionierhilfe und einen Graustufenbildsensor für die Messung. Ein deutscher Hersteller ermöglicht zusätzlich die Verwendung des Geräts als Digitalmikroskop, wobei die eingefrorenen Farbbilder unter Umgehen der Bildanalyse als hochaufgelöste Digitalfotos zu einem weiteren Bildspeicher weitergegeben werden.
Vervollständigt wird das Druckplattenmessgerät durch zwei virtuelle Komponenten:
- die Firmware, die alle Bedien-, Speicher- und Hintergrundfunktionen sicherstellt;
- die Bildanalyse-Software, die das eingefrorene Kamerabild in eine Grauwertematrix umsetzt.
Die PC-Software, die auf das Messgerät zugreifen kann, verfügt in der Regel über folgende Funktionen:
- bidirektionaler Datenaustausch mit dem Messgerät – 1. zum Messgerät hin: Installation, Freischaltung, Update und Upgrade der Firmware und Bildanalysefunktionen; 2. vom Messgerät her: Import der Vorschaubilder und der Messdaten;
- Darstellung der Messwerte als Tabelle oder grafisch als Kennlinien-Diagramm;
- Verwaltung der Tabellen und Kennlinien im Bezug auf individuelle „Jobdaten“ (Produktions- und Materialkenngrößen, Druckplattentyp und -charge, Datum, RIP, Belichter und Zieldruckmaschine gemäß Kompensationsanforderungen);
- Tabellenexport, um die Daten in einem Standardformat (beispielsweise in Microsoft Excel oder unformatiertem Text) an die RIP-Software zu übergeben.
Handhabung des Messgeräts
An das Bebildern der Druckplatte mit UV-, sichtbarer oder IR-Strahlung schließt sich bei den meisten Plattenfabrikaten ein chemischer Entwicklungsprozess an, wozu auch das dunkle Einfärben der später druckenden Plattenpartien gehört. Auf diese Weise wird zwischen den druckenden und nicht druckenden Plattenpartien – in den meisten Fällen sind das die stehengebliebenen Schichtanteile und das freigelegte Aluminiumoxid – ein genügend hoher Hell-Dunkel-Kontrast erzeugt, der das Messen ermöglicht. Gemessen wird an einem geeigneten Bildobjekt, meist einem Tonwertstufenkeil, dessen Rastertonwerte vom digitalen Datenbestand her bekannt sind (siehe Abschnitt Anwendung).
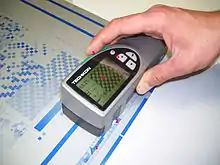
Das Platzieren des Messgeräts auf der Druckplatte erfolgt mittels einer visuellen Positionierhilfe, und zwar
- (an Geräten der ersten Generation) in Form einer gut einsehbaren Lochblende,
- mit Hilfe des grafikfähigen Flüssigkristall-Displays auf der Geräteoberseite (aktuelle Generation), wo das bewegte Aufnahmebild des integrierten Videokameramoduls in Echtzeit anzeigt wird,
- alternativ über einen PC-Monitor, wenn das Messgerät an einen PC angeschlossen ist, wo in einem Software-Fenster dasselbe Vorschaubild in Echtzeit anzeigt wird (erste und aktuelle Generation).
Sobald das Messgerät auf der gewünschten Messstelle platziert worden ist, kann die Messung gestartet werden. Das Auslösen der Messfunktion erfolgt entweder durch Bedienen einer Taste am Gerätegehäuse oder durch einen Mausklick in der Bedienoberfläche der PC-Software. Je nach Hersteller dauert der Messvorgang zwischen einer und drei Sekunden. Danach kann das Messgerät zur nachfolgenden Messstelle, beispielsweise zum benachbarten Feld eines Tonwertstufenkeils, verschoben werden.
