Drehteil (Werkstück)
Als Drehteil werden in der Zerspantechnik die Werkstücke bezeichnet, die durch das Fertigungsverfahren Drehen bearbeitet werden. Analog dazu spricht man von einem Gussstück oder einem Schmiedeteil, wenn es durch Gießen beziehungsweise Schmieden bearbeitet werden soll oder wurde.
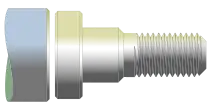
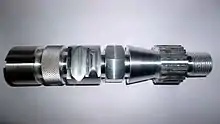
Drehteile haben überwiegend rotationssymmetrische Gestalt. Typische Drehteile sind Schrauben, Achsen, Wellen, Spindeln und Radnaben. Es können auch Gewinde vorhanden sein oder zentrische Bohrungen, die sich auf Drehmaschinen leicht fertigen lassen. Außermittige Bohrungen oder Bohrungen, die in einem bestimmten Winkel zur Drehachse liegen, lassen sich ebenfalls auf Drehmaschinen herstellen, wenn dort angetriebene Werkzeuge zur Verfügung stehen.
Arten
Je nach dem Verhältnis von Länge zu Durchmesser und den Rohteilen unterscheidet man bei Drehteilen zwischen Futterteilen, wellenförmigen Drehteilen, Scheiben und Stangenteilen, sowie Spitzenteilen:[1][2][3]
- Futterteile sind Drehteile, bei denen der Durchmesser in etwa der Länge entspricht. Sie werden einseitig in Drehfuttern festgespannt.
- Wellenteile haben die Form einer Welle. Ihre Länge beträgt ein Mehrfaches des Durchmessers. Sie biegen sich durch ihr Eigengewicht, die Bearbeitungskräfte und Unwuchten stärker durch als Futterteile und müssen daher zusätzlich abgestützt werden. Mittellange Drehteile werden am zweiten Ende mit dem Reitstock abgestützt, längere zusätzlich auf halber Länge mit einer Lünette.
- Scheibenförmige Teile haben einen gegenüber den übrigen Abmessungen großen Durchmesser. Sie werden bevorzugt auf Plandrehmaschinen bearbeitet. Falls sie innen hohl sind und praktisch nur aus einem dünnen, schmalen Ring bestehen, können sie sich während der Bearbeitung stark verformen. Für diese Fälle existieren spezielle Spannsysteme, bei denen besonders viele oder voll umschließende Spannbacken auf dem Umfang gleichzeitig spannen.
- Bei Stangenteilen wird als Rohteil eine Stange genutzt, deren Durchmesser in etwa dem des Werkstücks entspricht und deren Länge ein Vielfaches des Werkstücks beträgt. Diese Stangen werden häufig mit einem Stangenlader der Drehmaschine zugeführt. Häufig ist die Hauptspindel hohl, sodass durch sie hindurch das Rohteil zugeführt wird und mittels einer Spannzange fixiert werden kann. Nach der Bearbeitung wird das Werkstücke mittels Abstech-Drehen von der Stange getrennt und die Stange weiter in die Maschine hineingeschoben, sodass ein weiteres Werkstück bearbeitet werden kann. Das "Drehen von der Stange" kommt besonders oft bei Drehautomaten vor sowie bei der Serienfertigung.
- Spitzenteile sind Drehteile, die zwischen Spitzen gespannt und gedreht werden.
- Drehteile im Durchmesserbereich von 0,1 bis 32 mm werden Präzisionsdrehteile genannt. Diese finden vor allem Gebrauch in der Sensor-, Magnet-, Mess- und Medizintechnik. Dort werden Verbindungselemente, wie z. B. Titanschrauben und Gewindehülsen aus Gold-Platin-Legierungen für die moderne Medizintechnik gebraucht.
- verschiedene Werkstoffe als Stangenmaterial unterschiedlichen Durchmessers und unterschiedlicher Länge zur Herstellung von Drehteilen
- Bearbeitung von Stangenteilen
- Futterteile
- Ein besonders großes Wellenteil (Teil einer Turbine)
Gestaltung von Drehteilen
Der Konstrukteur nimmt mit der Gestaltung der Drehteile großen Einfluss auf die Kosten, die für die Fertigung anfallen. Es existieren daher eine Reihe von Gestaltungsrichtlinien. Grundsätzlich sollen die Werkstücke so gestaltet werden, dass die Bearbeitung möglichst einfach ist.[4]
- Oberflächen mit hoher Oberflächenqualität (geringer Rauheit) sind aufwendiger zu fertigen als Oberflächen mit großer Rauheit. Wenn aus technischen Gründen eine geringe Rauheit erforderlich ist, beispielsweise bei Lagersitzen, so sollten diese in ihrer Länge begrenzt sein und gegenüber angrenzenden Flächen abgesetzt sein.[5]
- Drehteile mit großen Durchmesserunterschieden erfordern einen hohen Aufwand, da viel Material vom Rohteil abgetrennt werden muss. Die Bearbeitung dauert daher lange und der Werkstoff wird ineffizient genutzt. Häufig ist es günstiger, zwei getrennte Teile zu fertigen und diese anschließend zu fügen.[6]
- Die Fertigung wird günstiger, wenn die Werkzeuge über die zu fertigenden Flächen hinausfahren können (sogenannter Werkzeugauslauf).[7]
- Übergänge zwischen verschiedenen Durchmessern sind an Drehteilen häufig gerundet, um die Kerbwirkung zu verringern und damit die Festigkeit zu verbessern. Wenn alle Rundungen denselben (großen) Radius haben, können sie mit einem runden Drehmeißel bearbeitet werden, dessen Radius dem des Werkstücks entspricht (Profildrehen). Bei unterschiedlichen Radien werden entweder verschiedene Werkzeuge benötigt oder Universalwerkzeuge, die über ihre Bewegung die Radien erzeugen, was länger dauert. Form-/Profilwerkzeuge verlieren mit leistungsfähigen CNC-Steuerungen und modernen Werkzeugen zunehmend an Bedeutung.
- Bei der Bearbeitung mit Profilwerkzeugen sollten die vorhandenen Durchmesserunterschiede möglichst gering sein. Da die Drehzahl konstant ist, ergibt sich über den Radius eine unterschiedliche Schnittgeschwindigkeit. Da diese einen großen Einfluss auf den Werkzeugverschleiß hat, wird dies möglichst vermieden.[8]
Literatur
- Herbert Schönherr: Spanende Fertigung, Oldenbourg, 2002, S. 110, 137.
- Andreas Hirsch: Werkzeugmaschinen – Grundlagen, Auslegung, Ausführungsbeispiele, 2. Auflage, 2012, Springer, S. 240–254.
Einzelnachweise
- Bahmann: Werkzeugmaschinen kompakt, 21. Auflage, Springer, S. 130f., 134–137.
- Hirsch: Werkzeugmaschinen, Springer, 2. Auflage, 2012, S. 3, 240, 243, 245, 252f.
- Neugebauer (Hrsg.): Werkzeugmaschinen, Springer, S. 101, 88, 92.
- Alfred Herbert Fritz, Günter Schulze (Hrsg.): Fertigungstechnik, Springer, 2015, 11. Auflage, S. 419–421.
- Herbert Schönherr: Spanende Fertigung, Oldenbourg, 2002, S. 139 f.
- Herbert Schönherr: Spanende Fertigung, Oldenbourg, 2002, S. 140.
- Herbert Schönherr: Spanende Fertigung, Oldenbourg, 2002, S. 140.
- Herbert Schönherr: Spanende Fertigung, Oldenbourg, 2002, S. 141.