Futura Carrier
Der Futura Carrier ist ein Binnenschiffstyp. Er ist von einem deutschen Firmenverbund aus den Bereichen Schiffsplanung und -bau, Maschinenbau, Antriebstechnik und Elektrotechnik entwickelt worden und wurde maßgeblich vom Bundesumweltministerium gefördert.
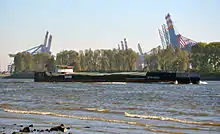
Der Schiffstyp verfügt über eine Reihe von Neuerungen. Er ist zum Beispiel als modulares System mit neuartigem Schiffsrumpfdesign aufgebaut, besitzt vier redundante Ruderpropeller-Antriebe und eine leistungsfähige Binnenschiffs-Automation.
Bisher sind vier Schiffe dieses Typs vom Stapel gelaufen, weitere sind geplant.
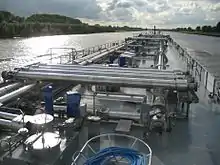
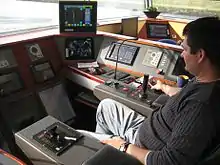
Prinzip
Der für die Binnen- und kleine Küstenfahrt entwickelte Schiffstyp Futura Carrier basiert auf einem Baukastenprinzip mit Schiffskörper- und Technikmodulen, mit dem Vorteil, dass jeder zu erstellende Neubau für unterschiedliche Einsatzbedingungen speziell auf Ladung und Größe zugeschnitten werden kann. Dementsprechend kann ein Futura Carrier als Massengutfrachter, Containerschiff oder Tankschiff ausgelegt sein. Die Konstruktion und Planung beim Futura Carrier ermöglicht den Bau durch verschiedene Werften ohne eigenen Entwicklungsaufwand für Planung, Projektierung und Arbeitsvorbereitung. Für die Entwicklung des Futura-Carrier-Konzeptes war das Kieler Unternehmen New Logistics verantwortlich. Ein einfacher Linienriss ermöglicht die schiffbauliche Fertigung an zahlreichen Plätzen. Alle erforderlichen Systeme, Fundamente, Rohr- und Kabelführungen, einschließlich der schiffbaulichen Schottdurchführungen wurden in der Konstruktion berücksichtigt. Die erforderlichen Aggregate wie Stromerzeugungsaggregat, Pumpen, Lüfter, Kompressoren sowie alle anderen gehören zum Lieferpaket. Dieses unterscheidet sich je nach Schiffstyp und Einsatzbereich.
Gegenüber vergleichbaren, existierenden oder geplanten Binnen- und Küstenschiffen soll der Futura-Carrier-Typ weniger Kraftstoff verbrauchen und die Betriebskosten deutlich senken. Dafür soll die bugseits katamaranförmige Rumpfform und die so genannte Luftschmierung, die Unterströmung des Rumpfes mit Luftbläschen zur Verringerung der Reibung und damit des Widerstandes sorgen. Dies soll einen geringeren Reibungswiderstand bewirken und die Wellenbildung sowie Schwellschäden an empfindlichen Uferbereichen und Flussbetten vermindern. Ein weiteres Novum der Futura-Carrier-Schiffe ist der Einsatz von im Straßenverkehr erprobter Abgasreinigungstechnik. Hier wurde erwartet, dass sich der Ausstoß von Stickoxiden um bis zu 70 Prozent und die Emission von Feinstaubpartikeln um bis zu 99 Prozent reduzieren lassen. Auf dem Testprüfstand wurden diese Werte erreicht. Abgaswerte und Systeme der Abgasnachbehandlung werden innerhalb des ersten Betriebsjahres von unabhängigen Sachverständigen regelmäßig kontrolliert und aufgezeichnet. In der Praxis arbeitete die neuentwickelte Technik jedoch nur unzureichend und versagte häufig.[1]
Schiffskörper und Laderäume
Der Schiffsrumpf eines Futura Carriers besteht aus dem Heck-, dem Laderaum- und dem Bugmodul. Gemäß dem Bauprinzip bilden die drei fest miteinander verschweißten Module eine Schiffseinheit. Der Doppelrumpf-Bug und das breite Heck sind, unter Berücksichtigung der Anordnung der Antriebe, speziell für die extremen Strömungsverhältnisse in flachem und engem Fahrwasser und für den Einsatz der „Luftschmierung“ optimiert. Für den Schiffskörper wird herkömmlicher, teilweise hochfester Schiffbaustahl verwendet. Alle Decks werden ohne Sprung und ohne Balkenbucht ausgeführt.
