Kanban
Kanban ist eine Methode der Produktionsprozesssteuerung. Das Vorgehen orientiert sich ausschließlich am tatsächlichen Verbrauch von Materialien am Bereitstell- und Verbrauchsort. Kanban ermöglicht eine Reduktion der lokalen Bestände von Vorprodukten in und nahe der Produktion, die dort in Produkten der nächsten Integrationsstufe verbaut werden.
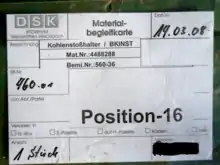
Ziel der Kanban-Methode ist es, die Wertschöpfungskette auf jeder Fertigungs-/Produktionsstufe einer mehrstufigen Integrationskette kostenoptimal zu steuern. Dabei erfolgen die Entnahmen aus den jeweiligen Pufferlagern und das Nachliefern in dieselben Pufferlager asynchron. Durch das Verteilen der Pufferlager in der Produktion entlang der Integrationskette wird mit einfachen Mitteln der Information und mit kurzen Wegen des Transports eine einfache Lösung erreicht.
Kanban entstammt dem Japanischen. Dort heißt かんばん (看板) so viel wie „Karte“, „Tafel“ oder „Beleg“. Kanban ist eine Umsetzung des unter den Synonymen Hol-, Zuruf- oder Pull-Prinzip bekannten Steuerungsverfahrens.
Historische Entwicklung
Das ursprüngliche Kanban-System wurde 1947 von Taiichi Ōno in der japanischen Toyota Motor Corporation entwickelt. Ein Grund hierfür war die ungenügende Produktivität des Unternehmens im Vergleich zu US-amerikanischen Konkurrenten. Ōno beschrieb die Idee so: „Es müsste doch möglich sein, den Materialfluss in der Produktion nach dem Supermarkt-Prinzip zu organisieren, das heißt, ein Verbraucher entnimmt aus dem Regal eine Ware bestimmter Spezifikation und Menge; die Lücke wird bemerkt und wieder aufgefüllt“.[1]
Ebenso stellten die gestiegenen Erwartungen der Kunden an die Produktionsgeschwindigkeit und Lieferbereitschaft sowie die immer engeren Zuliefererbeziehungen zwischen den Unternehmen eine neue Situation dar, für die eine geeignete Lösung gefunden werden musste. Hohe und damit, insbesondere in einem räumlich beengten Inselstaat wie Japan, kostenintensive Lagerbestände an Rohmaterial und Halbfertigmaterialien waren hierbei die Kostentreiber. Um diese Kosten zu minimieren, wurde eine flexible und effiziente Fertigungssystematik gesucht. Diese fand man im Kanban-Verfahren, das bisherige gängige Verfahren der Produktionssteuerung und der Intralogistik ersetzte. Die eigentliche Produktion blieb davon unberührt. Daraufhin wurde dieses Konzept der kurzfristigen Disposition von zahlreichen japanischen Unternehmen übernommen, an die jeweiligen Anforderungen angepasst und schließlich im gesamten Toyota-Konzern eingeführt. In den 1970er Jahren wurde dieses Steuerungskonzept von Unternehmen in den USA und Deutschland adaptiert und eingeführt. Verbunden mit Toyota und damit Japan ist auch die Bedeutung des Wortes Kanban, das „Schild“ oder „Kärtchen“ bedeutet. Diese Karten sind Basiselement dieser PPS-Systematik und dienen der einfachen Informationsweiterleitung.
Vorteile gegenüber der zentralen Produktionssteuerung
In traditionellen, zentral gesteuerten Planungssystemen der Produktionssteuerung wird der gesamte Materialbedarf an einer zentralen Stelle bis ins kleinste Detail vorausgeplant. Die einzelnen Produktionsstellen haben kaum die Möglichkeit, bei Schwankungen im Durchsatz den Zufluss an Material zu beeinflussen. Diese Tatsache machte diese Systeme in herkömmlicher Organisation mit schwacher IT-Unterstützung unflexibel und im Falle kurzfristiger Änderungen der zu produzierenden Teile auch träge, da diese Änderungen weitreichende Folgen und einen hohen Koordinationsaufwand nach sich ziehen. Dies führt dazu, dass bei zentral geplanten Systemen eine hohe Vorratshaltung nötig ist, um die mangelnde Flexibilität zu kompensieren, was wiederum hohe Lagerhaltungskosten verursacht.