Anwender erwarten von modernen Plattenmessgeräten, dass sie auch autark eingesetzt werden können; das bedeutet, dass alle Messwerte zwischengespeichert und erst nach dem Anschließen des Geräts an einen PC aus dem Speicher ausgelesen werden. So ergonomisch angenehm diese Arbeitsweise auch sein mag, weil während der Messung kein Verbindungskabel zum PC stört, so umständlich und fehleranfällig ist sie zugleich. Denn das Zuordnen der Messreihen eines Plattensatzes (Druckplatten für die vier Prozessdruckfarben und gegebenenfalls Sonderfarben) zu den jeweiligen „Jobdaten“ lässt sich am PC-Monitor mit Hilfe einer übersichtlichen Software einfach verwechslungsfrei durchführen, sodass eventuelle Wiederholungen einzelner Messreihen vermieden werden können. Insofern ist eine Messung, bei der das Gerät mit der PC-Software online ist, immer sicherer und zeitsparend.
Kontrast- und Schwellenwert-Definition
Der Hell-Dunkel-Kontrast zwischen den nicht druckenden und den druckenden Plattenpartien ist nicht diskret. Das bedeutet, dass die Hell-Dunkel-Übergänge – also die Kanten der belichteten und entwickelten Raster-, Strich- und Schriftelemente – mehr oder weniger allmählich ausgebildet sind. Je weniger allmählich, also je steiler der Übergang von der Schichtoberfläche zur freigelegten Aluminiumoxid-Oberfläche, umso schärfer wird das jeweilige Element auf der Druckplatte dargestellt. Genau diese möglichst kantenscharfe Wiedergabe wird bei der Plattenbebilderung angestrebt, was die verschiedenen Bebilderungstechnologien aber nicht in einheitlich hoher Qualität vermögen.
Die Kantenschärfe wird beeinflusst
- von der Wellenlänge des Laserstrahls und somit seinem Brechungsverhalten in optischen Systemen, also seiner Fokussierbarkeit;
- von der Entfernung des Laser-Moduls von der Druckplattenoberfläche – je nach Belichterbauweise „Innentrommel“, „Außentrommel“ oder „Flachbett“ im Millimeter- oder Dezimeterbereich –, wodurch der Einfluss der Fokussierqualität des Laserstrahls mehr oder weniger groß ist;
- im Zusammenhang mit der Wellenlänge von der darauf spektral abgestimmten Empfindlichkeit der Plattenkopierschicht und somit von der Fähigkeit des Schichtmaterials, nach Abschluss der Prozesse des Bebilderns, der fotochemischen Entwicklung und der physikalischen Konditionierung möglichst steile Kantenübergänge ausbilden zu können;
- von der Rauheit des freigelegten Aluminiumoxids, dessen mikroporöse Oberfläche den Schichtrand mehr oder weniger stark verlaufen lässt.
Die Beleuchtung der Plattenoberfläche unter einem Winkel von 45° verursacht bei einer Auflichtmessung unter einem Winkel von 0° die Bildung von Schatten an größeren Unebenheiten – vor allem im Aluminiumoxid, also in den nicht druckenden Bereichen. Dadurch werden vom Messgerät zusätzlich zu den druckenden, dunkel eingefärbten Schichtpartien auch die dunklen Schatten in den Mikroporen wahrgenommen. Unabhängig davon können Staub, Kratzer und andere Störfaktoren störende Schatten werfen.
Deshalb muss an das Messgerät die technische Forderung gestellt werden, dass es bei der Bildanalyse die Intensität der Schatten vom Grauwert der eingefärbten Schicht unterscheidet. Diese Fehlerunterdrückung muss dazu führen, dass ausschließlich die Schichtpartien als druckende Elemente erkannt werden, d. h., dass alle störenden Grauwerte nicht in der Grauwertematrix abgebildet werden. Technisch wird diese Forderung gelöst, indem das Messgerät automatisch eine Kontrastgrenze setzt, die als Schwellenwert bezeichnet wird. Dieser Schwellenwert ist diejenige Helligkeitsstufe, bei der alle Grauwerte im Analysebild diskret unterschieden werden: Alle helleren Grauwerte werden in Weißsignale umgewandelt, alle dunklere Graustufen in Schwarzsignale.