Antriebsanlage
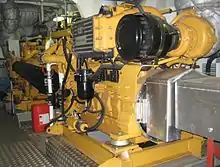
Um eine hohe Manövrierfähigkeit des Schiffes vor allem bei niedrigen Wasserständen und engem Fahrwasser zu erreichen, ist der Schiffstyp mit einem dezentralen Antrieb bestehend aus vier identischen 360°-Ruderpropeller-Einheiten der Firma HRP ausgerüstet. Während sich die beiden vorderen Antriebe in den Kufen des Schiffskörpers befinden, hängen die hinteren Module außen, frei unter dem leicht ansteigenden Rumpf. Dabei werden die drehbaren Ruderpropeller jeweils vom gleichen Motorentyp direkt angetrieben und können synchron im Dauerbetrieb fahren. Die Gesamtantriebsleistung von bis zu 2400 kW wird von vier Caterpillar oder MTU-Dieselmotoren mit einer Leistung von jeweils bis zu 600 kW erzeugt. Die HRP-Ruderpropeller sind verhältnismäßig klein und für die Flussfahrt optimiert. Sie sollen auch in flachem Fahrwasser den sicheren Betrieb gewährleisten und fungieren als kombinierte Antriebs- und Steuerungssysteme. Dementsprechend können sie zum Antrieb und zum Manövrieren eingesetzt werden. Über das sogenannte „Multi Thruster Controle System“ (MTCS) lassen sich die vier Antriebe in Kombination mit einem Rechner steuern. Fallen einzelne Antriebe aus oder werden gezielt abgeschaltet, erkennt dies die MTCS-Technik selbstständig und kompensiert automatisch.
Die Antriebsmodule sind so angeordnet, dass sie z. B. bei Wartungsarbeiten oder Reparaturen schnell ausgetauscht werden können, ohne das Schiff zu docken. Die Motoren und Generatoren werden indirekt über Kastenkühler in der Außenhaut gekühlt. Jeder Haupt- und Hilfsdiesel ist mit eigener Starterbatterie, Lichtmaschine und angehängtem Ladegerät ausgestattet. Alle vier Antriebe arbeiten jeweils komplett autark auch bei Ausfall des gesamten Bordnetzes inklusive Notdieselgenerator.
Abgasnachbehandlung
Futura Carrier sind die ersten Binnenschiffe, welche mit einem Kombinationssystem aus Partikelfilter und NOx-Reduktion ausgestattet wurden, wobei das gesamte System zur Abgasnachbehandlung von der Firma Greentop entwickelt wurde. Es ist mit vier Abgasreinigungsmodulen (ein Modul pro Hauptmotor) ausgerüstet, die gleichzeitig auch als Schalldämpfer fungieren. Ein Abgasnachbehandlungssystem besteht aus einer Kombination aus einem Dieselpartikelfilter und einem SCR-System zur NOx-Reduktion. Die Kombination ist auf möglichst geringen Abgasgegendruck ausgelegt.
