Monolithische Kuppel
Monolithische Kuppel oder Monolithischer Kuppelbau (engl. Monolithic Dome) bezeichnet tonnen- oder kuppelförmige Gebäude, deren tragende Schale nahtlos aus einem einzigen Werkstoff gefertigt wird. Meist besteht die Kuppel aus Stahlbeton, der gegossen oder als Spritzbeton aufgetragen wird. Als Schalung oder als tragende Hülle von kleineren Kuppelbauten wird auch Ortschaum bzw. Hartschaum verwendet.
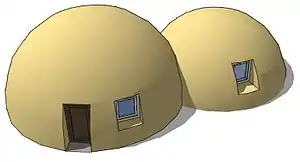
Die Kuppelbauten haben häufig die Form einer Halbkugel und gleichen Iglus. In Europa ist diese Bauform und -konstruktion nahezu unbekannt.
Moderne Herstellungsverfahren
Das US-amerikanische Monolithic Dome Institute (MDI) fertigt Kuppelbauten mit einer Schalung aus Folie und Ortschaum, die von innen mit Spritzbeton ausgefüllt wird. Auf einem Betonfundament wird eine große kuppelförmige Hülle aus Kunststoff befestigt, welche die spätere Form des Gebäudes vorgibt. Sie wird von mehreren Gebläsen mit Luft gefüllt und bis zum Erhärten des Stahlbetons durchgängig unter Druck gehalten. Auf die Innenseite der Hülle wird zunächst eine mehrere Zentimeter dicke Schicht aus Ortschaum gespritzt. In den erhärteten Schaum werden Klammern und Drähte geschoben, an denen später die Stahlbewehrung befestigt wird. Eine zweite Schicht Ortschaum überdeckt und sichert die Befestigung der Bewehrung. Schließlich werden mehrere Schichten Spritzbeton aufgetragen, bis die Bewehrung überdeckt ist. Öffnungen für später einzufügende Fenster und Türen bleiben dabei ausgespart.
Geschichte
Luftdichte Schalungen, die mit Luftdruck aufgeblasen werden, werden als pneumatische Schalung (englisch pneumatic formwork) bezeichnet.[1]
Methode von Wallace Neff
Bereits 1941 beantragte Wallace Neff (1895–1982) ein Patent für seine Methode, eine aufblasbare Schalung mit Spritzbeton zu bekleiden, um schnell und preisgünstig Kuppelkonstruktionen zu errichten.[1][2][3] Später ließ er sich das Design seiner Kuppelhäuser schützen.[4][5] Er entwickelte eine Verstärkung, um die Außenwände aufrechter und das Dach flacher gestalten zu können, ohne dass dies eine größere Menge Spritzbeton erforderte.[6]
Methode von Lloyd S. Turner
Lloyd S. Turner bekam 1966 das Patent für seine Methode zur Herstellung einer selbsttragenden Polyurethanschaumkuppel (englisch foam dome). An ein kreisförmiges Streifenfundament wird eine vorgeformte Folie luftdicht angeschlossen und aufgeblasen. Von innen wird Polyurethanschaum an die Folienkuppel und auf das Fundament gesprüht. Später wird der schwimmende Estrich erstellt. Mit dieser Methode können nur kleine Gebäude errichtet werden. Für eine längere Haltbarkeit und für größere Konstruktionen schlägt Turner das Bekleiden und Verstärken der Hartschaumschicht mit anderen Materialien vor.[7][8]
Methode von Dante Bini
Eine schnelle Methode, um Betonkuppelgebäude ohne Gerüste zu erstellen, wurde vom Italiener Dante Bini entwickelt, einem forschenden Architekt im Bereich automatisierter Bautechniken. Für die Bini Kuppeln (englisch Bini dome) nach dem Binishell System wird zuerst eine runde Fundamentplatte mit umlaufendem Fundamentring gegossen. Auf dem Ring wird ein geschlossener Moniereisenring befestigt, der den Durchmesser der Moniereisenkonstruktion vorgibt. Daneben, zum Mittelpunkt hin, ist ein im Fundamentring eingelassener Schlitz, der sich im inneren des Ringfundaments zu einem ovalen Querschnitt verbreitert. Auf der anderen Seite des Moniereisenrings sind Befestigungslöcher eingelassen. Innerhalb des Moniereisenrings wird eine wiederverwendbare kuppelförmig vorkonfektionierte nylonverstärkte Neoprenfolie flach ausgelegt und luftdicht im Schlitz verankert. Darauf werden PVC-Folienstücke überlappend ausgebreitet, damit sich die Neoprenfolie später mit wenig Reibung auseinander falten kann. Auf dieser Fläche werden federnde Spiralen nach vorgegebenem Muster in den Moniereisenring gespannt. Sie haken ineinander und es werden Moniereisenstäbe überlappend in sie hinein