Wirbelschicht
Der Begriff Wirbelschicht (auch Wirbelbett genannt, englisch fluidized bed) stammt aus dem Bereich der thermischen und mechanischen Verfahrenstechnik. Wirbelschicht wird eine Schüttung von Feststoffpartikeln genannt, welche durch eine aufwärtsgerichtete Strömung eines Fluids in einen fluidisierten Zustand versetzt wird. Der Begriff „fluidisiert“ weist in diesem Zusammenhang darauf hin, dass die (ehemalige) Schüttung nun Fluid-ähnliche Eigenschaften aufweist. In einigen Berechnungsmodellen wird dies als grundlegender Ansatz herangezogen. Da es sich bei einer Wirbelschicht um ein Fluid-Feststoff-Gemisch handelt, kann dieser Ansatz trotz zumeist guter Ergebnisse nicht alle Phänomene beschreiben.
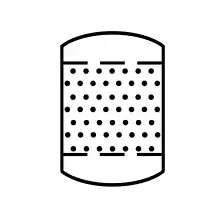
Wirbelschichtverfahren haben eine herausragende Bedeutung in Wirbelschichttrocknern bei der Trocknung granularer Medien, bei Feuerungen von Kohle, Ersatzbrennstoffen oder Klärschlamm, bei der Fluid-Catalytic-Cracking-Kraftstoffherstellung oder auch der Kaffee-Röstung.
Geschichte
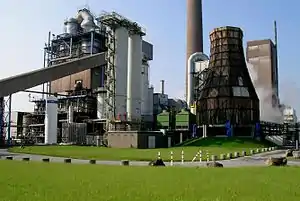
Im Rahmen der Optimierung des Haber-Bosch-Verfahrens entwickelte der deutsche Chemiker Fritz Winkler bei BASF die erste Wirbelschichtvergasung zur Herstellung von Synthesegas aus feinkörniger Braunkohle im Winkler-Generator,[1] wofür er 1922 ein Patent erhielt.[2] 1926 wurde die erste großtechnische Anlage in Betrieb genommen.[3] 1929 gingen vier weitere Anlagen in Betrieb. Durch die Anwendung der Wirbelschicht in den Vereinigten Staaten für das katalytische Cracken von Mineralölen in den 1940er Jahren erfolgten rasch umfangreiche theoretische und experimentelle Untersuchungen des Fließbettes. In den 1960er Jahren wurde im damaligen VAW-Lippewerk in Lünen das erste Kraftwerk mit zirkulierender Wirbelschicht zur Verbrennung ballastreicher Steinkohlen gebaut, später für die Kalzinierung von Aluminiumhydroxid. Inzwischen werden Wirbelschichtanlagen für viele verschiedene Zwecke benutzt.
Eigenschaften von Wirbelschichten
Eine Wirbelschicht weist flüssigkeitsähnliche Eigenschaften auf. So bildet sich, wie bei Wasser, stets eine horizontale Oberfläche aus. Werden in zwei miteinander verbundenen Behältern Wirbelschichten erzeugt, so stellt sich in beiden die gleiche absolute Höhe der Wirbelbettobergrenze ein (Prinzip der kommunizierenden Röhren). Weiterhin sinken in einem Wirbelbett Objekte mit höherer Dichte als das Bett ab, während Objekte mit geringerer Dichte schwimmen (Archimedisches Prinzip). Da sich die ‚Dichte‘ (eigentlich der Feststoffvolumenanteil im Gemisch) des Wirbelbettes mit der Fluidisierungsgeschwindigkeit ändert, können Objekte mit ähnlicher Dichte wie das Wirbelbett durch Änderung der Fluidisierungsgeschwindigkeit zum Absinken bzw. Wiederauftauchen gebracht werden.
In Wirbelschichten kommt es zu einem engen Kontakt des Wirbelgutes (Feststoffpartikel) mit dem Wirbelmedium (Fluid: Gas oder Flüssigkeit) und zu lebhaften Platzwechseln der einzelnen Partikel nach allen Richtungen. Dies führt in Wirbelschichtfeuerungen zu einem guten Wärmetransport innerhalb der Anlage und zu einem guten Wärmeübergang zwischen Wirbelschicht und der Behälterwand bzw. eingebauten Wärmetauschern. Gleichzeitig sorgen der gute Wärmetransport und die (im Vergleich zu Gas) enorm hohe Wärmekapazität des Bettinventars für ein relativ homogenes Temperaturfeld in der Anlage, was eine schadstoffarme Verbrennung zur Folge hat. Charakteristisch für die Beurteilung des Fluidisierungszustandes von Wirbelschichten ist der Verlauf des Feststoffvolumenprofils, das sich aus dem (scheinbaren) Druckverlust über der Anlagenhöhe berechnen lässt.
