Rotary-Bohrverfahren
Das Rotary-Bohrverfahren ist ein Verfahren bei geologischen Bohrungen und wird hauptsächlich bei senkrechten oder schwach geneigten Tiefbohrungen nach Erdöl, Erdgas oder bei Geothermiebohrungen eingesetzt. Das wesentliche Merkmal des Rotary-Bohrverfahrens besteht in einem rotierenden Bohrgestänge. Während über lange Zeit des 20. Jahrhunderts mit Drehtischantrieb und einem klassischen pyramidenförmigen Turm (engl. Rig) gearbeitet wurde und viele Arbeiten manuell durchgeführt werden mussten, arbeiten moderne Anlagen häufig mit Masten, das Bohrgestänge wird über einen Kraftdrehkopf angetrieben und die Arbeit ist hochmechanisiert.
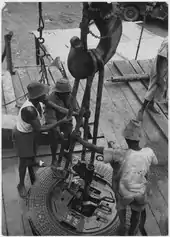
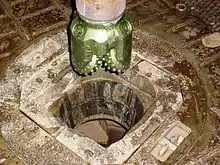
Bestandteile eines klassischen Bohrturms mit Drehtischantrieb
Das Rotary-Bohrverfahren wurde vor allem in den USA entwickelt und perfektioniert, so dass viele englischsprachige Begriffe unübersetzt im Deutschen verwendet werden. Auch in der deutschen Sprache gibt es eigene Fachbegriffe oder Fachbegriffe aus dem Bergbau, die, um die einzelnen Prozesse beim Bohren zu verstehen, erst einmal erklärt werden müssen.
- Wenn die Stangen untereinander oder mit der Zugkappe oder dem Meißel verschraubt werden, muss die Verschraubung mit einem hohen Drehmoment angezogen werden. Dies wird kontern genannt. Beim Auseinanderschrauben muss dieses Drehmoment wieder gelöst werden. Dieses nennt man brechen. Das hohe Drehmoment wird beim klassischen Rotaryverfahren mit den Rotary-Zangen, auch Maschinenzangen genannt, aufgebracht.
- Muss der Bohrmeißel gewechselt werden, so muss das gesamte Gestänge vom Kelly bzw. der Bohrstange (daher der Name Kellybohrverfahren) am Kraftdrehkopf bis hin zum Meißel gezogen und dann wieder eingesetzt werden. Dieser Prozess wird Round Trip genannt. Beim Ziehen des Bohrgestänges wird der Spülkopf gegen den Elevator getauscht, einen Greifer, der den Kopf des Gestänges fasst. Beim hochmechanisierten Verfahren mit Kraftdrehkopf wird der Elevator meistens hydraulisch vor den Drehkopf geschwenkt.
- Der Zug: Beim Round Trip werden bei höheren Bohrtürmen nicht alle Stangen auseinandergeschraubt, sondern sie werden in Verbänden zu mehreren Stangen (je nach der Höhe des Bohrturms beim Double Stand zwei Stangen, beim höheren Triple Stand drei Stangen) in der Fingerbühne abgestellt. Solch einen Verband nennt man einen Zug. Im Single können keine Züge abgestellt werden, bestenfalls die einzelnen Bohrstangen.
- Muss der Bohrstrang um eine weitere Stange ergänzt werden, nennt man dies Nachsetzen.
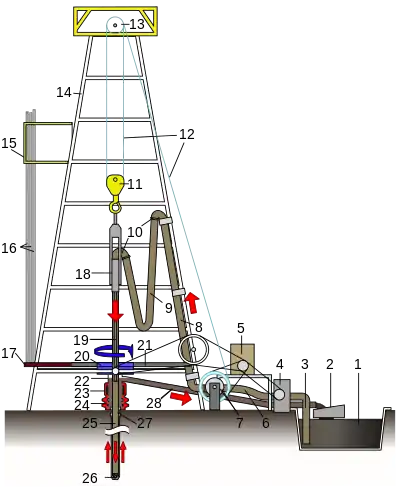
- Tank bzw. Teich für die Bohrspülung
- Rüttelsieb Shale Shakers und Fliehkraftabscheider Desilter und Desander'. Hier wird das Bohrklein, also das ausgebohrte Gestein, von der Bohrspülung getrennt.