Der Dieselpartikelfilter, bestehend aus vier Filtereinheiten mit jeweils über 40 Liter Volumen, reduziert bis zu 99 Prozent der Partikelemission. Der angesammelte Ruß kann auf zwei Arten regeneriert (verbrannt) werden: Dem Kraftstoff wird eine äußerst geringe Menge eines Additivs (10 ppm) beigemischt, wodurch der Ruß bei einer Abgastemperatur von ca. 400 °C selbständig verbrennt. Wird diese Abgastemperatur über einen längeren Zeitraum nicht erreicht (z. B. bei leerer Talfahrt) wird der kraftstoffbetriebene Dieselbrenner eingeschaltet, der dann die Temperatur des Rußes über die Zündtemperatur bringt. Dadurch ist eine Regeneration unter allen Betriebsbedingungen gewährleistet.
Das SCR-System zur NOx-Reduktion besteht aus einem Reaktor aus katalytisch beschichteten Keramikelementen. In den Abgasstrang vor den Reaktor wird ein Reduktionsmittel (flüssiger Harnstoff, AdBlue) eingedüst, welches die Stickoxide zu Stickstoff und zu Wasserdampf umwandelt.

Tanks
Im Vor- und Achterschiff befindet sich je ein separater, von der Außenhaut unabhängiger Brennstoffvorratstank. Die Tanks sind mit einer elektrischen Inhalts-Fernanzeige versehen, die sich im Steuerhaus ablesen lässt. Schmierölvorratstanks und entsprechende Altöltanks sind als lose Tanks im hinteren Pumpenraum und im Generatoren-Betriebsraum vorhanden. Das Befüllen der Dieselmotoren mit Frischöl und das Absaugen des Altöls erfolgt mittels Handpumpen. Alle Tanks sind durch wasser- bzw. öldicht verschraubte Mannlöcher begehbar und verfügen, wie auch die Leerzellen, über eine natürliche Entlüftung. Am Ende der Entlüftungsleitungen sind Flammschutzsiebe angebracht. Für Trinkwasser gibt es einen etwa 20 Kubikmeter fassenden Tank unterhalb des Wohnmoduls mit außen liegenden Füllanschlüssen. Hier befindet sich auch der Schmutzwassertank (30 Kubikmeter) mit Übergabestutzen in der Vorderkante der Wohneinheit, oberhalb vom Hauptdeck.
Luftblasenschmieranlage
Auch die Luftblasenschmieranlage der Futura Carrier, die den Schiffswiderstand und somit auch Kraftstoffverbrauch und Schwellbildung positiv beeinflussen soll, ist als Baukastensystem ausgelegt. Abmessungen und Leistungen lassen sich an die jeweilige Schiffsgröße anpassen. Die eingesetzten Komponenten werden seit über 40 Jahren in der Abwassertechnologie angewendet. Den Kern der Anlage bilden ein Kompressor und Belüfterplatten, die für den konstanten, feinblasigen Luftschleier in den vorderen Propulsionstunneln bzw. unter dem Schiffsboden sorgen. Das hierfür verwendete Material zeichnet sich durch niedrige Widerstände aus und ist resistent gegen Bewuchs. Unter dem Schiffsbug verläuft ein außen offenes, querlaufendes U-Profil, das in den Boden integriert ist und einen ca. 300 mm breiten und ca. 200 mm tiefen Belüftungskanal bildet. Dieser Kanal und die Ausströmer im Heck und in den Propulsionstunneln werden zur Außenhaut bündig mit den Belüfterplatten verschlossen.