Im Gegensatz hierzu bietet die Kanban-Systematik ein hohes Anpassungspotenzial bei kurzfristigen Änderungen des Bedarfs, da mit dem Zur-Neige-Gehen eines benötigten Vorprodukts der Auftrag zur Nachproduktion zeitnah ausgelöst wird. Hier erfolgt die Informationsweiterleitung stets aktuell und somit angepasst an die momentane Bedarfssituation vom Verbraucher zum Produzenten oder zum Lieferanten. Dadurch lassen sich unnötige Lagerbestände drastisch reduzieren und die Durchlaufzeiten deutlich verkürzen.
Kanban stellt eine Möglichkeit für Unternehmen dar, die teilweise sehr aufwendige und verschachtelte Produktionssteuerung mit autonomen Regelkreisen zu bedienen, was den Steuerungsaufwand deutlich reduziert und die Transparenz der Prozesszusammenhänge erhöht. Im Vorfeld jedoch sind die lokalen Ketten und das Erzeugnisspektrum genau auf die Methode mit Kanban einzustellen. Wenn diese Vorbereitung erfüllt wird, ist Kanban besonders für Unternehmen mit relativ geringer Variantenvielfalt und relativ konstantem Verbrauch interessant, bei denen Lagerkosten ein großer Kostenfaktor sind.
Aber auch bei größerer Variantenvielfalt oder langen Lieferketten kann Kanban sinnvoll verwendet werden, wenn beispielsweise moderne Informationstechnik eingesetzt wird. Hier ist jedoch ein erheblich größerer Planungs- und Koordinationsaufwand nötig.
Ungeeignet ist Kanban für Einzelprodukte oder für Sonderaufträge oder gar Projektfertigung, da hier die benötigte Standardisierung des Produktionsprogramms nicht gegeben ist.
Durch das erreichte hohe Maß an Flexibilität und Liefertreue sind JIT-Aufträge mit Kanban leichter zu bewältigen als mit herkömmlichen PPS-Systemen.
Durch die gesteigerte Verantwortung und Qualifizierung innerhalb der Regelkreise kann die Motivation der Mitarbeiter erheblich gesteigert werden.
Ziele
Ziel von Kanban-Systemen ist die Reduzierung von Lagerbeständen und damit Reduzierung von Kapitalbindung und eine Erhöhung der Flexibilität im Hinblick auf geänderte Bedarfsmengen. Dieses Ziel soll ohne Verluste von Lieferbereitschaft, ohne Verschlechterung von Ausschussquoten, ohne Erhöhung von Nacharbeit, zusätzlichen Transporten etc. erzielt werden. Dies alles soll dabei mit stark vermindertem Planungsaufwand erfolgen.
Die häufig beobachteten Verbesserungen im Bereich Lieferbereitschaft, Ausschussquoten, Nacharbeit etc. sind sekundäre Effekte.
Voraussetzungen für die Anwendung von Kanban
Kanban verlangt von Unternehmen unter Umständen eine Vielzahl von Veränderungen, um dieses Materialsteuerungssystem wirksam einzuführen. Takeda nennt sieben essenzielle Voraussetzungen, die vor dem Einsatz von Kanban unbedingt erfüllt sein müssen.[2]
- Aufbau einer Fließfertigung
- Das Produktionsprogramm muss in gleichmäßigen Fluss gebracht werden. Das heißt, der Standardisierungsgrad der Produkte muss erhöht und die Produktion streng getaktet werden.
- Verkleinerung der Losgrößen
- Um eine Just-in-time-Produktion zu erreichen und eine Senkung der Lagerbestände zu erzielen, muss von der herkömmlichen Optimierung der Losgrößen Abstand genommen werden. Ziel hingegen muss die Vermeidung von Überproduktion sein, um eine bedarfsgemäße Produktion zu verwirklichen. Rüstkosten sind hierbei eher zu vernachlässigen.
- Geglättete Produktion
- Da sich die Kanban-Systematik über mehrere Produktionsstufen erstreckt, ist die Vermeidung großer Schwankungen und die genaue Planung der Produktion auf der letzten Stufe äußerst wichtig. Jede unvorhergesehene Schwankung würde sich auf die vorgelagerten Stufen übertragen und zu Belastungen führen, was wiederum Pufferbestände oder Pufferkapazitäten nach sich ziehen und somit Verschwendung darstellen würde.
