Mitteldichte Holzfaserplatte
Die mitteldichte Holzfaserplatte oder mitteldichte Faserplatte, kurz MDF-Platte, ist ein Holzwerkstoff aus dem Bereich der Faserplatten. Das Produkt wurde in den USA erfunden und fand in Europa Ende der 1980er-Jahre eine größere Verbreitung. Der Verwendungsbereich ähnelt dem von Spanplatten.
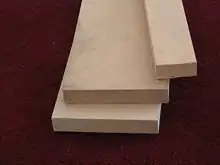
Fein zerfasertes, hauptsächlich rindenfreies Nadelholz wird zu einem in Längs- und Querrichtung gleichermaßen homogenen Holzwerkstoff verpresst. Die Kanten sind glatt und fest und können ohne besonderen Anleimer profiliert werden. Im Handel sind Dicken von 2 mm bis 60 mm mit Dichten von 600 kg/m³ bis 1000 kg/m³ erhältlich. MDF-Platten besitzen in alle Richtungen ähnliche Quell- und Schwindeigenschaften, haben aber eine wesentlich geringere Festigkeit als Vollholz.
Zusammensetzung
Je nach Verwendungszweck werden MDF-Platten mit Zusatzstoffen behandelt. Folgende Angaben sind in etwa für eine MDF-Möbelplatte, welche entsprechend der Emissionsklasse E1 mit einem Urea-Formaldehyd-Leim (UF-Leim) hergestellt wurde, gültig: 80 bis 83 Prozent Holz, 9 bis 10,5 Prozent Leim, 0,5 bis 2,5 Prozent Zusatzstoffe und 6 bis 8 Prozent Wasser.
Holz
Verschiedene Holzarten werden verwendet, neben den Klassikern Kiefer, Fichte und Buche sind es inzwischen auch Eucalyptus, Birke, Pappel, Akazie und viele mehr. Entscheidend ist eher der Preis der Holzsorten als deren Eignung für eine optimale Produktion.
Klebstoffe
Zumeist werden Harnstoff-Formaldehyd-Harze (Harnstoffharze, Urea-Formaldehyde UF) zur Beleimung eingesetzt. Diese Harze können mit Melamin oder Phenol verstärkt sein, um die Feuchtebeständigkeit der Leimverbindung zu verbessern. Nur in seltenen Fällen werden Isocyanate (Polymeres Diphenylmethandiisocyanat – PMDI) als Leimsystem eingesetzt. In neueren UF-Leimsystemen wird der molare Anteil an Formaldehyd gegenüber dem Harnstoff immer weiter reduziert, um die gesetzlichen Vorgaben bezüglich der Formaldehydemissionen von Holzwerkstoffen (Klasse E1, E2 in Europa[1], CARB in den USA[2] bzw. F**** („F-4-Star“) in Japan) einhalten zu können.
Zusatzstoffe
Zusatzstoffe werden aus unterschiedlichen Gründen eingesetzt. Paraffin, welches den größten Anteil der Zusatzstoffe ausmacht, wird in Form von Schmelzwachs oder Paraffinemulsion eingesetzt, um die Quelleigenschaften der Platte zu verbessern. Harnstoff wird zum Teil bei den klassischen Formaldehydleimen als Fänger eingesetzt, um die Formaldehydemissionen der Platte zu reduzieren. Ammoniumsulfat oder auch Ammoniumnitrat werden als Härter für eine schnellere Abbindung von Formaldehydleimen eingesetzt. Farben werden häufig zur Kennzeichnung besonderer Eigenschaften wie Quellvergütung oder Brandschutzvergütung zugesetzt, können jedoch ebenso aus dekorativen Gründen in Form einer vollständigen Durchfärbung eingesetzt werden. Bei Bedarf kommen weitere Chemikalien zum Einsatz, welche aufgrund der Kosten nur bei Erfordernis eingesetzt werden.
Fungizide oder Insektizide werden zum Teil eingesetzt, um die MDF-Platten gegen Insekten- oder Pilzbefall zu schützen. Hierfür kommen zumeist chrom- oder borhaltige Chemikalien zum Einsatz. Durch andere Zusatzstoffe behandelte MDF genügen in Deutschland den Baustoffklasse B1 nach DIN 4102 Teil 4 und gelten als schwer entflammbar. Daneben können zahlreiche weitere Zusatzstoffe zur Anwendung kommen.
