Uhrglas (Uhr)
Ein Uhrglas ist ein durchsichtiger Schutz des Zifferblattes und der Zeiger von Uhren in einer Vielzahl von Formen, Größen und Qualitäten.
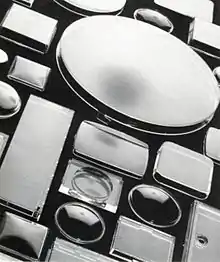
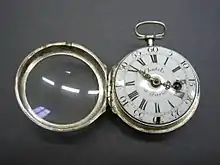
Werkstoffe
- Vom Anfang her: ungehärtete Mineralgläser (auch bezeichnet als Silikatgläser, Kristallgläser oder Gläser aus anorganischem Glas)
- Seit den 1930er Jahren: Kunststoffgläser aus Kunststofftafeln
- Seit den 1950er Jahren: Spritzguss-Kunststoffgläser aus Granulat
- Seit den 1970er Jahren: gehärtete Mineralgläser
- Seit den 1980er Jahren: Saphirgläser
Ungehärtetes Mineralglas
Die ersten Uhrgläser waren aus Glas. Als später Uhrgläser aus Kunststoffen hergestellt wurden und das Warenzeichen Plexiglas für einen Kunststoff registriert wurde, ergab sich gerade bei Uhrgläsern die Notwendigkeit zur eindeutigen Unterscheidung. Inzwischen hat sich in der Branche der Begriff Mineralglas gefestigt, der von dem führenden deutschen Uhrglashersteller, der Firma Münchmeyer Sternkreuz GmbH & Co. KG, in ihrer vielsprachigen Werbung weltweit empfohlen wurde. Für die Uhrgläser wird farbloses optisches Glas eingesetzt, das ursprünglich zu Kugeln geblasen und dann in Kugelabschnitte zerlegt wurde. Aus den sogenannten Kalotten wurden dann die Uhrgläser geschnitten, an den Kanten geschliffen und poliert. Anfangs hatten alle Uhrgläser daher ein sphärische Wölbung, auch wenn sie z. B. rechteckig waren. Später wurden die Gläser in kleinen Muffelöfen erneut aufgeheizt und mittels Holzstempeln in Kaolinformen gedrückt, so dass beispielsweise größere Randwölbungen hergestellt wurden und vielfältige Formen mit flachen Auflagen. Auch diese Gläser wurden an den Kanten geschliffen und poliert. Durch die Bearbeitung streuten die Abmessungen weit, daher wurden die fertigen Gläser auf 1/10 mm genau vermessen und sortiert. Heute wird das optische Glas in flachen Tafeln hergestellt (gezogen).
Kunststoffgläser aus Kunststofftafeln
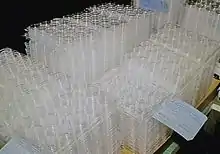
Ende der 1920er, Anfang der 1930er Jahre brachte das nordamerikanische Unternehmen Germanow-Simon, Rochester, Uhrgläser aus Zelluloid heraus, die mit dem Merkmal „unzerbrechlich“ sofort zu großer Nachfrage führten, obwohl der Werkstoff Zelluloid, in großer Menge extrem feuergefährlich, im Sonnenlicht sehr schnell vergilbte und schrumpfte. Sehr bald wurde es durch den Werkstoff Cellon ersetzt, der aber eine bläuliche Eigenfarbe hatte und auch nicht sehr formbeständig war. Erst als 1934 von Röhm, Darmstadt, der Werkstoff Polymethylmethacrylat als Plexiglas zur Marktreife gebracht wurde, hatte man einen lichtbeständigen, nicht schrumpfenden Werkstoff, der dann dem Kunststoffuhrglas den Weltmarkt öffnete. Celluloid, Cellon und auch Acrylglas (Sammelname für zahlreiche Handelsmarken auf dem Markt) waren Plattenwerkstoffe, die in den verschiedenen Stärken zwischen 0,5 und 1,5 mm zu erwerben waren, erwärmt und dann verformt wurden. Bis heute sind dazu verschiedene Verformungsverfahren im Einsatz.
