Textilbeton
Textilbeton ist ein künstlicher Verbundwerkstoff, der ähnlich dem Stahlbeton aus den zwei Komponenten Beton und Bewehrung besteht. Er eignet sich sowohl zur Herstellung neuer als auch für die Verstärkung bestehender Bauteile. Als Beton kommen feinkörnige Betone mit einem Größtkorn von <= 2 mm sowie Normalbetone mit einem Größtkorn von <=8 mm zur Anwendung[1]. Wie im Stahlbetonbau auch wird die vergleichsweise geringe Zugfestigkeit des Betons durch zugfeste Bewehrung kompensiert. Bei Textilbeton werden technische Textilien, in der Regel Gelege, benutzt. Als Fasermaterial bewährt haben sich alkaliresistentes Glas (→ Glasfasern) und Carbon. Textilbeton wurde seit Mitte der 1990er Jahre vornehmlich an den Universitäten in Dresden und Aachen entwickelt und im Rahmen zweier Sonderforschungsbereiche der Deutschen Forschungsgemeinschaft (DFG) in seinen Grundlagen erforscht.[2] Der Begriff Textilbeton umfasst mattenartige Bewehrungen aus alkaliresistentes Glas und Carbon oder auch Basalt, jedoch keine stabförmigen Bewehrungen aus diesen Materialien. Im Gegensatz dazu umfasst der Begriff Carbonbeton mattenartige und stabförmige Bewehrungen aus Carbon, jedoch nicht alkaliresistentes Glas und Carbon. Somit ist der Textilbeton weder ein Überbegriff noch eine Untergruppe des Carbonbetons. Beide Bereiche haben vielmehr eine Schnittmenge bei den mattenartigen Bewehrungen aus Carbon.[3]
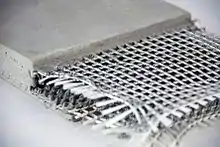
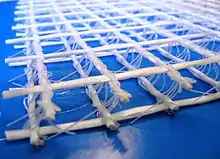
Geschichte
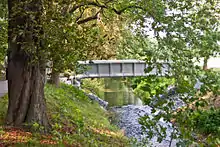
Seit mehreren Jahrzehnten wird nach Alternativen zur korrosionsanfälligen Stahlbewehrung gesucht. Vor allem seit 1999 wurde die Entwicklung dieses neuartigen Werkstoffes in zwei von der Deutschen Forschungsgemeinschaft (DFG) geförderten Sonderforschungsbereichen – SFB 528[4] (Schwerpunkt Verstärkung, Sprecher: Manfred Curbach) in Dresden und SFB 532[5] (Schwerpunkt neue Bauteile, Sprecher: Prof. Josef Hegger) in Aachen – vorangetrieben. Im Dresdner Sonderforschungsbereich lag der Fokus vor allem auf Möglichkeiten der Instandsetzung und Verstärkung von Massivbauwerken mit Textilbeton. An der RWTH Aachen stand der Einsatz von Textilbeton für neue Bauteile im Vordergrund der Forschung. Mit Hilfe von Zulassungen im Einzelfall wurden schon während der Laufzeit der Sonderforschungsbereiche erste Praxisprojekte verwirklicht. Die Umsetzung in die Praxis entlang der gesamten Prozesskette – vom Werkstoff bis zum fertigen Bauteil – wird seit 2014 in Deutschlands größtem Forschungsprojekt im Bauwesen „C³ – Carbon Concrete Composite“ weitergeführt. Das C³-Projekt wird mit 45 Millionen Euro Fördermitteln des Bundesministeriums für Bildung und Forschung (BMBF) im Rahmen der Förderinitiative Zwanzig20 – Partnerschaft für Innovation unterstützt und hat über 160 Mitglieder (Stand April 2019).[6]
Inzwischen gibt es zahlreiche zugelassene Textilbetonprodukte, Praxisprojekte und Interessenverbände, wie den TUDALIT e. V.[7], den Texton e. V.[8] oder auch die Abteilung CC BAU des CC e. V.[9]
Bestandteile und Zusammensetzung
Textilbewehrter Beton besteht aus zwei Komponenten: dem Bewehrungstextil zur Aufnahme der Zugkräfte und einem Beton für die Abtragung von Druckspannungen, die Herstellung des Verbundes und den mechanischen Schutz des Textils.
