Räumwerkzeug
Ein Räumwerkzeug ist ein Zerspanungswerkzeug zum Räumen und wird auf Räummaschinen genutzt. Die länglichen Werkzeuge haben mehrere hintereinanderliegende Schneiden, die jeweils um die Spanungsdicke größer werden. Der Zahnvorschub ist demnach im Werkzeug integriert; eine Vorschubbewegung gibt es nicht. Das Werkzeug wird beim Innenräumen durch eine bereits vorhandene Bohrung gezogen oder beim Außenräumen außen an ihm entlanggeführt. Als Schneidstoff (Werkzeugmaterial) wird fast immer Schnellarbeitsstahl genutzt. Die Werkzeuge bestehen aus einem Schaft, einem Schneidenteil in der Mitte und dem Endstück sowie Führungen zur Zentrierung. Das Räumen ist sehr wirtschaftlich und produktiv, eignet sich jedoch wegen der hohen Werkzeugkosten[1] nur für größere Stückzahlen.
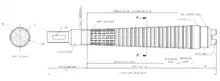
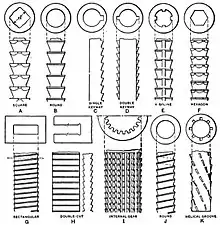
Bauarten
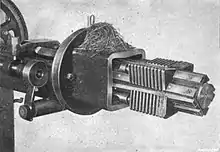
Es gibt verschiedene Bauarten von Räumwerkzeugen. Am häufigsten werden Räumnadeln eingesetzt. Sie werden zum Innenräumen eingesetzt und werden durch die Bohrung gezogen. Teilweise werden jedoch auch sämtliche Räumwerkzeuge als Räumnadel bezeichnet. Werkzeuge, die geschoben werden, werden als Räumdorn[2] bezeichnet. Räumnadeln und -dorne werden bis zu einem Durchmesser von 150 mm als einteilige Werkzeuge gefertigt. Mehrteilige werden entweder mit Räumbuchsen oder Räumeinsätzen hergestellt und eignen sich für Durchmesser bis 500 mm.[3] Derart große Durchmesser werden zum Innenräumen von Hohlrädern benötigt; ihre Länge reicht von 100 mm bis 10 m.[4] Räumwerkzeuge, die aus mehreren Buchsen bestehen und auf einem Dorn gespannt sind, haben fertigungstechnische Vorteile: Sie biegen sich beim Härten weniger durch, wodurch das Aufmaß für das anschließende Schleifen geringer ausfallen kann.[5] Daneben gibt es noch Werkzeug die aus einem einfachen länglichen Grundkörper bestehen, in den die Schneiden eingesetzt werden.[6]
Beim Profilräumen werden auch Schneidscheiben eingesetzt, die auf einem Block verschraubt sind. Wenn die Schneiden abstumpfen müssen sie nachgeschliffen werden und werden dabei kleiner. Bei Schneidscheiben kann dabei jeweils eine neue Scheibe mit vollem Umfang aufgeschraubt werden und die vorderste entfernt werden.[7]
Für das Tubusräumen (auch Topfräumen genannt), das sich zur Herstellung von geschlossenen Außenprofilen eignet, werden Werkzeuge verwendet, die aus einem länglichen Hohlzylinder bestehen. Im Inneren befinden sich Führungsleisten und Schneiden. Meist wird das Werkstück hindurchgedrückt.[8]
Für das Rotationsdrehräumen gibt es spezielle Werkzeuge deren Schneiden nicht linear angeordnet sind, sondern auf einer Kreisbahn. Das Werkzeug wird dabei während der Bearbeitung geschwenkt.[9]
Die meisten Werkzeuge bestehen aus Vollmaterial, meist Schnellarbeitsstahl. Für Sonderanwendungen, etwa das Hartzerspanen, das Rotationsdrehräumen oder die Großserienfertigung, existieren auch Werkzeuge mit austauschbaren Wendeschneidplatten. Sie können mit veränderten Schneidplattengeometrien schnell an andere Werstückgeometrien angepasst werden.[10]
Schneidstoffe