geschoben. Darauf kommt eine dünne Schicht Beton. Auf diesem wird eine weitere vorgeformte und bereits vorgefaltete Folie aus PVC ausgerollt. Der Rand der Folie wird um gebogenen Latten gespannt und mit Schraubhaltern am Fundament befestigt. Bevor der Beton aushärtet, wird in der Mitte der Fundamentplatte Druckluft eingeleitet, um das Sandwich aus zwei Folien und Stahlbeton in die Höhe zu heben. Während sich die Folie entfaltet, streckt sich das Netz aus den sich überschneidenden und gelenkig verbundenen Moniereisen zu einer Kuppelform. Die Spiralen haben die Aufgabe ein ungleichmäßiges Ausdehnen zu verhindern, den Beton am Ort zu halten und die gleichmäßige Verteilung des Betons während des Hebevorgangs sicherzustellen. Auch schützen sie die Folie, wenn die Moniereisen aneinander vorbei gleiten. Diese Methode wird als Bini-Schalung oder Pneumoform bezeichnet. Wenn die von der Folie vorgegebene Form erreicht ist, werden an Seilen geführte Betonverdichtern außen über die Kuppel bewegt. Wenn der Beton nach ein bis drei Tagen genügend ausgehärtet ist, wird der Druck abgelassen, die äußere Folie entfernt, Öffnungen in den Beton geschnitten und die innere Folie entfernt. Der Vorteil der Methode ist die hohe Produktivität in überbauten Quadratmetern bei niedrigem Personal- und Produktionsmitteleinsatz. Eine 36 m weite Kuppelschale ist im Scheitel 75 mm stark und an der Basis 125 mm.[9][10] Auf die rohe Kuppel wird nach dem Anfertigen aller Öffnungen eine flüssige Dampfsperre aufgesprüht, gefolgt von einer wärmeisolierenden Schicht Ortschaum. Auf den unteren drei Metern wird zusätzlich Sprühputz aufgebracht, bevor alles mit einer wasserdichten Farbe versiegelt wird.[10]
Zwischen 1970 und 1990 wurden 1500 Bini-Kuppeln mit rundem oder elliptischem Grundriss und Durchmessern zwischen 12 und 40 Metern errichtet.[9][11][12]
Mit der Methode eine flache Betonschicht pneumatisch vom Boden anzuheben und zu formen, werden ein- oder mehrstöckige Häuser, Hallen und offene Unterstände gebaut.[9][13] Aufwendig herzustellen sind die luftundurchlässigen Abdichtungen der inneren Folie im Fundament. Darum wird inzwischen mit einem geschlossenen Luftkissen unter dem Folien-Beton-Sandwich gearbeitet. Die Methode wurde 2014 weiterentwickelt mit dem Unterschied, dass nicht nur ein Luftkissen benutzt wird, sondern mehrere, die Kuppeltortenstücken ähneln. Damit können vor allem zweifach gekrümmte runde bzw. elliptische Betonschalen, aber auch längere elliptische Konstruktionen hergestellt werden.[1][13]
In den 1970er Jahren entwickelte Dante Bini das Minishell-System für nahezu quadratische Unterstände und Häuser mit acht mal acht oder zehn mal zehn Metern Grundfläche. Erst wurde ein achteckiges, nahezu quadratisches Fundament gegossen. Darauf kam ein etwa quadratisches Luftkissen, das mit PVC-Folienstücken abgedeckt wurde. In Kreuzform wurden Moniereisen von überwiegend 6 mm Durchmesser ausgelegt und an den Seiten des Fundaments mit einem Freiheitsgrad befestigt. Dann wurde nur 4,5 Kubikmeter Beton aufgebracht mit einer durchschnittlichen Dicke von 7,5 cm. Ohne abdeckende Folie wurde die Schicht angehoben. Dabei verschob und bog sich die Schicht, wobei sie größer und dünner wurde, so dass eine Hülle in Form eines Kissens mit offenen Ecken entstand. Pro überbautem Quadratmeter fielen 1,5 Arbeitsstunden an.[11][14]
System nach Turner als Notunterkunft
In den 1970er Jahren wurden in Afrika Kuppelhäuser nach einer leicht abgewandelten Turner-Methode erstellt. Die Kuppel hatte keine Verstärkung durch Beton, Folie, UV-Schutzbeschichtung oder ähnliches. Es waren schnell produzierbare Notunterkünfte für Flüchtlinge, die für wenige Monate Einsatzzeit gedacht waren. Obwohl die Kuppeln keinen UV-Schutz hatten, wodurch die Oberfläche verwitterte und der Hartschaum versprödete, waren weitgehend erhaltene Exemplare noch in den 1980er Jahren bewohnt. Die Form der Kuppelhäuser erinnerte an die traditionelle Hütte der Zulu, der iQhugwane.
