Lean Development
Lean Development (auch Lean Product Development) ist die Anwendung des Lean-Management-Konzepts „Lean Production“ auf den Produktentstehungsprozess (PEP).
Die Anwendung schlanken Denkens in der Produktion hat zu großen Erfolgen geführt. Die Erfolgsgeschichte von Toyota kann aber in ihrer Dynamik und Nachhaltigkeit durch eine schlanke Produktion alleine nicht mehr erklärt werden. Durch die Analyse der vergangenen Jahre ist vielmehr deutlich geworden, dass Lean Production bei Toyota nicht etwa ein singuläres Produktionssystem ist, sondern vielmehr das Ergebnis einer Unternehmenskultur im Bereich der Produktion darstellt.
Diese schlanke Unternehmenskultur kann über die Produktion hinaus auch weitere Unternehmensprozesse prägen. Damit können traditionelle Organisationsfelder wie Innovation, F&E-Management, Vorentwicklung, Applikation, Anlaufmanagement, Entwicklungslieferanten etc. auf ein in sich geschlossenes gemeinsames Fundament gestellt werden. Erfolgt dies bei dem der Produktion direkt vorgelagerten Kernprozess der Produktentstehung spricht man von Lean Development.
Die fünf Leitprinzipien des Lean Management
- Wert: Spezifiziere präzise den Wert deines Produktes
- Wertstrom: Erkenne den Wertstrom
- Flow: Erzeuge einen Wertstromfluss ohne Unterbrechungen
- Pull: Lasse den Kunden den Takt der Bearbeitung bestimmen
- Perfektion: Verbessere die Dinge kontinuierlich
sind eben auch in der Entwicklung zu verwirklichen und prägen dann das Lean Development (engl. lean product development) des jeweiligen Unternehmens.
Vereinfachend kann man sagen, dass Lean Development im Kern darauf beruht, Strukturen, Prozesse und Werkzeuge auf Unnützes, das heißt „Verschwendung“ (jap. Muda), hin zu untersuchen und die identifizierten Schwachpunkte und deren Verschwendungsursachen durch Gegenmaßnahmen zu bekämpfen. Im Zentrum der MUDA-Eliminierung steht die Erkenntnis, dass die gleichen Gestaltungsprinzipien, die zu schlanken Produktion führen, auch auf die Leistungserstellung in der Produktentstehung anwendbar sind und dort zu einer effizienten („die Dinge richtig machen“) und effektiven („die richtigen Dinge machen“) Arbeitsfolge führen. So entsteht Lean Development, das aufgrund seiner enormen Reichweite und Hebelwirkung das Potenzial für einen nachhaltigen Wettbewerbsvorteil bietet. Die Studie „Lean Development in Deutschland“[1] hat unter anderem gezeigt, dass in Entwicklungsprozessen 20–30 % der Kapazität durch Verschwendung gebunden sind. Ziel der Lean Development Initiativen ist es, diese neu gewonnene Kapazität in wertsteigernde Tätigkeiten zu investieren, so dass z. B. die Time-to-Market verkürzt wird, mehr Projekte mit gleicher Mannschaft möglich werden, sichere Produktionsanläufe und eine bessere Produktqualität gesichert werden.
„Lean Development“ darf nicht mit dem Toyota-Produktionssystem verwechselt werden. Toyota war der Benchmark in der Studie von Womack, Jones & Roos[2] am MIT (Boston, USA). Lean ist jedoch ein aus dieser Studie entwickeltes akademisches Konstrukt, das sich bis zum heutigen Tag weiterentwickelt und im umfassenden „Lean-Thinking“-Ansatz mündet. Die zum Toyota Product Development (z. B. Morgan & Liker)[3] öffentlich zugänglichen Informationen beschreiben eher das Vorgehen für Applikationskonstruktionen und greifen damit als Kopiervorlage eher zu kurz. Unternehmen, die dem grundlegenden Lean Konzept von Toyota folgen möchten sind daher dazu aufgefordert, ein unternehmensspezifisches Lean Development (LD)-Konzept zu entwickeln.[4] Durch die Einführung von Gestaltungsprinzipien, Methoden und Werkzeugen, die an denen der schlanken Produktion angelehnt sind, ist das Lean Development in der Lage, signifikante Verbesserungen hinsichtlich Lieferzeiten und Produktentwicklungskosten zu erzielen.[5]
Lean Development ist ein noch wenig beachteter Ansatz, wobei die Studie darauf hindeutet, dass viele Unternehmen bereits auf dem Weg sind diesen aufzugreifen. Betrachtet man die aktuelle Fachliteratur, so ist zu erkennen, dass mit unterschiedlichen Herangehensweisen gearbeitet wird. Diese reichen von umfangreichen, methodischen Systembeschreibungen, über Methodenbaukästen, bis hin zu punktuell, aufgabenfixierten Praxislösungen. Es ist zu erwarten, dass sich das Konzept, getrieben durch die Praxiserfahrungen, in schnellen Schritten weiterentwickeln wird.