- Verkürzung und Vereinheitlichung der Transportzyklen
- Die Reduzierung von Lagerbeständen erfordert einen erhöhten Transportaufwand. Damit die Produktion durch ausbleibende Vorprodukte nicht ins Stocken gerät, ist sicherzustellen, dass der Materialtransport von der vorgelagerten zur nachfolgenden Stelle stets nach dem logistischen Prinzip erfolgt.
- Kontinuierliche Produktion
- Durch Kanban soll eine konsequente Auslastung der Produktionsstellen erreicht werden. Dies muss durch eine geeignete Dimensionierung und Standardisierung des Kanban-Systems erfolgen. Jedoch müssen auch Fälle wie Sonderaufträge berücksichtigt werden können.
- Bestimmung der Adressen
- Da der Materialfluss im Kanban-System durch Karten gesteuert wird, benötigt jede produzierende und verbrauchende Stelle sowie jedes Pufferlager und jeder Artikel eine eindeutige Bezeichnung, womit eine genaue Zuteilung der Karten, Materialien und Behälter möglich wird. Diese Systematik muss so transparent und einfach wie möglich gehalten werden, um Fehler zu vermeiden.
- Konsequentes Behältermanagement
- Behälter erfüllen beim Transport mehrere Aufgaben. So stellen sie unter anderem den beschädigungsfreien Transport der Produkte sicher und geben über Anzahl und Art des Inhaltes Aufschluss. Bei der Wahl des Behälters ist auf die Bedürfnisse des nachfolgenden Prozesses zu achten und es ist eine möglichst kleine Behältergröße zu wählen.
Weiterhin sind hohe Qualität der Vorprodukte in Verbindung mit einer ausgeprägten Qualitätssicherung Schlüsselvoraussetzungen für ein funktionierendes Kanban-System, da durch die niedrigen Lagerbestände eine Kompensation von Schlechtteilen zu Stockungen im Produktionsablauf führen kann. Deshalb muss ein Qualitätsmanagement-System implementiert werden, das aus automatischen Qualitätskontrollen, Selbstkontrolle durch die Mitarbeiter und aus Prozesskontrollen besteht.
Eignung für die Kanban-Fertigung
Kanban ist als Steuerungsinstrument für die Produktion nicht in jedem Fall geeignet. Neben den genannten Voraussetzungen für den Einsatz von Kanban muss insbesondere die Erzeugnisstruktur auf Kanban ausgerichtet sein. Hier sind die wichtigsten Kriterien, die erfüllt sein müssen:
- Es eignen sich besonders Produkte mit hohem Wertanteil und hoher mengenmäßiger Vorhersagegenauigkeit, geringen Nachfrageschwankungen (AB/XY-Artikel) und niedrigem Anteil an Sonderwünschen. Eine große Variantenvielfalt, Einzelfertigung oder häufige Produktänderungen können für die Kanban-Systematik hingegen problematisch werden und sind daher weniger gut geeignet.
- Im Fertigungsbereich sind nur Produktionsstätten geeignet, die sich durch relativ konstante und niedrige Rüstzeiten, qualifiziertes Personal sowie ausreichende und relativ flexibel disponierbare Kapazitäten auszeichnen.
- Wenn Kanban zur Steuerung des externen Einkaufes verwendet werden soll, sind sowohl die Eignung der Zulieferer zu hoher Liefertreue als auch eine gleich bleibend hohe Qualität ausschlaggebend.
Sind die Voraussetzungen und die Kriterien nicht erfüllt, ergeben sich Probleme, die das Scheitern einer Einführung des Kanban-Systems zur Folge haben können. Daher ist es von eminenter Wichtigkeit, diese Punkte im Vorfeld kritisch zu begutachten und bei Bedarf Änderungen in den Abläufen vorzunehmen.
Einsatzgebiete
Das System lässt sich sehr gut bei einstufiger Produktionstiefe (Endproduktfertigung) zur Versorgung der Fertigungseinrichtungen mit Teilen aus dem Lager einsetzen. Eine Reduzierung des Lagerbestands ist dann allein damit aber nicht möglich.
Kanban lässt sich generell in den meisten Fertigungsbereichen einsetzen, unabhängig ob die Teile aus dem Lager entnommen oder erst gefertigt werden. In größeren Fertigungsstätten muss das Holen der Teile (und damit die automatische Bedarfsmeldung) durch ein selbstständiges innerbetriebliches Transportwesen erfolgen. Insbesondere für relativ standardisierte Produkte mit geringer Variantenanzahl bei relativ konstanter Nachfrage ist Kanban geeignet.