- Saugrohr der Spülpumpen
- Spülpumpe
- Bohrturmantrieb (meist Dieselmotoren)
- Das Hochdruckschlauchstück zwischen Spülpumpe und Standrohr wird im Englischen Vibrating Hose genannt, weil es auf Grund der Druckstöße der Pumpe stark schlagen oder vibrieren kann.
- Hebewerk als Hauptzug
- Standrohr
- Schlauch zum Spülkopf, Kelly-Schlauch Kelly Hose
- Goose Neck, Rohrkrümmer für den Spülschlauch, auch Schwanenhals genannt
- Kloben Traveling Block. Der Kloben ist die Unterflasche des Flaschenzugs des Hebewerks.
- Seil des Hebewerks Drilling Line
- Turmrollenlager Crown Block. Das Turmrollenlager ist die Oberflasche des Flaschenzugs des Hebewerks.
- Bohrturm selbst Derrick
- Affenbühne, Gestängebühne oder Aushängebühne Monkey Board: Hier werden durch den Bühnenmann beim Round Trip die Züge aus dem Elevator gelöst und in die Fingerbühne gestellt, die sich direkt an die Affenbühne anschließt.
- Züge des Bohrgestänges Stand (of drillpipes)
- Boden des Lagers für die Züge, meist aus Holz, damit die Gewinde der Züge nicht beschädigt werden.
- Spülkopf
- Kelly, die Mitnehmerstange. Das Kelly ist ein prismatisches Rohr mit quadratischer, hexagonaler oder oktogonaler Grundfläche. Oben und unten an dem Kelly befinden sich die für das Bohrgestänge üblichen Kegelgewinde.
- Drehtisch. Der Dreh- oder Bohrtisch ist vereinfacht eine horizontale kreisförmige Platte mit einer zentralen Bohrung, die sich in den Anfangszeiten auf der Arbeitsbühne befand, in moderneren Anlagen in die Arbeitsbühne eingelassen ist und durch die das Bohrgestänge eingefahren wird. Der Drehtisch wird von einem großen Kugellager geführt und wird durch den Bohrturmantrieb in Drehung versetzt. Er besitzt Bohrungen für die Zapfen des Mitnehmers, der dann das Kelly dreht.
- Arbeitsbühne oder Tisch
- Spülungsauslauf Bell Nipple
- und 24. Bohrlochkontrollvorrichtung Blow-Out-Preventer (BOP)
- 25. Bohrgestänge
- 26. Bohrmeißel
- 27. Kopf der Verrohrung
- 28. Bohrspülungrückleitung
Hier nicht abgebildet befindet sich neben dem Drehtisch leicht schräg in den Untergrund führend ein Rohr, in dem die nächste Bohrstange zum Verlängern des Gestänges vorgehalten wird, das Mousehole. Manche Bohrtürme besitzen ein zweites Abstellrohr, in das die Kelly gestellt werden kann, das dann als Rathole bezeichnet wird.
Der Bohrturm besitzt weitere wichtige Betriebsmittel, die nicht abgebildet sind:
- Neben dem Hebewerk besitzt der Turm zusätzliche Kettenzüge oder Seilzüge als Hilfswinden, die sogenannten Luftwinden. Mit einem horizontalen Seilzug oder Spill auf der Affenbühne werden die Schwerstangen durch zwei Bühnenmänner in die Fingerbühne geholt. Die Zangen und andere schwere Werkzeuge hängen an eigenen Luftwinden. Die einzelnen Bohrstangen werden mit einer Luftwinde vom horizontalen Stangenlager vom Catwalk über die Rampe (Pipe Ramp) durch die Tür gezogen und ins Mouse Hole gestellt.
- Auf dem Tisch stehen die Absetzkeile (Slips), mit dem das Bohrgestänge abgefangen wird, damit es nicht ins Bohrloch zurückfällt, wenn es aus dem Bohrloch gezogen wird. Beim Nachsetzen einer Bohrstange benutzt man die Handkeile, beim Round Trip gibt es auch Automatikkeile, die während des Trips im Loch des Drehtisches verbleiben und so nicht immer wieder hochgehoben werden müssen.