Gestaltungsprinzipien schlanker Produktentstehungsprozesse
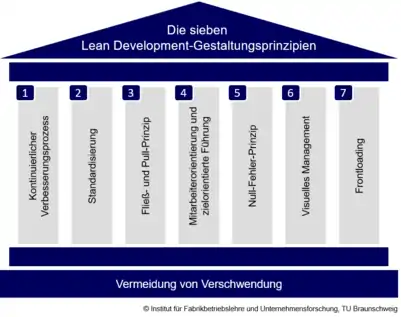
Die Umsetzung eines Lean Development Systems (LDS) basiert, analog zu einem Ganzheitlichen Produktionssystem, auf einer Reihe von Gestaltungsprinzipien, die sich im Wesentlichen auf sieben Prinzipien reduzieren lassen. Zu diesem Ergebnis kommt eine umfangreich angelegte Literaturstudie des Instituts für Fabrikbetriebslehre und Unternehmensforschung der TU Braunschweig.[6] Die Gestaltungsprinzipien basieren auf dem Fundament „Vermeidung von Verschwendungen“ und können bildlich durch ein Lean Development-Haus dargestellt werden. Die sieben Gestaltungsprinzipien werden im Folgenden kurz vorgestellt.[7]
Kontinuierlicher Verbesserungsprozess
Die kontinuierliche Verbesserung leitet sich grundsätzlich von dem kontinuierlichen Verbesserungsprozess (KVP) bei der Implementierung Ganzheitlicher Produktionssysteme ab. Unter Berücksichtigung einiger Besonderheiten kann der KVP ebenso auf die Produktentstehung angewendet werden. Hierbei darf der Verbesserungsprozess nicht auf die Produktentstehung beschränkt werden. Vielmehr muss der gesamte Produktlebenszyklus betrachtet werden, da ein Großteil der Lebenszykluskosten bereits in dem Produktentstehungsprozess fixiert wird. Die Produktentstehung ist zudem in wesentlichem Maße von Innovation und Kreativität getrieben, sodass die kontinuierliche Prozessverbesserung durch die Individualität und Einmaligkeit erschwert wird.
Methoden zur kontinuierlichen Verbesserung:
- Ideenmanagement
- A3-Methode
- PEP-Wiki
Standardisierung
Die Produktentstehung ist durch kognitive und kreative Prozesse geprägt und lässt sich aufgrund ihrer Individualität nur schwer standardisieren. Eine Unterscheidung in repetitive und kreative Prozesse erscheint sinnvoll, wobei vor allem repetitive Prozesse große Standardisierungspotenziale aufweisen. Am Beispiel Toyota können die unterschiedlichen Bereiche zur Standardisierung veranschaulicht werden:[3]
- Design-Standardisierung: Nutzung gleicher Komponenten, Plattformen, Produkte
- Prozessstandardisierung: Aufgaben und deren Reihenfolge, Arbeitsanweisungen
- Standardisierung der Ingenieurqualifikationen: Standardisierung der Fähigkeiten und Fertigkeiten von Entwicklungsingenieuren
Methoden zur Standardisierung:
- Shopfloor Management
- Kennzahlensysteme
- Projektkategorisierung
Fließ- und Pull-Prinzip
Die Einführung des Pull-Prinzips in der Produktentstehung beschränkt sich darauf, notwendige Informationen zur richtigen Zeit, in der geforderten Qualität, am richtigen Ort zur Verfügung zu stellen.[8] Eine Optimierung der Prozesse wird erzielt, indem Arbeitsaufwände gleichmäßig verteilt werden und Arbeitsphasen im nächsten Schritt durch Anwendung des KVPs stetig verkürzt werden.
