Molded Interconnect Devices
Als Molded Interconnect Devices oder Mechatronic Integrated Devices[1] (MID), englisch für Spritzgegossene Schaltungsträger, werden spritzgegossene Kunststoffbauteile mit nach speziellen Verfahren aufgebrachten metallischen Leiterbahnen bezeichnet, die als Schaltungsträger für elektronische bzw. mechatronische Baugruppen dienen.
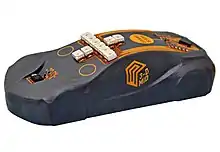
Wesentliche Einsatzgebiete für die MID-Technik sind der Automobilbau, die Industrieautomatisierung, die Medizintechnik, die Hausgeräteindustrie, die Telekommunikationstechnik, die Mess- und Analysetechnik sowie die Luft- und Raumfahrt. Das Marktvolumen der MID-Technik unterliegt einem stetigen Wachstum.
Vorteile der MID-Technik
Die Vorteile der MID-Technik liegen sowohl in der verbesserten Gestaltungsfreiheit und Umweltverträglichkeit, als auch in einem Rationalisierungspotenzial bezüglich des Herstellungsprozesses des Endproduktes.
Die verbesserte Gestaltungsfreiheit und die Integration von elektrischen und mechanischen Funktionen in ein Spritzgussteil kann zu einer Miniaturisierung der Baugruppe führen. Außerdem können neue Funktionen realisiert und beliebige Formen gestaltet werden.
Die Rationalisierungspotentiale liegen in der Reduzierung der Teileanzahl (Materialeinsparung) und der Verkürzung der Prozessketten. Des Weiteren kann durch die Reduzierung der Montageschritte die Zuverlässigkeit erhöht werden.
Durch den Einsatz der MID-Technik kann der Materialmix einer Kombination aus Leiterplatte und Mechanikkomponente (konventionelle Lösung), der meist aus vielen Werkstoffen besteht, durch ein metallisiertes Kunststoffteil (MID) ersetzt werden. MIDs werden aus rezyklierbaren Thermoplasten hergestellt und sind unkritischer bei der Entsorgung als konventionelle Leiterplatten. Das Basismaterial für eine Leiterplatte ist dagegen im Allgemeinen ein schwer entsorgbarer und nicht rezyklierbarer Duroplast.
MID-Herstellungsverfahren
MIDs können auf verschiedenste Art gefertigt werden. Die wichtigsten Verfahren zur Aufbringung der Leiterbahnen sowie von sendenden bzw. schirmenden Flächen sind der Zweikomponentenspritzguss, das Heißprägen, das Maskenbelichtungsverfahren, die Laserstrukturierung und das Folienhinterspritzen. Grundsätzlich wird zwischen subtraktiv strukturierenden und additiv metallisierenden Verfahren unterschieden.
Zweikomponentenspritzguss
Beim Zweikomponentenspritzguss wird das Werkstück in zwei Spritzgießetappen (engl.: two shot molding) hergestellt. Ein Kunststoff bildet den Grundkörper, ein weiterer ist metallisierbar und bildet das Leiterbahnlayout ab. Es gibt zwei gebräuchliche Methoden, das PCK- und das SKW-Verfahren[2].
Beim PCK-Verfahren (PCK = engl. Printed Circuit Board Kollmorgen) wird für den einen Schuss ein metallisierbarer, nicht elektrisch leitender Kunststoff verwendet. Der andere Schuss wird mit einem nicht metallisierbaren Kunststoff ausgeführt. Je nach Variante werden also die später leitenden Bereiche (Variante a) oder die später nicht leitenden Bereiche (Variante b) aufgefüllt.
Das SKW-Verfahren (SKW = engl. Sankyo Kasei Wiring Board) entspricht im Wesentlichen dem PCK-Verfahren Variante b, es verwendet jedoch zwischen den beiden Spritzgießetappen einen weiteren Prozesschritt: das später leitende, noch freiliegende Strukturteil wird bereits oberflächlich bekeimt, das heißt mit einem Katalysator (z. B. Palladium) versehen.
Nach dem zweiten Schuss hat das MID-Basisteil seine endgültige Form und es werden in den nachfolgenden Schritten die entsprechenden Metalle auf den metallisierbaren Kunststoff aufgebracht. Je nach Verfahren muss nun zunächst die Oberfläche des metallisierbaren Kunststoffs aktiviert werden (beim SKW-Verfahren entfällt dies). Auf diese Oberfläche wird galvanisch Metall aufgebracht. Dazu wird erst eine dünne Kupferschicht chemisch abgeschieden und anschließend galvanisch verstärkt.
MID-Heißprägen
Das Heißprägeverfahren ist ebenfalls ein volladditives Herstellungsverfahren, das jedoch mit sehr wenigen Arbeitsschritten auskommt. Es besitzt nur eingeschränkte Dreidimensionalität und es können nur einfache Formen hergestellt werden.
