Supervisory Control and Data Acquisition
Mit dem Begriff Supervisory Control and Data Acquisition (SCADA, zu deutsch: Überwachung, Steuerung und Datenerfassung) wird im Bereich der Industrial Control Systems (ICS, zu deutsch Industrielle Steuerungsanlagen) das Computer-System bzw. die Software zur Überwachung und Steuerung technischer Prozesse beschrieben.
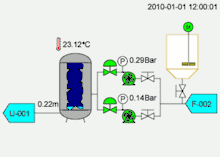
Konzept
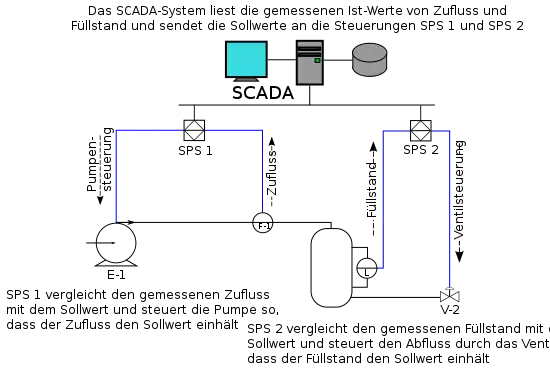
In der Literatur werden zwei grundlegende ICS-Architekturen als Prozessleitsysteme (von englisch Process Control Systems) in Industrieanlagen benannt: Die SCADA-Systeme und DCS (Distributed Control System, zu deutsch: Verteiltes Steuersystem). Als gemeinsames Ziel verbindet sie die Überwachung und Steuerung von Produktions- bzw. Industrieprozessen, aber weder in der Literatur noch in der Praxis herrscht Einigkeit über die Bedeutung und Abgrenzung dieser Begriffe.[2]
Die Architektur von Automationen wird in mehrere Ebenen unterteilt. Dies wird durch die Automatisierungspyramide veranschaulicht. Dabei ist das Level 1 die prozessnahe Schicht mit Sensoren und Aktoren. Die 2. Ebene dient der Steuerung. SCADA-Systeme werden auf der 3. Ebene, der Prozessleitebene zur Überwachung und Kontrolle der Prozesse, verortet.[3] Durch Auswertung der Betriebsdatenerfassung (BDE) bzw. Maschinendatenerfassung (MDE) wird ermittelt, ob Werte einen bestimmten Schwellwert überschreiten. Wenn das passiert schlagen sie Alarm, um den Nutzern die Möglichkeit zu geben durch Inspektion, Wartung bzw. Reparaturen oder Umplanung das Problem zu beheben.[4] Auf der 4. Ebene, der Betriebsleitebene, spielt sich die Planung der Produktion durch Manufacturing Execution Systeme (MES) ab. Das MES dient somit als Schnittstelle zwischen der betriebswirtschaftlich orientierten Unternehmensebene und den operativen Produktionssystemen.[5]
Der Terminus SCADA bezieht sich gewöhnlich auf dezentrale Systeme, die die gesamte Installation überwachen, visualisieren sowie steuern und regeln. Meist sind sie aus einem oder mehreren sogenannten Master Terminal Units (MTU, auch SCADA-Master oder SCADA-Server genannt) aufgebaut.[6] Der größte Teil der Regelung wird automatisch durch Fernbedienungsterminals (Remote Terminal Units, RTU) oder durch Speicherprogrammierbare Steuerungen (SPS) durchgeführt. Die Aufgabe der Level-2-Automation ist es, die Funktion der Level-1-Automation zu optimieren, sowie Stellgrößen und Sollwerte auszugeben. Die Level-3-Automation dient hingegen der Planung, Qualitätssicherung und Dokumentation.
Die Datenerfassung beginnt gewöhnlich mit dem Level 1 und enthält die Koppelung an Messgeräte und Statusinformationen wie Schalterstellungen, die von dem SCADA-System erfasst werden. Die Daten werden dann in einer benutzerfreundlichen Darstellung präsentiert und ermöglichen es, steuernd in den Prozess einzugreifen.
SCADA-Systeme implementieren typischerweise eine verteilte Datenbasis, die Datenpunkte beinhaltet. Ein Datenpunkt enthält einen Ein- oder Ausgangswert, der durch das System überwacht und gesteuert wird. Ein physischer Datenpunkt stellt einen Eingang oder Ausgang dar, während ein berechneter Punkt durch mathematische Operationen aus dem Zustand des Systems hervorgeht. Normalerweise werden Datenpunkte als eine Kombination von Werten mit Zeitstempel behandelt. Eine Serie von Datenpunkten ermöglicht die historische Auswertung.
