CNC-Drehmaschine
Eine CNC-Drehmaschine ist eine Bauart der Drehmaschine und eine CNC-Maschine, also eine Drehmaschine bei der die Werkzeugbewegungen mit numerisch gespeicherten Programmen gesteuert werden (CNC = Computerized Numerical Control). Im Gegensatz zu einer NC-Drehmaschine besitzen die meisten CNC-Maschinen einen Speicher für Programme und eine Schnittstelle, mit der auch CAD-Zeichnungen eingelesen und direkt programmiert werden können.
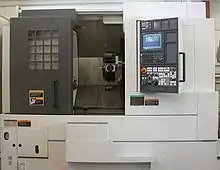
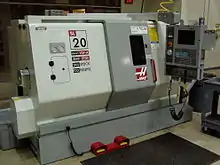
Grundfunktionen
Eine CNC-Drehmaschine besitzt eine Computerized Numerical Control (deutsch: computer- numerische Steuerung). Computerized besagt, dass die Bearbeitungsinformationen in den Speicher der Steuerung eingelesen und ohne weitere Informationszufuhr immer wieder für die Bearbeitung eingesetzt und gespeichert werden können. Im Gegensatz dazu muss bei NC-Maschinen (Numerical Control) mit jeder Bearbeitung die Steuerungs-Information satzweise von einem äußeren Informationsträger (beispielsweise Lochstreifen) eingelesen werden.
Numerisch bedeutet, dass sämtliche Sollvorgaben der Steuerung in Zahlenform codiert mitgeteilt werden und im Arbeitsprozess mittels Regeleinrichtungen ständig verglichen werden:
- die Lage des Werkzeugs und die Geschwindigkeit seiner Spanungsbewegungen
- die Umdrehungsgeschwindigkeit und Lage der Hauptspindel (und damit des Werkstücks)
- die Kühlmittelzufuhr
- Materialzufuhr/Stangenlader
Programmierung
Für die Arbeit mit CNC-Maschinen ist es wichtig, vor der Bearbeitung das nötige CNC-Programm zu erstellen. Das kann entweder direkt an der Maschine (Werkstattprogrammierung), mithilfe von Datenträgern (CD, Diskette, Laptop) geschehen oder über ein spezielles Netzwerk (DNC). Programmiert wird grundsätzlich nach DIN 66025, zusätzlich sind die Herstellerangaben zu beachten. Der Anfang eines Programmes wird mit Oxxxx oder mit %xxxx beschrieben, wobei die x durch Ziffern ersetzt werden. Sie können auch der Anfang oder das Ende z. B. einer Auftragsnummer sein. Danach wird eine sogenannte Technologiezeile erstellt, in dieser Zeile müssen Angaben zu Werkzeugnummer T…., Spindeldrehzahl S… und Drehrichtung der Spindel (M03 Uhrzeigersinn / M04 Gegenuhrzeigersinn) vorhanden sein. Um einen wirtschaftlichen Ablauf zu gewährleisten, sollten CNC-Programme so kurz und übersichtlich wie möglich sein. Buchstaben (außer N) bezeichnet man als Adresse. Eine Adresse mit Ziffern 0–9 ist ein Befehl. Die Befehle werden in der Reihenfolge der tatsächlichen Werkzeugbewegungen eingegeben. Mehrere Befehle für einen Bearbeitungsschritt werden in einem Satz (Zeile) zusammengefasst.
Adressen
Die wichtigsten Adressen (Buchstaben) in einem CNC Programm:
- T… Ruft das entsprechende Werkzeug auf (z. B. T0101 oder T01, T=Tool)
- S… Auswahl der Spindeldrehzahl (zwei bis sechsstellig, z. B. S800 S=Speed)
- M… sogenannte Modalfunktionen (ein- bis dreistellig, je nach Hersteller, z. B. M08 Kühlmittelversorgung EIN M=Miscellaneous)
- G… Wegbefehle (ein- bis dreistellig, Herstellerabhängig, z. B. G00 Gerade Bewegung des Werkzeugs im Eilgang G=Go)
- X, Y, Z, U, V, W, I, J, K, C sind Koordinaten, auf die das Werkzeug fährt
Sogenannte Hilfsparameter für Längen-, Winkel- und andere Zusatzfunktionen sind herstellerabhängig, aber bei allen CNC-Maschinen vorhanden. Die Weg- und Steuerbefehle können auch einstellig angegeben werden, z. B. G1. G0, M3. Eine CNC-Steuerung erkennt in der Regel beide Schreibweisen.