Wasser
Holzwerkstoffplatten sind hygroskopisch und quellen daher bei Feuchtigkeit auf.
Herstellung
Für die Herstellung von Faserplatten wird das Holz zunächst zerfasert, beleimt und anschließend zu Platten gepresst.
Aufbereitung
Als Rohstoffe für die Holzfaserherstellung werden überwiegend Rundholz (Stammholz), Hackschnitzel, Schwarten und in geringerem Maße Altholz, Restrollen der Schälfurnierherstellung, Furnierreste und Sägespäne verwendet.
Hackschnitzelerzeugung
Rundholz wird in den meisten Fällen entrindet und in Scheibenhackern oder wie auch die Schwarten oder Altholz in Trommelhackern zu Hackschnitzeln zerkleinert. Die Hackschnitzel werden vor der Weiterverarbeitung zunächst sortiert (gesiebt) und zumeist nass oder trocken von Sand und Steinen gereinigt. Rindenabfälle und Holzabfälle werden zumeist zwischengelagert und später zur thermischen Energieerzeugung in der Anlage genutzt.
Hackschnitzellagerung
Ein Lager für die erzeugten Hackschnitzel ist erforderlich, um eine kontinuierliche Versorgung der Produktionsanlage mit Holz zu gewährleisten. Die Größe des Lagers ist abhängig von der zu erwartenden Dauer der Zufuhrunterbrechung von der Hackschnitzelerzeugung. Unterbrechungen können z. B. durch Messerwechsel am Hacker entstehen, Verbote zur Hackschnitzelerzeugung aufgrund von Lärmemissionen in der Nacht, an Wochenenden und so weiter. Die Hackschnitzel können entweder automatisch über Schnecken oder Schubbodenanlagen oder aber mit Fahrzeugen aus dem Lager entnommen und dem nachgeschalteten Prozess zugeführt werden.
Reinigung
In vielen Anlagen werden die Hackschnitzel von Fremdstoffen gereinigt, indem sie einer maschinellen Reinigung zugeführt werden. Hierbei unterscheidet man die „Trockenreinigung“ von der „Nassreinigung“. In der Trockenreinigung werden die Hackschnitzel mit Hilfe von Luft von Schwerkörpern befreit. In der Nassreinigung erfolgt die Trennung von Steinen, Sand und Metallen von den Hackschnitzeln in Wasser.
Zerfaserung
Anschließend gelangen die Hackschnitzel zur hydrothermischen Vorbehandlung in einen Vordämpfbehälter, wo sie drucklos und unter einer Temperatur von bis zu 100 °C „vorgedämpft“ werden. Durch diese Behandlung werden die Mittellamellen der Holzzellen erweicht, was die Kompressionsfähigkeit der Hackschnitzel und auch später die Zerfaserung begünstigt. In den Kocher gelangen die teilweise plastifizierten Hackschnitzel über den Vibrationsaustragsboden und über die Stopfschnecke. An dieser Stelle werden meist auch erst die Sägespäne in den Prozess gegeben. Die Steigung der Schneckenwendel verringert sich kontinuierlich, wodurch sie die Hackschnitzel zu einem relativ druckdichten Pfropfen komprimiert. Hierbei wird das sogenannte Quetschwasser aus den Hackschnitzeln gepresst. Mit diesem Pfropfen findet die Abdichtung zum Kocher statt. Hier werden die Hackschnitzel bei einem Dampfdruck (je nach Holzart und Anforderung an die Fasern) zwischen 6 und 10 bar „gekocht“. Im Kocher bleiben die Hackschnitzel etwa zwei bis vier Minuten, bevor sie durch eine Förderschnecke (Austragsschnecke) und über die Einspeiseschnecke in den Refiner (Zerfaserer) kommen.
Im Refiner rotieren relativ zueinander zwei gerillte Mahlscheiben mit einem geregelten Abstand von etwa 0,1 mm. Man unterscheidet zwischen Einscheibenrefinern mit nur einer drehenden Scheibe und Doppelscheibenrefinern, bei denen sich beide Scheiben drehen. Zwischen diese Scheiben gelangen die erweichten Hackschnitzel unter dem Druck der Förderschnecke und werden aufgemahlen. Der zerfaserte Stoff wird aus dem Refiner über ein regelbares „Blasventil“ durch die „Blasleitung“ herausgeblasen. Im Refiner befinden sich ebenfalls 6 bis 10 bar Dampfdruck. Der Dampf bildet das Transportmittel für die Fasern auf ihrem Weg durch die Blasleitung in den Trockner.