Arten von Wirbelschichten
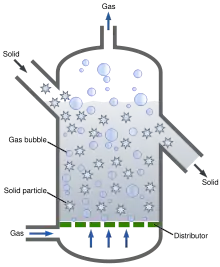
Man unterscheidet zwischen homogenen Wirbelschichten mit einer räumlich gleichmäßigen Verteilung der dispersen Phase und inhomogenen Wirbelschichten, die eine räumlich ungleichmäßige Verteilung der dispersen Phase aufweist. Daneben gibt es stationäre oder blasenbildenden Wirbelschichte (BWS), bei denen die fluidisierte Schüttung eine deutliche Grenze besitzt, aus der nur sehr wenige (feine) Partikel ausgetragen werden und zirkulierende Wirbelschichten (ZWS), bei der die fluidisierte Schüttung auf Grund einer größeren Strömungsgeschwindigkeit des Fluids keine deutliche obere Grenze mehr besitzt und Partikel in großem Maße nach oben ausgetragen werden. Diese fallen dann in Form von Clustern wieder in das Wirbelbett zurück oder werden in den Gaszyklon ausgetragen, dort vom Gasstrom getrennt und über eine Rückführung wieder der Bodenzone zugeführt, also (re-)zirkuliert.
Wirbelschichtzustände
Homogene Wirbelschicht
Bei der homogenen Wirbelschicht ist der Feststoff (grobdisperse Phase) gleichmäßig verteilt, und es erfolgt bei Erhöhung der Fluidgeschwindigkeit eine kontinuierliche Expansion. Homogene Wirbelschichten stellen sich bei feinkörnigen, engverteilten und nichtkohäsiven Stoffsystemen mit geringer Dichtedifferenz und bei Flüssigkeits-Wirbelschichten ein.
Inhomogene Wirbelschicht
Inhomogene Wirbelschichten treten vor allem bei Gas-Feststoff-Wirbelschichten und bei breiter Partikelgrößenverteilung bzw. großen Dichteunterschieden auf. Dies gilt auch für große und/oder kohäsive Partikel. Zu den Erscheinungsformen von inhomogenen Wirbelschichten werden unter anderem gezählt:[4][5]
- blasenbildende Wirbelschichten
- gassenbildende Wirbelschichten
- stoßende Wirbelschichten
Blasenbildende Wirbelschicht
Eine Wirbelschicht kann verschiedene Zustände annehmen. Geht man zunächst von einem Festbett aus, das von einem Fluid- oder Gasstrom durchströmt wird, und erhöht man diesen fortwährend, so wird der Feststoff ab dem sogenannten Lockerungspunkt, dem Punkt der minimalen Fluidisierung, durch den Strom getragen (Zustand A). Die dazu korrespondierende Fluidisierungsgeschwindigkeit wird im Allgemeinen mit bezeichnet. Erhöht man den Gasstrom weiterhin, so kommt es zu einer Blasenbildung in der Wirbelschicht (Zustand B), die jetzt auch als blasenbildende oder stationäre Wirbelschicht bezeichnet wird.
In einem relativ großen Bereich von Gasgeschwindigkeiten verändert sich dieser Zustand nicht wesentlich. Abhängig von der Partikelform, deren Größe, Scheindichte etc., behält die Wirbelschicht (bis z. B. fünf bis sechsmal ) ihren blasenbildenden Charakter. Mit zunehmender Gasgeschwindigkeit nimmt der Blasenanteil zu, wodurch der Suspensionsvolumenanteil geringer wird. In der Regel findet man in blasenbildenden Wirbelschichten Feststoffvolumenanteile von ca. 20 % bis 40 %.
Die Gasgeschwindigkeit in diesem Zustand ist jedoch deutlich geringer als die Einzelkorn-Sinkgeschwindigkeit der Partikel. Bildlich kann von einem Schwarmverhalten der Partikel gesprochen werden. Einige Partikel ‚reihen sich nebeneinander auf‘, so dass deren Strömungswiderstand () deutlich höher ist als der Strömungswiderstand des Einzelpartikels. Gleichzeitig kommt es zu einem ‚Windschattenfahren‘ darüber liegender Partikel, so dass diese nicht dem vollen Gasstrom ausgesetzt sind und schneller ‚nach unten fallen‘. Das Ergebnis ist eine kompakte Suspensionsschicht mit deutlich definierter Oberfläche, die durch an der Oberfläche zerplatzende Blasen aufgewühlt wird.
