Scherkopf
Ein maschineller Scherkopf ist ein Bestandteil eines elektrischen Rasierers und setzt sich aus den Komponenten Klingen und Scherfolie zusammen. Dabei ist die Scherfolie fest angebracht während sich die Klingen als Klingenblock darunter bewegen.
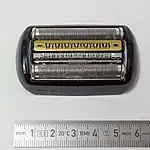
Moderne Scherköpfe besitzen einen komplexen Aufbau und bestehen oft aus mehreren kleineren Schereinheiten, die zusammengenommen einen starken Einfluss auf das Rasierverhalten nehmen. Einzelne Schereinheiten sind für sich flexibel gelagert, wodurch sich die Schereinheit als ganzes ergonomisch unterschiedlichen Gesichtsformen anpassen kann und ein gründlicheres Rasurergebnis erzielt.
Der Schervorgang wird maßgeblich durch die Scherpartner Klinge und Scherfolie beeinflusst. Auf die Rasur einflussnehmende Faktoren wie die Abnutzung, das Scherverhalten und mögliche Hautirritationen werden durch unterschiedliche Geometrien und die Materialauswahl bestimmt.[1]
Scherfolie
Geometrie
Moderne Scherfolien (2014) weisen eine ähnliche Sechskantlöcher-Struktur auf[2] wie historische Scherfolien (1959). Während die Struktur beim alten Modell über die gesamte Folie hinweg gleichmäßig ist, ist bei der Folie des aktuellen Modells eine Verzerrung des Musters nach außen hin vorhanden. Diese äußert sich sowohl in einer Verzerrung der Sechsecke als auch in einer teilweisen Reduktion auf fünf Ecken. Diese Geometrie erinnert an das Zusammenspiel von Fünf- und Sechsecken und sorgt für eine lückenlose Struktur wie die eines Fußballs (Ikosaederstumpf). Außerdem sind die Löcher der neuen Scherfolie wesentlich kleiner als früher.
Werkstoffe und Fertigung
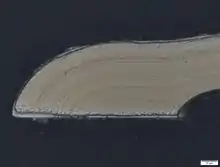
Scherfolien werden aus dem Werkstoff Nickel gefertigt. Diesbezüglich gab es in den letzten 50 Jahren keine Änderung. Die Verwendung ist im Zuge der Rasur und insbesondere der Nassrasur vor allem deshalb sinnvoll, da dieser Werkstoff eine hohe Korrosionsbeständigkeit gerade bei Kontakt mit Alkalien (Seifen) aufweist.[3][4] Die Scherfolie weist eine hohe Härte auf, die bei Nickelwerkstoffen vor allem durch Kaltumformungen erzeugt werden kann.[5] Eine hohe Härte ist für die Schnitthaltigkeit der Schneidekanten unerlässlich. Aufgrund der guten Kaltumformbarkeit und der hohen Duktilität[6] ist zu vermuten, dass die Folie zunächst als dünnes Blech gewalzt und anschließend durch einen Stanzvorgang in die endgültige Struktur gebracht wurde.
Zu bemerken ist die Verwendung von Nickel trotz einer großen Anzahl von Verbrauchern mit einer entsprechenden Allergie.[7] Begründen lässt sich dies mit den Vorteilen in der Fertigung und damit, dass der Hautkontakt mit Nickel erst ab einem Migrationslimit von 0,5 μg/cm²/Woche ein tatsächliches Risiko der allergischen Reaktion darstellt.[8] Des Weiteren besteht das Risiko lediglich bei Kontakt mit Schweiß, da dann Nickelionen freigesetzt werden und diese durch die Haut in den Körper gelangen.[9]
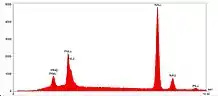
Ender der 1950er Jahre wurde die Scherfolie mit Edelmetall beschichtet, was unter dem Begriff "platinbeschichtet" werbewirksam eingesetzt wurde.[10] In einer energiedispersiven Röntgenspektralanalyse lässt sich jedoch feststellen, dass die Beschichtung aus den Elementen Platin und Palladium besteht. Der Anteil von Palladium ist höher als der von Platin.[1] Palladium wurde vermutlich eingesetzt, um die Herstellungskosten zu reduzieren. Die Beschichtung sorgt für eine erhöhte Kratzfestigkeit.[11] Möglicherweise wird aus Kostengründen bei den neueren Modellen auf eine Edelmetallbeschichtung komplett verzichtet.