- Mit den Rotary-Zangen werden die Stangen nach dem Verschrauben fest angezogen (gekontert) und wieder voneinander gelöst (gebrochen). Wurden ursprünglich die Rohre noch mit der Spinkette verschraubt und dann mit den Zangen gekontert, so gab es später bei diesem Verfahren mechanische Hilfsmittel zum Drehen der Rohre, die Spinner wie z. B. den Spinnerhawk und für die Kelly-Stange den Kellyspinner, und das nicht ganz ungefährliche Arbeiten mit der Spinkette wurde auf Ausnahmefälle begrenzt. Wurden die Zangen zu Anfang noch mit Muskelkraft betätigt, so brachte man später die Kraft zum Kontern oder Brechen mit Spills und heute mit meist hydraulisch angetriebenen Seil- oder Kettenzügen auf, die Katzenköpfe (Catheads) genannt werden. Mit der fortschreitenden Mechanisierung der Arbeit wurden zuerst die hydraulischen Zangen eingeführt. Schließlich wurden Spinner und Zangen zum Iron Roughneck auch Hydraulic Roughneck genannt, einer hydraulischen Brech-/Kontervorrichtung vereinigt.
Prozesse und technische Entwicklungen
Je größer die Teufe (Tiefe) ist, in die eine Bohrung vorgetrieben werden soll, desto größer ist der technische Aufwand. Grob kann gesagt werden, dass mit steigender Teufe mit einem größeren Bohrlochdurchmesser begonnen werden muss. So wird verständlich, dass sich die Bohrstangen bei den ersten Rotary-Bohrungen ab 1901 noch von Hand mit der Kettenrohrzange Kontern und Brechen ließen, heute zum Kontern und Brechen jedoch kraftbetriebene Arbeitsmittel wie schwere Zangen, die über Katzenköpfe betätigt werden, hydraulische Rohrzangen oder Iron Roughnecks verwendet werden müssen.
Die Länge einer normalen Bohrstange beträgt ca. 9 m. Wenn nach Verschleiß des Meißels das komplette Bohrgestänge gezogen werden muss, so bedeutet dies, dass bei einer nur mitteltiefen Bohrung von ca. 2000 m Teufe schon 222 Stangen gezogen, gebrochen, auseinandergeschraubt, abgestellt, zusammengeschraubt und gekontert werden müssen. Die Arbeit der Roughnecks genannten Arbeiter auf der Arbeitsbühne und des Derrick Man genannten Arbeiters auf der Affenbühne ist aus Sicht der Arbeitssicherheit nicht ungefährlich, es sind schwere Teile zu bewegen, man arbeitet in der Nähe ungeschützter und sich mit hohen Kräften und Energien bewegender Teile, teilweise in schwindelnder Höhe, und auch gerade bei Bohrarbeiten gilt: Zeit ist Geld. Dazu kommt noch, dass eine Tiefbohrung teilweise hoch brennbare Gase und Flüssigkeiten ausbrechen können. Der technische Fortschritt bezog sich deshalb beim Rotary-Verfahren vor allem auf die Bemühungen, die Arbeit schneller und sicherer zu machen und mit möglichst wenig Personal auszukommen. Unabhängig von den Eigenschaften des zu durchbohrenden Gebirges bestimmt die Zeit, die zum Verschrauben und Kontern bzw. zum Brechen und Auseinanderschrauben des Gestänges benötigt wird sowie die Geschwindigkeit des Hebewerks die Tripgeschwindigkeit (ungefähr entsprechend den englischen Begriffen Trip Speed oder Tripping Speed) und ist ein wichtiger Kostenfaktor einer Tiefbohrung. Wenn für das Ziehen oder Nachsetzen einer Stange oder eines Strangs eine Zeit von 2 Minuten angegeben wird, lassen sich in einer Stunde 30 Stränge nachsetzen. Im englischen Sprachraum würde eine Tripping Speed von 30 Stands per hour angegeben (30 Züge pro Stunde). Deutsche Hersteller geben die Tripgeschwindigkeit in Metern pro Stunde an. Hier wird also auch die Länge des Zugs einbezogen. Dieses Leistungsmaß eines Bohrturms zeigt, dass seine Leistungsfähigkeit unter anderem von seiner Höhe abhängt, denn je höher ein Bohrturm ist, desto länger sind die Züge, die abgestellt werden können. Bohrtürme werden unter anderem nach der Länge ihrer Züge typisiert:
- Single entspricht einem Rohr, dieses entspricht 30 Fuß oder 9 m
- Double entspricht zwei Rohren, dieses entspricht 60 Fuß oder 18 m
- Triple entspricht drei Rohren, dieses entspricht 90 Fuß oder 27 m
Vereinzelt wurde auch von Anlagen mit Zügen von vier Rohrlängen berichtet.