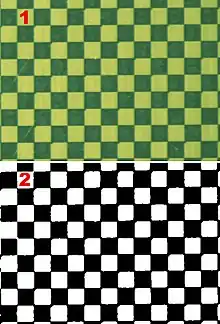
Bei kontrastschwachen oder kritischen Plattenfärbungen wird die Software beim Finden des richtigen Schwellenwerts durch die oben erwähnten Lookup-Tabellen (LUTs) unterstützt, in denen das Helligkeitsniveau, auf dem in „Weiß“ und „Schwarz“ unterschieden werden soll, zahlenmäßig vorgegeben wird. Farbsensoren, die LUTs eigentlich nicht brauchen, geben zusätzliche Sicherheit und spielen ihre Stärke vor allem dann aus, wenn an chemikalienfrei zu entwickelnden Druckplatten mit Minimalkontrast gemessen werden muss.
Geometrische Bildanalyse
Nachdem in der vorbereiteten Grauwertematrix nunmehr nur noch schwarze (druckende) und weiße (nichtdruckende) Bildpunkte vorliegen, kann der nächste Analyseschritt abgearbeitet werden. So werden die Koordinaten jedes einzelnen schwarzen und weißen Bildpunktes benutzt, um aus sämtlichen Schwarz-Weiß-Übergängen den Verlauf von Kanten bis hin zu geometrischen Figuren – die von den Kanten eingeschlossenen Flächen – zu erkennen:
- positive Rasterelemente zwischen 0- und 50-prozentigem Tonwert bzw. negative Rasterelemente zwischen 50- und 100-prozentigem Tonwert sowie umgekehrt
- positive Rasterelemente zwischen 50- und 100-prozentigem Tonwert bzw. negative Rasterelemente zwischen 0- und 50-prozentigem Tonwert.
Sollten dunkle Objekte, die nicht am Druckprozess beteiligt sind – also Schatten, Flecken oder Kratzer –, als vermeintlich druckendes Element schwarz dargestellt werden, sollte die Bildanalyse-Software in der Lage sein, diese Objekte als Fehler zu erkennen und sie nicht in die weitere Analyse einfließen zu lassen. Solche Fehler lassen sich durchaus nach bestimmten mathematischen Kriterien automatisch erkennen, nämlich wenn das jeweilige Objekt
- die Homogenität einer weißen Fläche stört, und zwar ab einem definierten, auf jeden Fall sehr hohen Weiß-Prozentwert (umgekehrt gilt dies auch für die Homogenität schwarzer Flächen, wenn darin weiße Kratzer auftauchen);
- die durchschnittliche Größe benachbarter Rasterelemente deutlich unterschreitet;
- eine Kontur aufweist, die sowohl für periodische als auch für nichtperiodische Rasterelementformen untypisch ist.
Aus der korrigierten Konturen- und Flächenstruktur erkennt die Software die gewünschten geometrischen Rasterkenngrößen. Daneben lässt sich nun auch die wichtigste Kenngröße berechnen: der Flächendeckungsgrad. Er kann gleichgesetzt werden mit dem früher densitometrisch gemessenen Rastertonwert. Während in einem Densitometer die Lichtstromverhältnisse analysiert werden, wird bei der Bildanalyse das Verfahren der digitalen Planimetrierung herangezogen.
Anwendung
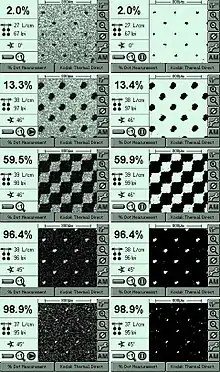
Rasterkenngrößen
Die geometrische Analyse identifiziert
- das Rasterungsmodell, d. h. das Modulationsverfahren, also
- einen amplitudenmodulierten Raster (AM), auch periodischer oder autotypischer Raster genannt, dessen Elemente regelmäßig geformt sind und deren Mittelpunkte in gleichen Abständen und in einer Vorzugsrichtung verteilt sind;
- einen frequenzmodulierten Raster (FM), auch nichtperiodischer oder stochastischer Raster genannt, dessen Elemente unregelmäßig geformt sind und deren Mittelpunkte in ungleichen Abständen und ohne Vorzugsrichtung zufällig verteilt sind (wobei sich 1. und 2. Generation der FM-Raster unterscheiden, dass der Einfluss des Zufallsgenerators reduziert wurde, um eventuell störend wirkende Bildpunkt- und Elementhäufungen gezielt zu vermeiden);
- einen „crossmodulierten“ Raster (XM), auch Hybridraster genannt, weil er Merkmale sowohl des AM- als auch FM-Rasters aufweist;
- die geometrischen Wege, d. h. die Abstände von Kanten zu Kanten sowie Höhen, Breiten und Durchmesser von Rasterelementen, also
- die Rasterweite bei AM- und XM-Rastern,
- die Rasterelementgrößen bei FM- und XM-Rastern;
- die Vorzugsrichtung der Rasterelemente in AM- und XM-Rastern, d. h. der Rasterwinkel, der für den betreffenden Farbauszug im RIP generiert wurde.