Das Spritzgussteil, das die geometrische Endform bereits besitzt, wird in eine Prägepresse eingelegt. Eine oberflächenmodifizierte Metallfolie wird mit dem Prägewerkzeug gleichzeitig gestanzt und unter Verwendung von Druck und Wärme mit dem Spritzling verbunden. Die Prägefolien sind mit einer Klebstoffschicht versehen oder haben eine Schwarzoxid-Beschichtung, die für die Haftung sorgt.
Das Heißprägen hat nur wenige Arbeitsschritte und erfordert geringe Investitionen in die Anlagen.
Laser-MID-Verfahren
Beim Laser-MID-Verfahren unterscheidet man die Laser-Direkt-Strukturierung (additiv) und die subtraktive Laserstrukturierung:
Laser-Direkt-Strukturierung (LDS)
Die Laser-Direkt-Strukturierung (LDS), auch LDS-Verfahren genannt, wurde 1997 bis 2002 an der Hochschule Ostwestfalen-Lippe in Lemgo erfunden und im Rahmen einer Forschungskooperation mit dem Unternehmen LPKF entwickelt, von den Erfindern patentiert und zunächst exklusiv an LPKF lizenziert. 2002 wurden die das LDS-Verfahren beinhaltenden Patente an die LPKF übertragen.
Das LDS-Verfahren nutzt einen thermoplastischen Kunststoff, dotiert mit einer (nichtleitenden) laseraktivierbaren Metall-Verbindung als Kunststoff-Additiv. Das Basisbauteil wird im Einkomponenten-Spritzguss hergestellt, fast ohne Limitierung bezüglich der 3D-Gestaltungsfreiheit. Ein Laserstrahl schreibt nun die späteren Leiterbahnen auf den Kunststoff. Wo der Laserstrahl auf diesen Kunststoff trifft, wird oberflächlich die Kunststoffmatrix in flüchtige Spaltprodukte zersetzt, also geringfügig abgetragen. Gleichzeitig werden aus dem Additiv Metallkeime abgespalten, die feinst verteilt in der rauen Oberfläche liegen. Diese Metallpartikel katalysieren die nachfolgende chemisch-reduktive Kupfermetallisierung. Darauf lassen sich dann galvanisch Schichten aus Kupfer, Nickel oder ein Goldfinish aufbringen. Siehe auch Kunststoffmetallisieren.
Das LDS-Verfahren erreicht bei entsprechender Laserstrahlführung volle Dreidimensionalität in einer Kugelsphäre. Es ist hochflexibel: für einen geänderten Verlauf der Leiterbahnen müssen nur neue Steuerdaten an die Lasereinheit übermittelt werden. Damit können aus einem Basisbauteil verschiedene Funktionsbauteile entstehen. Feinste Leiterbahnen mit einer Breite von < 100 µm sind möglich[3]. Darauf können deshalb sogar integrierte Schaltkreise mit der Flip-Chip-Montage platziert werden.
Mit einem speziellen, mit LDS-Additiv dotierten Lack lassen sich beliebige Körper beschichten und strukturieren. Wird also ein Bauteil z. B. in einem 3D-Drucker aus für das Laserstrukturieren ungeeigneter Plaste aufgebaut und mit dem LDS-Lack beschichtet, kann dennoch die Laser-Direkt-Strukturierung erfolgen. Die so erstellten Bauteile dienen z. B. als Funktionsmuster oder Prototyp.
Subtraktive Laserstrukturierung
Bei der subtraktiven Laserstrukturierung wird die gesamte Bauteiloberfläche metallisiert und anschließend Ätzresist aufgetragen. Mit Hilfe des Lasers wird der Ätzresist strukturiert und die freigelegte Kupferschicht weggeätzt.
Maskenbelichtungsverfahren
Das Verfahren entspricht dem konventionellen fotochemischen Herstellungsverfahren für Leiterplatten. Nach dem Spritzgießen des Kunststoffteils und der Oberflächenaktivierung erfolgt zunächst ganzflächig eine chemische Grundmetallisierung mit einer dünnen Kupferschicht. Darauf wird ein Fotolack aufgebracht.
Das Belichten mit Ultraviolett erfolgt durch eine gekrümmte Photomaske. Der belichtete Photolack wird entwickelt und entfernt und im nächsten Schritt wird die freigelegte Leiterbahngeometrie bis zur gewünschten Schichtdicke galvanisch verstärkt. Nach Entfernen des verbliebenen Photoresists wird die Grundmetallisierung weggeätzt.
Das Maskenbelichtungsverfahren erfordert viele Prozessschritte und ist wenig flexibel. Es ist nur eingeschränkt 3D-fähig, jedoch sind feinste Leiterbahnbreiten wie bei konventionellen Leiterplatten möglich.