Sätze
CNC-Sätze können mit N und einer Satznummer beginnen. Sie enthalten alle Befehle für einen Bearbeitungsschritt und enden mit einem Satzendezeichen (; oder Zeilenumbruch). Der nächste Satz wird erst begonnen, wenn der vorherige abgearbeitet ist.
Beispiel einer CNC Programmzeile:
Die Befehle haben hier folgende Bedeutung:
- G01 Arbeitsgang, gerader Fahrweg des Werkzeugträgers
- X135.5 Fahre auf Absolut-Koordinaten X135.5
- Z7.2 Fahre auf Absolut-Koordinaten Z7.2
- F0.05 …mit einer Vorschubgeschwindigkeit von 0,05 mm/Umdrehung
- A150 …in einem 30°-Winkel
Diese Angaben sind nur ein Beispiel für einen Ausschnitt aus einem möglichen Programm mit absoluten Koordinatenwerten.
Nullpunkte
Der Maschinennullpunkt ist der, vom Hersteller vorgegebene, Anfang des Koordinatensystems. Jedes CNC-Programm bezieht sich normalerweise auf den einstellbaren Werkstücknullpunkt. Der Werkstücknullpunkt X (und Y) ist bei Drehmaschinen immer die Drehmitte. Der Werkstücknullpunkt Z liegt normalerweise auf der Planfläche des fertigen Werkstücks. Dieser Nullpunkt wird beim Einrichten der Maschine manuell in der Steuerung in Z gesetzt, wobei ca. 1/10 mm Aufmaß für eine nachfolgende Schlichtbearbeitung berücksichtigt wird. Der Werkstücknullpunkt kann bei Bedarf mit Programmbefehlen verschoben werden.
Achsen beim Drehen
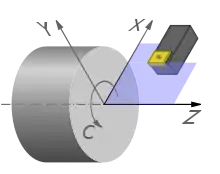
blau = Arbeitsebene G18
Die Bezugsachse beim Drehen ist die Rotationsachse der Hauptspindel, um die sich das Werkstück und das Futter drehen. Diese wird als Z-Achse bezeichnet und zeigt vom Futter in Richtung Reitstock.
Senkrecht zur Z-Achse stehen die Planachse X und die Y-Achse. Die X-Achse zeigt normalerweise nicht den Weg der Planachse, sondern den Durchmesser des Werkstücks an. Die Hauptschneide des Drehwerkzeuges wird in Richtung Y-Achse beim Rüsten fest auf Werkstückmitte eingestellt und liegt meist exakt in der Arbeitsebene G18 bzw. XZ-Ebene. In besonderen Ausnahmefällen, wie dem Abstechdrehen, kann das Drehwerkzeug auch geringfügig unter Drehmitte eingestellt werden.
Drehwinkel um die Hauptachsen werden mit A (Drehung um X), B (Drehung um Y) und C (Drehung um Z) bezeichnet. Weitere Achsen können u. a. die von Werkzeugrevolvern, Lünetten, angetriebenen Werkzeugen, Gegenspindeln oder Reitstöcken sein.
Werkzeuge
Für CNC-Maschinen gibt es wie auch für andere Drehmaschinen eine Vielzahl von Werkzeugen für fast alle gängigen Arbeitsgänge. Die wichtigsten Werkzeuge sind verschiedene Wendeschneidplatten zur zerspanenden Bearbeitung von Rund- oder Kantmaterial sowie Bohrer und Gewindeschneider. Seit einigen Jahren gibt es auch angetriebene Werkzeuge mit deren Hilfe man z. B. auch Fräsarbeiten an konventionellen CNC-Drehmaschinen durchführen oder Gravuren setzen kann. Zu erwähnen sind auch spezielle Messwerkzeuge zum Vermessen produzierter Teile. Eines der wichtigsten Merkmale einer mit CNC gesteuerten Maschine ist die Möglichkeit, in einem Arbeitsgang mehrere unterschiedliche Werkzeuge für eine vielfältige Bearbeitung zu nutzen, ohne die Werkzeuge erst während des Arbeitsganges zu rüsten. Auch bei einfacheren Maschinen sind schon bis zu 99 Werkzeuge programmierbar. Der Nachteil bei solchen Maschinen ist aber oft Platzmangel im Arbeitsraum der Maschine, so dass oft nur maximal vier bis fünf Werkzeughalter zum Einsatz kommen. Besondere Maschinen (CNC mit Werkzeugrevolver, Bearbeitungszentren) können aber bis zu 50 Werkzeuge in bereits integrierten Haltern unterbringen.
