Drehwerkzeug
Drehwerkzeuge sind Zerspanungswerkzeuge für das Fertigungsverfahren Drehen. Sie bestehen aus einem Schaft, der in der Drehmaschine eingespannt wird, einer Schneide für die Bearbeitung der Werkstücke und einem Werkzeug-Grundkörper, der Schaft und Schneide verbindet. Als Drehmeißel werden Drehwerkzeuge bezeichnet, bei denen die drei Komponenten aus einem einzigen durchgängigen Material bestehen (meist Schnellarbeitsstahl (HSS)) oder deren Schneiden auf den Körper aufgelötet sind (in diesem Fall meist Schneiden aus Hartmetall). Wenn die Schneiden verschlissen sind, werden sie nachgeschliffen (Werkzeugschleifen). Außerdem gibt es noch Klemmhalter bei denen Wendeschneidplatten in das Drehwerkzeug geklemmt oder geschraubt werden. Verschlissene Schneidplatten werden gewendet, um neue Kanten zum Eingriff zu bringen. Wenn sämtliche möglichen Kanten verschlissen sind, wird eine neue Platte eingespannt und die alte weggeworfen. Häufig werden auch sämtliche Drehwerkzeuge als Drehmeißel bezeichnet.
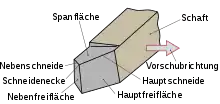
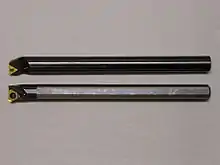
Mit den meisten Drehwerkzeugen wird die Form der Werkstücke erzeugt durch die Relativbewegung zwischen Werkzeug und Werkstück. Es gibt jedoch auch Werkzeuge, die zumindest teilweise die Form des Werkstücks als Negativ enthalten. Dazu zählen Gewindedrehmeißel, Gewindestrehler und Schneideisen mit denen genormte Gewinde gefertigt werden können. Außerdem gibt es noch Profildrehmeißel für das Profildrehen. Dabei handelt es sich meist um Sonderanfertigungen, bei denen aus HSS oder Hartmetall-Drehmeißeln die gewünschte Form in die Schneiden geschliffen wurde. Drehmeißel gibt es sowohl für die Außen- als auch für die Innenbearbeitung. Letztere werden teilweise auch als Bohrstange bezeichnet, wenn sie besonders lang sind.
Drehmeißel aus Schnellarbeitsstahl
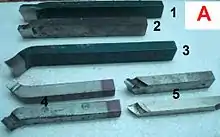
Drehmeißel aus Schnellarbeitsstahl (HSS) bestehen aus einem einzigen Stück. Sie können durchgehend aus HSS bestehen, mit einem vergüteten Schneidenteil oder der Schaft und Grundkörper bestehen aus einfachem Stahl mit einer angeschweißten Schneide aus HSS. Die Schäfte sind rechteckig oder quadratisch bei Werkzeugen für die Außenbearbeitung und rund oder vieleckig für die Innenbearbeitung. Ein wichtiges Unterscheidungsmerkmal für HSS-Drehmeißel ist der Grundkörper: er kann gegenüber dem Schaft gerade sein, gebogen oder abgesetzt. Die Form der Schneide hängt vom Drehverfahren ab: es gibt Werkzeuge für das Plandrehen, Runddrehen, Gewindeschneiden oder Abstechen.[1]
Normen für Drehmeißel aus HSS oder Hartmetall
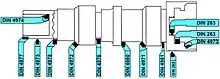
Die verschiedenen Formen sind in zahlreichen Normen geregelt. Meist existieren dieselben Formen sowohl für Werkzeuge aus HSS als auch aus Hartmetall. In Klammern sind die Normen für die Hartmetallwerkzeuge angeführt.[2]
- Gerader Drehmeißel: DIN 4951 (4971)
- Gebogener Drehmeißel: DIN 4952 (4972)
- Eckdrehmeißel: DIN 4965 (4978)
- Abgesetzter Stirndrehmeißel: k. A. (4977)
- Abgesetzter Seitendrehmeißel: DIN 4960 (4980)
- Breiter Drehmeißel: DIN 4956 (4976)
- spitzer Drehmeißel: DIN 4955 (4975)
- Stechdrehmeißel: DIN 4961 (4981)
- Innendrehmeißel: DIN 4953 (4973)
- Innen-Eckdrehmeißel: DIN 4954 (4974)
- Innen-Stechmeißel (auch Hakendrehmeißel): DIN 4963 (k. A.)
