Innenhochdruckumformen
Innenhochdruckumformung (kurz IHU) ist dem Hydroforming (meist synonym verwandt) zuzurechnen und bedeutet das Umformen metallischer Rohre oder Hohlkörper im geschlossenen Formwerkzeug mittels Innendruck. Es ähnelt dem Tiefziehen mit Wirkmedien. Genormt ist es in der DIN 8584 und wird zum Zugdruckumformen gezählt.
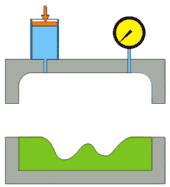
Von anderen wirkmedienbasierten Verfahren zur Umformung von metallischen Blechen, z. B. der Außenhochdruckumformung (siehe Bild rechts, englisch Sheet-Hydroforming), dem Hydraulischen Tiefziehen oder dem Hydromechanischen Tiefziehen, unterscheidet sich das Verfahren dadurch, dass das Werkstück selbst weitestgehend die Dichthülle des Druckes bildet.
Der Druck wird z. B. durch eine Wasser-Öl-Emulsion in den Hohlkörper eingebracht. Die Öffnungen werden während des Umformprozesses durch Dichtstempel, die durch Hydraulikzylinder angetrieben werden, abgedichtet. Wesentliche Prozessparameter sind dabei der Innendruck, der bis zu 30.000 bar betragen kann, sowie im Falle von Rohren das Nachschieben von Material bzw. Stauchen von den Bauteilenden her mit Hilfe der Dichtstempel. Es gibt eine Vielzahl von Verfahrensvariationen (zum Beispiel Vorform-Operationen) und -ergänzungen (zum Beispiel integrierte Lochoperationen). Die Prozesse laufen bei Raumtemperatur ab.
Das Autofrettage-Verfahren funktioniert ähnlich, soll jedoch keine Verformung des Bauteils bewirken, sondern lediglich eine Erhöhung der Festigkeit.
Geschichte
Das Verfahrensprinzip des Innenhochdruckumformens war bereits im 19. Jahrhundert bekannt. Das Verfahren basierte auf der Tatsache, dass sich beim Nachschieben des Materials von den Bauteilenden her eine Volumenänderung bzw. -reduktion im Innern ergibt, wodurch der Umformdruck aufgebaut wurde. Der Prozess konnte also nicht geregelt werden und war daher nur schwer zu beherrschen. Er gewann erst in der zweiten Hälfte des 20. Jahrhunderts wieder an Bedeutung, als die hohen Drücke im Wirkmedium erzeugt werden konnten.
Das klassische Bauteil, das mittels Innenhochdruckumformung gefertigt wurde und auch heute noch wird, ist das Kupfer-T-Stück, das z. B. in Wasserleitungen eingesetzt wird.
Im Laufe der 1990er Jahre gewann das Verfahren zunehmend an Bedeutung, als vermehrt IHU-geformte Bauteile in der Automobilindustrie eingesetzt wurden. Das erste Großserienfahrzeug, das größere IHU-Teile in der Karosserie verbaut hatte, war der Audi A8 (seit 1994).[1]
Die Innenhochdruckumformung nimmt heute als Spezialverfahren einen wichtigen Platz im Bereich der Metallumformung ein.
Verfahrenstechnik
Anlagentechnik
Die Formwerkzeuge zur Fertigung von IHU-Bauteilen werden typischerweise in hydraulischen Pressen betrieben, die um ein entsprechendes Wasserhydraulikaggregat und die zugehörige Steuerung ergänzt werden. Die hydraulische Presse dient dabei als Zuhaltevorrichtung für das Werkzeug. Aufgrund der variablen Druckverläufe im Werkzeug, die die Werkzeughälften auseinanderdrücken wollen, ist eine geregelte Zuhaltevorrichtung in den meisten Fällen unabdingbar.
Aufgrund der hohen Drücke im Werkzeug sind in der Regel Pressen mit großen Zuhaltekräften erforderlich. Auch die Werkzeugkonstruktion muss die hohen Drücke berücksichtigen, um entsprechende Standzeiten zu gewährleisten.
Verfahrensauslegung und Machbarkeitsgrenzen
Da es sich bei der Innenhochdruckumformung um ein komplexes Verfahren mit vielen verstellbaren Parametern handelt, ist oft ein hoher Aufwand zur Verfahrensauslegung erforderlich. In vielen Fällen können Machbarkeitsuntersuchungen und Verfahrensvorauslegungen mittels FEM-Simulationen durchgeführt werden. Dennoch ist oft ein Prototyping zur Bestätigung der Machbarkeit anzuraten beziehungsweise ein aufwändiger Inbetriebnahmeprozess zu erwarten.
Die Realisierbarkeit hängt im Wesentlichen von der zur Herstellung eines konkreten Bauteils erforderlichen maximalen Aufweitung/Dehnung ab. Diese darf im Normalfall nicht die Gleichmaßdehnung des eingesetzten Werkstoffs übersteigen. Lediglich im sogenannten Nachschiebebereich (Bereich in dem mit Hilfe der Dichtstempel Material nachgeschoben werden kann) kann diese partiell überschritten werden. Ist dies nicht ausreichend, so wird eventuell ein Zwischenglühprozess erforderlich.