Zudem eignet sich Kanban für produzierende Unternehmen, die in einem sich schnell wandelnden Markt tätig sind. Die Reduktion der Eigenkapitalbindung erlaubt es ohne große Verluste die Produktpalette zu wechseln, um agil am Markt bestehen zu können.
Letztlich eignet sich Kanban insbesondere für Reihenfertigung.
Kanban ist ungeeignet für Einzelfertigung. Auch der Einkauf von Rohmaterial und Teilen lässt sich darüber nicht abwickeln. Ebenso ist es nicht geeignet bei sperrigen Teilen (beispielsweise Verpackungen), die jeweils in Lkw- beziehungsweise Containergröße angeliefert werden.
Funktionsweise eines Kanban-Systems
Ein Kanban-System wird grundsätzlich von der Produktion der letzten Fertigungsstufe gesteuert: Unterschreitet dort der Lagerbestand eines bestimmten Materials einen definierten Mindestwert (Meldebestand), wird dies an die vorgelagerte Produktionseinheit bzw. das zuständige Lager gemeldet. Das stößt ggf. Fertigung und dann die Bereitstellung des Materials für den Einsatzort an.
Im klassischen Kanban-System nutzt diese Kommunikationskette die Kanban-Karten, die mit den gefüllten Transportbehältern an die Senke geliefert werden. Sobald der Inhalt des Behälters verbraucht ist, legt die Senke die Kanban-Karte in eine Kanban-Sammelbox. Die Karten werden regelmäßig an die zuständigen Quellen verteilt. Die Quelle ist dann für die rechtzeitige Bereitstellung des benötigten Materials bei der Senke verantwortlich.
Nach Erhalt der Kanban-Karte beginnt die Quelle mit der Produktion bzw. Bereitstellung der auf der Karte festgelegten Art und Menge des Materials und lagert diese in Kanban-Behältern. Sobald der Kanban-Behälter mit der geforderten Menge gefüllt ist, wird er mit der Kanban-Karte in das Pufferlager der Quelle transportiert. Von dort aus versorgt sich die Senke dann selbst. So entsteht ein sich selbst steuernder Regelkreis ohne zentrale Planungsinstanz.
Oft wird dieses System auch mit einem Supermarkt verglichen, bei dem sich die Kunden (Senken) selbst bedienen und das Personal (Quellen) für ausreichende Bestände in den Regalen (Pufferlager) sorgt. Erreicht die verbrauchende Stelle wieder den Meldebestand, beginnt der Zyklus von Neuem.
Generell unterscheiden lassen sich das Zweikartensystem, das mit Produktions- und Transport-Kanbans arbeitet, und das Einkartensystem, das sich der Transportbehälter als Hilfsmittel bedient.
Während das Zweikartensystem vorwiegend in der innerbetrieblichen Produktion Anwendung findet, wird die Einkartensystematik aufgrund der einfacheren Handhabung häufig für die Steuerung in Zusammenarbeit mit externen Zulieferern eingesetzt.
Damit eine ausreichende Anzahl von Kanban-Karten im System vorhanden ist, ermittelt ein Kanban-Koordinator im Vorfeld die benötigte Zahl der Karten und passt diese gegebenenfalls geänderten Umständen an. Grundsätzlich gilt für die Anzahl der Kanban-Karten im System die Regel, dass ausreichend Material zirkulieren muss, um die im Wiederbeschaffungszeitraum auftretenden Bedarfsmengen zu decken.
Kanban-Regeln
Um ein reibungsarmes Funktionieren des Kanban-Systems sicherzustellen, ist die Einhaltung verbindlicher Regeln unerlässlich. Diese sind im Einzelnen:
- Die Senke darf nur so viel Material anfordern, wie sie benötigt.
- Das bedeutet, dass nur Material mit zugehörigen Kanban-Karten im Umlauf sein darf.
- Die Senke darf nicht vorzeitig Material anfordern.
- Eine Missachtung dieser Regel würde zu Störungen im Produktionsablauf führen, da alle Kapazitäten sehr eng aufeinander abgestimmt sind.
- Die Quelle darf nicht auf Vorrat produzieren.
- Dies würde ebenfalls zu Überschreitungen in den Produktionskapazitäten führen.
- Die Quelle muss für einwandfreie Qualität der Teile sorgen.
