Refiner
Als Refiner bezeichnet man von einem Gehäuse ummantelte Maschinen, die in der Papierindustrie vor allem zur Erzeugung von Holzstoffen verwendet werden. Mit Refinern werden hauptsächlich Hackschnitzel mechanisch zerfasert und die Fasern mechanisch bearbeitet (Faserstoffmahlung). Der Refiner wird aber auch zur Bearbeitung von Altpapier verwendet, hierbei werden aber meist nur die Langfasern bearbeitet. Diese werden mittels Fraktionierung von den Kurzfasern getrennt.[1]
Geschichte
Bis ins 19. Jahrhundert hinein waren Hadern (Lumpen) der bevorzugte und hauptsächlich verwendete Rohstoff für die Produktion von Papier. Doch schon während des 18. Jahrhunderts wurde aufgrund des Mangels beim Nachschub an Lumpen intensiv an alternativen Rohstoffen für die Papierherstellung geforscht. Den Durchbruch brachten Erfindungen zur Gewinnung von Holzfasern, die sich für die Herstellung von Papier optimal eignen. Im Jahr 1843 erfand Friedrich Gottlob Keller den mechanischen Holzaufschluss zur Erzeugung von Holzschliff (Weißschliff). 1850 erfand der Amerikaner Joseph Jordan den ersten Refiner: eine Kegelstoffmühle, die nach ihm auch Jordan-Mühle genannt wird.[2] Jordan ließ sich die Erfindung im Jahr 1858 patentieren. 1851 erfanden die Chemiker Hugh Burgess und Charles Watt die Herstellung von Zellstoff aus Holz mittels eines Natronverfahrens.[2]
Durch die große Nachfrage nach Papier wurden die mechanischen und chemischen Holzaufschlussverfahren immer weiter optimiert. Diese Optimierungsentwicklung zog sich durch das gesamte 20. Jahrhundert und hält bis heute an.[3] Erst um 1960 waren die Refiner so weit entwickelt, dass sie die bis dahin noch gebräuchlichen Holländer zu verdrängen begannen.[4]
Refinerarten
Refiner werden hinsichtlich der geometrischen Form ihrer Trägerkörper unterschieden. Auf den Trägerkörpern befinden sich Mahlkörper (Mahlplatten) aus hochfestem Stahl, die verschiedene Profile aufweisen (Mahlgarnitur). Die Mahlgarnitur ist mit dem Mahlspalt maßgeblich für die Qualität des erzeugten Holzfaserstoffes verantwortlich. Man unterteilt die Refinerarten in zwei Kategorien (Scheibenrefiner, Kegelrefiner).[5]
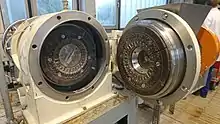
Scheibenrefiner (Scheibenmühle)
Die Scheibenrefiner weisen sowohl eine hohe Durchsatzkapazität, als auch eine hohe Leistungsfähigkeit auf. Bei den Scheibenrefinern wird das Mahlgut zwischen zwei Mahlscheiben mechanisch behandelt. Es tritt an der Rotorwelle im Zentrum ein und passiert die Mahlscheibe von innen nach außen. Auf den Mahlscheiben befinden sich die Mahlkörper, die das Holz zerfasern (Fibrillation).[5]
Die Scheibenrefiner werden mit Antriebsleistungen von 750 kW bis 11000 kW gebaut. Der Scheibendurchmesser liegt, je nach Bauart, zwischen 914 mm und 1524 mm.[5]
Einscheibenrefiner
Ein Einscheibenrefiner besteht aus einer Mahlscheibe und einem Gegenkörper. Hierbei dreht sich nur die Mahlscheibe und der mechanische Aufschluss findet zwischen Mahlscheibe und Gegenkörper, im Mahlspalt statt. Die Drehzahlen liegen hier bei 1500/min bis 1800/min.[5]
Doppelscheibenrefiner
Der Doppelscheiberefiner besteht aus zwei Mahlscheiben, die sich entgegengesetzt zueinander drehen. Hierbei findet der mechanische Aufschluss zwischen den zwei Mahlscheiben, im Mahlspalt statt. Die Drehzahlen liegen hier bei 1200/min bis 1500/min.[5]
Twin-Refiner
Der Twin-Refiner besteht aus zwei nicht drehbaren Mahlscheiben, die eine sich drehende Mahlscheibe einschließen. Die bewegliche Mahlscheibe ist beidseitig mit Mahlplatten besetzt. Die mechanische Zerfaserung findet beidseitig zwischen den starren Mahlscheiben und der beweglichen Mahlscheibe, im Mahlspalt statt. Der Twin-Refiner bietet im Vergleich zum Doppel- und Einscheibenrefiner eine doppelt so große Wirkfläche und dadurch eine höhere Durchsatzkapazität.[3]
Kegelrefiner (Kegelmühle)
Die Kegelrefiner bestehen aus einem mit Messern besetzten Kegel (Rotor), der sich in einem ebenfalls mit Messern besetzten Stator dreht. Hierbei tritt das Mahlgut an der Spitze des Kegels in den Refiner ein und wird über den jeweiligen Kegelwinkel (Konizität des Rotors) nach außen transportiert. Die Mahlung findet im Mahlspalt zwischen dem Kegel und dem Stator statt. Man unterscheidet zwischen zwei verschiedenen Arten von Kegelrefinern: Flachkegelrefiner (20–35°) und Steilkegelrefiner (ca. 60°).[6]
