Metallpulverspritzguss
Das Metallpulverspritzgießen, auch MIM-Verfahren (von englisch Metal Injection Mo(u)lding, MIM) ist ein Urformverfahren zur Herstellung von metallischen Bauteilen komplexer Geometrie und hat seinen Ursprung in der Spritzgusstechnologie der Kunststoffe. Als MIM-Werkstoffe eignen sich prinzipiell alle Metalle bzw. Legierungen, die als Pulver zur Verfügung stehen und gesintert werden können, am häufigsten verbreitet sind jedoch rostfreie Stähle (1.4404/316L bzw. 1.4542/17-4 PH).
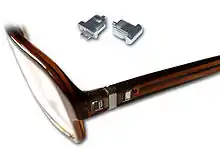
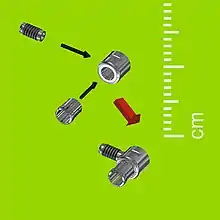
Eine Prozessvariante unter dem Oberbegriff Pulverspritzgießen ist das Keramikpulverspritzgießen, das prozesstechnisch ähnlich, jedoch auf die Fertigung von keramischen Bauteilen hin optimiert ist.
Der Markt für Metall-Spritzguss wurde 2016 auf 2,40 Mrd. USD geschätzt und wird bis 2022 voraussichtlich 3,77 Mrd. USD erreichen, mit einer durchschnittlichen Wachstumsrate von 7,83 %.[1] Der größte Teil des Wachstums der letzten Jahre fand in Asien statt, getrieben in erster Linie durch Funktionsbauteile in Mobiltelefonen und vergleichbaren Elektro- und Elektronikkomponenten für den Consumerbereich.[2]
Das Metallpulverspritzgießen (MIM) ist ein Metallverarbeitungsprozess, bei dem feines Metall- oder Keramikpulver mit einem organischen Binder vermischt und dann auf einer Spritzgussmaschine in Form gebracht wird. Anschließend wird der Binder wieder entfernt und das Bauteil bei hoher Temperatur in einem Ofen gesintert. Als Ergebnis erhält man ein rein metallisches Enderzeugnis, das die mechanischen Vorteile gesinterter Bauteile mit der großen Formgebungsvielfalt des Spritzgießens verbindet,[3][4][5] (siehe Abbildung Brillenscharnier).
Bekannt ist das Pulverspritzgießen (Powder Injection Mo(u)lding, PIM) bereits seit den 1920er-Jahren, als erste keramische Gehäuse für Zündkerzen mit diesem Verfahren gefertigt wurden.[6][7] Die erste Beschreibung einer Übertragbarkeit dieses Keramikpulverspritzgiessens (CIM für Ceramic Injection Mo(u)lding) auf Metalle wird vereinzelt P.O. Gribovsky zugeschrieben,[8] patentiert wurde das MIM-Verfahren allerdings von R. E. Wiech Jr. im Jahr 1972.[9]
Industriell konnte sich das Metallpulverspritzgießen ab etwa 1980 mit der Fertigung kleiner, hochpräziser metallischer Bauteile für Industriegüter und Handfeuerwaffen etablieren; heute ist MIM ein wirtschaftliches Fertigungsverfahren für Großserienprodukte, das aufgrund der derzeitigen Anlagenbeschränkungen vor allem bei der Herstellung kleinerer bis mittelgroßer Bauteile mit eher komplexer Geometrie und einem Gewicht von 0,1 bis etwa 150 Gramm zur Anwendung kommt.
Ein wesentlicher Vorteil des MIM-Verfahrens ist, dass Bauteile mit anspruchsvoller Geometrie, die in konventionellen Herstellungsprozessen nur mehrteilig zu fertigen sind, mit hoher geometrischer Präzision in einem einzigen Stück hergestellt werden können (siehe Abbildung rechts). Da der Spritzgussvorgang in Werkzeugen (Gussformen) mit mehreren Kavitäten (Hohlräumen/ Hohlformen) durchgeführt werden kann, ist das Verfahren kosteneffektiv für kleine, komplexe Bauteile in hohen Stückzahlen. Haupteinsatzgebiete sind der Automobil- und Maschinenbau, die Mess- und Steuerungstechnik, die Feinmechanik und der Waffenbau, die Schloss- und Beschlagindustrie, die Werkzeugtechnik sowie der Bereich der Haushaltsgeräte und Consumer-Elektronikgeräte (Smartphones u. ä.).
