Keilzinkung
Als Keilzinkung oder Keilzinkenverbindung wird eine Methode der Längsverbindung zweier Bauteile aus Vollholz oder Holzwerkstoff bezeichnet.
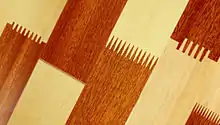
Zweck
Diese Art der Holzverbindung wird eingesetzt, um sehr lange Holzbauteile herzustellen oder unschöne Äste und festigkeitsmindernde Risse herauszutrennen. Mit Keilzinkenverbindungen ist es möglich, kurze Holzstücke zu einem theoretisch endlosen Holzstrang zu verbinden. Neben der Verlängerung von Werkstücken wird die Keilzinkung auch verwendet, um Bauteile unter beliebigem Winkel auf Gehrung zusammenzufügen.[1][2]
Es handelt sich um eine in Längsrichtung angewendete Zinkung und um eine Weiterentwicklung der seit der Vorgeschichte angewendeten Schäftung. Die Keilzinkenverbindung wird in der Regel zusätzlich geklebt. Ihre Zugfestigkeit beruht auf der Vervielfachung der Fläche der zur Faserrichtung des Holzes flach geneigten Klebefuge.[3] Sie hat infolge des stetigen Übergangs zwischen den beiden verbundenen Teilen auch eine relativ hohe Biegefestigkeit. Hinsichtlich dieser Eigenschaften ist sie Stahl-Holz-Verbindungen sowie anderen Holz-Holz-Verbindungen überlegen. Keilgezinkte Bauteile können unter optimalen Randbedingungen in der Produktion und Qualitätssicherung nahezu die Tragfähigkeit der am Stück gewachsenen Bauteile erreichen.[4]
In der zusätzlich verklebten und mit Längskräften zusammengefügten Verbindung entstehen Stoff-, Kraft- und Formschluss.[5] Die Keilzinken stecken in Querrichtung formschlüssig ineinander. Kraftschluss entsteht zwischen den Keilflächen der Zinken, da letztere beim Zusammenfügen elastisch „verdünnt“ werden. Die elastischen Reaktionskräfte sind bei genügend kleinem Flankenwinkel der Zinken groß genug, um Selbsthemmung gegen Herausrutschen auseinander zu bewirken. Der Klebstoff auf den Zinkenflanken stellt einen Stoffschluss zwischen ihnen her. Dieser Stoffschluss ist im Allgemeinen aber wirksamer als der selbsthemmende Kraftschluss. Somit ist die Keilzinkenverbindung bei Zug in Längsrichtung eine primär durch Kleben stoffschlüssig hergestellte Verbindung. Sie ist überlagert durch Formschluss der Klebeschicht mit der faserig-porösen Oberfläche fast aller Holzarten. Ebenfalls nachgewiesen ist das Wirken zwischenmolekularer Kräfte.[6]
Definition
In der Normenliteratur ist die Keilzinkenverbindung definiert als „Längsverbindung zweier Vollhölzer, z. B. Bretter, Bohlen, Kanthölzer, deren Enden mit keilförmigen Zinken gleicher Teilung und gleichen Profils ineinandergreifen und miteinander verklebt sind.“[7] Es existieren weitere, produktspezifische Begriffsdefinitionen mit ähnlichem, aber leicht abweichendem Wortlaut.[8][1] Diese Normdefinition ist für tragende Bauteile aus Bauholz verbindlich. In einigen nichttragenden Anwendungen wie etwa im Möbelbau existieren hiervon abweichende, nicht normkonforme Keilzinkenverbindungen.
Geschichte
Grundlegende Erkenntnisse für die Entwicklung der Keilzinkenverbindung lieferten die Baustoffwissenschaftler Otto Graf und Karl Egner. Die systematische Untersuchung an geleimten Laschenverbindungen begann Graf 1933.[9] In einem zusammen von Graf und Egner 1938 veröffentlichten Aufsatz wurden konstruktive Vorschläge zur Verbesserung von geklebten Laschenverbindungen vorgestellt. Durch abgeschrägte Laschen und entsprechend zugespitzte Hölzer wurde gegenüber der bisher üblichen Ausführungsart eine bedeutende Steigerung der Tragfähigkeit erreicht. Im Zugversuch ertrug die neuartige Laschenverbindung um durchschnittlich 75 % höhere Bruchlasten gegenüber der Verbindung mit geraden Laschen.[10] Diese Versuchsreihe markiert den Beginn der Keilzinkenverbindung.[11] Zunächst wurde für die neue Laschenverbindung der Begriff Schiftzinkung[Anm. 1] verwendet.