- Mangelnde Qualität führt auf Grund der minimalen Lagerbestände zu Produktionsverzögerungen bei den nachfolgenden Stellen.
- Der Kanban-Koordinator hat für eine gleichmäßige Belastung der Produktionsstellen zu sorgen.
- Ohne gleichmäßige Belastung lassen sich Ziele wie niedrige Lagerbestände und optimaler Materialfluss nicht realisieren.
- Der Kanban-Koordinator sorgt für eine möglichst geringe Anzahl von Kanban-Karten.
- Jede einzelne Karte stellt gebundenes Material dar, welches Kosten in Form von Lagerhaltung und Transport erzeugt.
Zur Einhaltung dieser Regeln sind die Mitarbeiter, die in hohem Maße an den Funktionen des Kanban-Systems beteiligt sind, zu schulen, und die strikte Beachtung dieser Grundvoraussetzungen muss von den Mitarbeitern auch akzeptiert werden.
Elemente und Hilfsmittel der Kanban-Steuerung
Kanban-Karten
Kanban-Karten sind im klassischen Kanban-System das vorrangige Steuerungselement und der elementare Informationsträger, welcher alle für Produktion, Lagerung, Einkauf und Transport von der Quelle zur Senke relevanten Daten enthält. Diese sind unter anderem:
- Artikelnummern/Identifizierungsnummern
- Angaben über Art und Füllmenge der Transportbehälter
- Bezeichnungen der Quellen und Senken
- Arbeitsanweisungen/Qualitätsdaten
- Nummer der Kanbankarte
Gemeinhin lassen sich sechs Arten von Kanban-Karten unterscheiden:
- Produktions-Kanban
- Transport-Kanban
- Einkaufs-Kanban
- Laufkarten-Kanban
- Lager-Kanban
- Sonder-Kanban
Die Ermittlung der Anzahl an Kanban-Karten innerhalb eines Kanban-Kreises (Strecke zwischen Quelle und Senke) erfolgt auf Basis nachfolgender Formel:
hierbei bedeutet:
Anzahl Karten im System (bzw. im Kanbankreis) | |
Sammelmenge (Losgröße, die die Nachproduktion zu Beginn des Kanbankreises (Quelle) auslöst mit ) | |
Tagesverbrauch (die Stückzahl, die durchschnittlich pro Tag nachgefragt wird, d. h. aus dem betrachteten Kanbankreis abfließt (Senke)) | |
Wiederbeschaffungszeit in Arbeitstagen (intern oder extern), um SM nachzuproduzieren | |
Sicherheitszuschlag (Menge, die abgedeckt werden muss, falls doch Qualitätsprobleme oder Maschinenausfallzeiten etc. in Erscheinung treten können) | |
Stückzahl pro Behälter |
Über die Anzahl an Karten im Kanbankreis (zwischen Quelle und Senke) kann auch der geschätzte Durchschnittsbestand in Stück ermittelt werden:
Durchschnittsbestand in Stück
Dieser Wert kann deswegen herangezogen werden, da bei der Kanbansteuerung die nachgefragte Menge und die produzierte Menge keinen großen Schwankungen unterliegt; somit gleichmäßig verbraucht und nachproduziert wird.
Produktions-Kanban
Diese Kanbans lösen einen Auftrag zur Produktion des auf der Karte genannten Materials aus und werden dem Material beigelegt, welches sich im Pufferlager der Senke befindet. Sobald die Senke Material aus dem Pufferlager entnimmt, wird das Produktions-Kanban an die Quelle weitergeleitet, worauf der Produktionsauftrag ausgelöst wird.
Für den Fall, dass das erzeugte Material im selben Regelkreis bestellt wird, kann das Produktions-Kanban gleichzeitig als Transportauftrag von der Quelle zur Senke dienen. Wichtig ist, dass gemäß den aufgeführten Kanban-Regeln keine Produktion ohne Produktions-Kanban erfolgen darf, da andernfalls die Produktion nicht mehr verbrauchsgesteuert ist.
Transport-Kanban
Sobald eine Senke einen Behälter vollständig verbraucht hat, bezieht sie durch die Weiterleitung eines Transport-Kanbans Nachschub aus dem Pufferlager. Dort wird das dem Transportbehälter beiliegende Produktions-Kanban durch das Transport-Kanban der Senke ersetzt, und das benötigte Material wird gemäß den Informationen auf der Karte der Senke zugeführt. Somit dient das Transport-Kanban als innerbetrieblicher Transportauftrag. Gleichzeitig wird das dem Kanban-Behälter beiliegende Produktions-Kanban an die Quelle geschickt und löst eine Nachproduktion aus.