Für kleinere Stückzahlen und Prototypen ist das MIM-Verfahren aufgrund der hohen Initialkosten, die durch die Konstruktion und Fertigung des Spritzgusswerkzeugs verursacht werden, nur bedingt geeignet. Es werden derzeit Entwicklungsanstrengungen unternommen, metallische Bauteile vergleichbarer Präzision und Oberflächengüte mittels sinterbasierter additiver Fertigungsverfahren werkzeuglos herzustellen, um den Anwendungsbereich kleinerer Stückzahlen abzudecken und damit den Markt komplexer metallischer Präzisionsbauteile z. B. für spezifische Luft- und Raumfahrt- sowie Medizintechnikanwendungen zu erweitern.[10]
Die Prozessschritte des Pulverspritzgießens
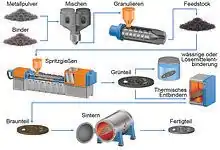
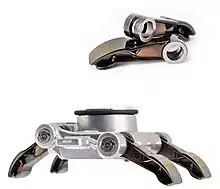
Das Pulverspritzgießen besteht aus den vier aufeinanderfolgenden Prozessschritten:
- Feedstockproduktion (Metallpulver-Bindemittel-Gemisch),
- Spritzgießen,
- Entbindern
- Sintern,
die schematisch in nebenstehender Abbildung dargestellt sind. Das fertige Bauteil kann anschließend noch einer Nachbehandlung unterzogen werden.
Feedstockproduktion
Im ersten Prozessschritt wird ein feines Metallpulver mit einem organischen Binder zu einer homogenen Masse vermischt (Feedstock), die analog zur Kunststoffverarbeitung in einem Spritzgussprozess verarbeitet werden kann. Im Gegensatz zum (Press) Sintern, wo aufgrund der stabileren Formgebung des Grünkörpers durch (axiales) Pressen gerne spratzige Pulver (mit kantiger Korngeometrie) zum Einsatz kommen, werden beim Metallpulverspritzguss sphärische Pulverkörnungen bevorzugt, da die Pulvermorphologie das Fließ- und Füllverhalten des Feedstocks beim Spritzguss maßgeblich beeinflusst und gemeinsam mit dem organischen Binder einen erheblichen Beitrag zur Maßhaltigkeit und Verringerung der Riss- und Lunkerneigung des Bauteils leistet.
Bevorzugt werden gasverdüste Pulver, die gleichmäßig sphärisch („rund“) sind. Prozessbedingt haben diese haben jedoch oft eine zu breit gestreute Partikelgrößenverteilung (PSD, Particle Size Distribution), so dass die für den MIM-Prozess bevorzugten Pulver über einen nachgeschalteten Ausleseprozess gewonnen werden müssen. Die alternativ verfügbare Wasserverdüsung unter hohem Druck erzeugt kleine, bereits MIM-gerechte Partikel, die allerdings eher plättchenförmig sind und deshalb durch Prall-, Strahl- oder Kugelmahlprozesse nachbearbeitet werden müssen, um bessere Fließeigenschaften zu bekommen. Wasserverdüste Pulver sind preisgünstiger und haben eine große Marktdurchdringung.
Obwohl der Binder nur temporär während des Spritzgießprozesses benötigt und danach wieder möglichst rückstandsfrei entfernt wird, handelt es sich dabei um die Schlüsselkomponente für einen erfolgreichen MIM-Prozess. Er hat die Aufgabe, die Pulverpartikel prozesssicher und gleichmäßig verteilt in die Spritzgusskavität (negatives Abbild der zu erzeugenden Geometrie) zu bringen und das Pulver so in Form zu halten, dass das Grün- bzw. Braunteil nicht wieder in sich zusammenfällt. Oft enthält der Binder noch eine Komponente, die den Verschleiß des Spritzgusswerkzeugs reduziert.
Moderne MIM-Bindersysteme bestehen üblicherweise aus drei Komponenten mit unterschiedlichen Eigenschaften.