In den Jahren 1937 bis 1942 erforschte Egner die Schiftzinkung weiter zur Keilzinkung.[12] Er setzte sich mit der Zinkengeometrie hinsichtlich Tragfähigkeit und maschineller Herstellung auseinander und wirkte bei der Entwicklung entsprechender Bearbeitungsmaschinen und Werkzeuge mit.[13][14] Damit waren die Voraussetzungen für eine breite Anwendung im Holzbau geschaffen: Zum einen durch die Möglichkeit der maschinellen und damit reproduzierbaren und ökonomischen Herstellung der Keilzinken, zum anderen eignete sich diese neue Verbindung durch die hohe Festigkeit für vielfältige Einsatzmöglichkeiten, auch in tragenden Konstruktionen.
Die von Egner entwickelte Geometrie und seine grundlegenden Erkenntnisse fanden 1958[Anm. 2] mit der DIN 68140 Eingang in die Normung.[15] In dieser Norm sind die Anforderungen an Keilzinkenverbindungen für tragende Holzbauteile geregelt. In den 1960er Jahren wurde die Keilzinkenverbindung Gegenstand zahlreicher Forschungsarbeiten, unter anderem in den Bereichen Klebstoffe, Anwendungsgebiete, Zinkengeometrien und Werkzeugtechnik.[16] Hinsichtlich der Geometrie ging der Trend zu kürzeren Zinkenlängen, um die Holzausbeute zu erhöhen. So betrug die 1944 von Egner vorgeschlagene Zinkenlänge noch 40 Millimeter.[17] Untersuchungen unter Leitung von Joseph-Eric Marian führten in der zweiten Hälfte der 60er Jahre zur Entwicklung der Minizinken mit 7,5 Millimeter Zinkenlänge und etwa 1970 zur Entwicklung der Mikrozinken mit 4 Millimetern Zinkenlänge.[12][18] Gegenwärtig werden allgemein kürzere Zinkenlängen bevorzugt. In der industriellen Produktion sind Zinkenlängen von 4 oder 10 Millimetern Länge für nicht tragende Bauteile verbreitet. Bei tragenden Bauteilen sind Zinkenlängen von 10, 15 oder 20 Millimetern die Regel.[12]
Herstellung
Zur Herstellung sind im Wesentlichen drei Verfahrensschritte nötig: Das Herstellen der Zinkengeometrie, das Auftragen des Klebstoffes auf die Zinken und das anschließende Verpressen der mit Klebstoff benetzten Flächen. Keilzinkenprofile werden fast ausschließlich durch Fräsen hergestellt, selten durch Sägen (zum Beispiel bei Trigonit-Trägern).[19] Im handwerklichen Bereich werden die Zinken auf Tischfräsmaschinen oder Oberfräsen gefertigt, die industrielle Herstellung erfolgt auf speziellen Keilzinkenfräsmaschinen.[20] Mittels Zinkenfräswerkzeug wird die Zinkenkontur durch Spanabnahme im Holz abgebildet. Abhängig vom Maschinenkonzept geschieht die Vorschubbewegung durch das Werkstück oder das Werkzeug. Einfluss auf das Arbeitsergebnis haben vor allem der Zahnvorschub, der Werkzeugzustand, die Holzart und die Beschaffenheit des Werkstücks. Der Klebstoffauftrag geschieht zeitnah nach der Zinkenfräsung. Im Allgemeinen wird der Klebstoff automatisch aufgetragen, ein händischer Auftrag ist nur in der handwerklichen Produktion üblich. Das automatisierte Auftragen des Klebstoffs geschieht am häufigsten durch Gegenprofilwalzen oder Kämme unmittelbar nach dem Fräsen, bei einigen Anlagen durch Bürsten oder kontaktlos durch Aufsprühen. Der Klebstoffauftrag erfolgt in der Regel aus Sicherheitsgründen beidseitig.[21] Seit 2008 ist auch ein Verfahren für den einseitigen Klebstoffauftrag im tragenden Holzbau zugelassen, bei dem der Klebstoffauftrag hinsichtlich Menge und Verteilung des Klebstoffs kontinuierlich überwacht wird.[21][22] Das Aufbringen eines Längspressdrucks zur Herstellung der Klebeverbindung ist entscheidend für die spätere Festigkeit der Verbindung. Einfluss auf die Güte der Klebung haben die Pressdauer und der Pressdruck in der Klebefuge.