Textilien aus Hochleistungsendlosfasern wie zum Beispiel aus alkaliresistentem Glas oder Kohlenstofffasern, haben den großen Vorteil, nicht zu rosten. Ein textiles Gelege besteht aus Garnen, die wiederum aus vielen Endlosfasern (Filamenten) zusammengesetzt und auf Textilmaschinen zu gitterartigen Strukturen verarbeitet werden. Variieren können sowohl der Faserwerkstoff als auch Herstellungsart und Geometrie der Textilien. Somit können Textilien maßgeschneidert für verschiedenste Anwendungen bereitgestellt werden.
Der Beton hat in der Regel ein Größtkorn von maximal 8 mm Durchmesser.[10] Gerade bei Bauteilverstärkungen ist man bestrebt, Textilbeton in dünnen Schichten aufzutragen, was nur bei Verwendung einer feinen Körnung (Größtkorn von maximal 2 mm Durchmesser) funktioniert. Sind größere Bauteildicken von über 3 cm erlaubt, haben sich Betone mit größerem Größtkorn (bis 8 mm) bewährt.[11]
Anwendungen
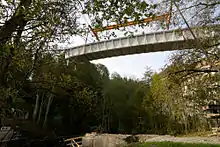
Textilbeton zeichnet sich in erster Linie durch seine Leichtigkeit bei gleichzeitig hoher Tragfähigkeit aus. Außerdem ist er prädestiniert für die Herstellung von frei geformten Schichten und Bauteilen, da das Gelege flexibel ist und der anfangs plastische Beton nach der Erstarrung jede Form konservieren kann.
Die Verstärkung von Betonbauteilen mit Textilbeton erlaubt enorme Tragfähigkeitssteigerungen und ist eine ernsthafte Alternative zu herkömmlichen Methoden wie Spritzbeton oder faserverstärkten Kunststoffen. Außer der Traglasterhöhung sind auch eine Begrenzung der Verformungen und eine Verringerung von Rissbreiten sehr positiv. Ausgeführte Projekte sind z. B. die Ertüchtigung eines Hörsaaldaches an der FH Schweinfurt, eines denkmalgeschützten Tonnendaches und einer denkmalgeschützten Kuppel in Zwickau, von Decken in einem Geschäftshaus oder eines Zuckersilos. Diese Maßnahmen wären ohne Textilbeton nicht realisierbar gewesen.
Auch für neue Bauteile ist Textilbeton gut geeignet. Etabliert hat sich der Baustoff bereits bei leichten Fassadenplatten. Ein weiteres Anwendungsgebiet sind leichte Brücken. Die weltweit erste Brücke aus Textilbeton entstand 2005 für die Landesgartenschau in Oschatz. Sie wurde mit mehreren Preisen ausgezeichnet, darunter dem Special Encouragement Award der fib (fédération internationale du béton). Im Herbst 2007 wurde eine zweite, rund 17 Meter lange Fuß- und Radwegbrücke in Kempten der Öffentlichkeit übergeben, welche im Gegensatz zu der Brücke in Oschatz neben der Fußgängerlast auch ein Räumfahrzeug tragen kann. Dies ist aktuell die weltweit längste Segmentbrücke aus Textilbeton. Die derzeit längste Brücke aus Textilbeton überquert die Bundesstraße 463 in Albstadt-Lautlingen. Diese im November 2010 fertiggestellte Brücke hat eine Länge von 97 Meter bei Einzelstützweiten von bis zu 17 Meter.
