Betonplatte
Betonplatten sind Bauteile aus Beton, die als Straßenbelag, Bodenbelag oder auch Wandverkleidung Verwendung finden.
Herstellungsverfahren
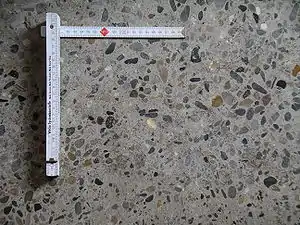
Das gängigste Verfahren zur Herstellung von Betonplatten ist das Hermetikverfahren. Es eignet sich für dickere Platten von rund vier bis zwölf Zentimeter Dicke. Die Herstellung geschieht meist auf einer Drehtischpresse mit meist sieben, manchmal auch nur fünf Stationen. Dabei werden zwei verschiedene Betonsorten verwendet: Der relativ dünnflüssige Vorsatzbeton und der sehr trockene Hinterbeton. Der Vorsatzbeton bildet später die sichtbare Oberseite der Platte und ist bezüglich Farbe und Körnung entsprechend individuell gestaltet. Für den Hinterbeton wird meist eine einheitliche Betonsorte verwendet.
Zunächst wird der Vorsatzbeton in die Form eingefüllt und durch Rütteln verteilt. Danach wird der Hinterbeton eingefüllt und die gesamte Füllung (meist in zwei Schritten) durch Pressen verdichtet. Durch den hohen Druck von bis zu 1200 Tonnen wandert ein Teil der Feuchtigkeit aus dem Vorsatz- in den Hinterbeton, wodurch sich beide Lagen homogen verbinden. Nach dem Öffnen der Form wird die rohe Platte entnommen, auf eine Palette aus Metall, Holz oder (seltener) Kunststoff gelegt und in ein Lager gebracht, damit der Beton abbinden kann.
Das Nasspressverfahren ähnelt dem Hermetikverfahren, jedoch wird hier nur eine Betonsorte verwendet. Dadurch können sehr dünne Platten hergestellt werden. Da der Beton beim Einfüllen noch relativ dünnflüssig ist, muss während des Pressvorgangs der größte Teil des Wassers aus der Form entweichen können.
Bestimmte Platten werden auch in Formen (z. B. aus Polyurethan) gegossen und erst nach dem Abbinden entnommen (Wetcast-Verfahren). Dies hat den Nachteil, dass entsprechend viele Formen vorgehalten werden müssen.
Früher wurden Betonplatten auch gestampft. Dieses Verfahren gilt heute aber als veraltet.
Zur Vermeidung von Schrumpfrissen beim Aushärten werden dem Beton oft Fasern zugegeben, man spricht dann von Faserbeton. Die Fasern nehmen die beim Aushärten entstehenden Zugspannungen auf und ermöglichen es dadurch große Platten herzustellen.
Besondere Effekte
Ist der Boden der Form nicht glatt, sondern weist ein Muster auf, so wird dieses auf der fertigen Platte reliefartig abgebildet. Auf diese Weise kann man beispielsweise ein sandsteinähnliches Aussehen erreichen.
Durch das Einsprühen von zusätzlicher Farbe vor dem Einfüllen des Hinterbetons kann ein Marmoriereffekt erzielt werden.
Bei der Direktauswaschung werden die Platten sofort nach der Entnahme aus der Presse mit einem Hochdruck-Wasserstrahl bearbeitet. Dabei werden die feinen Bestandteile des Betons an der Oberfläche entfernt, während die gröberen Körner erhalten bleiben.
Kleidet man den Boden der Form mit Papier aus, das mit einem Abbindeverzögerer (z. B. Zucker) getränkt ist, so kann die Vorderseite der Platte nicht aushärten. Nach dem Abbinden des Betons können Papier und nicht ausgehärtete Betonreste durch Bürsten und mit Hilfe von Wasser entfernt werden. Man erhält so den klassischen Waschbeton.
Weiterverarbeitung
Nach dem Abbinden können die Platten auf verschiedene Art weiter bearbeitet werden. Die wichtigsten Möglichkeiten sind:
- Schleifen
- Strahlen mit oder ohne vorhergehendes Schleifen. Durch die Verwendung von Matrizen können auch Teilbereiche der Plattenoberfläche gestrahlt werden, während andere unbearbeitet bleiben
- Rumpeln, also das maschinelle Abklopfen der Plattenoberfläche mit einer Art Hammer
- Bearbeitung der Kanten, z. B. durch das Anschleifen von Fasen
- Absäuern zum Entfernen von Zementresten oder zur Erzielung einer größeren Rauigkeit der Oberfläche
- Das Aufsprühen einer Beschichtung, um die Widerstandsfähigkeit gegen Verschmutzung und Witterungseinflüsse zu erhöhen