Die blasenbildende Wirbelschicht ist charakterisiert durch intensive Durchmischung in vertikaler Richtung. Je nach Querschnittsfläche des Bettes bilden sich großräumige Zirkulationsströmungen aus. Im Allgemeinen steigt Feststoff im Zentrum der Wirbelschicht auf, der an den Rändern wieder absinkt. Bei sehr großen Querschnittsflächen bilden sich mehrere Auf- und Abstiegszonen aus. Dieser Effekt kann durch speziell angeordnete Gasverteilerböden noch verstärkt werden, um z. B. die Brennstoffeinmischung in die Bodenzone bei Wirbelschichtfeuerungen zu verbessern.
Bei relativ groben Bettmaterial und engen Rohrquerschnitten kann es zu einer „schlagenden“ Wirbelschicht kommen, da sich in solchen Betten die Blasengröße über den gesamten Querschnitt erstreckt (Zustand C). Wird die Fluidisierungsgeschwindigkeit erhöht, kommt es bei einigen Prozessen zunehmend zu einem Austrag von Feinmaterial, dass z. B. durch interne Gaszyklon dem Bett zurückgeführt wird. (Zustand D).
Zirkulierende Wirbelschicht
Ein weiterhin anwachsender Fluidstrom führt zu einem vermehrten Austrag zunächst feinerer Partikel aus der Wirbelschicht (Zustand E). Zur Rückführung dieser Partikel wird (bei Gasen als Fluid) in der Regel ein Aerozyklon zur Feststoffabscheidung mit einer Rückführleitung installiert. Dieser trennt vom Gasstrom den ausgetragenen Feststoff ab, der dann in die Bodenzone der sich jetzt ausbildenden zirkulierenden Wirbelschicht zurückbefördert wird. Im Gegensatz zum Zustand D ist die zu bewältigende Gas- und Feststoffmenge so groß, dass der Zyklon nicht mehr in der Brennkammer bzw. im Steigrohr (je nach Prozessanwendung) der Anlage integriert werden kann und außen installiert werden muss.
Die Vorteile in der technischen Anwendung der zirkulierenden Wirbelschicht gegenüber der blasenbildenden Wirbelschicht besteht in der deutlich höheren Gasgeschwindigkeit, die bei Verbrennungsprozessen größere Brennstoffzugaben erlaubt. Bei katalytischen Prozessen, z. B. ‚Fluid-Catalytic-Cracken‘ (FCC), kann der ausgetragene Katalysator ohne mechanische Installationen vom sog. Cracker in den Regenerator überführt werden.
Die Nachteile der zirkulierenden Wirbelschicht gegenüber der blasenbildenden Wirbelschicht bestehen in dem höheren apparativen Aufwand (führt zu höheren Erstellungskosten) sowie dem höheren Energieaufwand für die Gebläse (führt zu höheren Betriebskosten).
Die Entscheidung, welche Wirbelschicht(-feuerung) zum Einsatz kommen soll, richtet sich also nach der Größe des zu bewältigenden Eduktstroms. Kleine (Feuerungs-)Anlagen werden häufig als blasenbildende, größere Anlagen als zirkulierende Wirbelschicht ausgeführt.
Zirkulierende Wirbelschichten weisen ebenfalls eine dichte Bodenzone aus, die in der Regel jedoch keine deutliche obere Grenze mehr besitzt. Durch den hohen Fluidstrom werden relativ viele Partikel aus der Bodenzone ausgetragen und (bei Verbrennungsanlagen) zum Teil dem angeschlossenen Gaszyklon zugeführt. Ein gewisser Anteil des Feststoffes fällt jedoch noch in der Wirbelschicht wieder in die Bodenzone zurück. Im sogenannten ‚Freiraum‘ (englisch freeboard) oberhalb der dichten Zone bildet sich ein Strömungsbild aus, das als Kern-Ring-Struktur (englisch core-annulus) bezeichnet wird. Im relativ breiten Kern steigt der Feststoff als dünne Suspension auf, während sich direkt am Rand der Anlage (im industriellen Maßstab bei einer Anlagenhöhe von 30 m bis ca. 30 bis 50 cm Entfernung von der Behälterwand) der Feststoff in Clustern mit hoher Geschwindigkeit nach unten bewegt.