Methoden zum Fließ- und Pull-Prinzip:
- Prozesssynchronisation
- Simultaneous Engineering
- Prozessorientierte Projektorganisation
Mitarbeiterorientierung und zielorientierte Führung
Im Gegensatz zur klassischen Mitarbeiterführung ist die zielorientierte Führung und Mitarbeiterorientierung im Lean Development von gegenseitigem Vertrauen geprägt. Der Mitarbeiter fungiert als Experte, der die Schwachstellen kennt und vom Führungspersonal die Befugnis erhält Missstände eigenständig zu beheben, Verbesserungen voranzutreiben und zu kontrollieren. Eine offene Kultur, frei von gegenseitigen Beschuldigungen (No-Blame-Kultur) ist dabei essenziell, um die Mitarbeiter zu motivieren, kontinuierlich Missstände aufzudecken und zu beheben.
Methoden zur Mitarbeiterorientierung und zielorientierte Führung:
- Hoshin Kanri
- Fehler- und No-Blame-Kultur
- Qualifizierungsplanung
Null-Fehler-Prinzip
Das Null-Fehler-Prinzip in der Produktentstehung betrifft zum einen die durchgehende, sorgfältige und vollständige Übergabe von Informationen innerhalb der Prozesse in einem Lean Development System. Weiterhin ist sicherzustellen, dass mögliche Missstände beim entwickelten Produkt in frühen Stadien entdeckt werden. Hierzu eignen sich Methoden wie das Rapid Prototyping oder das Cardboard Engineering.
Methoden für das Null-Fehler-Prinzip:
- Quality Function Deployment
- Rapid Prototyping
- Cardboard Engineering
Visuelles Management
Die Darstellung von Informations- und Wissensflüssen gestaltet sich im Produktentstehungsprozess teilweise schwierig, da diese häufig nicht sichtbar sind. Das visuelle Management in einem Lean Development System zielt daher auf eine transparente Darstellung von Projektfortschritten ab. Hierbei kann durch kontinuierliche, transparente Soll-Ist-Vergleiche der Stand der Entwicklung visuell und für alle Mitarbeiter sichtbar dargestellt werden.
Methoden zum visuellen Management:
Frontloading
Das Frontloading basiert auf der Erkenntnis, dass der Großteil anfallender Produktkosten in der Produktentstehung festgelegt wird. Es gilt als zentrales Gestaltungsprinzip im Lean Development und hat das Ziel, durch gründliche und weitsichtige Planungsaktivitäten künftige Verschwendungen zu vermeiden. In der Praxis werden Produktänderungen häufig erst spät veranlasst und verursachen dabei hohe Kosten. Das Lean Development versucht diesem Problem durch eine Wissenserhöhung im Bereich der Produktplanung zu begegnen, welche im Wesentlichen durch eine Aufstockung der Personalkapazitäten geschaffen werden kann. Dabei entstehende Mehrkosten können in späteren Produktlebenszyklen wieder eingespart werden.