Verschleiß
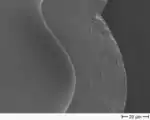
Die im Abschnitt Werkstoffe vorgenommene Analyse hinsichtlich der Beschichtung erklärt, warum die Oberfläche der neuen Folie im Vergleich zu dem älteren Modell einen erhöhten Verschleiß aufweist. In REM-Bildern ist zu erkennen, dass auf der Außenseite der Scherfolie von 1959 wesentlich weniger Kratzer vorhanden sind. Die erhöhte Kratzfestigkeit ist dabei auf den Werkstoff der Beschichtung zurückzuführen und nicht auf die Härte nach Vickers des Grundmaterials.[12] In der Prüfung des Querschliffs liegen mit 634 HV 0.05 beim neueren Modell und 595 HV 0.05 beim älteren die Härtewerte in der gleichen Größenordnung. Eine höhere Härte durch die Beschichtung ist nicht festzustellen, da diese mit weniger als 1 μm Stärke sehr dünn ist.[1]
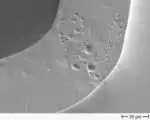
Auf den Innenseiten der beiden Modelle sind jeweils Riefen in Bewegungsrichtung der Klingen zu erkennen, welche auf die direkte Interaktion von Klinge und Folie beim Schervorgang hinweisen. Bei näherer Betrachtung der Sechskantlöcher fällt auf, dass die Abnutzung in den Ecken im Vergleich zu den Stegen vermehrt auftritt. Dies lässt sich auf das Zusammentreffen von Haar, Scherfolie und Klinge in der Ecke zurück führen.[1]
Klingen
Geometrie
Bei einem untersuchten Rasierapparat aus dem jahre 1959 wurden 24 Klingen mit rechteckigem Querschnitt in einen Block aus Metall eingebettet. Diese sind nicht senkrecht zur Scherrichtung angeordnet, sondern leicht angewinkelt. Der wesentlich kleinere Rasierblock aus dem Jahr 2014 wird als ein Gussteil produziert und besteht aus 31 einzelnen Klingen. Diese haben einen trapezförmigen Querschnitt mit konkav ausgeformten Seitenflächen und stehen senkrecht zur Bewegungsrichtung.
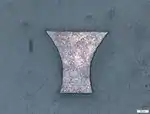
Während die Klingenradien mit etwa 1,5 μm bei beiden Modellen gleich sind zeigen sich deutliche Unterschiede beim Vergleich der Schnittwinkel, die vermutlich maßgeblichen Einfluss auf das Rasurergebnis haben. Mit einem Winkel von ca. 55° kann man bei der neueren Klinge von einem schneidenden Abscheren der Barthaare sprechen, wohingegen bei der älteren Klinge mit einem Winkel von ca. 90° eher ein stumpfes Abscheren stattfindet.[1]
Werkstoffe und Fertigung
Bei den in der Mitte des 20. Jahrhunderts gefertigten Klingenblöcken wurde für die Klingen ein Chromstahl, verwendet. Im Zuge eines Druckgussverfahrens wurden die Klingen in einer tertiären Aluminium-Silicium Legierung eingebettet. Diese weist ausgezeichnete Eigenschaften in der Gießbarkeit auf.[13] Im geätzten Schliff zeigt sich in der AlSi Legierung ein unregelmäßiges, zweiphasiges Mischgefüge.
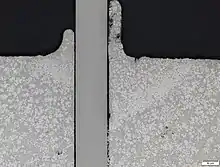
Während des Druckgussvorgangs wird die Wärme des Aluminiumblocks vom flüssigen Inneren nach außen abgeleitet. Durch diesen Wärmefluss wird die Abkühlung des gegossenen Materials beeinflusst, was sich im Gefüge zeigt. Durch äußere Abkühlung am Materialüberschuss, der teilweise seitlich an den Klingen vorzufinden ist, kühlt dieser Bereich sehr schnell ab und es entsteht ein ungeordnetes Gefüge mit wenig Diffusionsvorgängen beim Erkalten. Ergebnis ist ein ungeordnetes, kleinkörniges Gefüge. Benachbart bildet sich ein V-förmiger Bereich aus Aluminiumkörnern. Dort liegt eine ausgeprägte Dendritenstruktur vor, deren Entstehung auf eine geringere Abkühlgeschwindigkeit schließen lässt.[13] Aufgrund der verlangsamten Erstarrung liegen im dritten Bereich größere Aluminiumkörner in einer Matrix aus einer AlSi-Phase vor. Im Härteverlauf nach Vickers des martensitischen Klingenquerschnitts, der von einem Härtewert von 600 HV 0.05 im Innern bis zu einem Wert von 683 HV 0.05 im äußeren Bereich der Klinge liegt, ist ein Anlasseffekt des Stahls durch den Druckguss vorzufinden.[1]
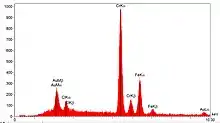