Trocknung
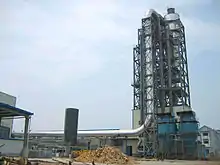
Nach der Zerfaserung wird der Faserstoff – im Gegensatz zu Spänen – mit (zumeist direkt mit Rauchgasen oder Brennern beheizten) Stromtrocknern getrocknet. Der Faserstoff wird in den heißen Abgasstrom gegeben und bei der pneumatischen Förderung im Trocknungskanal getrocknet. Seltener werden auch andere Systeme mit indirekter Beheizung (Lufterwärmung über Dampf- oder Thermalöl-Wärmetauscher) eingesetzt. Am Ende wird der Faserstoff mit etwa 8 bis 12 Prozent Holzfeuchte (atro) in Zyklonen vom Luftstrom abgeschieden. Bei der Trockenbeleimung (s. u.) werden die Fasern bis auf ca. 2 Prozent (atro) getrocknet.
Beleimung
Es werden drei Verfahren der Beleimung unterschieden:
- Mischerbeleimung
- ältestes Verfahren, führt jedoch zu so genannten „Leimflecken“,
- Blow-Line-Beleimung
- derzeit häufigstes Verfahren, keine Leimflecken, jedoch erhöhter Leimbedarf,
- Trockenbeleimung
- modernstes Verfahren, niedrigerer Leimbedarf, höhere Investitionen und höhere Betriebskosten.
Mischerbeleimung
Nach dem Trocknen wird der Faserstoff in einem Bunker gesammelt und anschließend in einem Mischer beleimt. Die Leimflotte muss gleichmäßig unter die Fasern gemischt werden, wozu umlaufende Wellen mit Mischarmen, auch Paddel genannt, das Gut durchmischen, während der Leim entweder direkt durch die Außenwand in den Trog oder am Ende der Paddel eingegeben wird. Vor der Untermischung wird der Leim aufbereitet, indem in die Leimflotte gleichbleibende Anteile der verschiedenen Komponenten gegeben und vermischt werden. Das Leimsystem darf dabei noch nicht aushärten, sondern erst durch die Aktivierung unter der Hitze in der Presse vernetzen, weshalb auch gekühlte Mischer eingesetzt werden. Je nach System wird der beleimte Faserstoff nun noch einmal in einem erwärmten Luftstrom transportiert, um die mit dem Leim eingebrachte Zusatzfeuchte wieder abzutrocknen. Nach der Beleimung gelangt das Gemisch mit einer Faserstofffeuchte von 9 bis 11 Prozent zur Formstation.
Blow-Line-Beleimung
Bei einer Blow-Line-Beleimung wird die Leimflotte direkt in der Blowline in den Faserstrom eingespritzt. Die leichte Aushärtung des Leimes an der Faseroberfläche und an der Leimtropfenoberfläche wird in Kauf genommen, da beim Pressen noch genügend flüssiges Material zur Verfügung steht. Dieses Verfahren führt zu einer sehr homogenen Leimverteilung. Allerdings wirkt sich die thermische Beanspruchung des Leimes im Trockner auf die „Restfestigkeit“ des Leimes aus, was letztlich zu einem höheren Leimverbrauch führt.
Trockenbeleimung
Diese stellt das modernste Verfahren dar, ist jedoch bisher nur in wenigen Anlagen realisiert. Dabei wird der Leim auf die getrockneten Fasern durch extrem feines Verdüsen aufgebracht. Da der thermisch intensive Trocknungsprozess im Wesentlichen vor der Beleimung stattfindet, ist der Leimverbrauch deutlich geringer als bei der Blow-Line-Beleimung bei weitgehend homogener Leimverteilung. Auch bei diesem System ist eine Nachtrocknung erforderlich, um die mit dem Leim eingebrachte Feuchte zu reduzieren.
