Tiefdruckzylinder
Mit Tiefdruckzylinder wird die Druckform für den Tiefdruck bezeichnet. Im Allgemeinen besteht die Druckform aus einem zylindrischen Stahlhohlkern, der mit einer aus Kupfer beschichteten Oberfläche bedeckt ist. In diese etwa 100 μm dünne Kupferschicht wird das Druckbild in Form von winzigen Näpfchen chemisch eingeätzt oder elektronisch eingraviert. Abschließend wird die Kupferschicht zusätzlich verchromt, um eine bessere Haltbarkeit für höhere Auflagen zu erreichen.
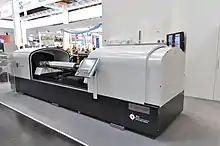
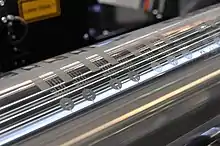
Zylinderherstellung
Der Grundzylinder besteht normalerweise aus einem Stahlhohlkern, der in einem elektrolytischen Bad zuerst mit Kupfer und nach dem Aufbringen der Bilddaten mit Chrom beschichtet wird. Dieser Vorgang erfolgt durch eine galvanische Bearbeitung des Tiefdruckzylinders. Die galvanische Produktionslinie besteht in der Regel aus dem Entfettungsbad, dem Kupferbad, dem Chrombad, dem Nickelbad und Entchromungsbad. Durch die Anbindung einer zentralen Chemie-Einheit an die Galvanikanlagen kann ein automatisches Befüllen der Bäder mit den entsprechenden Stoffen gewährleistet werden. Die Qualität des aufgetragenen Kupfers beeinflusst ganz wesentlich die Qualität der anschließenden Gravur.
Nach Beendigung des Drucks wird die Chrom- und Kupferschicht mechanisch abgetragen oder abgezogen. Zur Wiederverwendung wird die Zylinderoberfläche gereinigt und poliert. Danach erfolgt eine erneute Galvanisierung und der Zylinder kann wieder mit einer Gravur versehen werden.
Grundsätzlich besteht ein Tiefdruckzylinder nach allen Arbeitsgängen aus einem Stück. Es gibt jedoch auch Technologien, die den Aufbau des Zylinders in Schichten ermöglichen. Mit sogenannten „Sleeves“, die z. B. aus Aluminium bestehen können, wird ein Trägerkern ummantelt. Dieses System hat sowohl in ökonomischer als auch ökologischer Hinsicht Vorteile, da schnellere Wechsel möglich sind und weniger Material verbraucht wird. Nur der Sleeve wird gewechselt, die Zylinderkerne können weiter verwendet werden.
Eine ähnliche Methode ist die Ballardhaut. Dabei wird eine dünne Kupferschicht im Galvanikbad aufgebracht, die sich aufgrund einer vorherigen Behandlung des Basiszylinders mit Trennmitteln nicht fest mit diesem verbindet, sondern wieder abgezogen werden kann. Die Ballardhaut kann wie ein normaler Tiefdruckzylinder weiterbearbeitet werden und in den Druck gehen. Sie vereinfacht ebenfalls die Wiederverwendung des Basiszylinders.
Übertragung des Druckbilds
Die Übertragung des Druckbilds auf den Tiefdruckzylinder wird im allgemeinen Sprachgebrauch als Gravur bezeichnet. Das Druckbild, also Fotos, Texte, Grafiken, Bar-Codes, Sicherheitsmerkmale usw., wird in Form von Näpfchen in dem Druckzylinder geätzt oder graviert.
Bei der elektromechanischen Gravur (EMG oder E-Gravur) sind der Abtastzylinder und der zu gravierende Druckformzylinder mit einer Welle miteinander verbunden. Auf dem Abtastzylinder befindet sich ein sogenannter Opalfilm mit allen Bildinformationen, Texten und Strichzeichnungen. Dabei wird ein spezieller Diamantstichel verwendet, der mit bis zu 12.000 „Stichen“ pro Sekunde schwingt und die Näpfchen in die Kupferoberfläche graviert. Der Diamantstichel ist in einem Gravurkopf befestigt, der das Herzstück der Gravurmaschine (Helio-Klischograph) darstellt und über einen Verstärker von der Gravurmaschine angesteuert wird.