Die erste Komponente ist der Hauptbinder, ein Polymer, das bei Spritzgusstemperatur eine niedrige Viskosität aufweist. Somit garantiert es einen guten Pulvertransport während des Spritzgussprozesses; bei Abkühlung reagiert es mit einem großen Viskositätssprung, um eine hohe Grünteilfestigkeit sicherzustellen. Als Hauptbinder geeignet sind z. B. kurzkettige Thermoplaste, da sie aufgrund ihrer Molekularstruktur einer anisotropen Ausrichtung der Partikel in der Schmelze entgegentreten. Der Hauptbinder wird im ersten Entbinderungsschritt (s. u.) z. B. durch Lösemittel oder Temperaturerhöhung entfernt.
Bei der zweiten Komponente des Binders handelt es sich um den Restbinder, auch Backbone genannt. Dieser sorgt nach Entfernung des Hauptbinders für einen zwar reduzierten, für die weiteren Verarbeitungsschritte (z. B. Teiletransport in den Sinterofen) aber noch ausreichenden Zusammenhalt der Pulverpartikel. Die Restbinderkomponente wird üblicherweise thermisch entfernt und sollte deshalb rückstandsfrei verbrennen und einen geringen Dampfdruck entwickeln, so dass das Bauteil während der thermischen Entbinderung keine strukturelle Schädigung erfährt.
Die dritte Komponente ist ein Additiv, das mehrere Aufgaben erfüllt. Es sorgt für eine vollständige Benetzung des Metallpulvers durch den Binder, erleichtert das Mischen der Komponenten während der Feedstockproduktion, wirkt Pulveragglomerationen entgegen und minimiert den Werkzeugverschleiß beim Spritzgießen.
Pulver, Binder und Additive werden in einer für das jeweilige Bindersystem optimierten Reihenfolge und Verarbeitungstemperatur homogen gemischt. Hierzu kommen spezielle Knetmischer, Scherwalzen-Mischsysteme oder Extruder zum Einsatz. Hierbei ist das Verhältnis von Pulver zu Binder von entscheidender Bedeutung: Zu hoher Pulveranteil bewirkt erhöhte Viskosität und erschwert die Werkzeugbefüllung. Dies führt zu Bauteilen mit geringer Dichte und Poren. Zu hoher Binderanteil begünstigt Entmischungen, starke Verarbeitungsschwindung und hohe innere Spannungen, was sich durch Verzug und Spannungsrissen am Fertigteil bemerkbar macht.
Spritzgießen
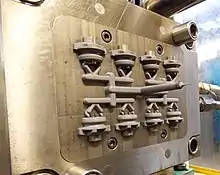
Die meisten kommerziell verfügbaren MIM-Bindersysteme basieren auf thermoplastischen Kunststoffen und können deshalb auf handelsüblichen vertikalen und horizontalen Kunststoffspritzgussmaschinen verarbeitet werden. Der Feedstock wird dabei in verflüssigter Form (üblicherweise bei erhöhter Temperatur) in ein geschlossenes Werkzeug eingespritzt, wo er durch gezielte Temperaturführung die Form (Kavität) erst komplett ausfüllt und anschließend plastifiziert. Im Gegensatz zum Kunststoffspritzguss verbleibt das eingespritzte MIM-Material für eine gewisse Haltezeit unter Druck in der Kavität, während das Werkzeug über integrierte Kühlkanäle heruntergekühlt wird. Dabei plastifiziert der Binder im Feedstock und der nun formstabile Körper (Grünteil oder Grünling) kann anschließend aus dem geöffneten Werkzeug ausgeworfen werden. Danach schließt das Werkzeug wieder und der Zyklus kann erneut beginnen.
Die Werkzeugtechnologie für den MIM-Prozess entspricht der des Kunststoffspritzgusses. Die wichtigste Komponente des Werkzeugs ist die Kavität, ein negatives Abbild des Formteils, das in ihr abgeformt werden soll. Im Gegensatz zum Kunststoffspritzguss ist diese Kavität allerdings größer dimensioniert als das spätere Fertigteil, da dieses während der Fertigung, insbesondere bei der Entbinderung und dem Sintern, signifikant schwindet. Die Schwindung kann je nach Werkstoff, Pulveranteil des Feedstocks und der Geometrie des Bauteils bis zu 25 % betragen.