Methoden für das Frontloading:
- Set-based Engineering
- Target Costing
- Lebenszyklusplanung
Ziele im Lean Development
Die wichtigsten Zielsetzungen eines Lean Development Systems können auf die drei Zieldimensionen
- Effektivität
- Effizienz und
- Befähiger
zurückgeführt werden.[9] Diesen Zieldimensionen können wiederum Zielgrößen zugeordnet werden.[10]
Effektivität
Effektivität im Produktentstehungsprozess beschreibt die Entwicklung von Produkten, die eine Nachfrage am Markt generieren und von Kunden erworben werden. „Die richtigen Dinge tun“ ist der Leitspruch der Effektivität und bedeutet bezogen auf den Produktentstehungsprozess, aus einer Vielzahl von Ideen, die richtigen bzw. erfolgversprechenden auszuwählen und Produkte gewinnbringend auf den Markt zu bringen. Zielsetzungen einer effektiven Produktentstehung können unter anderem sein:
- Strategiekonformes Produktportfolio
- Innovationen
- Hohe Stakeholderzufriedenheit
Effizienz
Effizienz meint „Die Dinge richtig tun“ und bedeutet in Bezug auf die Produktentstehung, eine verschwendungsarme Entwicklung zu gewährleisten, indem nicht-wertschöpfende Tätigkeiten weitestgehend reduziert werden. Zielgrößen dieser Dimension sind:
- Hohe Qualität
- Kurze Entwicklungszeiten
- Geringe Kosten
Befähiger
Befähiger beschreiben Fähigkeiten, die vonnöten sind um einen effektiven und effizienten Produktentstehungsprozess zu erreichen. Zugehörige Zielsetzungen sind:
- Qualifizierte Mitarbeiter („Können“)
- Motivierte Mitarbeiter („Wollen“)
- Fähige Organisation („Dürfen“), die einen regen Wissensaustausch von Abteilungen fördert ist notwendig. Kennzahl: Anzahl Meetings, Anzahl Eskalationen pro Projekt.
- Fähige Lieferanten
Literatur
- Uwe Dombrowski: Lean Development: Aktueller Stand und zukünftige Entwicklungen. Springer Vieweg, Heidelberg 2015
- O. Fieth, T. Huber: Einstieg in die schlanke Produktentstehung. In: CADplus Business+Engineering, 04/2005, S. 23 ff.
- H. Joka: Lean Management braucht die angstfreie konstruktive Diskussion. In: VDI nachrichten, 7. März 2008, Nr. 10, S. 19.
Weblinks
- Jan Alonso-Michel: Leadership as a Sustainable Success Factor of Lean Manufacturing. (PDF; 860 kB) MBA-Thesis, International Lean Manufacturing Consulting, April 2008 (englisch)
- Homepage des Instituts für Fabrikbetriebslehre und Unternehmensforschung
Einzelnachweise
- M. Graebsch, U. Lindemann, S. Weiß: Lean Development in Deutschland: Eine Studie über Begriffe, Verschwendung und Wirkung. Dr. Hut, München 2007, ISBN 978-3-89963-496-9
- J.P. Womack, D.T. Jones, D. Roos: The Machine That Changed the World: The Story of Lean Production – Toyota’s Secret Weapon in the Global Car Wars That Is Now Revolutionizing World Ind. Free Press, New York 2007, ISBN 978-0-7432-9979-4
- J.M. Morgan, J.K. Liker: The Toyota Product Development System – Integrating People, Process, and Technology. Productivity Press, New York 2006, ISBN 978-1-56327-282-0
- Uwe Dombrowski: Lean Development: Aktueller Stand und zukünftige Entwicklungen. Springer Vieweg, Heidelberg 2015, ISBN 978-3-662-46163-1
- Uwe Dombrowski: Lean Development: Aktueller Stand und zukünftige Entwicklungen. Springer Vieweg, Heidelberg 2015, ISBN 978-3-662-46163-1, S. 198
- Uwe Dombrowski: Lean Development: Aktueller Stand und zukünftige Entwicklungen. Springer Vieweg, Heidelberg 2015, ISBN 978-3-662-46163-1, S. 12
- Uwe Dombrowski: Lean Development: Aktueller Stand und zukünftige Entwicklungen. Springer Vieweg, Heidelberg 2015, ISBN 978-3-662-46163-1, Kap. 2
- F.J. Brunner: Japanische Erfolgskonzepte – KAIZEN, KVP, Lean Production Management, Total Productive Maintenance, Shopfloor Management, Toyota Production Management. Hanser, München 2008
- Uwe Dombrowski, K. Schmidtchen, D. Ebentreich: Balanced Key Performance Indicators in Product Development. Internat Conf on Manufacturing and Industrial Engineering. Kota Kinabalu, Malaysia, 2012
- Uwe Dombrowski: Lean Development: Aktueller Stand und zukünftige Entwicklungen. Springer Vieweg, Heidelberg 2015, ISBN 978-3-662-46163-1, S. 170–182