Über die Höhe der Anlage bildet sich ein Profil der Feststoffvolumenkonzentration aus, dessen Maximum sich in der Regel an der ‚Obergrenze‘ der dichten Zone befindet und dessen Minimum am Kopf der Anlage zu finden ist. Der Feststoffvolumenanteil im Freiraum hat im Mittel bei modernen Verbrennungsanlagen weniger als 1 %. Cracker weisen dort deutlich höhere Feststoffvolumenanteile auf.
Geldart-Gruppen
Ihrem unterschiedlichen Fluidisationsverhalten entsprechend hat Derek Geldart Schüttgüter für Gas/Feststoff-Wirbelschichten in die vier sogenannten „Geldart-Gruppen“ unterteilt. Diese sind in einem doppellogarithmischen Diagramm von Dichtedifferenz (Fluid - Feststoff) über Partikelgröße aufgetragen.[6]
- Gruppe A
- Die Partikelgröße liegt zwischen ca. 20…100 μm, die Partikeldichte unter ca. 1400 kg/m³. Bevor Blasenbildung entsteht, expandiert die Schicht bis zum zwei- bis dreifachen der Schichtdicke am Lockerungspunkt. Zu dieser Gruppe zählen die meisten pulverförmigen Katalysatoren.
- Gruppe B
- Die Partikelgröße liegt zwischen ca. 40…500 μm, die Partikeldichte bei ca. 1400…4500 kg/m³. Blasenbildung setzt direkt nach Überschreitung des Lockerungspunktes ein.
- Gruppe C
- Hier handelt es sich um äußerst kleine und damit sehr kohäsive Partikel mit einer Größe unter 20…30 μm. Aufgrund der starken Kohäsionskräfte lassen sich diese Partikel nur sehr schwer (z. B. unter Zuhilfenahme von mechanischen Rührern) fluidisieren.
- Gruppe D
- Die Partikelgröße liegt hier bei über 600 μm bei sehr hohen Partikeldichten. Zur Vermischung wird ein sehr großer Volumenstrom benötigt, was wiederum Abriebgefahr birgt.
Modell
Wird ein Festbett von einem Fluid durchströmt, steigt der Druckverlust etwa proportional mit der Strömungsgeschwindigkeit. Am Wirbelpunkt () wird das Bettmaterial vom Gasstrom getragen. Der Druckverlust bleibt dann konstant.
Am Boden der Anlage ist der (scheinbare) Druckverlust multipliziert mit der Querschnittsfläche des Wirbelbettes gleich der Gewichtskraft des Feststoffinventars (abzüglich des Auftriebs des Feststoffes im Fluid).
Zur Abschätzung des Fluidisierungszustandes eignet sich das von Lothar Reh entwickelte Reh-Diagramm.[7]
Anwendung
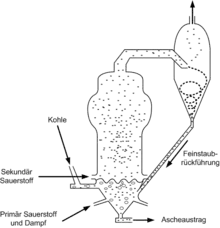
Wirbelschichtanlagen werden in technischen Prozessen genutzt, um Feststoffe mit Gasen, Flüssigkeiten oder anderen Feststoffen in engen Kontakt zu bringen. In der Wirbelschicht werden unter anderem die folgenden charakteristische Grundeigenschaften der Verfahrenstechnik und der chemischen Reaktionstechnik ausgenutzt:
- hohe Relativgeschwindigkeiten zwischen den kontinuierlichen Fluiden und der dispersen festen Phase,
- häufiger Partikel-Partikel-Stoß und Partikel-Wand-Stoß
- intensive Vermischung der Partikel
Wirbelschichtanlagen werden für eine Vielzahl von technischen Prozessen eingesetzt. An dieser Stelle sollen die wichtigsten kurz genannt werden:
- Trocknungsprozesse
- chemische Reaktionen und im Bereich der Energieumwandlung für Vergasungs- und Verbrennungsprozesse
- Klassierung heterogener Schüttungen
In letzter Zeit findet der Wirbelschichtreaktor immer mehr Anwendung in der Kraftwerkstechnik, wo er zu Wirkungsgradverbesserungen beiträgt. Auch Vorgänge wie die Pulverbeschichtung können so durchgeführt werden.
Anwendungsbeispiele
Kraftwerke mit Wirbelschichtfeuerung
- ZWS-Kraftwerk Gardanne, Frankreich, 250 MWel
- Klärschlammverbrennung im Klärwerk Berlin-Ruhleben.