Der Flächendeckungsgrad F, d. h. der druckende Flächenanteil auf der gemessenen Druckplatte, wird planimetrisch ermittelt, indem die gedeckte Fläche (schwarz) mit 100 Prozent multipliziert und ins Verhältnis zur Summe zur Gesamtfläche – den gedeckten (schwarzen, S) plus ungedeckten (weißen, W) Flächenanteilen – gesetzt wird. Hierfür müssen die schwarzen Bildpunkte (S) gezählt werden; die Gesamtfläche (S+W) ist von vornherein bekannt, da sie der insgesamt vorhandenen Bildpunktezahl des Matrixsensors entspricht.
Kennlinien der Tonwertübertragung
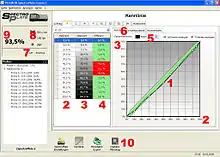
Einzelmesswerte haben hinsichtlich des Ziels der Druckplattenmessung keine Bedeutung. Das Verhalten des Plattenbebilderungssystems über die gesamte Tonwertskala von 0 bis 100 % kann nur eine Kennlinie beschreiben. Zwei Arten von Kennlinien sind zu unterscheiden:
- die „Übertragungskennlinie“ – gemessene Istwerte (y-Achse) über den Sollwerten (x-Achse);
- die „Tonwertzuwachskennlinie“ – Soll-Ist-Differenzwerte (y-Achse) über den Sollwerten (x-Achse).
Die Wertetripel (Sollwert; Istwert; Soll-Ist-Differenzwert) werden an die RIP-Software übergeben und dort in geeigneter Weise verarbeitet, um eine der beiden Kennlinienarten zu implementieren. Dies bewirkt ganz pauschal ein lineares Ausgabeverhalten (Istwerte = Sollwert) des Belichters, indem das charakteristische Tonwertübertragungsverhalten des Belichters (Sollwerte + Differenzwerte) korrigiert wird.
Letztendlich ist es das Ziel, standardisierte und jederzeit reproduzierbare Bedingungen in der Druckplattenbebilderung sicherzustellen. Das ist die Voraussetzung dafür, dass die Tonwertzuwachswerte, die
- im Rahmen des ProzessStandard Offsetdruck als „Charakterisierungsdaten für den standardisierten Druck“[2] für die verschiedenen Offsetdruckszenarien („Produktionsbedingungen“) vorgegeben werden
- oder die sich im Betrieb bewährt haben,
zuverlässig angewendet werden können. Sie ergänzen das Farbmanagement, indem bei der Ausgabe der Farbauszugdateien die Farbwiedergabeeigenschaften der Prozesskette (in Form von ICC-Profilen) unter Verwendung der Charakterisierungsdaten automatisch auf ein identisches Tonwertübertragungsverhalten des Plattenbelichters gebaut werden kann. Auf Grund der heute üblichen Berücksichtigung von Tonwertzuwachsdaten im ICC-Profil wäre es kontraproduktiv, zusätzlich zur Linearisierung eine Korrekturkurve für den typischen Tonwertzuwachs des Offsetdruckverfahrens in die RIP-Software zu übernehmen. Bis zur Einführung standardisierter Charakterisierungsdaten ins Farbmanagement war das Darüberlegen einer Tonwertzuwachs-Korrekturkurve über die Linearisierungskurve eine oft praktizierte Option gewesen.