Der Standardschneidstoff für Räumwerkzeuge ist Schnellarbeitsstahl. Beim Räumen kommen meist nur geringe Schnittgeschwindigkeiten von maximal 30 m/min vor, was zu geringen Temperaturen von höchstens 600 °C führt. Schnellarbeitsstahl ist damit meist vollkommen ausreichend. Ein weiterer Grund für Schnellarbeitsstahl ist neben den geringen Kosten die gute Schleifbarkeit. Räumwerkzeuge haben meist eine recht komplizierte Schneidengeometrie und werden häufig nachgeschliffen.[11] Für die Bearbeitung von Grauguss werden auch Werkzeuge genutzt, die mit Schneiden aus Hartmetall bestückt sind. Beim Harträumen oder für Grauguss kommt auch Kubisches Bornitrid in Frage. Zur Erhöhung der Standzeit werden Werkzeuge für die Serienproduktion häufig beschichtet mit Titannitrid oder Titancarbonitrid.[12][13]
Bestandteile
Räumwerkzeuge bestehen aus einem Mittelteil mit Schneiden, sowie einen Schaft am schmalen Ende der in die Maschine eingespannt wird, um das Werkzeug zu ziehen. An den Schaft schließt sich ein Einführungsteil an, das das Einführen in die Bohrung erleichtert. Danach folgt der Schneidenteil, der sich in drei Bereiche unterteilen lässt:
- Schruppteil für das Schruppen (Grobbearbeitung), mit relativ großer Spanungsdicke und entsprechend hohem Zahnvorschub.
- Schlichtteil für das Schlichten (Feinbearbeitung), mit geringerer Spanungsdicke und Zahnvorschub. Der letzte Schlichtzahn legt die Endkontur fest.
- Kalibrier- oder Reserveteil. Er besteht aus mehreren gleich großen Reservezähnen, die die verschleißbedingte Maßänderung der Schlichtzähne ausgleichen. Falls die Schrupp- und Schlichtzähne wegen Verschleiß nachgeschliffen werden müssen, werden sie dabei kleiner. Der erste Kalibrierzahn wird dabei zum letzten Schlichtzahn. Räumwerkzeug sind die einzigen Zerspanungswerkzeuge mit Reservezähnen, was an ihren hohen Kosten liegt.
Am Ende des Schneidenteils folgt ein weiteres Führungsteil zur Stabilisierung der Lage in der fertigen Innenkontur, sowie ein weiteres Endstück zum Einspannen in der Maschine. Meist werden sie an diesem Teil gehalten und in die Bohrung eingeführt. Danach greift von der anderen Seite der Bohrung ein anderes Spannmittel nach dem vorderen Teil und zieht das Räumwerkzeug durch die Bohrung. Nachdem das Werkstück aus der Maschine entfernt wurde, greift wieder das erste Spannmittel nach dem Endstück und fährt in die Ausgangsposition zurück.
Die Länge des Schneidenteils ergibt sich aus der Anzahl der Zähne und der Zahnteilung also dem Abstand zweier Zähne. Er ist eine wichtige konstruktive Größe. Ist die Teilung zu klein, können die abgetrennten Zähne nicht in den Zwischenräumen aufgenommen werden, ist er sehr groß dauert die Bearbeitung lange und wird unwirtschaftlich. Üblicherweise haben Räumwerkzeuge im Schrupp-, Schlicht- und Kalibierteil unterschiedliche Zahnvorschübe und Teilungen.[14][15][16]
Schneidengeometrie und Spanungsgrößen
Die Spanungsgrößen sind anders als sonst bei Zerspanungswerkzeugen fest im Werkzeug integriert. Der Konstrukteur des Werkzeuges legt somit auch die Verfahrensparameter fest. Der Abstand zweier aufeinanderfolgender Zähne senkrecht zur Schnittrichtung ergibt direkt den Zahnvorschub (Vorschub pro Zahn) , der mit der Spanungsdicke identisch ist. Die Schnittbreite entspricht wie beim Sägen der Breite des Werkzeuges und damit auch der Breite der erzeugten Nut beim Planräumen. Mit dem Neigungswinkel der die Neigung der Schneiden gegenüber der Schnittrichtung angibt, erhält man die Spanungsbreite durch
- .