Folienhinterspritzen
Beim Folienhinterspritzen wird eine separat hergestellte, ein- oder mehrlagige flexible Leiterbildfolie in ein Spritzgusswerkzeug eingelegt und mit geeigneten Kunststoffen hinterspritzt.
Das Folienhinterspritzen erlaubt den Strukturierungsprozess vor dem Spritzgießen. Es hat wenige Prozessschritte und beliebige Plastematerialien können verwendet werden.
Direktes Leiterzugschreiben
Wesentliche Vorteile der direkten Verfahren sind die chemie- und maskenfreie Herstellung sowie die hohe Flexibilität; es lassen sich durch geänderte Bahnsteuerung auch Einzelexemplare kostengünstig herstellen. Im Folgenden sind beispielhaft zwei der Verfahren genannt.
Flamecon
Beim sogenannten Flamecon-Verfahren wird Kupfer aufgeschmolzen und mit Druckluft oder Schutzgas auf die Trägermaterialien aufgespritzt. Zur Verbesserung der Strukturschärfe und -kanten wird vorher strukturiert ein Haftvermittler aufgetragen, sodass nur dort Material haftet. So kann das mit Primer vorstrukturierte Bauteil angeblich auch durch eine Metallschmelze gezogen werden, um die Leiterzüge aufzubringen.
Das Verfahren ist hinsichtlich der Substrate und Strukturierung ein optimiertes thermisches Spritzverfahren ähnlich dem Flammspritzen und gestattet Leiterzugbreiten >1 mm und Schichtdicken.
Plasmadust
Das sogenannte Plasmadust-Verfahren verwendet ein nichtthermisches Plasma bei Normaldruck, zusammen mit sehr feinem Metallpulver (100 nm bis 20 µm). Gegenüber dem konventionellen Plasmaspritzen ist die Plasmatemperatur so gering, dass Thermoplaste beschichtet werden können. Die Oberfläche wird durch das Plasma aktiviert, dadurch haften die Schichten gut.
Forschungsvereinigung 3-D MID
Die Forschungsvereinigung Räumliche Elektronische Baugruppen 3-D MID e. V. wurde 1993 in Erlangen gegründet. Ziel der Forschungsvereinigung ist die Förderung und Weiterentwicklung der MID-Technologie. Dazu werden Projekte zur Gemeinschaftsforschung durchgeführt, der Erfahrungsaustausch unter den Mitgliedern gefördert und durch geeignete Öffentlichkeitsarbeit die Umsetzung der neuen technischen Möglichkeiten angeregt. Ein besonderes Anliegen ist die Unterstützung kleiner und mittelständischer Unternehmen. Mit 65 Mitgliedsfirmen und 34 Forschungsinstituten der größte industrielle Forschungsverbund im Bereich der 3D-MID-Technologie weltweit.
Literatur
- J. Franke (Hrsg.): Räumliche elektronische Baugruppen (3D-MID): Werkstoffe, Herstellung, Montage und Anwendungen für spritzgegossene Schaltungsträger. Hanser, München 2013.
- Elektronik. Sonderausgabe Räumliche elektronische Baugruppen. WEKA Verlag, 2011.
- J. Franke, J. Gausemeier, C. Goth, R. Dumitrescu: MID-Studie 2011 Markt und Technologieanalyse. Paderborn 2011.
- H. Wißbrock: Laser-Direkt-Strukturieren von Kunststoffen – ein neuartiges Verfahren im Spiegel eingeführter MID-Technologien. In: Kunststoffe. 11, (2002), Vol. 92, S. 101–105.
- G. Naundorf, H. Wißbrock: Leiterbahnstrukturen und Verfahren zu ihrer Herstellung. Patent WO 2003005784, 2001.
Weblinks
- www.3d-mid.de – Offizielle Website der Forschungsvereinigung 3-D MID
Einzelnachweise
- Jörg Franke: Three-Dimensional Molded Interconnect Devices (3D-MID). Hanser, München 2014, ISBN 978-1-56990-551-7, S. V.
- Irene Fassi, David Shipley: „Micro-Manufacturing Technologies and Their Applications“; Springer-Verlag 2017; 295 Seiten; S. 181f
- https://www.plasticsportal.net/wa/plasticsEU~de_DE/function/conversions:/publish/common/upload/technical_journals/electronics_and_mechatronics/Laser_Direkt_Strukturierung_von_MID_Bauteilen.pdf Reinhard Stransky, Nils Heininger, Wolfgang John, Hans-Jürgen Boßler: „Direkt aufs Bauteil“; Zeitschrift PLASTVERARBEITER, Jahrg. 56 (2005), Nr. 4, S. 62f