Diese Prozessreproduzierbarkeit kann also nur durch regelmäßig durchgeführte Druckplattenmessungen gewährleistet werden. Um die Messreihen auf der Druckplatte aufnehmen zu können, bedarf es geeigneter Kontrollmittel.[3] , der neben zahlreichen Prüfelementen auch einen Graustufenkeil bietet. Dieser Keil besteht aus Rastertonwert-Messfeldern, die in den Sollwerten 0 (total rasterfrei), 1 %, 2 %, 3 %, 5 %, 10 %, 20 %, 30 %, 40 %, 50 %, 60 %, 70 %, 80 %, 90 %, 95 %, 97 %, 98 %, 99 % und 100 % („Vollton“) auf die Platte bebildert werden. Jedes dieser Felder wird nacheinander mit dem Plattenmessgerät erfasst. Resultat ist eine Kennlinie. Für die nötige statistische Sicherheit sorgen Software-Funktionen, die aus mehreren Messreihen eine aus Mittelwerten aufgebaute Kennlinie liefern können.
Digitale Mikrofotografie
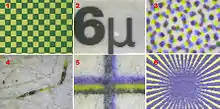
Da es sich bei den eingesetzten Sensoren um Matrixsensoren aus der Digitalkameratechnik handelt, lag es für einen deutschen Hersteller von Plattenmessgeräten und Spektraldensitometern nahe, als Zusatznutzen des Druckplattenmessgeräts die Kamerafunktion zu implementieren. In Verbindung mit der Mikroskopoptik liefert das Gerät digitale Mikroskopaufnahmen. Diese Möglichkeit lässt sich in vielen Qualitätssicherungsaufgaben in der Druckerei nutzen:
- Beurteilen des Auflösungsvermögens von Druckplatten und Bebilderungssystemen;
- Prüfen der Passerqualität an gedruckten Rastern;
- Beurteilen der Homogenität von Papieroberflächen im Rahmen der Materialeingangsprüfung.
Die Bilder können als Belege zusammen mit den Prüfprotokolldaten archiviert werden und bieten der Druckerei bei Reklamationsfällen eine spezielle Beweissicherheit.
Heutige gerätetechnische Lösungen
Im Hauptanwendungsgebiet werden Plattenmessgeräte heute als Handgeräte für Einzelmessungen angeboten. Meistens angeschlossen an einen PC wird das Gerät zum Aufnehmen einer Kennlinie an die Stelle der Offsetdruckplatte aufgesetzt, wo der Rasterstufenkeil aufbebildert worden ist. Jedes Messfeld wird einzeln gemessen, indem das Gerät unter Sichtkontrolle positioniert und der eigentliche Messvorgang per Knopfdruck am Gerät oder per Mausklick in der PC-Bedienoberfläche ausgelöst wird.
Einen anderen Zweck verfolgt die Einbindung eines Plattenmesskopfes in hoch automatisierte Linien für die Druckplattenbebilderung: die permanente Prozess- und Qualitätskontrolle. Auf die Druckplatte werden mehrere nebeneinander angeordnete Testelemente (Targets) bebildert. Anhand eines eingefrorenen Kamerabildes, das auf kurze Distanz aufgenommen worden ist, werden Kontrast, Vollständigkeit der Details, Auflösung und Verzerrungsfreiheit geprüft. Auf eine Bildanalyse nach obiger Beschreibung wird verzichtet, weil manche Probleme nur durch feinere Grauwertabstufungen im Videobild erkennbar sind. Eine andere Bildanalyse wird aber trotzdem durchgeführt: Das Ist-Bild wird mit einem Soll-Bild verglichen. So gibt diese Art der Analyse Aufschluss über die korrekte Ausführung aller Funktionen bei der Laser-Bebilderung und der chemischen Entwicklung. Aus Abweichungen von einem Referenzbild wird ersichtlich, ob Laserdioden ausgefallen sind oder die Konzentration der Entwicklerchemikalien sinkt. Dann gibt das System Alarm und markiert auf einem Monitor die erkannte Abweichung.[4][5]
Implementierung von Branchenstandards
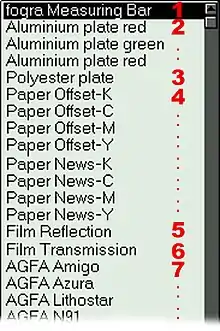
Die Fogra Measuring Bar [FMB] ist eine mit Rasterstufenkeilen exakt bebilderte Musterdruckplatte. Sie gilt als anerkanntes Vergleichsnormal für die Druckplattenmesstechnik. Die Keile sind in AM- wie auch FM-Rasterung aufbereitet worden. Bei einer Messung der Keilfelder mit einem Plattenmessgerät müssen ganz bestimmte Flächendeckungsgrade angezeigt werden. Diese Referenzwerte wurden bei der Fogra Forschungsgesellschaft Druck e.V. in München mit einem Labormessgerät exakt ermittelt und in einem beiliegenden Protokoll festgehalten.[6] Die Fogra ihrerseits belegt den Referenzstatus des Labormessgeräts durch Vergleichsmessungen, durchgeführt bei der Bundesanstalt für Materialforschung und -prüfung in Berlin.