Drehmeißel mit gelöteten Hartmetallschneiden
Drehmeißel mit aufgelöteten Hartmetallschneiden ähneln denjenigen aus HSS. Die Formen und Verwendungszwecke sind grundsätzlich die gleichen. Schneiden aus Hartmetall sind härter und spröder. Sie sind verschleißfester, aber teurer. Daher bestehen die Körper immer aus einem günstigen Werkstoff und nur die Schneiden aus Hartmetall. Verschlissene Schneiden können nachgeschliffen werden mit Schleifscheiben aus Diamantkorn und Kunstharzbindung. Die Hartmetalldrehmeißel sind in der DIN 4982 genormt.[3]
Klemmhalter
Klemmhalter sind Drehwerkzeuge, in die eine Wendeschneidplatte als Schneide eingeklemmt oder geschraubt wird. Das aufwendige Nachschleifen kann bei ihnen entfallen. Die Schneiden können viel einfacher gewechselt werden, weshalb sie in der industriellen Praxis weit verbreitet sind. Sowohl die Schneidplatten als auch die Klemmhalter sind genormt, letztere in der DIN 4984.
Schneidplatten für Klemmhalter
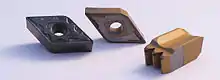
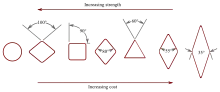
Sie sind genormt in der DIN ISO 1832 und werden mit einem Kurzzeichen benannt das aus 10 Stellen besteht:[4][5]
- Schneidplattenform: Es gibt runde, dreieckige, quadratische, rhomboide und vieleckige Plattenformen, die mit Buchstaben bezeichnet werden. Mit der Form wird auch zugleich der Eckenwinkel festgelegt.
- Der (Normal-)Freiwinkel der Platte. Er reicht von null Grad bis zu 30°. Sogenannte neutrale Platten mit einem Freiwinkel von null werden mit einem N bezeichnet. Bei ihnen lassen sich sowohl die Ober- als auch die Unterseite als Schneiden verwenden, sonst nur die Oberseite.
- Toleranz der Platte: Toleriert sind der Durchmesser des einbeschriebenen Kreises und die Dicke der Platte.
- Befestigung und Spanbrecher: Es gibt Platten mit mittiger Bohrung zum Festschrauben oder -klemmen und Platten ohne Bohrung. Die Bohrungen können zylindrisch oder angefast sein. Manche besitzen auf der Oberseite oder zusätzlich auf der Unterseite Spanbrecher.
- Schneidkantenlänge: Sie reichen von 3,97 bis 32 mm. Bei runden Platten wird der Durchmesser angegeben.
- Plattendicke: Sie reichen von 1,59 mm bis 9,52 mm.
- Eckenradius: Liegt zwischen 0 und 3,2 mm.
- Schneidkantenausführung: Es gibt scharfkantige Schneiden, die mit einer Rundung (Schneidkantenradius), mit Fasen, gefast und gerundet, doppelt gefaste sowie doppelt gefaste und gerundete Schneiden.
- Schneid- oder Schnittrichtung: Es wird unterschieden zwischen rechten, linken und neutralen Ausführungen. Die rechten Werkzeuge schneiden von rechts nach links. Neutrale lassen sich in beide Richtungen verwenden.
- Schneidstoff (Material):[6]
- Die einfachsten Platten bestehen aus Hartmetall. Es ist härter (und damit verschleißfester) und spröder als Schnellarbeitsstahl, aber weicher und zäher als andere Schneidstoffe. Es kann mit härteren Schneidstoffen beschichtet werden. Hartmetall ist universell einsetzbar.
- Cermet (ceramic metal): Bildet den Übergang zu den Schneidkeramiken und wird nur selten verwendet.
- Schneidkeramik: Es ist härter als Hartmetall, insbesondere auch bei hohen Temperaturen, weshalb es für die Hochgeschwindigkeitsbearbeitung und die Trockenbearbeitung (ohne Kühlschmiermittel) geeignet ist. Es ist jedoch auch spröder als Hartmetall und empfindlich gegen schwankende Temperaturen.