Recycling
Ein wichtiger Baustein einer erfolgreichen Markteinführung ist die vollständige Recyclingfähigkeit. Aktuelle Forschungs- und Entwicklungsergebnisse zeigen, dass nach dem Ende der Nutzungszeit die textile Bewehrung und der Beton, mit bereits heute üblicher Technik, wieder getrennt werden können. Ein Reinheitsgrad von 97 % wird erreicht. Anschließend kann der Beton im Betonrecycling und das Carbon im Carbonrecycling – also dort wo auch Sportartikel, Autos, Flugzeuge usw. – recycelt werden. Ansätze zur Verwertung von Recyclingfasern, z. B. zu Kurzfasern, Vliesen oder Langfasern, werden zum Teil bereits im industriellen Maßstab umgesetzt. Auch wenn die textile Bewehrung und der Beton bereits getrennt und recycelt werden können, fehlen im Bauwesen (wie auch in anderen Branchen) weitgehend Produkte, in denen recycelte Carbonfasern genutzt werden. Dies wird ein Schwerpunkt der Forschung der kommenden Jahre sein. Für die frühzeitige und umfangreiche Betrachtung dieser Prozesse und der gesamten Nachhaltigkeit wurden die Entwicklungen um den Carbonbeton bereits mit zahlreichen Auszeichnungen gewürdigt.[12][13]
Preis-Leistungs-Verhältnis
Ein Kilogramm Stahl kostet etwa 1,- Euro, ein Kilogramm Carbon etwa 16,- Euro. Allerdings ist die Tragfähigkeit von Carbon sechsmal höher als die von Stahl. Zudem beträgt die Dichte von Carbon nur ein Viertel von Stahl. Für einen etwa 16-fachen Preis bekommt man also die 24-fache Leistungsfähigkeit (Dichte x Tragfähigkeit). Daher wäre rein rechnerisch Carbon schon heute preiswerter als Stahl. Da die Produktion von Stahlbeton im Vergleich zu der von Carbonbeton inzwischen stark optimiert und automatisiert ist, sind Stahlbetonteile immer noch preiswerter als die oft noch manuelle Herstellung von Carbonbeton. Allerdings macht sich der deutlich reduzierte Materialeinsatz wiederum positiv für Carbonbeton bemerkbar. Fassadenplatten oder Verstärkungsschichten mit Carbonbeton beispielsweise sind nur noch etwa 2 cm dick statt wie bei Stahlbeton etwa 8 cm. Dies bedeutet, dass 75 % weniger Material hergestellt, transportiert, eingebaut sowie verankert werden muss.
Somit ist bei einigen Praxisprojekten schon heute Texilbeton wirtschaftlicher als Stahlbeton und kommt zur Anwendung.
Siehe auch
Literatur
- M. Dupke: Textilbewehrter Beton als Korrosionsschutz. 1. Auflage. Diplomica Verlag, 2010, ISBN 978-3-8366-9405-6.
- M. Curbach u. a.: Sachstandsbericht zum Einsatz von Textilien im Massivbau. In: Deutscher Ausschuss für Stahlbeton. Heft 488, Beuth, Berlin 1998.
- M. Curbach, F. Jesse: Verstärken mit Textilbeton. In: Betonkalender. 99, T. 1, Ernst & Sohn, Berlin 2010, S. 457–565.
- K. Bergmeister, J.-D. Wörner: Betonkalender 2005. Ernst & Sohn, 2004, ISBN 3-433-01670-4.
- W. Brameshuber (Hrsg.): Textile Reinforced Concrete: State-of-the-Art Report of RILEM Technical Committee 201-TRC: Textile Reinforced Concrete. (= Report. 36). RILEM, Bagneux 2006, ISBN 2-912143-99-3.
- M. Curbach, S. Scheerer: Concrete light – Possibilities and Visions. In: V. Šrůma (Hrsg.): Proceedings of the fib Symposium Prague 2011: Concrete Engineering for Excellence and Efficiency, 8.–10. Juni 2011, Keynote Plenary Lectures. DVD-ROM. ISBN 978-80-87158-29-6, S. 29–44.
- M. Curbach, S. Scheerer: Wie die Baustoffe von heute das Bauen von morgen beeinflussen. In: KIT (Hrsg.): Baustoffe und Betonbau – Lehren, Forschen, Prüfen, Anwenden. Festschrift zum 60. Geburtstag von Prof. Dr.-Ing. Harald S. Müller. zusammengestellt von M. Haist und N. Herrmann. Karlsruher Institut für Technologie, Karlsruhe 2010, ISBN 978-3-86644-795-0, S. 25–36.