Ein Single besäße bei einer Tripping Speed von 30 Zügen Pro Stunde eine Tripgeschwindigkeit von 270 m/h. Ein Double besitzt bei derselben Trippig Speed schon eine Tripgeschwindigkeit von 540 m/h und ein Triple erreicht gar 810 m/h. Zum Vergleich die Leistung einer modernen Anlage: Streicher gibt die Leistung seiner VDD 370 mit Single-Mast mit einer Tripgeschwindigkeit bis 400 m/h an. Dies mag einem relativ langsam vorkommen, kann eine Mannschaft von gut trainierten Roughnecks einen Zug in einem Triple doch in knapp 2 Minuten ausbauen, es ist jedoch zu berücksichtigen, das moderne hochmechanisierte Anlagen mit erheblich weniger Personal auskommen.
Bohren
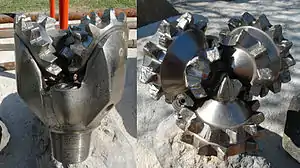
Während anfänglich nur so genannte Fischschwanzmeißel eingesetzt wurden, die eine sehr hohe Torsionsbeanspruchung des Bohrgestänges (dem verschraubten Rohrstrang) verursachten, werden heute Rollen- oder Kronenmeißel verwendet. Rollenmeißel besitzen üblicherweise drei gegeneinander winkelig angeordnete, gezähnte Kegelrollen. Wenn der Bohrmeißel in Drehung versetzt wird, rollen die Kegelrollen auf der Bohrlochsohle ab und zerkleinern dabei das zu durchbohrende Gestein. Für hartes Gestein gibt es Rollenmeißel, deren Zähne mit Hartmetallstiften besetzt sind. Ebenso finden besonders bei hartem Gestein PDC-Meißel (ohne bewegliche Teile) mit einem Besatz aus künstlichen Diamanten, Schneidkeramiken oder Hartmetall Verwendung.
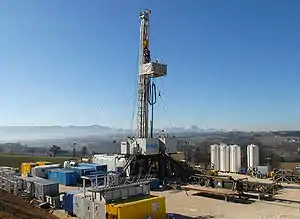
Das zerkleinerte Gestein wird über eine durch das Bohrgestänge zugeführte und am Meißel austretende Spülflüssigkeit kontinuierlich entfernt und gelangt im Ringraum zwischen Bohrloch und Bohrgestänge an die Erdoberfläche. Die Bohrspülung besteht zumeist aus Wasser und Tonmehl mit einem Zusatz aus Barytmehl, das auf Grund seiner hohen Dichte den Schweredruck in der Flüssigkeit so weit erhöht, dass damit das noch nicht verrohrte Bohrloch stabilisiert und das durch den Bohrmeißel zerkleinerte Gestein an die Erdoberfläche transportiert werden kann. Überdies ermöglicht die Spülflüssigkeit in Zusammenhang mit leistungsfähigen Spülpumpen, die Bohrleistung deutlich zu erhöhen, indem die Flüssigkeit mit Geschwindigkeiten von über 100 Meter pro Sekunde aus Düsen im Bohrmeißel austritt und somit zum Gesteinsabtrag wesentlich beiträgt. Die Tonspülung hat darüber hinaus die Eigenschaft, dass ihre Viskosität in Abhängigkeit von der Strömungsgeschwindigkeit variiert (Thixotropie). Sollten die Spülpumpen ausfallen, kommt die Spülung zum Stillstand und geht nach einer gewissen Zeit in einer gelartigen Zustand über. Dadurch wird ein Absinken des im Ringraum befindlichen Bohrkleins in Richtung Bohrlochsohle und damit ein Festwerden des Meißels verhindert.