System nach Turner ohne nennenswerte Verstärkungsschicht für große Häuser
Der von Kuppelhäusern überzeugte Bob Masters baute 1979 sein erstes fast nur aus gesprühtem Hartschaum bestehendes Xanadu – Home of Tomorrow Musterhaus in Wisconsin Dells. Architekt Steward Gordon entwarf das aus gesprühtem Schaum mit wenig stabilisierender Beschichtung hergestellte Haus der Zukunft. In die weitgehend ungeglätteten Schaumwände waren teilweise Stützkonstruktionen einlaminiert. Größere Kuppeln wurden durch sichtbare baumähnliche Stützstrukturen stabilisiert. Bilderhaken wurden einlaminiert und für das Interieur wurde der Schaum auf ein Gerüst aus geformter Pappe gesprüht. Ein weiteres Xanadu Musterhaus eröffnete 1983 im Touristenort Kissimmee. Es wurde vom Architekten Roy Mason entworfen und lockte täglich bis zu 1000 zahlende Besucher an. Später eröffnete ein weiteres im Erholungsort Gatlinburg, Tennessee. Sie wurden irgendwann aufgegeben, sich selbst überlassen und bis 2005 abgerissen.[15][16][17]
In den Wäldern Floridas steht ein weiteres Haus aus weitgehend unverstärktem Hartschaum. Es wird vermutet, dass es von den Xanadu-Häusern inspiriert wurde. Die Innenwände und einige Schränke sind aus überstrichenem ungeglättetem Polyurethanschaum und wölben sich im unteren Bereich, als ob der gesprühte Schaum vor dem Aushärten nach unten gesackt wäre. An den häufig berührten Stellen ist der Schaum mit Fliesen oder Steinen verkleidet. Auch die überdachte Vorfahrt ist aus dickem Hartschaum. In den 80er Jahren war es noch bewohnt. 2017 war das Haus verlassen, aber existent.[18][19] [20]
Nicolo Binis Methode für komplexe Häuser
Seit ca. 2016 errichtet Nicolo Bini, Sohn von Dante Bini, Häuser nach einem veränderten Neff-System. Im Gegensatz zu seinem Vater konzentriert er sich auf kleinere Objekte in eckigeren Formen. Komplexere Innenraum-Formen werden nicht mehr mit mehreren Luftkissen nacheinander hergestellt, sondern mit einem einzigen komplex geformten Luftkissen in einem Durchgang. Die Moniereisen werden speziell für die angefertigt und mit Abstandshaltern an das aufgeblasene Luftkissen installiert, bevor Spritzbeton aufgebracht wird.[21]
Merkmale
Diese Baukonstruktion eignet sich sowohl für kalte als auch für warme Klimata. Sie spart Heizenergie und ist im Bau günstiger als ein konventioneller Massivbau aus Stahlbeton. Monolithic Domes gelten als sturmfest und dauerhaft. Verwendung finden sie als Wohnhaus, eignen sich jedoch auch für öffentliche Einrichtungen wie Schulen und Kirchen.
Siehe auch
Weblinks
- monolithic.com – Monolithic Dome Institute (englisch)
Einzelnachweise
- Benjamin Kromoser, Johann Kollegger: Pneumatische Schalungen im Brückenbau. Hrsg.: Institut für Tragkonstruktionen an der Technischen Universität Wien. Wien 12. Januar 2016 (tuwien.ac.at [PDF; 175 kB; abgerufen am 27. September 2020]).