Der Spanungsquerschnitt pro Schneide ergibt sich zu
- .
Zwischen zwei benachbarten Zähnen liegen Spankammern, die zur Aufnahme der Späne dienen. Der Abstand zweier Zähne in Schnittrichtung wird wie auch beim Sägen als Teilung bezeichnet. Die Anordnung der Zähne wird als Staffelung bezeichnet. Wenn jeder Zahn auf voller Breite Material abträgt und jeder darauffolgende tiefer in den Werkstoff eindringt, ist das Werkzeug in Tiefenstaffelung ausgeführt. Wenn dagegen einzelne schmale Zähne jeweils seitlich versetzt sind, spricht man von Seitenstaffelung. Es sind auch Kombinationen möglich.
Die Wahl der Schneidengeometrie ist von zahlreichen Faktoren abhängig. Dazu zählt der Werkstoff, die Spannung des Werkstücks, der Schneidstoff und die Beschichtung des Werkzeuges, die Schnittgeschwindigkeit, die Maschinendynamik und die Kühlschmierstoffe. Die Bezeichnungen der Schneidengeometrie sind in der DIN 1415-1 und der DIN 1409 festgelegt.[17]
Zahnvorschub / Spanungsdicke
Der Zahnvorschub und damit auch die Spanungsdicke ist abhängig von Werkstoff und der Art der Staffelung. Außerdem ist sie im Schruppteil größer als im Schlichtteil. Beim Räumen von Stahl liegen die Dicken zwischen 0,01 mm bis 0,15 mm im Schruppteil und 0,003 mm bis 0,025 mm beim Schlichten. Anhaltswerte bietet die folgende Tabelle.[18]
Werkstoff | Spanungsdicke h in mm | ||
---|---|---|---|
Tiefenstaffelung | Seitenstaffelung | ||
Schruppen | Schlichten | ||
Stahl / Gussstahl / Gusseisen mit Kugelgraphit | 0,01 bis 0,15 | 0,003 bis 0,025 | 0,8 bis 0,25 |
Gusseisen mit Lamellengraphit / Nichteisenmetalle | 0,02 bis 0,2 | 0,01 bis 0,04 | 0,1 bis 0,5 |
Kunststoff | 0,02 bis 0,06 | 0,1 bis 0,5 |
Teilung
Der Abstand zweiter Zähne ist die Teilung . Je größer sie ist, desto länger sind die zwischen den Zähnen liegenden Spankammern. Das Werkzeug wird jedoch länger und die Bearbeitungszeit steigt somit. Bei einer geringen Teilung sind außerdem mehr Zähne gleichzeitig im Eingriff, sodass sich die Maschinenleistung besser ausnutzen lässt. Die Spankammer benötigt jedoch einen bestimmten Mindestquerschnitt zur Aufnahme der Späne. Wird die Tiefe der Spankammer erhöht, schwächt dies die Stabilität der Schneiden.
