Reaktives Ionentiefenätzen
Reaktives Ionentiefenätzen (englisch deep reactive ion etching, DRIE), eine Weiterentwicklung des reaktiven Ionenätzens (RIE), ist ein hoch anisotroper Trockenätzprozess für die Herstellung von Mikrostrukturen in Silicium mit einem Aspektverhältnis (Verhältnis von Tiefe zu Breite) von bis zu 50:1, wobei Strukturtiefen von einigen 100 Mikrometern erreicht werden können. Dies wird beispielsweise für die Herstellung von Silizium-Durchkontaktierungen eingesetzt/benötigt. Es gehört zu den Verfahren des Plasma-unterstützten Ätzens.
Geschichte
Das reaktive Ionentiefenätzen wurde ursprünglich Anfang der 1990er Jahre von Franz Lärmer und Andrea Schilp in Form eines Trockenätzprozesses für Silicium entwickelt. Sie waren Angestellte der Robert Bosch GmbH, deren Vermarktung des Prozess-Patents dazu führte, dass sich die Bezeichnung Bosch-Prozess als Synonym für das reaktive Silicium-Ionentiefenätzen einbürgerte.[1] In den folgenden Jahren wurde das ursprüngliche Verfahren mit den Kooperationspartnern Surface Technology Systems Plc. (STS) und Alcatel Vacuum Technology weiterentwickelt. Außerdem wurde die benötigte Anlagentechnik verfeinert, an den Prozess angepasst und kommerziell vertrieben. So vermarktet STS seit einigen Jahren einen verbesserten Prozess zusammen mit der Anlagentechnik unter dem Namen Advanced Silicon Etching (ASE).
Prozessbeschreibung
Aspektverhältnis (Tiefe:Breite) | bis 50:1 |
Flankenwinkel | 90° ± 2° |
Ätzrate | (max.)20 µm/min (standard) 1–2 µm/min |
Oberflächenrauhigkeit | 10 nm |
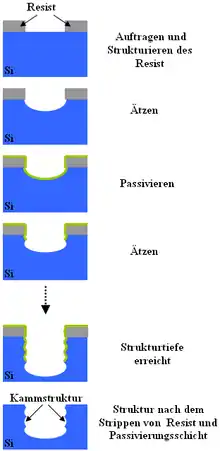
Der DRIE-Prozess ist wie der ursprüngliche Bosch-Prozess ein zweistufiger, alternierender Trockenätzprozess, bei dem sich Ätz- und Passivierungsschritte abwechseln. Ziel ist es, möglichst anisotrop zu ätzen, das heißt richtungsabhängig, senkrecht zur Wafer-Oberfläche. Auf diese Weise können beispielsweise sehr schmale Gräben geätzt werden.
Die Prozesse lassen sich wie folgt zusammenfassen. Zunächst wird der Silicium-Wafer maskiert, beispielsweise mit Fotolack oder mit einer Hartmaske aus Siliciumdioxid, Siliciumnitrid und anderen Stoffen, die jene Stellen des Wafers abdeckt, die nicht geätzt werden sollen. Anschließend beginnt der eigentliche Ätzprozess. Dazu wird Schwefelhexafluorid (SF6) in einem Trägergas (meist Argon) in den Reaktor mit dem darin befindlichen Substrat eingeleitet. Durch Erzeugen eines energiereichen Hochfrequenzplasmas entsteht aus dem SF6 ein reaktives Gas. Zusammen mit der Beschleunigung der Ionen in einem elektrischen Feld wird eine chemische isotrope Ätzreaktion durch aus SF6 gebildete Radikale und ein physikalischer anisotroper Materialabtrag durch Sputtern mittels Argon-Ionen überlagert.
Der Ätzprozess wird nach kurzer Zeit gestoppt und ein Gasgemisch aus Octafluorcyclobutan (C4F8) und Argon als Trägergas eingeleitet; auch andere Gasgemische sind möglich, beispielsweise CF4/H2. Im Plasma des Reaktors wird Octafluorcyclobutan aktiviert und bildet auf dem gesamten Substrat eine Polymer-Passivierungsschicht, das heißt sowohl auf der Maske als auch auf dem Boden und den vertikalen Seitenwänden des Grabens/Lochs. Auf diese Weise werden die Seitenwände im Folgenden vor weiterem chemischen Materialabtrag geschützt, um die Anisotropie des Gesamtprozesses zu gewährleisten. Denn durch den anschließend wiederholten Ätzschritt mit SF6 wird die Passivierungsschicht der horizontalen Flächen (Grabenboden) durch die gerichtete physikalische Komponente (Ionen) der Ätzreaktion deutlich schneller entfernt als die Schicht an den Seitenwänden.