Die entscheidende Kenngröße zur Fertigung maßhaltiger MIM-Präzisionsteile ist der Werkzeugaufmaßfaktor (WAF), der das Verhältnis zwischen den Abmessungen der Spritzgussform (Werkzeugmaß) und den Abmessungen des fertig gesinterten Metallteils (Zeichnungsmaß) definiert. Er wird durch Probesinterungen an genormten Prüfkörpern bestimmt und bei kommerziell verfügbaren Feedstockrezepturen im Rahmen der Materialspezifikation als Zahl (z. B. 1,154) angegeben. Um nach dem Sintern ein maßhaltiges Bauteil zu erhalten, muss der Konstrukteur die Fertigmaße des Bauteils mit dem WAF multiplizieren. Soll das zu fertigende Bauteil z. B. eine Länge von 10 mm haben, so muss die Grünteilkavität in dieser Stelle ein Maß von 10 mm × 1,154 = 11,54 mm aufweisen.
Mit Ausnahme der (allseitig gleichen) prozessbedingten WAF-Maßabweichungen weist der durch das Spritzgießen erzeugte MIM-Formkörper bereits alle typischen geometrischen Merkmale des fertigen Bauteils auf.
Bei großen Stückzahlen ist das MIM-Werkzeug oft mit mehreren identischen Kavitäten versehen (siehe Abbildung rechts), die durch einen Verteiler im Angußkanal gleichzeitig befüllt werden. Dies senkt sowohl die Werkzeugstückkosten als auch die Taktzeit des Prozesses und erhöht so Produktivität.
Entbindern
Um ein rein metallisches Bauteil ohne Rückstände von Kohlenstoff und anderen unerwünschten Stoffen zu erhalten, müssen im Prozessschritt Entbinderung möglichst alle Binderkomponenten rückstandsfrei aus dem haufwerksporigen Grünteil entfernt werden. Um die gewünschte Geometrie des Bauteils einhalten zu können, muss die Entbinderung möglichst gleichmäßig über den Bauteilquerschnitt erfolgen. Spannungseinträge durch Blasenbildung etwa können beim nachfolgenden Sintern zu Rissen oder Verzug führen können. Die Entbinderung von MIM-Bauteilen ist ein anspruchsvoller, in mehreren Schritten ablaufender Prozess.
Im ersten Prozessschritt wird die Hauptbinderkomponente entfernt, das Grünteil wird zum Braunteil. Je nach Feedstockrezeptur geschieht dies entweder durch Einsatz eines Lösemittels oder thermisch.
Bei der Lösemittelentbinderung wird die Hauptbinderkomponente durch ein Lösemittel von außen nach innen aus dem Pulver-Binder-Verbund herausgelöst, was eine offenporige Struktur hinterlässt. Der Restbinder ist im verwendeten Lösemittel unlöslich und hält die Pulverpartikel bis zur Sinterung formstabil zusammen.
Bei der thermischen Entbinderung wird die Hauptbinderkomponente durch Zersetzung oder Verdampfung entfernt. Der Restbinder in thermisch entbinderbaren Systemen muss dabei eine deutlich höhere Schmelz- oder Zersetzungstemperatur als der Hauptbinder haben, um seine Funktion erfüllen zu können.
Eine kommerziell weitverbreitete Sonderform der thermischen Entbinderung ist die katalytische Entbinderung. Hier wird dem Trägergas Stickstoff bei erhöhter Temperatur gasförmige Salpetersäure (HNO3) als Katalysator zugemischt. Durch die katalytische Wirkung der Säure werden die langkettigen Moleküle des Hauptbinders (meist Polyacetal) leichter aufgespalten. Diese gehen direkt in den gasförmigen Zustand über und können so über den kontrollierten Austausch der Gasatmospäre sehr viel schneller abgeführt und verbrannt werden als bei ausschließlich thermischer Entbinderung.
Die Entfernung der Restbinderkomponente aus dem Braunteil erfolgt in der Serienfertigung üblicherweise über eine in den Sinterprozess integrierte thermische Entbinderung. Dazu werden die Braunteile in einer Vorphase des Sinterporzesses für eine definierte Zeitdauer bei einer Temperatur im Sinterofen gehalten, bei der sich die Restbinderkomponente zersetzt und ausgast.