Kanban-Behälter
Alternativ zu der dargestellten Kartensystematik lassen sich Kanban-Regelkreise auch über die zum Transport der Materialien nötigen Behälter steuern. Hierzu werden alle benötigten Informationen an den Transportbehältern selbst angebracht, und die Steuerung der Produktion erfolgt über Beobachtung der verbrauchten Behälter. Das heißt also, dass mit dem Eingang eines leeren Behälters bei der Quelle der Produktionsauftrag entsteht (Behälter-Kanban). Unabhängig davon, ob nun mittels Zweikartenkanban oder Behälterkanban gesteuert wird, gilt es, bei der Gestaltung der Transportbehälter die Größe und Form der Teile sowie die Handhabung, Sicherheit und Unterscheidbarkeit der Behälter sicherzustellen. Um hier eventuellen Verwechslungen vorzubeugen, muss auf jedem Kanban-Behälter das mit dem Behälter zu transportierende Material z. B. über eine Artikelnummer vermerkt sein. Um unnötige und kostenträchtige Transporte zu vermeiden, sollte die Größe des Behälters der Produktionslosgröße des Materials angepasst sein.
Kanban-Tafeln
Kanban-Tafeln erfüllen mehrere Funktionen in den Regelkreisen. Zum einen dienen sie der Reihenfolgeplanung der durch verschiedene Kanban-Karten ausgelösten Produktionsaufträge, und zum anderen dienen sie der Kapazitätsplanung und der Einteilung der Kanbans in verschiedene Dringlichkeitsstufen. Durch Kanban-Tafeln wird auch dem Verlust von Kanban-Karten vorgebeugt, indem man ein einheitliches Aufbewahrungssystem für die am Produktionsablauf beteiligten Karten verwendet. Dieses Hilfsmittel ist zwar kein essentieller Bestandteil eines Kanban-Systems, jedoch empfiehlt sich die Verwendung solcher Tafeln aus oben genannten Gründen.
Eintreffende Kanban-Karten werden ihrer Artikelnummer entsprechend in die freien Felder der Tafel von links beginnend abgelegt. Eines dieser Felder ist mit "Start" markiert. Sobald eine neu eingetroffene Karte auf dem „Start“-Feld abgelegt wird, werden alle diese Artikelnummer betreffenden Produktionsaufträge ausgeführt. Zusätzlich kann das Feld „Eilt“ für Sonderaufträge verwendet werden. Wichtig für eine funktionierende Kanban-Tafel ist, dass die Anzahl der zuzuordnenden Karten nicht zu hoch wird. Andernfalls entfällt der Vorteil der Übersichtlichkeit, und mögliche Störungen oder Engpässe im System werden nicht erkannt.
Kanban-Tafeln mit Strichcode
Neben der Signalisierung der Zustände „Voll“ und „Nachzuliefern“ besteht die Möglichkeit mit dreistufigen Informationen auch den Zustand „Bestellt“ oder „Wird in Kürze geliefert“ darzustellen. Es wird mit einem einfachen Schiebemechanismus der Zustand des Kanban-Behälters allen Beteiligten an dem Materialkreislauf dargestellt. So bedeutet z. B. die Farbe Grün „Voll“ oder „ausreichend Material enthalten“. Wird durch Verschieben der Tafel der Strichcode sichtbar z. B. auf gelben Untergrund, bedeutet das die Anforderung zur Nachlieferung. Durch Scannen des Strichcodes wird der Lieferauftrag erzeugt und elektronisch verarbeitet, im gleichen Zuge wird die Tafel weiter verschoben auf z. B. Rot, so ist der Scanvorgang dokumentiert und allen wird signalisiert, dass die Ware in Kürze kommt. Ein Beispiel für so eine Schiebetafel ist SLIDELOG. Besonders geeignet ist diese Vorgehensweise an den Endpunkten von EDV-Systemen, bei denen eine vollelektronische Erfassung umständlich oder zu zeitintensiv wäre.