Werkstoffe mit hohem Dehnvermögen (zum Beispiel Edelstähle, Kupfer) sind insofern besser für das IHU-Verfahren geeignet als solche mit geringem Dehnvermögen (zum Beispiel hochfeste Stähle, Aluminium). Durch Weiterentwicklungen des IHU-Verfahrens wurde aber auch die sichere Verarbeitung von Werkstoffen mit geringem Dehnvermögen möglich. Verformungs-Grenzkurven (siehe Forming Limit Curve) des eingesetzten Werkstoffs sind für Machbarkeitsuntersuchungen, FEM-Simulationen und Verfahrensauslegungen unumgänglich.
Eine weitere Machbarkeitsgrenze ist der maximal verfügbare Innendruck und die dadurch mögliche maximale Ausformung des Bauteils (insbesondere in Kofferecken und bei kleinen Radien). Der maximale Innendruck ist wiederum durch die wirtschaftlich realisierbare Anlagentechnik begrenzt.
Vor- und Nachteile
Wesentliche Nachteile des IHU-Verfahrens sind die verhältnismäßig langen Taktzeiten (verglichen zum Beispiel mit konventionellem Tiefziehen) und die hohen Investitionskosten (bei IHU/Rohrumformwerkzeugen).
Als Vorteile stehen dagegen weitgehende Gestaltungsfreiheiten, Einsparung von Einzelteilen (durch Kombination einzelner Bauteile, zum Beispiel bei bisher verwendeter Halbschalenbauweise), dadurch Entfall von Montage- und/oder Schweißoperationen, Kaltverfestigung des Werkstoffs beim Umformprozeß und Gewichtsersparnis als Resultat der vorgenannten Punkte. Auch die hohe Präzision und Wiederholgenauigkeit der Bauteile sprechen für das Verfahren.
Einsatzgebiete
Eingesetzt wird IHU bevorzugt für Rohre mit variablem Durchmesser und zur Herstellung von Kupferfittings, insbesondere T-Stücken. Heute werden vielfach die Aluminiumrohre zur Herstellung von Fahrradrahmen durch Hydroforming an die auftretende Belastung angepasst und in die notwendige geometrische Form gebracht. Auf diese Weise können die verwendeten Wandstärken minimiert werden, um Gewicht (und Kosten) zu sparen.
Im Karosseriebau werden hohle Blechteile hergestellt, indem 2 Bleche zunächst miteinander in bestimmten Nahtformen verschweißt werden und nachfolgend dazwischen Druck aufgebaut wird. Steppnähte, teilweise mit Durchbrüchen, sorgen z. B. für die Einhaltung spezifischer Belastungsanforderungen. Im Fahrwerksbau wird die Teilefertigung teils drastisch vereinfacht[2].
Forschung
Ausgewählte Forschungsrichtungen im Bereich der Innendruckformung sind:
Tailored Hybrid Tubes aus Stahl und Aluminium
Das Ziel war die Entwicklung verbesserter Leichtbauteile für den Automobilbau. Dazu wurde werkstoffseitiger Leichtbau durch Stahl-Aluminium-Mischverbindungen mit konstruktivem Leichtbau durch Rohre kombiniert. Die Rohrstrukturen wurden mittels Laserstrahllöten hergestellt. Zur Fertigung der geschlossenen Hohlprofile kam das IHU-Verfahren zum Einsatz. Auf diese Weise wurden Stahl-Aluminium-Rohre mit umformbarer Fügezone entwickelt.[3]
Titan
Es wurde eine mehrstufige Prozesskette zur Herstellung von IHU-Bauteilen aus Titan entwickelt. Dazu wurde ein geeignetes Werkstoffmodell der Legierung Titan Grade 2 und eine Glühbehandlung ausgelegt. Titan ist aufgrund des geringen maximalen Umformgrads normalerweise nur aufwendig umformbar. Durch die Glühbehandlung konnte der Werkstoff des umgeformten Bauteils in den Zustand vor der Umformung zurückversetzt werden und dadurch weiter umgeformt werden. So konnte ein zweistufiger Umformprozess entwickelt werden und erstmals IHU-Teile aus Titan hergestellt werden.[4]
Literatur
- Handbuch der Umformtechnik. Schuler GmbH, Berlin 1996, ISBN 3-540-61099-5
Einzelnachweise
- Peter Freytag: Verfahrensbilanz. Technische Fortschritte verbessern IHU-Potenzial. In: BLECH inForm. 05/2006, Carl Hanser Verlag, München
- https://www.schulergroup.com/technologien/produkte/grundlagen_innenhochdruckumformung_bauteile_fahrwerk/index.html IHU Fertigung von einem Fahrwerksteil aus einem Rohr
- Forschern gelingt Umformung von Hybridrohren aus Aluminium und Stahl. IPH, abgerufen am 14. Mai 2018.
- Anspruchsvolle Leichtbauteile in einem Schritt herstellen – durch Innenhochdruckumformung von Rohren und Profilen. (PDF) Abgerufen am 14. Mai 2018.