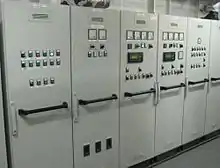
Fahrstand
Das Steuerhaus ist mit einem modernen, dem Stand der Technik entsprechenden und ergonomischen Einmann-Fahrstand ausgestattet. Er wurde unter Berücksichtigung aller relevanten Regeln und Vorschriften (LR-, SUK-, VDE-Richtlinien) eingerichtet. Wie die gesamte elektrische Anlage des Schiffstyps wurde der Fahrstand einschließlich sämtlicher Navigationssysteme von der Hamburger Firma Claus-D. Christophel konzipiert. Die elektrische Anlage umfasst neben der Energieverteilung auch die Beleuchtung, ein Typhon, die notwendigen Antennen und ein Kamerasystem für die Schiffsseiten und den Bug. Ein zweites Kamerasystem überwacht die Schiffsbetriebsräume. Die Navigations- und Kommunikationseinrichtungen bestehen aus zwei VHF-Sprechfunksystemen, Navtex, AIS, dem GPS-Empfänger mit Loganzeige, zwei Radar-Systemen mit Wendezeiger (Revier und See), einem Echolot (auch geeignet für Flachwasserfahrt), einem Kreisel- sowie einem Magnetkompass und dem Log. Eine Selbststeueranlage vervollständigt die nautischen Bedienelemente. Vom Steuerpult aus lassen sich weiterhin der klappbare Vormast, die Hebeeinrichtung des Steuerhauses sowie der auf dem Haus montierte, absenkbare Geräteträger fernbedienen. Auch die Luftblasenschmierung wird von hier aus gesteuert. Außerdem verfügt das Schiff über ein modernes Alarm-, Monitoring- und Kontrollsystem. Dieses ermöglicht die Erfassung und Bestätigung sämtlicher Signale von Alarmgebern und den seriellen Schnittstellen zu den Antriebsmotoren und den zwei Bordnetzaggregaten von einem einzigen Touch-Screen (Remote Operator Station) aus. Fällt dieser aus, so steht zusätzlich noch ein Notbedienterminal zur Verfügung.
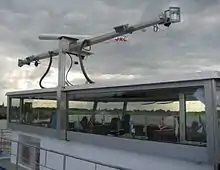
Automation
Die modulare Lösung zur Automation wurde unter der Bezeichnung INCONTROL ebenfalls von der Firma Claus-D. Christophel entwickelt und gebaut. Die Module umfassen folgende Funktionen:
- Schaltvorgänge – Von der Positionsbeleuchtung bis zum Heben- und Senken der Brücke und des Bordkrans lassen sich alle wichtigen Elemente zentral von der Schiffsführung schalten
- Überwachung und Alarmmeldeanlage – Überwachung des Motormanagements auf unzulässige Betriebswerte, des Hydraulikdruck wichtiger Antriebsaggregate, der Wicklungstemperatur der Pumpenmotore etc.
- Maschinenanlage – der CAN-Bus des Hauptantriebs wird laufend ausgelesen, an die Automation angebunden und wichtige Betriebswerte werden zentral angezeigt.
- Stromerzeugung – Der Schiffsführer sieht auf einen Blick, welche Verbraucher aktiv sind, aus welchen Stromerzeugern sie gespeist werden und welche Wege der Strom nimmt.
Für Tanker ist die Anbindung des Cargo-Controlsystems an die Automation von Bedeutung. Darüber hinaus ist mit Hilfe des optionalen Fleet Support Systems (FSS) die Möglichkeit eines Abrufs aller den Schiffsbetrieb betreffenden Informationen per Internet möglich, um im Ernstfall Diagnose und Service durch die Fachtechniker zu beschleunigen und Kosten zu reduzieren.
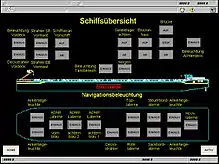
E-Anlage
Für die Stromerzeugung sind zwei gleich große Diesel-Drehstromaggregate im Vorschiff eingebaut. Ihre Leistung wird entsprechend dem Strombedarf des jeweiligen Futura Carriers ausgelegt. Sie sind elastisch im Generatoren-Betriebsraum gelagert und vom Steuerpult aus zu bedienen. Bei normalem Bordbetrieb reicht ein Aggregat, um den Leistungsbedarf zu decken. Der Parallelbetrieb ist im Falle von Belastungsspitzen vorgesehen. Das Zu- und Abschalten erfolgt lastabhängig. Die Bordnetzspannungen betragen 400 V, 50 Hz als 3-Leiter, 230 V, 50 Hz, einphasig sowie 24 V Gleichstrom. Die Notstromversorgung für die Automation der Hauptschalttafel, der Überwachungs-, Befehls- und Meldeanlagen sowie für Notbeleuchtung und Instrumente wird bei Fluss/See-gängigen Schiffen mittels Notaggregat und bei Binnenschiffen über die Bordnetzbatterien sichergestellt.