Sintern
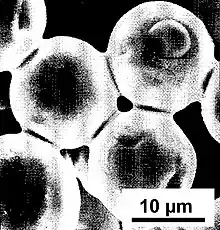
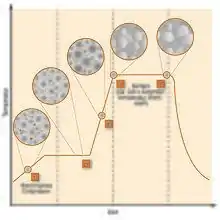
Das nach dem Entbindern zurückbleibende poröse MIM-Braunteil wird durch Sintern in eine dichte, mechanisch belastbare, polykristalline Festkörperstruktur überführt, deren Eigenschaften mit denen anderer metallischer Bauteile vergleichbar sind. Bei dieser Wärmebehandlung, die (knapp) unterhalb des Schmelzpunkts des Matrixwerkstoffs durchgeführt wird, wachsen die Pulverpartikel durch Diffusion und Kriechvorgänge zu einem Kristallgerüst zusammen und geben dem Bauteil die gewünschte Festigkeit. Die treibende Kraft im Sinterprozess ist die Oberflächenspannung der kugelförmigen Pulverpartikel. Diffundierende Atome versuchen, die freien Stellen zwischen den Partikeln zu füllen, und durchdringen dabei die Kristallstruktur entlang der Korngrenzen und über die Oberflächen. Bei erhöhter Temperatur nehmen die Beweglichkeit und damit die Diffusionstätigkeit der Atome zu und es bilden sich im ersten Schritt des Sinterprozesses an den Kontaktflächen der Pulverpartikel Sinterbrücken aus (siehe Abb. rechts.) Diese vergrößern sich durch weitere Diffusion und werden zu Korngrenzen, entlang derer die Diffusionstätigkeit weiter zunimmt. Die Atome sind bestrebt, die noch vorhandenen freien Stellen (Poren) zu füllen. So entsteht aus dem ursprünglich losen Pulveragglomerat des Braunteils eine dichte, nahezu porenfreie Gefügestruktur. In der Abbildung rechts ist schematisch die Entwicklung eines Gefüges während des Entbinder- und Sintervorgangs in Abhängigkeit von der Temperatur dargestellt. Je kleiner die Pulverpartikel, umso größer ist deren Oberflächenspannung und desto mehr Korngrenzen sind vorhanden. Die davon bestimmte Sinteraktivität ist bei der Auswahl bei der Sinterparameter für MIM-Werkstoffe zu berücksichtigen.
Um unerwünschte Oxidationsvorgänge zu vermeiden, werden MIM-Teile entweder im Vakuum oder unter Schutzgasatmosphäre (Wasserstoff, Stickstoff, Argon) bei Temperaturen von bis zu 1600 °C gesintert. Je nach Bauteilgröße und Stückzahl kann dies in Batch- oder Durchlauföfen erfolgen.
Nachbearbeitung
Grundsätzlich ist das Metallpulverspritzgießen ein endkonturnahes bzw. endkonturgetreues Herstellungsverfahren (net-shape). Die Bauteile haben eine hohe Dichte, die typischerweise mehr als 96 % des nicht gesinterten, homogenen Materials beträgt. Aufgrund des aufwändigen Herstellungsprozesses versucht man, die Nachbearbeitungsschritte bzw. Folgeprozesse schon in der Entwurfsphase auf ein Minimum zu reduzieren.
Grundsätzlich können MIM-Teile allen denkbaren Wärme- und Oberflächenbehandlungen unterzogen werden, die auch bei konventionell gefertigten metallischen oder keramischen Bauteilen anwendbar sind. Dies sind beispielsweise
- Oberflächenfinish: Sandstrahlen, Gleitschleifen, Polieren, Läppen
- Beschichtungstechnologie: Dünnschichttechnologie, Galvanisieren, Lackieren
- Verbindungstechnik: Laserschweißen, Löten, Montieren
- Wärmebehandlung: Härten, HIP (Heiß-Isostatisches Pressen)
- Spanende Bearbeitung: Drehen, Fräsen, Bohren, Schleifen, Reiben, Honen, Gewindeschneiden
- Umformtechnik: Biegen, Kalibrieren
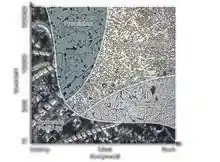
Abgrenzung zu anderen Herstellungsverfahren
Das Metallpulverspritzgießen (MIM-Verfahren) konkurriert mit der spanenden Herstellung, dem Presssintern und dem Feinguss.