Auf dem deutschen Markt erhältliche Druckplattenmessgeräte der letzten Generation sind intern auf die FMB-Referenzwerte kalibrierbar, indem eine spezielle Lookup-Tabelle hinzugefügt wird. Diese Kalibrierung ist dauerhaft im Gerät gespeichert; zeitraubende Nachkalibrierungen sind nicht erforderlich. Bei der ersten Inbetriebnahme der Messgeräte ist lediglich eine Weißkalibration auf einem mitgelieferten Weißstandard durchzuführen; damit ist das Gerät messbereit. Mit diesem Aktivieren der FMB-Referenz werden alle Messungen miteinander vergleichbar – unabhängig vom Messgerätetyp.
Lösungen für andere Druckverfahren
Druckformen werden heute auch in anderen Druckverfahren filmlos hergestellt. Somit besteht dort ebenso die Notwendigkeit, auf der Druckform zu messen. Doch anders als beim Offsetdruck, bei dem druckende und nichtdruckende Elemente in einer Ebene liegen, weisen die Druckformen der anderen Druckverfahren dreidimensionale Elemente auf:
- erhabene Druckelemente (Relief) im Flexodruck;
- tiefliegende Strukturen (Zellen) im Tiefdruck – sowie ferner auf Rasterwalzen im Flexodruck, in Lackiermodulen und Kurzfarbwerken des wasserlosen Offsetdrucks;
- durchlässige Gewebe (Schablonen) im Siebdruck.
Messgeräte, die zu einer 3D-Bildanalyse in der Lage sind, basieren heute auf Messmikroskopen. Neben dem Vermessen der zweidimensionalen Strukturen werden mit Hilfe der Fokussierung die Relief- und Zelltiefen „ausgelotet“. (Messungen im Siebdruck sind nicht notwendig, weil die Struktur mit dem ausgewählten Siebgewebe unbeeinflussbar vorgegeben ist.) Die Messungen können ziemlich fehlerbehaftet sein, weil subjektive Einstellungen vorgenommen werden müssen. So kann das kalottenförmige Profil von Tiefdrucknäpfchen nur sehr schwer auf die interessanteste Kenngröße, das Druckfarben-Entleerungsverhalten, hin bewertet werden. Und transparente Flexodruckplatten irritieren das Messgerät zusätzlich durch Lichtbeugungserscheinungen an steilen Kanten und durch fehlende Anhaltspunkte für das Scharfstellen des Bildes.
Einzelnachweise
- DMS910 Digital MicroScope Fills Calibration Needs Of Latest Platesetters, abgerufen am 18. Januar 2016.
- Forschungsgesellschaft Druck e.V.: Charakterisierungsdaten für den standardisierten Druck, abgerufen am 18. Januar 2016.
- Forschungsgesellschaft Druck e.V.: Fogra-Digital-Plattenkeil, abgerufen am 18. Januar 2016.
- Ifra Special Report 2.32: Automatisierte Prozesskontrolle der CTP-Produktion. Eine Machbarkeitsstudie (PDF; 598 kB), abgerufen am 18. Januar 2016.
- NELA PQM+: Vollautomatische Druckplatten-Qualitätsmessung (Seite nicht mehr abrufbar, Suche in Webarchiven) Info: Der Link wurde automatisch als defekt markiert. Bitte prüfe den Link gemäß Anleitung und entferne dann diesen Hinweis. , abgerufen am 18. Januar 2016.
- Forschungsgesellschaft Druck e.V.: Fogra Measuring Bar [FMB], abgerufen am 18. Januar 2016.