Beide Schritte werden nun so lange wiederholt, bis die gewünschte Bearbeitungstiefe erreicht ist. Wichtig ist dabei die Balance zwischen dem Ätz- und Passivierungsschritt. Wird beispielsweise die Polymerschicht zu dick aufgetragen, wird ein Großteil des Ätzgases und der Prozesszeit für den Abtrag des Polymers am Grabenboden verwendet, was zu höheren Prozesskosten führt. Wird die Schicht jedoch zu dünn aufgetragen oder ist das elektrische Feld für den Ionentransport zum Substrat zu gering gewählt, werden die Seitenwände zu stark geätzt.
Die Prozessparameter haben auch entscheidenden Einfluss auf die Struktur der Seitenwände; diese sind aufgrund des alternierenden Prozessablaufs in der Regel nicht glatt, sondern leicht gewellt. Die Stärke der Wellen kann jedoch durch geeignete Wahl der Prozessparameter minimiert werden, so dass sie die nachfolgenden Prozesse in der Herstellung nicht negativ beeinflusst.
Nach dem Ätzen müssen abschließend das Maskenmaterial (das ebenfalls teilweise geätzt wird) und die Passivierungschicht an den Grabenwänden entfernt werden.
Ein Nachteil des Verfahrens sind die im Vergleich zum Nassätzen sehr hohen Anlagenkosten sowie der geringe Fertigungsdurchsatz.
Neben dem alternierenden Prozess gibt es auch das Verfahren des gleichzeitigen Ätzens und Passivierens, ein sogenannter kontinuierlicher Prozess.
Anwendungsbereiche
Hauptanwendungsgebiet ist die Herstellung von Mikrosystemen.[2] Durch Anwendung verschiedener Maskenstoffe können mehrere Tiefenebenen realisiert werden, deren Zahl jedoch aufgrund des hohen Aufwandes sehr beschränkt bleibt (2½-D-Strukturen).
Weitere Anwendungsgebiete finden sich in der Halbleitertechnik, beispielsweise für die Fertigung von tiefen „Gräben“ für den Speicherkondensator bei einigen DRAM-Technologien oder für das Isolationsoxid in der Grabenisolation (wobei hier keine hohen Aspektverhältnisse benötigt werden).
In den letzten Jahren rückt eine weitere mögliche Anwendung in den Mittelpunkt des Interesses: Für eine 3D-Integration von Schaltkreisen, das heißt eine Stapelung von Bauelementen (z. B. Transistoren und Leiterbahnen) ist es notwendig, leitfähige Kanäle durch das (abgedünnte) Siliciumsubstrat zu erzeugen. Diese Kanäle müssen ein (extrem) hohes Aspektverhältnis von mehr als 50:1 aufweisen und werden daher mit reaktivem Ionentiefätzen hergestellt und anschließend mit Kupfer gefüllt.
Weblinks
- Mikrostrukturtechnik-Vorlesung an der Universität Uppsala. (Nicht mehr online verfügbar.) In: Universität Uppsala. Archiviert vom Original am März 2007 (schwedisch).
Literatur
- W. Menz, J. Mohr: Mikrosystemtechnik für Ingenieure. VCH-Verlag, Weinheim 1997, ISBN 3-527-30536-X.
- F. Laermer, A. Urban: Challenges, developments and applications of silicon deep reactive ion etching. In: Microelectronic Engineering. Band 67–68, Juni 2003, S. 349–355, doi:10.1016/S0167-9317(03)00089-3.
Einzelnachweise
- Patent DE4241045C1: Verfahren zum anisotropen Ätzen von Silicium. Angemeldet am 5. Dezember 1992, veröffentlicht am 26. Mai 1994, Anmelder: Robert Bosch GmbH, Erfinder: Franz Lärmer, Andrea Schilp.
- Fünf Milliarden MEMS-Sensoren von Bosch. In: bosch-presse.de. 18. Februar 2015, abgerufen am 3. April 2020.