Der Span benötigt umso mehr Raum je länger die Räumlänge (Schnittweg, Spanungslänge, Weg den die Schneiden im Werkstück zurücklegen) ist, je größer die Spanungsdicke ist und je größer der Spanraumfaktor (auch Spanraumzahl) ist. Erfahrungsgemäß kann die nötige Teilung mit folgender Formel abgeschätzt werden:[19]
Der Faktor 2,5 gilt für das Schlichten, 3 für das Schruppen.[20][21]
In der folgenden Tabelle stehen Anhaltswerte für den Spanraumfaktor bei Werkzeugen aus HSS. Wenn Werkzeuge mit anderen Schneiden verwendet werden, muss die Teilung entsprechend angepasst werden, um den passenden Spankammerquerschnitt zu erhalten. Die kleinen Werte gelten für die günstigen Umstände wie nidriege Schnittgeschwindigkeit, guter Ausfall der Späne aus den Kammern, kleine Spanungsdicke, Neigungswinkel größer Null oder Bürsten zum Entfernen der Späne. Eine Rolle spielen außerdem die gewünschte Oberflächenqualität, der Werkzeugverschleiß und die Maschinen.[22]
Werkstoff | Spanraumfaktor R | |||
---|---|---|---|---|
Innenräumwerkzeug | Außenräumwerkzeug | |||
Flach | Rund | Tiefenstaffelung | Seitenstaffelung | |
Stahl, Gussstahl, Gusseisen mit Kugelgraphit | 5 bis 8 | 8 bis 16 | 4 bis 10 | 1,8 bis 6 |
Gusseisen mit Lamellengraphit, Nichteisenmetalle, Kunststoffe | 3 bis 7 | 6 bis 14 | 3 bis 7 | 1 bis 5 |
Span-, Frei- und Neigungswinkel
Der Spanwinkel beeinflusst die Spanbildung, die auftretenden Kräfte und die Stabilität der Schneiden. Der Freiwinkel hat Einfluss auf den Verschleiß und die Reibung. Je höher die Schnittgeschwindigkeit ist, desto größer werden beide Winkel gewählt. Bei einem größeren Spanwinkel rollt sich der Span besser ein und bei größerem Freiwinkel bleibt weniger Material an der Freifläche haften. Bei der Wahl der Winkel ist auch zu beachten, dass sie die Form des Werkzeuges nach dem Schleifen beeinflussen.
Der Neigungswinkel betrug lange Zeit fast immer Null Grad. Lediglich beim Außenräumen kamen Neigungswinkel größer Null vor.[23] Grund dafür waren die hohen Kosten beim Schleifen für komplizierte Schneidenformen. Spätestens seit 2015 sind Schleifmaschinen verfügbar mit denen auch kostengünstig Neigungswinkel eingeschliffen werden können. Diese führen dazu, dass die Schneiden nicht sofort mit voller Breite mit dem Werkstück in Kontakt kommen, sondern allmählich was zu einem langsameren Ansteigen der Schnittkraft führt. Beim Austritt der Schneiden aus dem Werkstoff gilt dies ebenso. Dies führt über geringere Schwingungen zu besseren Genauigkeiten sowie zu einer geringeren Lärmentwicklung und einer leichteren Spanabfuhr.[24]
Bei langspanenden Werkstoffen (meist weiche zähe Werkstoffe wie Aluminium) kann der Spanbruch problematisch sein. Falls die Späne nicht brechen, neigen sie zum Verheddern. Die Schneiden werden dann in zwei ungleiche Hälften geteilt. Zwischen ihnen liegt die Spanteilernut. Dadurch wird der Spanbruch verbessert. Auf der nächsten Schneide sind die Spanteilernuten dann seitlich versetzt angeordnet.[25]
Staffelung
Die Art der aufeinanderfolgenden Zähne wird als Staffelung bezeichnet. Standard ist die Tiefenstaffelung, bei der jeder Zahn auf voller Breite in den Werkstoff eindringt und jeder weitere Zahn um die Spanungsdicke tiefer eindringt. Bei Gussstücken mit einer harten Gusshaut oder Schmiedestücken wird dagegen die Seitenstaffelung bevorzugt. Hier werden Streifen abgetrennt, die senkrecht zum Werkzeug liegen. Die Werkzeugbelastung ist dann geringer, es werden jedoch mehr Schnitte und somit längere Werkzeuge benötigt. Die Fertigbearbeitung erfolgt in Tiefenstaffelung. Eine Kombination aus Tiefen- und Seitenstaffelung wird als Keilstaffelung bezeichnet.[26]
Einzelnachweise
- Fritz Klocke, Wilfried König: Fertigungsverfahren Band 1: Drehen, Fräsen, Bohren, Springer, 8. Auflage, 2008, S. 483.
- Herbert Schönherr: Spanende Fertigung, Oldenbourg, 2002, S. 324.
- Herbert Schönherr: Spanende Fertigung, Oldenbourg, 2002, S. 335 f.