Die nach oben gelangte Spülflüssigkeit wird mittels Rüttelsieben (Shale Shaker) und Fliehkraftabscheider (Desander und Desilter) vom mitgebrachten Gesteinsmaterial gereinigt und kann so – nach Ergänzung der Beimengungsverluste – immer wieder verwendet werden.
Beim Rotaryverfahren wird der Bohrmeißel durch das Bohrgestänge in Drehung versetzt.
Bei sehr tiefen oder gerichteten Bohrungen kommt zumeist nicht das Rotary-Bohrverfahren, sondern eine Bohrturbine (bzw. ein Untertagebohrmotor) zum Einsatz, die direkt über dem Bohrmeißel sitzt. Das Bohrgestänge dreht sich in diesem Fall nicht, sondern dient nur mehr dem Meißelvorschub und der Zufuhr der Spülflüssigkeit, die auch die Turbine antreibt.
Beim klassischen Rotary-Bohrverfahren erfolgte die Drehung des Bohrstranges üblicherweise mittels eines so genannten Drehtisches auf der Arbeitsbühne der Bohranlage. Den oberen Abschluss des Bohrgestänges bildet dabei eine quadratische, sechs- oder achteckige Mitnehmerstange (Kelly), welche über den mit dem Drehtisch mittels Zapfen gekoppelten Mitnehmer die Drehbewegung vom Drehtisch auf das Gestänge überträgt und an der auch die Zuführung der Spülflüssigkeit erfolgt.
Heutige Bohranlagen verfügen zumeist über einen Kraftdrehkopf (engl. Top Drive), womit die Mitnehmerstange entfällt und so die stetig notwendige Verlängerung des Bohrstranges, das Nachsetzen vereinfacht wird.
Nachsetzen
Das Bohrgestänge besteht wie schon erwähnt üblicherweise aus Teilstücken zu je 30 Fuß (wegen der Herkunft der Bohrtechnologie aus den USA; ca. 9 m). Nach jeweils 9 m Bohrfortschritt wird zunächst mittels des Hebewerks, eines Flaschenzugs, zu dessen Zweck der Bohrturm besteht, der gesamte Bohrstrang so weit angehoben, dass die gesamte Mitnehmerstange und reichlich 1 m der obersten Bohrstange aus dem Bohrloch ragt. Dann wird unterhalb der Flanschstelle zur Mitnehmerstange der Bohrstrang mittels Handkeilen am Drehtisch gegen Absturz gesichert und die Mitnehmerstange gebrochen und abgeschraubt. Die Mitnehmerstange wird in der Folge mit einem Gestängeelement, das neben dem Drehtisch im Mousehole bereitsteht, verschraubt und gekontert. Anschließend werden die Mitnehmerstange mit dem neuen Gestängeelement wieder auf das Bohrgestänge aufgesetzt verschraubt und gekontert, das Gestänge wird angehoben, bis die Handkeile frei sind, dann werden die Keile entfernt, und der gesamte Rohrstrang wieder soweit abgesenkt, bis der Meißel mit dem notwendigen Druck die Sohle erreicht. Es können weitere 9 m gebohrt werden. Der beschriebene Wechselvorgang dauert 1,5 bis 4 Minuten.
Das Brechen oder Kontern des Bohrgestänges mit dem Drehtisch ist zu gefährlich und deshalb verboten. Zum Abschrauben nach dem Brechen wird meistens der Drehtisch verwendet, das untere Rohr wird gedreht. Zum Aufschrauben des neuen Rohres muss das obere Rohr gedreht werden. Das geschah früher bei kleinen Rohrdurchmessern teilweise von Hand, später mit der Spinkette, wobei bei ungeschickter Handhabung leicht Finger, Hand oder Arm gegen das Rohr gequetscht oder gewickelt werden konnten. Deshalb ist dies auch nur noch in Ausnahmefällen erlaubt. Die Schwerstangen wurden teilweise zeitaufwändig mit der Kettenrohrzange angedreht. Mit der Zeit kamen angetriebene Vorrichtungen auf, mit denen das obere Gestänge gedreht werden konnte, die sogenannten Spinner wie der Kellyspinner und der Spinnerhawk. Moderne Anlagen besitzen den weiter oben beschriebenen Iron Roughneck mit Zangen und Spinner, der nur noch an das zu verschraubende Gestänge herangeführt werden muss und dann die Zangenarbeit über Bedienhebel gesteuert ausführt.