Im Vergleich zur spanenden Fertigung oder zum Presssintern von einfachen, rotationssymmetrischen Bauteilen ist es unter Kostenaspekten klar im Nachteil. Das MIM-Verfahren weist jedoch immer dort Vorteile auf, wo komplexe Geometrien, spezielle Werkstoffanforderungen, hohe Präzision und geringe Fehlerquoten gefordert sind oder teure Nacharbeit vermieden werden soll.
Hinterschnitte, Bohrungen, Gewinde, Logos oder andere Beschriftungen können direkt in das Bauteil integriert oder ganze Baugruppen in einem Stück gefertigt werden. Somit handelt es sich beim MIM-Verfahren um ein endkonturnahes Fertigungsverfahren.
Oft wird das MIM-Verfahren mit dem konventionellen Presssintern verwechselt, bei dem – bezogen auf den Querschnitt – vergleichsweise flache Bauteile durch Pulverkompaktieren in Matrizenwerkzeuge gepresst und anschließend gesintert werden. Damit lassen sich jedoch nur weitaus weniger komplexe Bauteilgeometrien fertigen. Aufgrund der uniaxialen Verdichtung kommt es beim Presssintern über dem Bauteilquerschnitt außerdem zu einem Dichtegradienten, während MIM-Bauteile eine sehr gleichmäßige Dichteverteilung aufweisen.
Da das MIM-Verfahren ein werkzeuggebundenes Verfahren ist, müssen sich die Werkzeugkosten über die Stückzahlen amortisieren. Diese können je nach Anwendungsfall zwischen einigen tausend bis hin zu mehreren Millionen Bauteilen pro Jahr liegen.
Nebenstehende Abbildung zeigt schematisch die Abgrenzung der mit dem MIM-Prozess konkurrierenden Fertigungsverfahren, wobei die Grenzen fließend sind und immer von Bauteilgeometrie und eingesetztem Werkstoff abhängen.
Nicht berücksichtigt ist in der Darstellung die sinterbasierte additive Fertigung, da sich diese Fertigungstechnologien noch im Entwicklungsstadium befinden und deshalb die entsprechenden Verfahrensgrenzen noch nicht seriös bestimmt werden können.
Literatur
- Die Geschichte der Firma OBE Ohnmacht & Baumgärtner GmbH & Co. KG., Ispringen, 2004.
Quellen
- Metal Injection Molding Market by Material Type – Global Forecast to 2022 (Basisjahr der Studie ist 2016, der Prognosezeitraum ist von 2017 bis 2022), Markets & Markets. In: MarketsAndMarkets.com. Abgerufen im März 2021
- Subramanian, Vijay. „Metal and Ceramic Injection Molding – AVM049C“. www.bccresearch.com. Abgerufen im Mai 2015
- Metal Injection Moulding (MIM); abgerufen im März 2021
- Randall M. German, Animesh Bose, Animesh Bose: Injection molding of metals and ceramics. Metal Powder Industries Federation, Princeton, N.J., U.S.A. 1997, ISBN 1-878954-61-X.
- Carlo Burkhardt: Metallpulverspritzguss: Fertigung komplexer Bauteile in höchster Präzision. Verl. Moderne Industrie, Landsberg 2013, ISBN 978-3-86236-056-7.
- J.-E. Delaunay, G.-L. Dimitri; Fabrication de Stéatite Comprimée, Französische Patentatnummer 505.386, 21. November 1916.
- J.-E. Delaunay, G.-L. Dimitri, Fabrication de stéatite Comprimée, French patent nº. 498.015, 16. Juli 1918.
- P.O. Gribovsky; Hot casting of ceramic products; Gosenergoizdat publ. (1956) (russisch)
- R. E. Wiech Jr.; Manufacture of Parts for Particulate material", U.S. Patent Nr. 262,851, 14. Juni 1972.
- C. Burkhardt; A beginner’s guide to three leading sinter-based metal Additive Manufacturing technologies; Powder Injection Moulding International Band 14, Nr. 1, 2020, S. 69–79.