- Fritz Klocke, Wilfried König: Fertigungsverfahren Band 1: Drehen, Fräsen, Bohren, Springer, 8. Auflage, 2008, S. 486.
- Fritz Klocke, Wilfried König: Fertigungsverfahren Band 1: Drehen, Fräsen, Bohren, Springer, 8. Auflage, 2008, S. 488.
- Herbert Schönherr: Spanende Fertigung, Oldenbourg, 2002, S. 336.
- Fritz Klocke, Wilfried König: Fertigungsverfahren Band 1: Drehen, Fräsen, Bohren, Springer, 8. Auflage, 2008, S. 488.
- Herbert Schönherr: Spanende Fertigung, Oldenbourg, 2002, S. 336.
- Fritz Klocke, Wilfried König: Fertigungsverfahren Band 1: Drehen, Fräsen, Bohren. Springer, 8. Auflage, 2008, S. 460 f.
- Fritz Klocke, Wilfried König: Fertigungsverfahren Band 1: Drehen, Fräsen, Bohren. Springer, 8. Auflage, 2008, S. 491.
- Herbert Schönherr: Spanende Fertigung. Oldenbourg, 2002, S. 335.
- Alfred Herbert Fritz, Günter Schulze (Hrsg.): Fertigungstechnik. Springer, 9. Auflage, 2010, S. 308.
- Fritz Klocke, Wilfried König: Fertigungsverfahren Band 1: Drehen, Fräsen, Bohren. Springer, 8. Auflage, 2008, S. 484.
- Herbert Schönherr: Spanende Fertigung, Oldenbourg, 2002, S. 334–336
- Alfred Herbert Fritz, Günter Schulze (Hrsg.): Fertigungstechnik, Springer, 9. Auflage, 2010, S. 308–310.
- Christoph Klink, Karlheinz Hasslach, Walther Maier: Räumen, S. 469, 473 f. in: Uwe Heisel, Fritz Klocke, Eckart Uhlmann, Günter Spur (Hrsg.): Handbuch Spanen. 2. Auflage, Hanser, München 2014.
- Christoph Klink, Karlheinz Hasslach, Walther Maier: Räumen. S. 469 in: Uwe Heisel, Fritz Klocke, Eckart Uhlmann, Günter Spur (Hrsg.): Handbuch Spanen. 2. Auflage, Hanser, München 2014.
- Christoph Klink, Karlheinz Hasslach, Walther Maier: Räumen. S. 469 in: Uwe Heisel, Fritz Klocke, Eckart Uhlmann, Günter Spur (Hrsg.): Handbuch Spanen. 2. Auflage, Hanser, München 2014.
- Christoph Klink, Karlheinz Hasslach, Walther Maier: Räumen, S. 470 in: Uwe Heisel, Fritz Klocke, Eckart Uhlmann, Günter Spur (Hrsg.): Handbuch Spanen. 2. Auflage, Hanser, München 2014.
- Herbert Schönherr: Spanende Fertigung. Oldenbourg, 2002, S. 332.
- Alfred Herbert Fritz, Günter Schulze (Hrsg.): Fertigungstechnik. 11. Auflage. Springer Vieweg, Berlin/Heidelberg 2015, S. 332.
- Christoph Klink, Karlheinz Hasslach, Walther Maier: Räumen, S. 471 in: Uwe Heisel, Fritz Klocke, Eckart Uhlmann, Günter Spur (Hrsg.): Handbuch Spanen. 2. Auflage, Hanser, München 2014.
- Herbert Schönherr: Spanende Fertigung, Oldenbourg, 2002, S. 330.
- Christoph Klink, Karlheinz Hasslach, Walther Maier: Räumen. S. in: Uwe Heisel, Fritz Klocke, Eckart Uhlmann, Günter Spur (Hrsg.): Handbuch Spanen. 2. Auflage, Hanser, München 2014.
- Herbert Schönherr: Spanende Fertigung. Oldenbourg, 2002, S. 330.
- Alfred Herbert Fritz, Günter Schulze (Hrsg.): Fertigungstechnik. 11. Auflage. Springer Vieweg, Berlin/Heidelberg 2015, S. 332.