- Kubisches Bornitrid: Es ist nach Diamant der härteste Schneidstoff, verliert aber im Gegensatz zu Diamant seine Härte nicht bei hohen Temperaturen und ist auch chemisch beständig. Bornitrid wird bei besonders harten Werkstoffen eingesetzt (Hartzerspanen) oder bei Werkstoffen, die besonders harte Partikel als Einschlüsse enthalten, da diese sonst zu hohem Verschleiß führen würden.
- Diamant: Ist der härteste Schneidstoff und wird für die Bearbeitung von Nichteisenmetallen genutzt, darunter insbesondere Aluminium- und Kupferlegierungen. Diamant wird auch für die Hochpräzisionsbearbeitung dieser Werkstoffe genutzt, etwa für Spiegel. Die erreichbaren Genauigkeiten liegen bei Rz = 0,02 mm.
Befestigungsarten der Schneidplatten
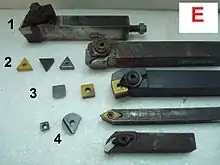
Es gibt mehrere Möglichkeiten die Schneidplatten in den Klemmhaltern zu befestigen.[7][8]
- Spannsystem C: Hier werden die Platten von oben mit einem Spannfinger festgeklemmt. Der Spannfinger selbst enthält eine Gewindebohrung und wird mittels einer Schraube auf die bohrungsfreie Platte gedrückt. Zwischen dem Spannfinger und der Platte kann sich auch eine verstellbare Spanleitstufe befinden. Diese Ausführung gilt als robust und leicht zu handhaben.
- Spannsystem M: Von oben über Spannfinger und zugleich über Bohrung. Die Platten enthalten eine zylindrische Bohrung. Der Spannfinger drückt sowohl von oben auf die Platte, als auch innerhalb der Bohrung auf die Seitenfächer der Bohrung und verhindert so ein Abheben und zugleich Herausrutschen der Platte.
- Spannsystem P: Nur über die Bohrung geklemmt. Die Platten enthalten eine zylindrische Bohrung. Ein Klemmhebel, der über eine Schraube geklemmt wird, drückt auf die Innenseite der Bohrung. Die Platten lassen sich damit besonders schnell wechseln.
- Spannsystem S: Über die Bohrung geklemmt mit einer Spannschraube. Die Platten verfügen über eine angefaste Bohrung, in die eine Schraube gedreht wird. Dieses System ist besonders einfach und kostengünstig und benötigt nur wenig Bauraum.
- Mit Spannfinger geklemmte Platte
- Mit Spannfinger und Bohrung
- Geschraubt
- Klemmhalter mit über Klemmhebel und Bohrung geklemmter Wendeschneidplatte und Werkzeug zum Schneidplattenwechsel
Normung der Klemmhalter
Ähnlich wie bei den Schneidplatten gibt es für die Klemmhalter ein System zur Bezeichnung.[9]
- Art der Klemmung
- Plattenform
- Halterform: Diese bestimmt den Werkzeug-Einstellwinkel.
- Freiwinkel der Platte
- Schnittrichtung: Links, Rechts oder Neutral.