Durch die Schwindung des Aluminiums beim Erkalten entstehen Hohlräume zwischen Klinge und AlSi-Fassung, sodass nur noch partiell Kontakte zwischen den Komponenten vorhanden sind und somit eine unzureichende Verbindung vorhanden ist. Dies kann im Laufe der Benutzung zu Bauteilversagen führen. In der Weiterentwicklung zeigt sich für eine Klinge aus dem Jahr 2014 eine Optimierung dieser Problemstellung durch Reduktion auf ein Bauteilelement in der Scherklinge. Trotz einer geringen Materialstärke von etwa 0,3 mm handelt es sich bei dieser Klinge um ein Gussteil, wie in dem geätzten Querschliff und der Seitenansicht zu sehen ist. Das harte martensitische Gefüge (720 HV 0.05) weist in beide Richtungen dieselbe Struktur auf und gibt somit Aufschluss über den beschriebenen Fertigungsprozess.[1] Die Verhältnisse der Peaks im EDX Spektrum sind denen, des Werkstoffs X153CrMoV12 sehr ähnlich.[14] Aufgrund der hohen Karbiddichte im Gefüge ist der Werkstoff besonders widerstandsfähig gegenüber adhäsiven und abrasiven Verschleiß und eignet sich daher gut für Feinschneidwerkzeuge. Zudem ist der Werkstoff – einmal in Form gegossen – maßänderungsarm und eignet sich gut für eine anschließende Beschichtung.[14] Eine solche zusätzliche Veredlung in Form einer dünnen Chrom-Hartbeschichtung ist im Bild aus dem REM sowie als Peak im EDX Spektrum sichtbar. Auch im Querschliff ist diese Schicht von etwa 1 μm zu erkennen.[15][1]
Verschleiß
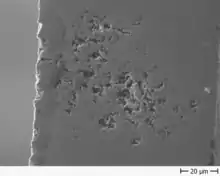
Bei näherer Betrachtung der beiden Klingen, weist die aus dem Jahr 1959 einen vergleichsweise höheren Verschleiß auf als die aus dem Jahr 2014. Die Mängel der älteren Klinge sind an tieferen Kratzern und bröseligen Stellen, die vermutlich auf Korrosion zurückzuführen sind, festzumachen.
Auf der Oberfläche der neueren Klinge sind lediglich Schleifspuren und leichte Kratzer zu erkennen. Schwerwiegendere Abnutzungsspuren werden vermutlich durch die oben genannten Materialeigenschaften verhindert. Im Härtevergleich der beiden Klingen ergeben sich nur geringfügige Unterschiede (683 HV 0.05 – Klinge 1959; 720 HV 0.05 – Klinge 2014 bei Härteprüfung des Grundwerkstoffs im Querschliff), weshalb der Großteil der Abnutzung auf die fehlende Hartchromschicht und den niedriger legierten Werkstoff beim Modell von 1959 zurückzuführen ist.[1]
Einzelnachweise
- Werkstoffkundliche Untersuchungen an Braun SM3 und Braun Series 9 am WAM der TH Köln Campus Gummersbach
- Gert Redlich: Max Brauns Rasierer - Teil 5. In: Hifimuseum. Artur Braun, Januar 2014, abgerufen am 31. Mai 2018.
- Pure Nickel & Other Alloys. In: Nickel Institute. Nickel Institute, abgerufen am 31. Mai 2018 (englisch).
- Peter Rauch: Die Eigenschaften und Verwendung von Nickel und seine Legierungen. Abgerufen am 31. Mai 2018.
- Heinrich Oettel, Hermann Schumann: Metallografie. Hrsg.: Heinrich Oettel, Hermann Schumann. 15. Auflage. WILEY-VCH, Weinheim 2011, ISBN 978-3-527-32257-2, S. 371.
- Heinrich Oettel, Hermann Schumann: Metallografie. Hrsg.: Heinrich Oettel, Hermann Schumann. 15. Auflage. WILEY-VCH, Weinheim 2011, ISBN 978-3-527-32257-2, S. 789 f.
- Nickelfrei.de: Verbreitung :: Nickelfrei.de - Das Informationsportal für Nickelallergiker. Abgerufen am 31. Mai 2018 (englisch).
- Verordnung (EG) Nr. 1907/2006 (PDF)
- Nickelfrei.de: Definition :: Nickelfrei.de - Das Informationsportal für Nickelallergiker. Abgerufen am 31. Mai 2018 (englisch).
- Die WELT (Hrsg.): Die WELT - Ausgabe vom 03.12.1968. Nr. 282, 3. Dezember 1968, S. 5.
- Platin-Beschichtung und Palladium-Beschichtung | surpro. Abgerufen am 31. Mai 2018.
- Norm DIN EN ISO 4957 - Werkzeugstähle. DIN, 31. März 2017.
- Heinrich Oettel, Hermann Schumann: Mettalografie. Hrsg.: Heinrich Oettel, Hermann Schumann. 15. Auflage. WILEY-VCH, Weinheim 2011, ISBN 978-3-527-32257-2, S. 818 ff.
- Dörrenberg Edelstahl GmbH: Werkstoff-Nr 1.2379. (PDF) In: Dorrenberg.es. Dörrenberg-Edelstahl GmbH, abgerufen am 7. Juni 2018.
- Hartchrom | Ernst Meuter GmbH & Co. KG. Abgerufen am 8. Juni 2018 (deutsch).