Signal-Kanban für Pufferbestände
Eine weitere Kanbanform funktioniert ohne bewegliche Karten als Hilfsmittel: Die Steuerung erfolgt durch visuelle Überwachung der Pufferbestände, welche an festgelegten Plätzen in der Nähe der Quelle gelagert werden. Diese Lagerplätze sind durch ortsfeste, meist dreieckige Karten, welche Maximal- und Minimalbestände ausweisen, gekennzeichnet. Sobald eine Materialart den Minimalbestand erreicht hat, beginnt die Nachproduktion. Es empfiehlt sich eine Einteilung einer solchen Lagerfläche in verschiedenfarbige Segmente, um die Übersichtlichkeit für die Quelle zu erhöhen.
E-Kanban
Moderne Produktionssysteme sind aufgrund ihrer Komplexität und Variantenvielfalt häufig auf starken Einsatz von Informationstechnologie angewiesen. Daher wurde es für Unternehmen wichtig, die eingeführte Kanban-Systematik in ihr PPS-System zu integrieren. Für diese Integration werden von verschiedenen Herstellern, wie z. B. SAP, CellFusion und anderen, Lösungen angeboten, die eine kanbangesteuerte Zuliefererkette auch über das Internet ermöglichen. Dadurch wird Kanban auch für Unternehmen möglich, deren Standorte weit verteilt sind, oder die auf andere Unternehmen als Zulieferer angewiesen sind. Jedoch entstehen hierbei zahlreiche Schnittstellen, die von einem solchen PPS-System bedient werden müssen. Unter anderem sind die Bereiche Produktionssteuerung, Einkauf, Qualitätssicherung, Transport und Montage betroffen und müssen Elemente der EDV sein. Um eine von den Mitarbeitern leicht zu bedienende und damit fehlerarme Systematik zu schaffen, empfiehlt sich der Einsatz von Kanban-Karten, welche mit Barcodes versehen sind. Durch diese kann der Status eines Artikels von „vorhanden“ auf „Nachproduktion“ umgestellt werden und somit automatisch einen Produktionsauftrag beim Lieferanten auslösen. Bei Wareneingang wird das Material durch erneutes Abscannen wieder als „vorhanden“ eingebucht. Von besonderer Wichtigkeit ist, dass sowohl Verbrauch als auch Eingang von Materialien von den Mitarbeitern konsequent erfasst werden. Andernfalls können sich aufgrund der unter Umständen langen Lieferzeiten wiederum Stockungen in der Produktion ergeben.
Ein weiterer Vorteil eines EDV-gestützten Kanban-Systems ist, dass sich alle Regelkreise, Quellen und Senken sowie Pufferlager jederzeit grafisch darstellen lassen und somit Engpässen oder Problemen schnell entgegengewirkt werden kann. Oft wird die Zuliefererkette durch dynamische Netzpläne grafisch dargestellt, wodurch eine Identifikation von Schwachstellen in dieser leichter erfolgen kann. Ein Beispiel für den erfolgreichen Einsatz von E-Kanban über eine große räumliche Distanz stellt das Daimler-Werk in Sindelfingen dar, welches die Bestellung von Sitzleder bis zum Erzeuger in Südafrika erfolgreich steuert.
Beispiel aus der Produktion
Die praktische Umsetzung eines elektronischen Kanban-Systems soll am realen Beispiel eines Luxusartikelherstellers verdeutlicht werden, welcher im Jahr 2003 ein solches System einführte. Die Zielsetzung war, die Durchlaufzeiten für die Produktion sowie die damit verbundene Kapitalbindung zu reduzieren. Von Vorteil erwies sich der hohe Anteil von AB-XY-Teilen mit ca. 66 % bei den Produkten des Herstellers, welche sich durch ihren relativ konstanten Verbrauch gut für die Kanban-Fertigung eigneten und einen großen Teil des Gesamtumsatzes ausmachten. Für die verbleibenden Teile, welche durch ihre geringe Prognostizierbarkeit und Verbrauch weniger gut für Kanban geeignet waren, wurden größere Lagerbestände eingeführt, um Schwankungen im Bedarf zu kompensieren. Ebenso sollten die bis dahin vorhandenen hohen Lagerbestände deutlich reduziert und gleichzeitig die Liefertreue gesteigert werden. Im Vorfeld wurden die beteiligten Prozesse einer genauen Prüfung auf ihre Eignung unterzogen und die Mitarbeiter umfassend geschult, um Verständnis und Akzeptanz für das neue System zu erzielen. Als Software wurde das bereits im Unternehmen vorhandene System um die Kanban-Funktionalität erweitert, was softwareseitige Probleme minimierte. Um eine möglichst fehlerfreie Auftragsverwaltung zu schaffen, wurde eine Barcode-Systematik eingeführt, welche durch einfaches Abscannen der Kanban-Karten Produktionsaufträge auslöst und auch abschließt. Externe Zulieferer, die die Voraussetzungen für Kanban erfüllen konnten, sind mittlerweile direkt in die Kanban-Regelkreise integriert, und die restlichen Zulieferer wenden Meldebestandsverfahren an, um ihre herkömmlichen PPS-Systeme weiterhin verwenden zu können.