- Thermische Ersatzbrennstoff-Verwertungsanlage (TEV), Neumünster
- ZWS-Biomassekraftwerk Lünen von Remondis-Lippewerk für Ersatzbrennstoffe
- ZWS-Kraftwerk Berlin-Moabit Steinkohle und Braunkohle 83 MWel 136 MWtherm
- Stadtwerke Flensburg GmbH, drei ZWS-Kessel für Steinkohle, Ersatzbrennstoff (EBS) und Holzhackschnitzel
- ZWS-Kraftwerk Berrenrath, RWE Power, Braunkohle mit Klärschlamm und EBS, 2 × 230 MWtherm
- ZWS-Fabrik Frechen – Kraftwerk, RWE Power, Braunkohle mit Klärschlamm 2 × 165 MWtherm
- HKW Merkenich, ZWS-Kraftwerk Wirbelschichtbraunkohle, 240 MWtherm, RheinEnergie, Köln
Kraftwerke mit Wirbelschichtvergasung
- Biomassevergasung im Biomasse-Kraftwerk Güssing, Österreich
Trocknung
- Wirbelschichtrockner mit interner Abwärmenutzung (WTA) der RWE Power AG, z. B. im Kraftwerk Niederaußem
- Druckaufgeladene Wirbelschichtverdampfungstrocknung (WVT, DDWT) mit überhitztem Wasserdampf-Trocknung von Zuckerrübenschnitzeln, NaWaRo (CSD) oder grubenfeuchten Braunkohlen (Versuchsanlagen an der Brandenburgischen Technischen Universität, Cottbus und im Industriepark Schwarze Pumpe)
Bei der Eisenherstellung
- FIOR-Verfahren (stationäre Wirbelschicht; einzige Anlage derzeit außer Betrieb) (Stand 2000)[8]
- FINMET-Verfahren[9] (stationäre Wirbelschicht; Anlagen mit einer Kapazität von 500.000 Jahrestonnen in Betrieb (Stand Mitte 2013))
- Circored- und Circofer-Verfahren (zirkulierende Wirbelschicht; einzige Anlage derzeit außer Betrieb)[10]
Andere Einsatzverfahren
- Wirbelschichttrocknung und -granulation in der Chemie- oder Pharmaindustrie
- Wirbelschicht-Röstung von sulfidischen Erzen (Zink, Pyrit, Kupfer)
- Wirbelschicht-Röstung von Kaffeebohnen
- Wirbelschicht-Kalzination von Gips
- Wirbelschicht-Kalzination von Aluminiumhydroxid[11]
- Abbeize-Regeneration (aus dem metallischen Beizprozess stammend, mit Eisen beladene Salzsäure wird wieder in reine Salzsäure umgewandelt)[12]
Weblinks
- Grundlagen zur zirkulierenden Wirbelschicht (Kaltmodell). (Memento vom 28. September 2007 im Internet Archive; PDF; 958 kB)
Einzelnachweise
- Chemietechnik, Nov. 2013, aufgerufen am 11. Dezember 2013.
- Patent DE437970: Verfahren zum Herstellen von Wassergas. Angemeldet am 28. September 1922, veröffentlicht am 2. Dezember 1926, Anmelder: IG Farbenindustrie AG, Erfinder: Fritz Winkler.
- C. Crowe: Multiphase Handbook. S. 5–71
- M. Stieß: Mechanische Verfahrenstechnik 2. Springer Verlag, 1995, Kapitel 11: Wirbelschichten und pneumatische Förderung.
- H. Schubert: Handbuch der Mechanischen Verfahrenstechnik. Band 1. Wiley Verlag, Weinheim 2003, Kapitel 3.2.2: Wirbelschichten.
- D. Geldart: Types of gas fluidization. In: Powder Technology. Band 7, Nr. 5, Mai 1973, S. 285–292, doi:10.1016/0032-5910(73)80037-3 (asia.edu.tw [PDF]).
- Vertiefung: Bestimmung des Wirbelpunkts durch dimensionslose Kennzahlen
- Developments in the Venezuelan DRI Industry (PDF) S. 5
- What is Finmet Process (Technology) of Ironmaking? (Memento vom 2. April 2015 im Internet Archive)
- Direct Reduction Technologies. (PDF) Outotec
- Alumina Solutions (PDF) Outotec
- Fließbett oder Sprührost: Fortschritte in der Entwicklung von Salzsäure-Regenerationsanlagen