- Schafthöhe
- Schaftbreite
- Werkzeuglänge
- Schneidkantenlänge
- Sonderformen, höhere Genauigkeiten oder herstellerspezifische Zeichen
Befestigung der Klemmhalter-Schäfte in der Maschine
Die Schäfte der Werkzeuge werden entweder direkt im Werkzeugschlitten eingespannt (einzelnes Werkzeug) oder in einem Werkzeugrevolver eingespannt, der mehrere Werkzeuge aufnehmen kann. Neben Drehwerkzeugen können dort auch angetriebene Werkzeuge eingespannt werden, beispielsweise Fräs- oder Bohrwerkzeuge. Es gibt Linear-, Stern-, Mehrkant-, Trommel-, Kronen- und Scheibenrevolver. Systeme für Vierkantschäfte sind in der DIN 4984 genormt, Systeme für runde Schäfte in der DIN 8025. Prismatische Schäfte die bei Großmaschinen verwendet werden, sind in der DIN 69880 genormt. Die Schaftsysteme sind dahingehend ausgelegt, dass sie die stabile Position der Schneide beibehalten – auch unter Last.[10]
Kurzklemmhalter
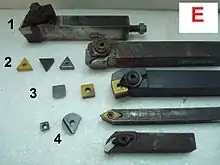
Kurzklemmhalter sind Klemmhalter, die hinten über eine Schraube zur Befestigung in der Maschine verfügen. Bei ihnen lässt sich die Plattenposition über Stellschrauben in Längs- und Querrichtung anpassen. Sie werden bevorzugt bei der Innenbearbeitung angewendet. Genormt sind sie in der DIN 4985.[11][12]
Schneidköpfe
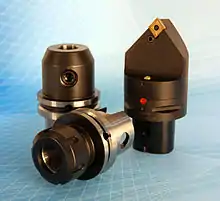
Schneidköpfe sind spezielle, herstellerabhängige (nicht genormte) Klemmhalter, die auf einen schnellen Werkzeugwechsel ausgelegt sind. Werkzeugwechselzeiten verhindern den Fertigungsfortschritt am Werkstück und bedeuten somit eine verringerte Produktivität. Schneidköpfe führen daher eine weitere Schnittstelle zur Maschine ein: Im Werkzeughalter wird ein Adapter montiert, in dem die eigentlichen Schneidköpfe schnell ein- und ausgebaut werden können. Diese Systeme sind möglichst kurz gehalten, um nur wenig Bauraum einzunehmen. Der Austausch kann manuell oder automatisch erfolgen. Schneidköpfe eignen sich für zahlreiche Bearbeitungen: Längs- und Plandrehen, Außen- und Innendrehen, Abstechen und Gewindedrehen. Da die Genauigkeit der Position der Werkzeugschneide auch von der Verformung des Halters abhängt, werden Schneidköpfe auf eine möglichst hohe Torsionssteifigkeit und Biegesteifigkeit ausgelegt.[13][14]
Multi-Task-Werkzeuge
Multi-Task-Werkzeuge sind Drehwerkzeuge, die an ihrem Ende mehrere Schneidplatten enthalten, und ähneln daher Werkzeugrevolvern. Multi-Task-Werkzeuge werden jedoch in Bohr- oder Frässpindeln eingespannt und sind daher für die Bearbeitung auf Bearbeitungszentren (Dreh-Fräs-Maschine) und Drehzelle gedacht. Die Frässpindel rotiert dabei derart, dass die gewünschte Schneide zum Eingriff kommt, und verharrt dann während der Bearbeitung in dieser Winkellage. Dadurch können einerseits die Werkzeugwechselzeiten reduziert werden und andererseits die Anzahl der benötigten Werkzeuge.[15]
Werkzeuge zur Gewindeherstellung
Für die Gewindeherstellung auf Drehmaschinen kommen mehrere Verfahren in Frage, die jeweils mit einem speziellen Werkzeug ausgeführt werden. Die Verfahren werden gemeinsam als Schraubdrehen bezeichnet. Das Gewindedrehen wird mit einem spitzen Drehmeißel durchgeführt dessen Spitzenwinkel dem Flankenwinkel des Gewindes entspricht. Gewindedrehmeißel bestehen aus Schnellarbeitsstahl oder Hartmetall und werden entweder als Vollprofilwerkzeug oder als Teilprofilwerkzeug angeboten. Bei letzteren wird das Drehteil zuvor auf den Durchmesser gedreht, der dem Außendurchmesser des Gewindes entspricht (bei Außengewinden). Bei Werkzeugen in Vollprofilausführung ist diese Vorarbeit nicht nötig, da diese nicht nur die Flanken, sondern auch die Außenkanten der Gewindegänge schneiden. Beim Gewindedrehen entspricht die Gewindesteigung dem Vorschub (mm pro Umdrehung). Meist sind mehrere Überläufe nötig.
Daneben gibt es noch Gewindestrehler. Bei ihnen liegen mehrere Profile nebeneinander, sodass nur ein einziger Überlauf nötig ist. Die Gewindesteigung ist bei Gewindestrehlern daher nicht variabel.
Mit Gewindeschneideisen und Schneidkluppen, bei denen in der Regel drei Schneiden (die wie Strehler mehrere Gewindegänge gleichzeitig schneiden) an verschiedenen Seiten des Umfangs zugleich angreifen, lassen sich Gewinde auch ohne den Einsatz einer Drehmaschine herstellen.