- Benjamin Kromoser, Patrick Huber: Pneumatic Formwork Systems in Structural Engineering. In: Hindawi (Hrsg.): Advances in Building Technologies and Construction Materials 2016. (Special Issue of: Advances in Materials Science and Engineering). Band 2016, Nr. 4724036, 14. August 2016, doi:10.1155/2016/4724036 (englisch, hindawi.com [abgerufen am 27. September 2020]).
- Patent USA2335300: Building construction. Angemeldet am 25. November 1941, veröffentlicht am 30. November 1943, Erfinder: Wallace Neff.
- Patent USAD140060: Design for a house. Angemeldet am 1. April 1944, veröffentlicht am 16. Januar 1945, Erfinder: Wallace Neff.
- Patent USA2365145: Building construction. Angemeldet am 3. April 1941, veröffentlicht am 12. Dezember 1944, Erfinder: Wallace Neff.
- Patent USA2892239: Improved method of erecting shell-form concrete structures. Angemeldet am 19. Juni 1952, veröffentlicht am 30. Juni 1959, Erfinder: Wallace Neff.
- Lloyd S. Turner : spray foam dome form. In: SprayWorks website. SprayWorks Equipment Group, abgerufen am 28. September 2020 (englisch, Zitiert US-Patent 3.277.219 vom 4. Oktober 1966).
- Patent USA3277219: Method of molding a building structure by spraying a foamed plastic on the inside of an inflatable form. Angemeldet am 27. März 1961, veröffentlicht am 4. Oktober 1966, Erfinder: Lloyd S. Turner.
- Will Mclean: Skill : Inflatable Concrete Domes. In: The Architectural Review. Emap Publishing, 31. Januar 2013, abgerufen am 27. September 2020 (englisch).
- Dante Bini. (1978). Spacecity. Nicolo Bini. Abgerufen am 3. Oktober 2020. 15 min. (Videodokumentation über den Herstellungsprozess)
- Construction Automation – Part 1. In: Binisystems. Dante N. Bini, 2016, abgerufen am 3. Oktober 2020 (englisch).
- Binishell System. In: Binisystems. Dante N. Bini, 2016, abgerufen am 3. Oktober 2020 (englisch).
- Benjamin Kromoser, Johann Kollegger: Efficient construction of concrete shells by Pneumatic Forming of Hardened Concrete: Construction of a concrete shell bridge in Austria by inflation. In: International Federation for Structural Concrete (Hrsg.): Structural Concrete. Journal of the fib. Band 21, Nr. 1. John Wiley & Sons, Februar 2020, S. 4–14, doi:10.1002/suco.201900169 (englisch, wiley.com [abgerufen am 27. September 2020] Online-Veröffentlichung bereits am 29. August 2019).
- Minishell System. In: Binisystems. Dante N. Bini, 2016, abgerufen am 3. Oktober 2020 (englisch).
- Arran: The Xanadu House Project – The Futuristic Houses That Never Took Off. In: House & History. Arran, abgerufen am 20. Dezember 2020 (englisch).
- Greg LeMaire: AD Classics: Xanadu House / Roy Mason. In: Arch Daily. ArchDaily, abgerufen am 20. Dezember 2020 (englisch).
- Milica Sterjova: Xanadu Houses: a peculiar architectural design for a “home of the future”. In: Walls with Stories. Timera Inc., 23. September 2017, abgerufen am 20. Dezember 2020 (englisch).
- Darren Boyle: The 'home of the future' with a dismal past: House made from FOAM is rotting away in the Florida woods after becoming abandoned years ago. In: MailOnline. Associated Newspapers Ltd, 20. Februar 2017, abgerufen am 20. Dezember 2020 (englisch).
- Abandoned Spray Foam House. (The Urethane Blog). In: Everchem Specialty Chemicals. Everchem Specialty Chemicals, 21. Februar 2017, abgerufen am 20. Dezember 2020 (englisch, Vollzitat des Artikels aus MailOnline).
- Zoe Cassell: Forgotten ‘Home of the Future’. In: Media Drum World. Media Drum, Ltd., 21. Februar 2017, abgerufen am 20. Dezember 2020 (englisch).
- Shane Hedmond: Company Believes Bubble Inspired Buildings Can Change The Construction Industry. In: Construction Junkie. Construction Junkie, 2. März 2017, abgerufen am 3. Oktober 2020 (englisch).