Wertstromanalyse
Die Wertstromanalyse ist eine betriebswirtschaftliche Methode zur Verbesserung der Prozessführung in Produktion und Dienstleistung. Sie wird auch als Wertstromaufnahme eines Ist-Zustandes bezeichnet, engl. Value stream mapping (VSM).
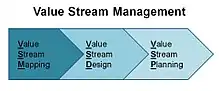
Dieser erste Verfahrensschritt des sogenannten Wertstrommanagements (Value Stream Management) liefert ein Modell der Material- und Informationsflüsse der einzelnen Wertströme.
In der Analyse werden die nicht-wertschöpfenden Prozesse identifiziert. Im folgenden Entwurfsansatz wird im Rahmen eines Wertstromdesigns ein verbesserter Wertstrom gestaltet, bei dem die nicht-wertschöpfenden Tätigkeiten und unnötige Liegezeiten eliminiert sind. Über die Wertstromplanung wird der Übergang vom Ist- zum Soll-Wertstrom geplant.
Der vergleichbare Ansatz im Dienstemanagement minimiert nicht die Liegezeiten, sondern die einzelnen Wartezeiten zwischen den Verrichtungen.
Insbesondere im Toyota-Produktionssystem ist das Eliminieren der (Zeit-)Verschwendung ein wichtiger Baustein. Das japanische Wort für Verschwendung ist Muda, das Verfahren zur Beseitigung der Verschwendung ist die sogenannte Muda-Elimination.
Vorgehen
Segmentierung der Produktion (Produktfamilien)
Zunächst wird die Produktion in einzelne Wertströme unterteilt, die anschließend analysiert werden. Die Unterteilung orientiert sich an den Prozessketten bzw. Materialflüssen der Produktion. Damit zielt das Wertstromdesign auf die Gestaltung einer Fließfertigung mit kurzen Durchlaufzeiten ab. Die Segmentierung nach dem Verrichtungsprinzip, wie in der Werkstattfertigung, ist unüblich, da sie häufig dem Ziel der kurzen Durchlaufzeiten widerspricht[1].
Ermittlung des Kundenbedarfs (Kundentakt)
Bei der Ist-Aufnahme wird der „Kundentakt“ für jeden Wertstrom bestimmt. Der Kundentakt bildet die mittlere geforderte Leistung der Produktion ab. Er beschreibt die zur Herstellung eines Produkts verfügbare Zeit. Jeder Prozess, der schneller als der Kundentakt produziert, kann den Kundenbedarf decken.
- Beispiel
Der Jahresbedarf des Kunden beträgt 20.000 Stück.
Die Fertigungskapazität der Firma beträgt 50 Wochen (je 5 Arbeitstage im Zweischichtbetrieb mit 8 Arbeitsstunden (=480 Minuten) pro Schicht).
Jeder Prozess muss somit in der Lage sein, alle 12 Minuten ein Produkt herzustellen, um den durchschnittlichen Kundenbedarf zu bedienen.
Darstellung des Wertstroms (Wertstromdarstellung)
Die Analyse wird meist rückwärts vorgehend vom Endkunden (Customer) über die Produktion (Producer) bis zu den Lieferanten (Supplier) durchgeführt. In der Wertstromdarstellung werden Produktion, Logistik und Informationsfluss mit definierten Symbolen dargestellt.
Produktionsprozesse
Die Produktionsprozesse werden als Kasten dargestellt, in dem die zentralen Kennwerte notiert sind. Dazu zählen beispielsweise:
- Bearbeitungs- und Rüstzeiten
- Anzahl an Mitarbeitern
- Anzahl produzierter Varianten

Materialfluss
Der Materialfluss zwischen den Prozessen wird abhängig von der Art der Verknüpfung eingezeichnet:
- Verknüpfungen ohne Reihenfolgevertauschung werden über das FIFO-Symbol dargestellt. (FIFO-Verknüpfung)
- Push-Verbindungen bei denen der vorhergehende Prozess den Materialfluss bestimmt werden über einen Pfeil dargestellt.