Automatisierung
Auf moderneren Maschinen ist eine weitgehende Automatisierung mit Hilfe von Zubringer- und Entnahmesystemen möglich, teilweise können Maschinen auch selbständig Messungen durchführen, dadurch wird das Bedienungspersonal weiter entlastet und die Produktivität weiter verbessert. Solche Arbeitsgänge können sehr wirtschaftlich gestaltet werden, da qualifiziertes Personal oft nur noch für Einstellen und Rüsten der Maschinen benötigt wird.
Benutzung
Das Arbeiten an CNC-Drehmaschinen ist einerseits eine Arbeitserleichterung für den Maschinenbediener, da ein einmal eingespeichertes Programm immer wieder abgearbeitet wird, während ein Dreher an einer von Hand oder mechanisch gesteuerten konventionellen Drehmaschine stets den Bearbeitungsvorgang beobachten und gegebenenfalls in ihn eingreifen muss. Andererseits sind die vorbereitenden Arbeiten auch komplexer, weil beim Rüsten oder Einrichten gedanklich die Abläufe der späteren Arbeit vorausgedacht (und teils programmiert) werden müssen.
Lediglich einfache Funktionen wie die Kühlmittelzufuhr oder ein automatischer Werkzeugwechsel werden über eine SPS wirklich (d. h. ohne Rückkopplung) gesteuert.
Vorteile
- Produktivitätssteigerung
- Hohe Stückzahlen bei gleichbleibender Qualität
- Reduzierung des Werkzeugverschleißes (durch konstante Bedingungen)
- Keine manuellen Eingriffe erforderlich (abgesehen von Werkzeugkorrekturen)
- Konstante Fertigungszeiten (Planbarkeit der Fertigung)
- CNC-Maschinen können miteinander verbunden werden (Fertigungssysteme)
- Große Vielfalt der Bearbeitungsmöglichkeiten
- Mehrmaschinenbedienbarkeit
- Bearbeitung komplexer Werkstücke
- Weitere Verbesserung der Automation durch Roboter, Lader, Einbettung in Netzwerksysteme (DNC) usw.
Nachteile
- Hohe Anschaffungskosten (Maschine plus Steuerung), welche aber durch den großen Preisverfall im Sektor der elektronischen Steuerungen immer geringer werden. Vom wirtschaftlichen Standpunkt her lohnt sich heute die Anschaffung einer konventionell automatisierten Werkzeugmaschine nur noch in Ausnahmefällen
- Hohe Entwicklungsanforderungen an die Arbeitsvorbereitung
- Wartung und Service müssen aufgrund der Komplexität der Anlagen meist von externen Dienstleistern ausgeführt werden
- Die Überwachungsarbeit bei laufender Fertigung wird zur Routinetätigkeit
- Unterschiedliche Belegung von Steuer- und Wegbefehlen einzelner Hersteller
Literatur
- CNC-Technik. Berufsschulausgabe, Christiani Verlag, Konstanz 2009, ISBN 978-3-86522-427-9.
- Fertigungsverfahren. Teil 1, Drehen, Fräsen, Bohren. Springer Verlag, 2008, ISBN 978-3-540-23458-6.
- Dietmar Falk: CNC-Kompendium PAL Drehen und Fräsen. Westermann, Braunschweig 2010, ISBN 978-3-14-235027-1.
- Peter Schierbock: Formeln und Tabellen für metalltechnische Berufe. Bildungsverlag EINS, Troisdorf 2009, ISBN 978-3-8239-7140-5.
Weblinks
- Informationen über CNC Programme, CAD und allgemeine Hinweise (Memento vom 27. Oktober 2014 im Internet Archive) von Theodor Schönwald