Round Trip
Zum Wechseln eines verschlissenen oder defekten Bohrmeißels muss das gesamte Gestänge aus dem bereits gebohrten Bohrloch herausgezogen werden. Dies erfolgt üblicherweise in Zügen zu 2 bis 4 Gestängeelementen, das heißt, es bleiben je nach Höhe des Bohrturmes 2 bis 4 Gestängeelemente verschraubt. Das komplette Ziehen und Wiedereinsetzen des Bohrgestänges wird als Round Trip bezeichnet. In der heute kaum noch verwendeten deutschen Bohrsprache nannte man diesen Vorgang des Aufholens, Meißelwechsels und Einlassens den Meißelmarsch.
Geschichte
Schon 1844 meldete der Brite Robert Beart ein Patent für ein Bohrverfahren an, das weitgehend der modernen Rotary-Tiefbohrtechnik entspricht. Dabei wird das mittels eines sich drehenden Meißels schabend zerkleinerte Gestein durch eine Spülflüssigkeit, die durch das Bohrgestänge nach unten gepumpt wird und am Meißel austritt, kontinuierlich abgeführt. Die hohen technischen Ansprüche (Übertragung einer großen Kraft auf ein verschiebbares Bohrgestänge, kontinuierliche Zuführung der Spülflüssigkeit in ein sich ständig drehendes Rohr, Notwendigkeit der Regulierung der auf den Bohrmeißel wirkenden Last) verhinderten lange Zeit eine Umsetzung des Konzeptes. Auch nach Lösung der meisten Probleme galt das Rotary-Verfahren bis in die Zeit nach dem Ersten Weltkrieg als zu störanfällig und damit dem Schlagbohrverfahren unterlegen.
Der erste berühmt gewordene Einsatzfall des Rotary-Verfahrens war die Bohrung am Spindletop-Hügel bei Beaumont (Texas), die am 10. Januar 1901 in 347 m Tiefe auf unter hohem Druck stehendes Erdöl stieß. Es erfolgte ein gewaltiger Ausbruch, in dessen Folge täglich etwa 100.000 Barrel Rohöl unkontrolliert aus dem Bohrloch ausgestoßen und aus dem sich gebildeten Ölsee abgeschöpft wurden. Plötzlich hatte sich die Ölproduktion der USA verdreifacht.
Das allgemein als Spindletop-Gusher oder Lucas-Gusher (nach dem die Bohrung durchführenden Geologen Anthony Lucas – gebürtig als Antonio Luchich – benannt) bekannte Ereignis ließ in Texas einen Erdölboom mit nachhaltigen Auswirkungen auf die Volkswirtschaft der USA ausbrechen.
Literatur
- G. Robello Samuel: Introduction to rotary drilling. (Drilling technology series; Segment 1) Petroleum Extension Service, Division of Continuing and Innovative Education, The University of Texas at Austin, Austin, TX, 2014, ISBN 978-0-88698-259-1.
- Heinrich-Otto Buja: Handbuch der Tief-, Flach-, Geothermie- und Horizontalbohrtechnik: Bohrtechnik in Grundlagen und Anwendung. Vieweg+Teubner, Wiesbaden 2011, ISBN 978-3-8348-1278-0, insbes. S. 367–372, 394–407.
- Ödön Alliquander: Das moderne Rotarybohren. 2., vollkommen überarb. und erw. Aufl., Dt. Verl. für Grundstoffindustrie, Leipzig 1968.
- Springer, F. P.: Zur Geschichte der Tiefbohrtechnik aus der Perspektive von Lehr- und Fachbüchern, Erdoel-Erdgas-Kohle (ISSN 0179-3187) Bd. 125, H. 7/8 (2009), S. 308–314.