Kommunikation
Die Kommunikation innerhalb von SCADA-Systemen erfolgt heute mehr und mehr auf der Basis von TCP-basierten Internettechniken. In der Feldebene spielen aber auch noch serielle Verbindungen in Form von Punkt-zu-Punkt-Kommunikationen und Feldbussystemen eine gewichtige Rolle, die wahrscheinlich auf absehbare Zeit erhalten bleiben wird. Die Standardisierung bei der Kommunikation ist noch nicht abgeschlossen. Versuche wie OPC beschränken sich häufig noch auf bestimmte Betriebssysteme. So kommunizieren SCADA-Systeme mit einer SPS oft über den OPC-Standard, welcher auf Microsofts TCP/IP-basiertem Distributed Component Object Model basiert.[7] Mit OPC XML-DA und OPC UA gibt es allerdings auch auf diesem Feld Entwicklungen in Richtung Betriebssystemunabhängigkeit.
Häufig sind im Bereich SCADA noch herstellerspezifische oder geschlossene Lösungen anzutreffen. Aber offene Protokolle wie IEC 60870-5-101/104, DNP3 und Modbus erfreuen sich wachsender Popularität. Über Gateways in Form eingebetteter Systeme lassen sich unterschiedliche Übertragungsprotokolle aneinander anpassen. Die Arbeitsplätze, an denen visualisiert wird, werden heute vermehrt über Ethernet oder drahtlose Netze, d. h. immer mehr auf Basis von TCP angebunden.
Anwendungsbeispiele
Systeme, die nach dem SCADA-Konzept gebaut werden, decken ein großes Spektrum von Anwendungen ab. Die Systeme können je nach Anwendung von nur zehn bis tausend Regelschleifen beinhalten. Zu den Beispielprozessen gehören industrielle, Infrastruktur- und anlagenbasierte Prozesse.
- Infrastrukturprozesse
- Im Energie- und Verkehrssektor gelten sie als Standard. In der Wasserversorgung halten sie mehr und mehr Einzug.[8] Aber auch bei Öl- und Gasleitungen, Stromübertragung und -verteilung sowie Windparks kommen sie zum Einsatz.
- Überwachung industrieller Prozesse
- Fertigung, Prozesssteuerung, Stromerzeugung, Fertigung und Raffination. Hier können sie in kontinuierlichen, Batch-, Wiederholungs- oder diskreten Modi ausgeführt werden.
- Anlagenprozesse in Flugzeugen, Schiffen und Raumstationen
- Sie überwachen und steuern Heizungs-, Lüftungs- und Klimaanlagen.
In Gebäuden werden die entsprechenden Steuerungs- und Überwachungsfunktionen im deutschen Sprachraum in der Regel mit dem Begriff Gebäudeleittechnik beschrieben. In der Verfahrenstechnik spricht man von Prozessleittechnik.
Siehe auch
Weblinks
- Joachim Schairer: Verwundbarkeit und Angriffsmöglichkeiten auf SCADA-Systeme. (PDF; 1,1 MB) (Nicht mehr online verfügbar.) VWEW-Vortrag, Fulda, 17. Oktober 2007, archiviert vom Original am 29. Juni 2016 .
Einzelnachweise
- SCADA Screenshots. In: integraxor.com. Ecava IGX Web SCADA, 18. Mai 2016, abgerufen am 5. August 2019 (englisch, Basic Animations).
- Olof Leps: Hybride Testumgebungen für Kritische Infrastrukturen. Springer Vieweg, Wiesbaden 2018, ISBN 978-3-658-22613-8, Der Aufbau von Betriebs- und Steuerungsanlagen, S. 26, doi:10.1007/978-3-658-22614-5_3 (springer.com [abgerufen am 30. Dezember 2018]).
- Lars Dürkop: Automatische Konfiguration von Echtzeit-Ethernet. Hrsg.: inIT – Institut für industrielle Informationstechnik Hochschule Ostwestfalen-Lippe. Springer, 2017, ISBN 978-3-662-54125-8, S. 9.
- Thomas Bauernhansl, Michael ten Hompel, Birgit Vogel-Heuser (Hrsg.): Industrie 4.0 in Produktion, Automatisierung und Logistik. Springer Vieweg, Wiesbaden: 2014, ISBN 978-3-658-04682-8, S. 405.
- Volker P. Andelfinger, Till Hänisch (Hrsg.): Industrie 4.0 Wie cyber-physische Systeme die Arbeitswelt verändern. Springer Gabler, Wiesbaden: 2017, ISBN 978-3-658-15557-5, S. 59.
- Olof Leps: Hybride Testumgebungen für Kritische Infrastrukturen. Springer Vieweg, Wiesbaden 2018, ISBN 978-3-658-22613-8, Der Aufbau von Betriebs- und Steuerungsanlagen, S. 27.
- Lars Dürkop: Automatische Konfiguration von Echtzeit-Ethernet. Hrsg.: inIT – Institut für industrielle Informationstechnik Hochschule Ostwestfalen-Lippe. Springer, 2017, ISBN 978-3-662-54125-8, S. 10.
- Harald Karutz (Hrsg.): Bevölkerungsschutz Notfallvorsorge und Krisenmanagement in Theorie und Praxis. Springer, 2017, ISBN 978-3-662-44635-5, S. 188.