Insgesamt führte dies zu einer Senkung der Lagerbestände um 48 % und durch Reduktion der Rüstzeiten und Produktionslosgrößen zu einer gesteigerten Flexibilität bei Bedarfsänderungen. Ebenso konnte die Lieferbereitschaft auf 98 % erhöht werden, was bisher durch Bevorratung in Lagern nicht zu erreichen war. Somit konnte die Fertigung effizienter gestaltet und die Kundenzufriedenheit gesteigert werden, was das Unternehmen als sehr positiv wertet.
Nachteile und Probleme
Obwohl sich das System einfach anhört, ist die Umsetzung komplex. An der Verbrauchsstelle muss Platz sein für mindestens zwei Gebinde jeden Teils. Die Gebindegröße und die Anzahl der Gebinde ist abhängig von den räumlichen Maßen der einzelnen Artikel, dem Materialbedarf pro Tag, dem angestrebten Sicherheitsbestand, der angestrebten Reichweite des Vorrats und somit der Frequenz des Auffüllens und dem Platzangebot an der Verbrauchsstelle. Die Vorfertigung und der innerbetriebliche Transport müssen abgewickelt werden können, ehe der Vorrat an der Verbrauchsstelle erschöpft ist.
Es gibt zudem auch Produktionsabläufe, in denen statt nach Verbrauch „auf Halde“ produziert wird; beispielsweise Kunststoffteile oder Stanzteile. Das Einrichten der Maschinen (Formenwechsel beziehungsweise Werkzeugwechsel) dauert lange und die Anlaufverluste (Ausschuss) sind hoch. Hier wird entweder nach Durchschnittsverbrauch, aufgrund eines Absatzplans oder eines Regelkreises mit Auslösebestand, Mindestbestand, Höchstbestand und eventuell optimaler Losgröße der Bedarf einer bestimmten Periode befriedigt.
Siehe auch
Literatur
- K. Bichler, N. Schröter: Praxisorientierte Logistik. 1. Auflage. Stuttgart/Berlin/Köln 1995.
- P. Dickmann: Schlanker Materialfluss. 2. Auflage. Springer, Berlin 2008, ISBN 978-3-540-79514-8.
- G. Geiger, E. Hering, R. Kummer: Kanban. 2. Auflage. München/Wien 2003.
- Taiichi Ohno: Das Toyota-Produktionssystem. Campus, Frankfurt am Main 1993, ISBN 3-593-37801-9.
- Hitoshi Takeda: Das synchrone Produktionssystem. 2. Auflage. Landsberg 1999.
- Hans-Otto Günther, Horst Tempelmeier: Produktion und Logistik. 7. Auflage. Springer, Berlin 2007, ISBN 978-3-540-74152-7.
- Ulrich Thonemann: Operations Management. 2005, ISBN 3-8273-7120-1.
- Ulrich Thonemann et al.: Supply Chain Champions. Financial Times Deutschland/Gabler, 2003, ISBN 3-409-12441-1.
- Rainer Weber: Zeitgemäße Materialwirtschaft mit Lagerhaltung. ISBN 3-8169-2670-3.
- Horst Wildemann: Kanban-Produktionssteuerung. 9. Auflage. München 2001, ISBN 3-929918-19-6.
- Taiichi Ohno: Das Toyota-Produktionssystem. Campus, Frankfurt am Main 2009, ISBN 3-593-38836-7.
- Steffen Lohmann: Bestandsregelnde Kapazitätssteuerung. Stuttgart 2010, ISBN 978-3-8396-0115-0.
Weblinks
- Beschreibung des Kanban bei Toyota (englisch)
Einzelnachweise
- Günther Zäpfel: Strategisches Produktions-Management. 2. Auflage. Oldenbourg, 2000, S. 228.
- Philipp Dickmann: Schlanker Materialfluss. 2. Auflage. Springer, 2008, S. 231.