Spritzguss-Kunststoffgläser aus Granulat
In den 1950er Jahren wurde der Kunststoff-Spritzguss zur Marktreife entwickelt. Der als Granulat im Vergleich zu den Tafeln preislich günstigere Kunststoff wird heiß und unter hohem Druck in fertige Stahlformen gedrückt und erhält so seine endgültige Form, von der nur noch die Anspritzstelle beseitigt werden musste. Für Uhrgläser hat dieses Verfahren Grenzen, weil gespritzte Kunststoffteile vom Anguss her unsymmetrische Herstellungsspannungen aufweisen. Armbanduhrgläser, in der Fachsprache auch „Kleinuhrgläser“ genannt, wurden ursprünglich alle in den Glasrand des Uhrgehäuses, die Lünette, eingesprengt, d. h. mit einer Wölbespannung eingesetzt. Die zusätzliche Herstellungsspannung vom Spritzen bringt solche eingesprengten Gläser sehr bald zum Reißen. Für Wecker, in welche die Gläser spannungsfrei eingebaut wurden, hat sich das gespritzte Kunststoffglas sehr schnell voll durchgesetzt. Bei Armbanduhren kam es erst zur Anwendung, als Einbaumethoden entwickelt wurden, die keine zusätzlichen Biegespannungen auf die Gläser brachten, z. B. sogenannte „Armierte Gläser“, mit einem Spannring, der das Glas gegen die Lünette drückt.
Gehärtete Mineralgläser
Glasscheiben von 3 mm Stärke aufwärts hat man sehr frühzeitig in der Entwicklungsgeschichte durch punktuelles Erhitzen und Abschrecken so mit Spannungen versehen, dass sie biegsam sind und im Zerstörungsfalle zu Krümeln zerfallen. Man nennt das thermische Glashärtung. In den 1970er Jahren wurde dann die chemische Glashärtung erfunden, bei der man die gewünschte Spannungsverteilung im Glas dadurch erzeugte, dass in einem Salzbad die kleineren Ionen in den beiden Glasoberflächen durch größere ausgetauscht wurden. So wurde es möglich, die Uhrgläser, die in der Regel 1 mm dick waren, zu härten. Seitdem haben diese Mineralgläser – die Härtung wird heute als selbstverständlich vorausgesetzt – die Kunststoffgläser wieder weitgehend verdrängt, abgesehen von Armbanduhren der unteren Preisklasse. Weckergläser werden allerdings unverändert wegen der Gesamtpreislage der Wecker aus Kunststoff im Spritzgussverfahren hergestellt.
Saphirgläser
Die Mineralgläser waren nunmehr nicht mehr zerbrechlich, aber die Glasoberfläche blieb kratzempfindlich. Die Kratzer in den Mineralgläsern waren, im Gegensatz zu Kratzern bei Kunststoffgläsern, tiefe Rillen, die man nicht auspolieren konnte. Älter werdende Mineralgläser wurden bis zur Undurchsichtigkeit verkratzt. Mittlerweile waren synthetische Saphire entwickelt, die bei hohen Temperaturen aus Tonerde hergestellt werden, und man hat die Bearbeitung dieser Saphire technisch gelöst. Der künstliche Saphir ist am Anfang eine längliche Birne, aus der man Uhrgläser quasi als Scheiben herausschneidet, die dann geschliffen und poliert werden müssen. Sowohl der Rohstoff, als auch die Bearbeitung sind teuer. Trotzdem hat sich inzwischen ab einer gewissen Klasse Armbanduhren das Saphirglas als Standard weitgehend durchgesetzt.
Wege vom Hersteller zum Verbraucher
Erstausstattung
Für die Uhrenindustrie werden die Uhrgläser – und die dazu notwendigen Formen und Werkzeuge – nach Wunsch des Uhrenherstellers oder auch des Gehäuseherstellers angefertigt. Ursprünglich wurde noch in Dutzend (12 Stück) und Gros (144 Stück) gezählt und in Rollen verpackt. Inzwischen gilt das Dezimalsystem und für die automatische Verarbeitung werden die Gläser häufig auf Tabletts geliefert.