Lager werden über ein Dreieck dargestellt, unter dem die entsprechenden Kennzahlen notiert sind. Dazu zählt insbesondere der Lagerbestand sowie die Lagerbestandsreichweite. Zur Abschätzung der Lagerreichweite wird der Lagerbestand durch die durchschnittliche Tagesstückzahl geteilt. Mit Kanban gesteuerte Lager werden als Supermarkt-Regal skizziert.
Beispiel (Lagerreichweite)
Ein Lagerbestand von 280 Stück hat bei einem Tagesbedarf von 80 Stück eine Reichweite von 3,5 Tagen.
Informationsfluss Abschließend wird der Informationsfluss aufgenommen. Dieser skizziert, wie die Produktionsprozesse und Lager gesteuert werden. Die Symbole orientieren sich an denen des Programmablaufplans.
Ableitung von Potentialen
Durch die Darstellung der Produktion als Wertstrom lassen sich zwei zentrale Potentiale identifizieren. Ziel ist die Reduktion der Lieferzeiten aus Kundensicht und die Erhöhung der Auslastung durch eine gleichmäßige Taktabstimmung.
Flussgrad
Kenndatum der Wertstromanalyse ist der Anteil der reinen Bearbeitungszeit an der gesamten Durchlaufzeit, der sogenannte Flussgrad. Bei einer Gesamtdurchlaufzeit von beispielsweise 4 Wochen kann die reine Bearbeitungszeit lediglich 10 Minuten betragen. Wertschöpfend an diesem Prozess sind nur die 10 Minuten, in denen das Werkstück bearbeitet wird. Der Rest sind Liegezeiten als entweder unvermeidbare Nicht-Wertschöpfung oder aber Verschwendung, die es zu minimieren gilt.
Taktabstimmung
Über das Taktabstimmungsdiagramm lassen sich die Zykluszeiten der einzelnen Prozesse dem Kundentakt gegenüberstellen. Prozesse deren Zykluszeit nahe am Kundentakt liegt deuten auf Engpässe hin. Prozesse mit deutlich kürzerer Zykluszeit als der Kundentakt deuten auf Überkapazität und somit Verschwendung hin.
Nächste Schritte
Mit der Analyse wird die aktuelle Fertigungssituation modelliert. Wenn alle Daten aufgezeichnet sind, wird mit einem Wertstromdesign aufgezeigt, wo Verbesserungen möglich sind. Die Umsetzung erfolgt in der Wertstromplanung in einer sogenannten „Wertstromschleife“. Die Wertstromplanung umfasst in der Regel einen Maßnahmenplan, der beschreibt, wer wofür zuständig und verantwortlich ist, was jeweils genau erreicht werden soll und vor allem bis wann die Maßnahmen erledigt sein sollen.
Literatur
- Klaus Erlach: Wertstromdesign. Der Weg zur schlanken Fabrik. 2. Auflage, Springer (VDI-Buch), Berlin, New York 2010, ISBN 978-3-540-89867-2
- Thomas Klevers: Wertstrom-Mapping und Wertstrom-Design. Verschwendung erkennen – Wertschöpfung steigern. mi-Fachverlag Redline GmbH, Landsberg am Lech 2007, ISBN 978-3-636-03097-9
- Mike Rother, John Shook: Learning to See – Value-stream mapping to create value and eliminate muda. Lean Enterprise Institute; deutsche Übersetzung: Mike Rother, John Shook: Sehen lernen – mit Wertstromdesign die Wertschöpfung erhöhen und Verschwendung beseitigen. Workbook, hrsg. vom Lean Management Institut, Aachen 2004, ISBN 978-3-9809521-1-8
Einzelnachweise
- Klaus Erlach: Wertstromdesign. 2010, S. 38, doi:10.1007/978-3-540-89867-2 (springer.com [abgerufen am 9. November 2020]).