- M. Curbach, B. Hauptenbuchner, R. Ortlepp, S. Weiland: Textilbewehrter Beton zur Verstärkung eines Hyparschalentragwerks in Schweinfurt. In: Beton- und Stahlbetonbau. 102, 6, 2007, S. 353–361. doi:10.1002/best.200700551
- F. Schladitz, E. Lorenz, F. Jesse, M. Curbach: Verstärkung einer denkmalgeschützten Tonnenschale mit Textilbeton. In: Beton- und Stahlbetonbau. 104, 7, 2009, S. 432–437.
- D. Ehlig, F. Schladitz, M. Frenzel, M. Curbach: Textilbeton-Ausgeführte Projekte im Überblick. In: Beton- und Stahlbetonbau. 107, 11, 2012, S. 777–785.
- M. Horstmann, J. Hegger: Sandwichfassaden aus Textilbeton – experimentelle Untersuchungen. In: Bautechnik. 88, 5, 2011, S. 281–291.
- H. N. Schneider, C. Schätzke, C. Feger, M. Horstmann, D. Pak: Modulare Bausysteme aus Textilbeton-Sandwichelementen. In: M. Curbach, F. Jesse (Hrsg.): Textile reinforced structures: Proceedings of the 4th colloquium on textile reinforced structures (CTRS4), 3.–5. Juni 2009. Dresden, S. 565–576.
- M. Curbach, W. Graf, D. Jesse, J.-U. Sickert, S. Weiland: Segmentbrücke aus textilbewehrtem Beton. In: Beton- und Stahlbetonbau. 102, 6, 2007, S. 342–352.
Weblinks
Einzelnachweise
- M. Lieboldt: Feinbetonmatrix für Textilbeton; Anforderungen – baupraktische Adaption – Eigenschaften. In: Beton- und Stahlbetonbau Spezial 110. Heft S1, 2015, S. 22–28.
- Sonderforschungsbereich 528. Abgerufen am 12. April 2019.
- F. Schladitz, M. Curbach: Carbon Concrete Composite. In: K. Holschemacher (Hrsg.): 12. Tagung Betonbauteile – Neue Herausforderungen im Betonbau. Beuth Verlag, 2017, S. 121–138.
- Sonderforschungsbereich 528. Abgerufen am 12. April 2019.
- DFG – GEPRIS – SFB 528: Textile Bewehrungen zur bautechnischen Verstärkung und Instandsetzung. Abgerufen am 12. April 2019.
- Übersicht der C³-Partner – Carbon Concrete Composite e. V. Abgerufen am 12. April 2019 (deutsch).
- TUDALIT. In: TUDALIT e. V. Abgerufen am 12. April 2019 (deutsch).
- Textilbeton: Netzwerk texton. Abgerufen am 12. April 2019.
- CC Bau | Carbon Composites e. V. – Das Netzwerk. Abgerufen am 12. April 2019.
- M. Lieboldt: Feinbetonmatrix für Textilbeton; Anforderungen – baupraktische Adaption – Eigenschaften. In: Beton- und Stahlbetonbau Spezial 110. Heft S1, 2015, S. 22–28.
- K. Schneider, M. Butler, V. Mechtcherine: Carbon Concrete Composites C³ – Nachhaltige Bindemittel und Betone für die Zukunft. In: Beton- und Stahlbetonbau. Ernst & Sohn Verlag für Architektur und technische Wissenschaften, 2017.
- Jan Kortmann, Florian Kopf: C³-V1.5 Abbruch, Rückbau und Recycling von C³-Bauteilen. Hrsg.: C³ – Carbon Concrete Composite e. V. und TUDALIT e. V. Tagungsband zu den 10. Carbon- und Textilbetontagen, 2018, S. 84–85.
- Jan Kortmann, Florian Kopf, Lars Hillemann, Peter Jehle: Recycling von Carbonbeton – Aufbereitung im großtechnischen Maßstab gelungen! In: Bauingenieur. Jahresausgabe 2018/2019 des VDI-Fachbereichs Bautechnik, ISSN 0005-6650, S. 38–44.