Furniturengläser
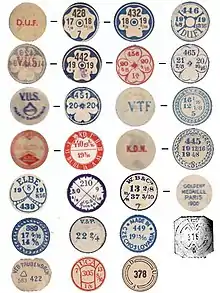
Ein Uhrmacher, der ein Uhrglas ersetzt, kann heute auf ein enorm großes Sortiment unterschiedlicher Größen und Sorten in den verschiedenen Qualitäten zurückgreifen. Dafür gibt es Kataloge in vielen Sprachen. Der Uhrmacher kauft seinen Bedarf, der ja auch viele andere Uhrenteile umfasst, beim Uhrenersatzteil-Großhandel. Die Uhrenersatzteile heißen im Fach Uhrenfurnituren[1] und die Großhandlungen Furniturengroßhandlungen. Daher spricht man auch von Furniturengläsern. Die Großhandlungen unterhalten selbst große Lager und greifen ihrerseits auf die noch größeren Lager bei den Glasherstellern zurück. Die Uhrgläser für den Vertrieb über den Großhandel an den Uhrmacher wurden ursprünglich zur Kennzeichnung von Typ und Größe einzeln mit Etiketten beklebt. Das Bild zeigt die Etiketten der DUF (siehe unten) und einiger anderer Fabriken. Mit dem Aufkommen der Kunststoffuhrgläser erfolgte die Verpackung der Gläser in einzelnen kleinen Tüten. Ursprünglich wurde wegen der Zerbrechlichkeit der Gläser jede Uhr in ihrem Lebenslauf mehrfach neu verglast. Inzwischen ist der Glasaustausch durch die „Wegwerf-Uhr“ im Billigbereich und die Saphirgläser bei den besseren Uhren stark zurückgegangen.
Geschichte der Uhrglasherstellung
Die Anfänge bis zum Ersten Weltkrieg
Die ersten Uhrglasfabriken in Europa entstanden um 1830/1840 in den Vogesen in Lothringen. Bekannt sind die Chrystallerie de Vallerysthal und Walter Berger & Co in Götzenbrück. Von 1860 bis 1870 übernahmen die Verreries de Trois-Fontaines (VTF) in Dreibrunnen die Marktführung. Diese Firmen bezogen die Rohglaskalotten (Kugelausschnitte) von der Deutschen Spiegelglas AG (DESAG, heute Schott AG) in Grünenplan, Kreis Holzminden. Diese Tafelglas-Hütte stellte und stellt optisches Glas her, das im Gegensatz zu allgemeinem Fensterglas absolut farblos ist. Das Glas wurde in großen Tonbottichen in Häfen erschmolzen, von denen zehn Stück in einem großen, ursprünglich mit Holz beheizten, Ofen standen. Die Häfen an den Stirnseiten des Ofens wurden nicht so heiß wie im Zentrum. Die optische Glasqualität war für Brillen und andere Optiken nicht ausreichend. Aus diesen Häfen wurde das Glas für die Uhrgläser geblasen. Für die DESAG, deren damaliger Direktor Franz Krippendorff war, erschien der Absatz des Glases für die Uhrgläser besonders wichtig. Als der größte Abnehmer, die VTF als Abnehmer wegen billigerer Konkurrenzangebote auszufallen drohte, gründete die DESAG 1906 in Zusammenarbeit mit den führenden deutschen Furniturengroßhandlungen Flume, Berlin, und Jakob, Leipzig, zwei eigene Uhrglasfabriken. Unter dem Namen Jequier & Co entstanden sie in Frammont in den Vogesen und in Fleurier in der Schweiz. Die Uhrgläser für die beiden beteiligten Großhandelsfirmen wurden unter einer eigenen Marke Elbe vertrieben.
Es entspann sich ein Konkurrenzkampf sowohl um die Uhrgläser für die Erstausstattung der Fabriken als auch um die Uhrgläser für den internationalen Ersatzteilgroßhandel, das heißt für die Uhrmacher. Die Preise verfielen derart, dass die Einstellung der Uhrglasproduktionen drohte. Unter Einschaltung der führenden Uhrenfirmenchefs Junghans, Kienzle, Kollmar, Daub und Haller erfolgte 1912 eine Einigung zwischen den Uhrglasfabrikanten, den Uhrenfabriken und dem Großhandel über die Gründung eines Uhrglassyndikates in Straßburg die Verreries Unies Strasbourg (VUS). Die Verhandlungsführung lag bei Rudolf Flume, Inhaber der Berliner Firma Flume. Ein weiterer Verfall des Uhrglasmarktes wurde verhindert, und die Produktion eines wichtigen Artikels konnte aufrechterhalten werden. Bis Ende 1918 verlief die Zusammenarbeit erfolgreich.