Verfahren mit durch Umformen eingepressten Keilzinkenprofilen haben sich bis heute nicht durchgesetzt.[12]
Verwendete Holzarten
Prinzipiell lässt sich jede Holzart mit dem Keilzinkenverfahren verarbeiten. Die tatsächliche Verwendung der verschiedenen Holzarten als Bau- und Werkstoff wird stark durch deren Material-, Verarbeitungs- und Gebrauchseigenschaften bestimmt. Zu den signifikanten Verarbeitungseigenschaften zählen die Zerspanbarkeit und Verklebungsfähigkeit. Zu den Materialeigenschaften zählen unter anderem die Rohdichte, Elastizitätsmodul, Härte, Zug-, Druck-, Biege- und Torsionsfestigkeit sowie die Spaltfestigkeit und Wärmeleitfähigkeit. Quell- und Schwindverhalten, Dauerhaftigkeit, Astigkeit, Farbe, Faserverlauf, Glanz und Geruch zählen zu den Gebrauchseigenschaften.
Die regionale Verbreitung und Verfügbarkeit einer Holzart spielt ebenso eine Rolle wie die Präferenz des Anwenders und Verbrauchers.
Tragende Bauteile
Nadelhölzer sind momentan die vorwiegend eingesetzten Hölzer im Baubereich.[23] Dies hängt unter anderem mit den Anforderungen der aktuellen Normen zusammen. Für etwaige Produkte aus Laubholz existieren keine Angaben zu herstellungsrelevanten Eigenschaften wie Festigkeit oder Verklebung.[24] Im konstruktiven Holzbau dürfen für tragende Bauteile nur zugelassene Holzarten verarbeitet werden. In Deutschland sind dies Fichte, Tanne, Kiefer, Douglasie, Laricio-Kiefer und Schwarzkiefer, Lärche, Strandkiefer sowie Pappel, Radiata-Kiefer, Sitkakiefer, Hemlocktanne und kanadische Rotzeder.[25] Somit ist neben zwölf Nadelhölzern lediglich die Pappel als einziges Laubholz zugelassen. In der Schweiz ist Laubholz als Bauholz für tragende Zwecke zwar grundsätzlich zugelassen, jedoch schränken fehlende Festigkeitsklassifizierung sowie Hinweise zur Klebfestigkeit deren Einsatzfähigkeit ein.[26] Die wirtschaftlich bedeutendste einheimische Holzart für den konstruktiven Holzbau ist Fichte, gefolgt von Tanne.[27] Üblich für Brettschichtholz ist Fichte, seltener kommen Tanne, Kiefer, Lärche und Douglasie zur Anwendung.[28]
Im Jahr 2005 machten Laubhölzer in Deutschland, Österreich und der Schweiz einen Anteil von 1 Prozent des Produktionsvolumens bei stabförmigen Vollholzwerkstoffen wie Brettschichtholz, Kreuzbalken, Duo- und Triobalken aus. Die meistverarbeitete Holzart war Eiche, gefolgt von Buche und Esche.[29] Um auch Laubhölzer für tragende Zwecke zu etablieren, sind etliche Forschungsvorhaben forciert worden. Speziell Buche als in Deutschland am häufigsten eingeschlagene Laubholzart[30] ist hinsichtlich ihrer Eignung zur Herstellung von Brettschichtholz intensiv untersucht worden.[31][32][33][34] Im Oktober 2009 erteilte das Deutsche Institut für Bautechnik (DIBt) die bauaufsichtliche Zulassung für Brettschichtholz und Hybridträger aus Buche.[35] Auch Bauwerke mit Brettschichtholz aus Esche und Eiche sind bereits realisiert worden.[36]
Nichttragende Bauteile