- Gewindedrehen (oben rechts und unten mitte)
- Wendeplatte zum Gewindedrehen mit drei Schneiden
- Gewindestrehler (rechts)
Werkzeugauswahl
Üblicherweise wird anhand des Rohteils und der herzustellenden Form zunächst das Drehverfahren (Längs-, Plandrehen etc.) ausgewählt. Anschließend wird noch entschieden, ob das Werkstück geschruppt (Grobbearbeitung) oder geschlichtet (Feinbearbeitung) werden soll. Dadurch wird die Anzahl der in Frage kommenden Werkzeuge stark eingeschränkt. Die Form der Schneiden und der Halter beeinflusst welche Formen herstellbar sind, das Schruppen/Schlichten beeinflusst die auftretenden Zerspankräfte und somit die Mindeststabilität der Schneide. Einen weiteren Einfluss hat die zur Verfügung stehende Maschinenleistung. Die Wahl des Spanwinkels und der Spanbrecher hängt auch vom Werkstoff ab. Weiche zum Verkleben neigende Werkstoffe werden eher mit positivem Spanwinkel bearbeitet, Werkstoffe mit hoher Festigkeit eher mit negativem.[16]
Weblinks
Einzelnachweise
- Pauksch: Zerspantechnik, 12. Auflage, S. 109.
- Pauksch: Zerspantechnik, 12. Auflage, S. 113.
- Pauksch: Zerspantechnik, 12. Auflage, S. 109.
- Schönherr: Spanende Fertigung. Oldenbourg, 2002, S. 76–78.
- Michel Köcher: Werkzeuge und Schneidstoffe zum Drehen, S. 166–168 in: Uwe Heisel, Fritz Klocke, Eckart Uhlmann, Günter Spur (Hrsg.): Handbuch Spanen. 2. Auflage, Hanser, München 2014.
- Michael Köcher: Werkzeuge zum Drehen, S. 169–171. in: Uwe Heisel, Fritz Klocke, Eckart Uhlmann, Günter Spur: Handbuch Spanen. 2. Auflage, Hanser, München 2014.
- Schönherr: Spanende Fertigung. Oldenbourg, 2002, S. 78 f.
- Michel Köcher: Werkzeuge und Schneidstoffe zum Drehen, S. 173 in: Uwe Heisel, Fritz Klocke, Eckart Uhlmann, Günter Spur (Hrsg.): Handbuch Spanen. 2. Auflage, Hanser, München 2014.
- Schönherr: Spanende Fertigung. Oldenbourg, 2002, S. 78–80.
- Michel Köcher: Werkzeuge und Schneidstoffe zum Drehen, S. 175 in: Uwe Heisel, Fritz Klocke, Eckart Uhlmann, Günter Spur (Hrsg.): Handbuch Spanen. 2. Auflage, Hanser, München 2014.
- Herbert Schönherr: Spanende Fertigung, Oldenbourg, 2002, S. 80.
- Michel Köcher: Werkzeuge und Schneidstoffe zum Drehen, S. 174 f. in: Uwe Heisel, Fritz Klocke, Eckart Uhlmann, Günter Spur (Hrsg.): Handbuch Spanen. 2. Auflage, Hanser, München 2014.
- Michel Köcher: Werkzeuge und Schneidstoffe zum Drehen, S. 176 in: Uwe Heisel, Fritz Klocke, Eckart Uhlmann, Günter Spur (Hrsg.): Handbuch Spanen. 2. Auflage, Hanser, München 2014.
- Herbert Schönherr: Spanende Fertigung, Oldenbourg, 2002, S. 80 f.
- Michel Köcher: Werkzeuge und Schneidstoffe zum Drehen, S. 175 in: Uwe Heisel, Fritz Klocke, Eckart Uhlmann, Günter Spur (Hrsg.): Handbuch Spanen. 2. Auflage, Hanser, München 2014.
- Michel Köcher: Werkzeuge und Schneidstoffe zum Drehen, S. 164 f. in: Uwe Heisel, Fritz Klocke, Eckart Uhlmann, Günter Spur (Hrsg.): Handbuch Spanen. 2. Auflage, Hanser, München 2014.