Die elektrische Versorgung sowie die Überwachung und Steuerung des gesamten Systems Futura Carrier ist modular aufgebaut. Dieses ermöglicht beim Bau einer Einheit eine Kombination vollständig vorgefertigter und erprobter Elemente entsprechend dem Kundenwunsch. Die Installation der Systeme erfolgt auf vorgesehenen Fundamenten sowie bereits vorverlegten Kabel- und Rohrinstallation. Selbst die wesentlichen Kabel und Rohrleitungen werden dabei weitestgehend vorkonfektioniert. Der Einbau der Systeme sowie die Installation kann dann mit lokalen Kräften durchgeführt werden.
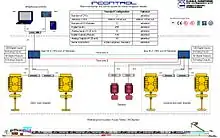
Kabinen
Die Kabinen der Futura Carrier sind in einem Wohnmodul auf dem Achterschiff untergebracht. In den Wohnbereichen besteht der Fußboden aus schallabsorbierendem, schwimmendem Estrich. Für die Möbel in den Crew-Kabinen und in der Messe wurde kunststoffbeschichtete Tischlerplatte als Material verwendet. Die Sanitärzellen für die Crew bestehen aus vorgefertigten Einheiten. Wand- und Deckenelemente sind in Sandwichbauweise aus verzinktem Stahlblech mit schalldämmender Isolierung und Hartträgerplatte gebaut. Der Boden ist mit rutschfesten Fliesen ausgelegt. Die für den Betrieb des Wohnmoduls erforderliche Versorgungstechnik, wie Druckwasseranlage, Warmwasseraufbereitung, Abwasser-, Klima- und Lüftungsanlage wurde im Betriebsraum unter dem Steuerhaus installiert. Wohnmodul und Steuerhaus sind von innen wärme- bzw. schallisoliert. Die Isolierungen wurden nach den Klassifikationsforderungen und Schallberechnungen ausgeführt.
Gebaute Einheiten
Bisher sind vier Futura Carrier im Einsatz:
- Der fluss- und seegängige Multi-Purpose-Carrier RMS Kiel, eine 99,90 m lange Version des Futura Carriers mit einer Breite von 14,10 m und 5,70 m Seitenhöhe, der von Mai 2007 bis Mai 2008 für das Rhein-, Maas- und See-Schiffahrtskontor in Duisburg im Einsatz war.
- Der Binnentanker Till Deymann der Harener Reederei Deymann, eine als Tankschiff gebaute Version des Futura Carriers mit 109,80 m Länge, 11,45 m Breite und 5,15 m Seitenhöhe, der seit Juni 2007 im Einsatz ist.
- Zwei Binnen-Bulker vom Typ FC-975 des Schifffahrtsunternehmens Hans Schramm & Sohn aus Brunsbüttel, die Schiffe Sophia Soraya und Kaja Josephine sind seit Mai 2007 in Fahrt.
- Aufträge über weitere Futura Carrier sind bereits erteilt.
Einzelnachweise
- Bestätigt: „Futura Carrier“ floppt in Binnenschifffahrts-Report 02/2014, Vol. 34, Bundesverband der Deutschen Binnenschifffahrt e.V., Duisburg, Mai 2014, S. 18.
Literatur
- Der Futura-Carrier - Top oder Flop, Volker Renner, Binnenschifffahrt, 04/2007
- Die „RMS Kiel“ hat Fahrt aufgenommen, Friedemann Stehr, Schiff & Hafen, 06/2007