Fasersichtung
In den meisten heutigen MDF-Anlagen werden die Fasern nach dem Trocknungsprozess oder – wenn vorhanden – erst nach der Nachbeleimung in einem Fasersichter nachgereinigt. Die Fasern werden in einen Luftstrom gegeben und entweder über Wirbelbildung, scharfe Umlenkungen, Prallsichtung, Steigluftsichtung oder einer Kombination mehrerer Effekte von Schwerteilen (Leimklumpen, Gummi, Metall usw.) weitestgehend befreit. Anschließend werden die Fasern erneut über Zyklonabscheider vom Luftstrom getrennt und der Formstation zugeführt.
Formung und Pressung
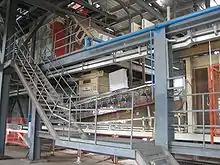
Streuung
Die Streustation besteht aus einem Dosierbunker, einer Mattenstreuung und einer Mattenglättung. Die Mattenstreuung hat sich im Laufe der Entwicklung deutlich gewandelt. In den Anfängen der MDF-Produktion wurden noch viele Streustationen mit einer Vakuum-Streuung ausgerüstet. Später etablierten sich aufgrund geringerer elektrischer Leistung und homogenerer Abstreuung immer mehr die mechanischen Streuköpfe. Die mechanischen Streumaschinen wurden anfangs mit Abfräswalzen zur Mattenglättung ausgestattet, die nach dem Abstreuen überschüssiges Material absaugten. In den modernen Streumaschinen kann auf diese Absaugung verzichtet werden und die Fasermatte wird über mechanische Egalisierungen geglättet.
Formstraße
Nach der Streustation wird die Fasermatte gewogen und die Faserfeuchte gemessen. Der Formling gelangt anschließend in die Vorpresse. Hier wird er bei kalter Vorverdichtung dickenreduziert, damit die Heißpressen effizienter beschickt werden können und die Gefahr der Beschädigung reduziert wird. Bei der Vorverdichtung im Durchlauf wird zumeist mit Bandvorpressen, nach dem Prinzip des Förderbandes (seltener mit Plattenbandvorpressen, nach dem Prinzip der Panzerkette, oder mit Walzenbandvorpressen, nach dem Prinzip des Pyramidensteintransportes mit Rundhölzern) gearbeitet.
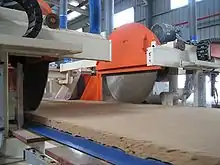
Nach der Vorpressung folgt die Mattenbesäumung, dort werden Seitenstreifen von der Fasermatte abgetrennt und die gewünschte Plattenbreite produziert. Die Seitenstreifen werden vor der Streumaschine in den Herstellungsprozess zurückgeführt. Messgeräte zur Dichtekontrolle oder Metallerkennung können folgen, optional auch eine Mattenbesprühung zur Verbesserung der Oberflächenqualität oder Beschleunigung der Mattendurchwärmung.
Heißpresse
Es folgt die Heißpressung, wo getaktet oder kontinuierlich gearbeitet wird.
- Bei Taktpressen sind Ein- oder Mehretagenpressen zu unterscheiden. Um kurze Presszeiten zu erzielen, werden Einetagenpressen mit höherer Temperatur, bis 230 °C, gefahren. Der Formling wird oben und unten mit einer Pressplatte bedeckt und in die Presse transportiert, die sich dann schließt und den Wärmeübergang auf das meist vorgewärmte Pressblech und schließlich auf das Pressgut gewährleistet. Bei fast allen Pressenarten wird zudem der Wärmeübergang in das Pressgut hinein durch den Dampfstoßeffekt verbessert. Wasser aus der befeuchteten Decklage verdampft durch die einseitige Erwärmung, diffundiert zur Plattenmitte und kondensiert unter Wärmeabgabe.
- Mehretagentaktpressen schließen simultan, um gleiche Presszeiten und damit gleichbleibende Plattenqualitäten zu erzielen. Hier wird nur mit 150 °C bis 200 °C gearbeitet, da die Presszeiten bei gleicher Kapazität zu Einetagenanlagen hier vergleichsweise länger sein können.
- Kontinuierlich arbeitende Pressen arbeiten mit einem Pressenband oder mit Pressplatten, über die der Druck und die Temperatur übertragen werden. Das Band wird dabei entweder von einem Rollenteppich (Küsters), einem Stabteppich (Siempelkamp, Dieffenbacher) oder einem Ölpolster (Bison) gegenüber den zumeist mit Thermalöl (seltener mit Dampf) beheizten Heizplatten abgestützt. Dieses Pressensystem stellt inzwischen den Stand der Technik dar und ermöglicht die Produktion von Plattendicken zwischen 1,5 mm und 60 mm.