Die elektronische Lasergravur erreicht höhere Gravurfrequenzen, allerdings werden die Näpfchen nicht immer mit einem "Schuss" geformt. Insofern ist die Gravurfrequenz mit der Frequenz eines EMG-Systems nur sehr eingeschränkt vergleichbar. Je nach Verfahren wird eine Zinkoberfläche statt des Kupfers oder eine dickere Chromschicht benutzt, was eine Änderung des Galvanischen Prozesses bedingt. Grundsätzlich werden auch bei der Lasergravur Vertiefungen in die Zylinderoberfläche „gebrannt“, die abhängig von der Stärke des elektronischen Signals ein entsprechend größeres oder kleineres Volumen aufweisen. Die hohe Schreibauflösung von bis zu 2.540 dpi ermöglicht eine sehr hohe Konturenschärfe. Darum ist die Laserdirektgravur prädestiniert für Anwendungen in den Bereichen Etiketten, Sicherheitstechnik und hochqualitativen Verpackungen, beispielsweise Zigarettenverpackungen.
Im modernen Ätz-Prozess wird der Zylinder zuerst mit einer Lack- oder fotoresistenten Schicht überzogen, die anschließend mit einem Laser belichtet wird. Dadurch wird die Schicht an den Stellen entfernt, an denen die Näpfchen später erscheinen sollen. Die anschließende computerüberwachte Ätzung oder elektrolytische Kupferabtragung generiert die endgültigen Näpfchen. Im Gegensatz zur elektromechanischen Gravur und zur elektronischen Lasermethode ist die Ätzung nur eingeschränkt reproduzierbar und verschwindet deshalb mehr und mehr aus den modernen Arbeitsprozessen.
Anwendung
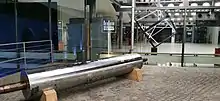
Für den typischen Illustrationstiefdruck werden heute ausschließlich Tiefdruckzylinder verwendet, die mit der Gravurmethode hergestellt wurden. Die Druckzylinder für fast alle großen Zeitschriften sowie für viele Kataloge, unter anderen die rund 160 Millionen Ikea-Kataloge weltweit, werden in dieser Art produziert. Dabei sind bis zu 16 Gravurköpfe auf einer Graviermaschine simultan in Betrieb. Jeder Gravurkopf deckt dabei die Breite einer Seite auf dem Zylinder ab, um Gravurzeit einzusparen.
Ein weiteres wichtiges Anwendungsgebiet ist die Verpackungsgravur bei Faltschachteln, Beutelverpackungen, Etiketten usw. Hier sind auf einer Graviermaschine maximal zwei Gravurköpfe im Einsatz. Das Verpackungslayout wird mehrfach auf einem so genannten „Ganzbogen“ angeordnet und dieser Bogen anschließend auf dem Tiefdruckzylinder reproduziert. Rastermarken und Schnittmarkierungen bestimmen die Bereiche, in denen später die gedruckten Verpackungen aus dem Bogen geschnitten oder gestanzt werden. Schließlich wird auch im Bereich Dekorpapiere (Möbelbeschichtungen, Bodenbeläge, Tapeten usw.) und beim Transferdruck (Dekorstoffe) hauptsächlich die elektromechanische Gravur auf Tiefdruckzylindern eingesetzt.
Literatur
- Helmut Kipphan: Handbuch der Printmedien. Springer, Heidelberg 2000, ISBN 3-540-66941-8.
- Bernd Ollech: Tiefdruck, Grundlagen und Verfahrensschritte der modernen Tiefdrucktechnik. Polygraph, Bielefeld 1999.