Die Umfangsgeschwindigkeit bei den Kegelrefinern liegt zwischen 15 m/s und 17 m/s.[6]
Flachkegelrefiner (20–35°)
Durch den kleinen Winkel kommt es bei der Abstandseinstellung zwischen Rotor- und Statormessern zu einer relativ hohen achsenbezogenen Verschiebung. Der Anpressdruck kann hier nicht so hoch gewählt werden wie beim Steilkegelrefiner.[6]
Steilkegelrefiner (ca. 60°)
Durch den steileren Winkel im Vergleich zum Flachkegelrefiner entsteht eine geringere achsenbezogene Verschiebung bei der Abstandseinstellung zwischen Rotor- und Statormessern. Der Anpressdruck kann hier höher gewählt werden als beim Flachkegelrefiner.[6]
Wirkungspaarungen
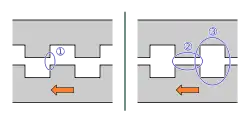
➀ Kante gegen Kante
➁ Fläche gegen Fläche
➂ Messerzelle gegen Messerzelle
Man unterscheidet zwischen drei Wirkungspaarungen. Davon sind zwei dem Nutzungsinteresse dienlich und eine stellt einen destruktiven Nebeneffekt dar.[7]
Kante ↔ Kante: Diese Wirkungspaarung ist für die ungewollte Faserkürzung verantwortlich. Die Faserkürzung ist ein negativer Nebeneffekt des Aufbaus der Mahlplatten.[7]
Fläche ↔ Fläche: Diese Wirkungspaarung ist für die Fibrillation (Auftrennung der Faser zu kleineren Fibrillen) der Zellfasern verantwortlich.[7]
Messerzelle ↔ Messerzelle: Diese Wirkungspaarung ist, wie die Wirkungspaarung Fläche ↔ Fläche, für die Fibrillation der Zellfasern verantwortlich.[7]
Refiner-Holzstoffverfahren
Durch die Refiner-Holzstoffverfahren wird aus Holz durch mechanische Zerfaserung Holzstoff gewonnen. Man unterscheidet vor allem drei verschiedene Verfahren, die aufeinander aufbauen: RMP-, TMP- und CTMP-Verfahren.[8]
RMP-Verfahren (refiner mechanical pulp)
Beim RMP-Verfahren werden die Hackschnitzel nicht thermisch vorbehandelt. In diesem Verfahren erfolgt die mechanische Zerfaserung bei Atmosphärendruck. Bei 100 °C werden die Hackschnitzel in zwei Stufen zerfasert. Die Stoffdichte beträgt in der zweiten Stufe 20–30 %. Durch die mechanische Zerfaserung entsteht so ein relativ grober Faserstoff, der bei der Papierproduktion zu vielen Qualitätsmängeln im Papier führt. Aufgrund dieses Nachteils wird das Verfahren heute kaum noch angewendet.[8]
TMP-Verfahren (thermomechanical pulp)
Beim TMP-Verfahren werden die Hackschnitzel vor der mechanischen Zerfaserung bis zu 5 Minuten lang mit 130 °C heißem Wasserdampf thermisch vorbehandelt. Im Anschluss findet die mechanische Zerfaserung bei Überdruck statt. Durch die Vorbehandlung entsteht ein sehr feiner Faserstoff, der bei der Weiterverarbeitung zu Papier wenig Qualitätsmängel aufweist. Das TMP-Verfahren hat das RMP-Verfahren fast gänzlich abgelöst.[8]
CTMP-Verfahren (chemithermomechanical pulp)
Beim CTMP-Verfahren werden die Hackschnitzel vor der mechanischen Zerfaserung zusätzlich chemisch vorbehandelt. Es erfolgt eine Imprägnierung mit Chemikalien (Natriumsulfit und Natriumcarbonat). Im Anschluss findet die Zerfaserung in zwei hintereinander geschalteten Stufen bei Überdruck statt. Die chemische Vorbehandlung führt zu einem Faserstoff ausgezeichneter Qualität, der in der Weiterverarbeitung zu Papier sehr wenig Qualitätsmängel aufweist.[8]
Siehe auch
Einzelnachweise
- Günter Krickler: Die Werkstoffe des Buchbinders. Schlüter, Hannover 1982
- Jürgen Blechschmidt (Hrsg.): Taschenbuch der Papiertechnik, Carl Hanser Verlag, 2., aktualisierte Auflage 2013, S. 27.
- Geschichte der Papierherstellung buecher-wiki.de, abgerufen am 9. November 2018.
- Jürgen Blechschmidt (Hrsg.): Taschenbuch der Papiertechnik, Carl Hanser Verlag, 2., aktualisierte Auflage 2013, S. 28.
- Lothar Göttsching, Casimir Katz: Papier Lexikon, R–Z. Euwid Verlag, ISBN 3-88640-080-8, S. 22 f.
- Lothar Göttsching, Casimir Katz: Papier Lexikon, R–Z. Euwid Verlag, ISBN 3-88640-080-8, S. 22.
- Meike Mentjes: Untersuchung des Trocknungsverhaltens von Papier bei der Anwendung von Trocknungstechniken aus der Papierrestaurierung, Konstruktion und Anwendung des Karibari-Trocknungspaneels. Siegl, München 2006.
- Lothar Göttsching, Casimir Katz: Papier Lexikon, R–Z. Euwid Verlag, ISBN 3-88640-080-8, S. 23 f.