- Auf Kalanderpressen können ausschließlich dünne Span- oder Faserplatten hergestellt werden. Die Pressung erfolgt hier mit Presswalzen und einem Außenband auf einer beheizten Kalanderwalze.
Endbearbeitung
Nach dem Pressen werden die Platten im Durchlauf besäumt und gekappt. Es folgt zumeist eine Reihe von Messungen zur Qualitätskontrolle. Diese sind in der Regel eine Dickenmessung, eine Spalterkennung und eine Plattenwaage. Seltener findet man eine Dichteprofilmessung und eine Restfeuchtemessung.
Zur Auskühlung der Platten vor der Abstapelung werden ein oder mehrere Kühlsterne verwendet. Nach der Kühlung werden die Platten meist über etwa ein bis drei Tage in einem Reifelager zwischengelagert. Die Platten weisen wegen der heißen Oberfläche der Pressplatten beziehungsweise Bänder eine Presshaut und unzureichende Dickentoleranzen auf. Weiterhin verändert sich die Plattendicke durch den „Reifevorgang“. Daher werden die Platten nach der Reifung auf Kalibrierschleifmaschinen geschliffen. Die Aufteilung in Fertigmaße findet meist in der gleichen Bearbeitungslinie statt, bevor die Platten für den Transport verpackt und eingelagert werden. Schleifstaub, Besäummaterial und Sägestaub werden zwischengelagert und der thermischen Energieerzeugung der Anlage zugeführt.
Energieanlage
In der Energieanlage, üblicherweise feststoffbeheizte Dampfkessel, werden die für den Produktionsprozess benötigten Wärmeträger erhitzt. Als Primärenergieträger werden Produktionsabfälle genutzt, welche den Energiebedarf je nach Holzaufbereitung und Plattentyp zu 30 bis 70 Prozent abdecken können. Zur Abdeckung des darüber hinausgehenden Energiebedarfes werden zumeist zugekaufte Biomasse (Holz) oder fossile Brennstoffe eingesetzt. Die für den Produktionsprozess benötigte Energie wird in Form von Dampf, heißem Thermalöl und gegebenenfalls Kesselabgasen zur Verfügung gestellt.
Verwendung
Rohplatten finden im Innen- und Dachausbau Anwendung. Faserplatten in beschichteter Form werden als Trägerplatten für Laminatfußböden und im Möbelbereich für Möbel- und Küchenfronten, im Ladenbau und Lautsprecherboxenbau eingesetzt. Aus MDF-Platten werden ganze Möbelserien gefertigt. Neben Schränken und Schranksystemen kommen MDF-Platten seit einigen Jahren in pulverbeschichteter Form als Tisch- und Abdeckplatten zur Anwendung. Sie eignen sich auch gut zum Herstellen von Profilverzierungen, zum Beispiel bei Küchenfronten. Auch im hochwertigen Lautsprecherboxenbau werden sie aufgrund ihrer hohen Biege- und Zugfestigkeit gerne verwendet. MDF-Platten können vielseitig mit Farben und Lacken behandelt werden, somit entsteht eine glatte, saubere Fläche mit profilierten Kanten, Ausfräsungen und so weiter.
Normung
MDF-Platten wurden ehemals in der Europäischen Norm EN 316 (1999), Absatz 3.2.3 als Faserplatte, hergestellt nach dem Trockenverfahren, definiert. Im Folgenden wird in der genannten Fassung der Norm gegenüber MDF eine Unterscheidung von HDF (≥ 800 kg/m³), Leicht-MDF (≤ 650 kg/m³) und Ultraleicht-MDF (≤ 550 kg/m³) vorgenommen. Diese Unterscheidung wurde in der aktuellen Fassung von 2009 jedoch entfernt. Platteneigenschaften werden in der EN 622-1 (2003) (Faserplatten: Allgemeine Anforderungen) und EN 622-5 (2010) (Anforderungen an Platten nach dem Trockenverfahren – MDF) für verschiedene Anwendungszwecke und Plattentypen (unter anderem für Leicht-MDF und Ultraleicht-MDF) definiert. Somit werden durch die aktuell gültige Norm für „Leicht-MDF“ und „Ultraleicht-MDF“ Eigenschaften definiert, der Dichtebereich für diese Platten aber nicht mehr festgelegt.