Von 1918 bis 1930
Mit Deutschlands Kapitulation zur Beendigung des Ersten Weltkrieges wurden durch den Vertrag von Versailles auch die Uhrglasfabriken in Frammont und ein Anteil an Fleurier enteignet. Die französischen Uhrglasfabriken stellten ihre Rohglaskäufe bei der DESAG ein. Durch die Inflation und den Devisenmangel gab es in Deutschland keine Uhrgläser mehr. In dieser Situation wurde von der Notgemeinschaft, bestehend aus der DESAG, den Firmen Flume, Jacob, Ludwig und Fries 1919 die Gründung der Deutschen Uhrglasfabrik GmbH (DUF) in Freden beschlossen, deren Kapital zu 100 Prozent die DESAG übernahm. Die Leitung übernahm der Generaldirektor der DESAG, Franz Krippendorff. Der DESAG wurde damit der Bezug von Rohglas gesichert und der deutschen Industrie und dem Großhandel die Lieferung von Uhrgläsern im Inland. Durch den frühen Tod von Krippendorff im Jahre 1919 kam der Firmenaufbau ins Stocken. Der Sohn Walter Krippendorff musste unter Abbruch des Studiums 1920 den Aufbau übernehmen und konnte diesen erfolgreich durchführen unter Verlagerung vom Gründungsort Freden zum Hauptsitz der DESAG nach Grünenplan. Anfang der 1920er Jahre wurden 50.000 bis 60.000 Uhrgläser pro Tag produziert.
Zwischen dem Straßburger Syndikat der Uhrglasfabriken und der DESAG in Grünenplan entwickelten sich erneut scharfe Konkurrenzkämpfe. Durch Vermittlung der Großhandelsfirmen wurde die DUF 1927 in das Syndikat aufgenommen, aber zu ungünstigen Bedingungen, und sie wurde innerhalb des Syndikates weiterhin still bekämpft. Das führte 1937 zum Austritt der DUF aus dem Syndikat. Die DUF konnte sich inzwischen auf dem Markt gut behaupten, allerdings wurden Armbanduhrgläser zunehmend aus Kunststoff hergestellt. Dementgegen wuchs der Markt für Wecker- und andere Großuhrgläser, zumal die Kunststoffspritzgusstechnik noch nicht existierte. Als später auch die Gläser für Wecker aus Kunststoff gefertigt wurden, stellte man die Produktion der DUF auf Rückspiegel für die Autoindustrie um. Das Unternehmen wurde führend in diesem Segment. Die DESAG wurde später ein Werk der Firma Schott, die DUF geschlossen, und die Produktion in das Hauptwerk übernommen. Die Fertigung von Rückspiegeln später aufgegeben.
Fertigung aus Kunststoff
Als die ersten Kunststoffuhrgläser aus den Vereinigten Staaten kamen, untersagte die DESAG ihrer Tochter, der DUF die Aufnahme der Kunststofffertigung. Man genehmigte aber dem Direktor, Walter Krippendorff, tätig zu werden. Gemeinsam mit seinem Kriegskameraden Dipl. Ing. Heinrich Münchmeyer gründete er 1930/31 in dessen Heimatort Verden die Firma Dipl. Ing. Heinrich. Münchmeyer, heute Münchmeyer Sternkreuz GmbH & Co. Diese Firma – einer der ersten deutschen Kunststoffverarbeiter – nahm aus kleinsten Anfängen die Produktion auf, zunächst aus Celluloid, dann aus Cellon und schließlich aus Acrylglas (Plexiglas).
Quellen
- Deutsche Uhrmacherzeitung 1920er Jahre Seite 979/980
- Dokumente der DUF im Familienbesitz Krippendorff
- Persönliche Aufzeichnungen von Walter Krippendorff (1896–1983)
Literatur
- Johannes Laufer: Von der Glasmanufaktur zum Industrieunternehmen: Die Deutsche Spiegelglas AG (1830–1955). Beiträge zur Wirtschafts- und Sozialgeschichte. Hrsg.: Gömmel, Klug u. Schneider, Bd. 75 in Kom bei Franz Steiner Verg. Stuttgart, 1997
Weblinks
Einzelnachweise
- A.-F. Jobin: Klassifikationen der schweizerischen Uhrwerke und Uhrenfurnituren. Genf, um 1938.