Spezialisierung
- MDF B1
- Die schwerentflammbare MDF-B1-Platte ist für den Innenausbau und Objektbereich geeignet, bei dem spezielle Anforderungen an den Brandschutz gestellt werden. Der Werkstoff kann wie herkömmliches MDF profiliert, gefräst, lackiert, beschichtet und furniert werden.
- Je nach Plattenhersteller können die B1-Platten einen stark rötlichen Kern aufweisen, der durch bewusste Farbmarkierung hervorgerufen wird und der je nach Bearbeitung (etwa optische oder akustische Schlitzung) störend zum Vorschein kommen kann.
- Topan form
- Bezeichnung für eine biegbare MDF-Platte (Firma Glunz AG)
- leitfähige MDF
- Die Beschichtung der MDF-Platten mit Pulverlacken erfordert, dass die Platte selbst eine Leitfähigkeit aufweist, da der Beschichtungsprozess über eine elektrostatische Applikation erfolgt. Die Ergebnisse der Beschichtung von Standardqualitäten blieben weit hinter den Erwartungen zurück. Deshalb wurden von diversen MDF-Herstellern Spezialpressungen unter Zugabe spezieller Leitfähigkeitsadditive vorgenommen. Das geringe Marktvolumen leitfähiger MDF-Platten hat dazu geführt, dass sich lediglich ein Anbieter in diesem Bereich engagiert. Die Beschichter arbeiten indes weiter an Lösungen für eine hochwertige Beschichtung von Standardqualitäten für die MDF-Pulverbeschichtung.
- MBPL
- Bezeichnung für eine leitfähige MDF-Platte (Firma Egger)
Kapazitäten
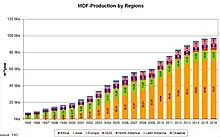
Die industrielle MDF-Produktion begann in den 1960er Jahren und hat seitdem entsprechend einer logistischen Wachstumskurve zugenommen, weil MDF erst andere Werkstoffe verdrängen musste.
Die ersten Produktionsanlagen waren auf kleine Kapazitäten von 100 m³ oder weniger pro Tag ausgelegt. Mit Einführung der kontinuierlichen Pressen nahmen die Kapazitäten auf 2000 m³ pro Tag zu.
In Deutschland erlangte die MDF-Platte zwischenzeitlich wirtschaftliche Bedeutung. Im Jahr 2008 wurden etwa 3,8 Mio. m³ produziert. In dieser Zeit wurde der zuvor führenden Produzent USA von China überholt. Seit 2008 bricht die Produktionskapazität in Deutschland ein, Deutschland fiel in der Produktionsstatistik von Rang zwei im Jahr 2008 auf Rang sieben im Jahr 2011 ab hinter China, Türkei, Brasilien, USA, Polen und Südkorea. Die drei größten Produktionsländer im Jahr 2016 waren China (etwa 57,7 Mio. m³), Türkei (etwa 5,1 Mio m³) und Brasilien (etwa 4,2 Mio m³).
Einzelnachweise
- Richtlinie über die Klassifizierung und Überwachung von Holzwerkstoffplatten bezüglich der Formaldehydabgabe. DIBt-Richtlinie 100, Fassung Juni 1994, Herausgeber: Deutsches Institut für Bautechnik – DIBt (Memento des Originals vom 10. August 2018 im Internet Archive) Info: Der Archivlink wurde automatisch eingesetzt und noch nicht geprüft. Bitte prüfe Original- und Archivlink gemäß Anleitung und entferne dann diesen Hinweis. (PDF; 485 kB)
- CARB-Fact Sheet (englisch; PDF; 41 kB)
Literatur
- André Wagenführ, Frieder Scholz: Taschenbuch der Holztechnik. Fachbuchverlag im Carl Hanser Verlag, Leipzig 2008, S. 127–259. ISBN 978-3-446-22852-8.
- M. Dunky, P. Niemz: Holzwerkstoffe und Leime. Springer, Heidelberg 2002, ISBN 3-540-42980-8.
Weblinks
- Verband der Deutschen Holzwerkstoffindustrie e. V (deutsch)
- European Panel Federation (englisch)
- MATERIAL ARCHIV – Umfangreiche Materialinformationen und Bilder