Leimholzplatten für den Innenbereich als Halbzeug für Tische, Küchenplatten, Treppenstufen und Möbelkörper sind häufig aus Hartlaubhölzern wie Buche, Eiche, Birke, Erle, Kirsch- oder Nussbaum, Esche, Ahorn, Robinie und Hainbuche. Buchenholzleimplatten kommen zudem für Arbeitsplatten und Werkbänke zum Einsatz. Aber auch Nadelhölzer wie Fichte und Kiefer werden zu Leimholzplatten verarbeitet.[37][38]
Verwendete Klebstoffe
Für die Verklebung tragender Bauteile dürfen nur Klebstoffe verwendet werden, welche die Prüfung nach der DIN EN 301 oder DIN EN 302 Teil 1 bis 4 bestanden haben oder im Rahmen einer Zulassung durch das Deutsche Institut für Bautechnik geregelt sind. Hinsichtlich der Gebrauchseigenschaften ist noch eine Prüfung nach DIN 68141 erforderlich.[39] Eine regelmäßig aktualisierte Liste der zugelassenen Klebstoffe steht öffentlich zur Verfügung.[40]
Zinkengeometrie
![]() |
a, b | Fügeteile |
c | Klebefläche an den Zinkenflächen | |
b | Breite Zinkengrund | |
bs | Breite Zinkenspitze | |
g | Zinkengrund | |
lsp | Zinkenspiel | |
lz | Zinkenlänge | |
p | Zinkenteilung | |
s | Zinkenspitze | |
x | Symmetrieachse des Zinkens | |
α | Flankenneigungswinkel |
Die wesentlichen Eigenschaften der Keilzinkenverbindung werden durch die Zinkenlänge lz, den Flankenneigungswinkel α, die Breite des Zinkengrundes b und die Zinkenteilung p bestimmt. Des Weiteren wird die Verbindung durch den Verschwächungsgrad
sowie das relative Zinkenspiel
näher beschrieben.[7] Der Verschwächungsgrad beschreibt den relativen Anteil der Breite der Zinkenspitze in Bezug auf die Zinkenteilung. Da der Bereich der Zinkenspitze keinen Anteil an der Festigkeit der Klebung hat, wirkt er schwächend auf die Verbindung.
Wesentlich für die Festigkeit der Verbindung ist nicht die Zinkenlänge, sondern der Flankenneigungswinkel. Mit kleiner werdendem Flankenneigungswinkel steigen sowohl die Biege- wie auch die Zugfestigkeit der Verbindung deutlich.[41]
Tragende Bauteile
Bei Keilzinkenverbindungen für tragende Bauteile müssen die Zinkenlänge, die Zinkenteilung und der Verschwächungsgrad in folgendem Verhältnis zueinander stehen:[42]
- bei Zinkenlängen lz = 10 mm: und
- bei Zinkenlängen lz > 10 mm: .
Der Flankenneigungswinkel muss
- bei Zinkenlängen lz = 10 mm: beziehungsweise
- bei Zinkenlängen lz > 10 mm: sein.
Der Verschwächungsgrad muss stets sein.
Bei tragenden Verbindungen wird zwischen Keilzinkenverbindungen einzelner Hölzer und Universalkeilzinkenverbindungen für Brettschichtholz (BSH) unterschieden. So kann durch die Keilzinkenverbindung einzelner Hölzer die Einzellamelle eines Brettschichtholzes gefertigt werden, während die Universalkeilzinkung zwei Brettschichthölzer miteinander verbindet. Die Symmetrieachse der Keilzinken muss stets parallel zur Holzfaserrichtung verlaufen. Wesentlich für die Belastbarkeit einer Keilzinkenverbindung ist das Vorhandensein des so genannten Zinkenspiels, also dem Abstand zwischen der Zinkenspitze und dem Zinkengrund. Das Zinkenspiel gewährleistet, dass sich infolge des bei der Klebung anzuwendenden Längspressdrucks ein sattes Anliegen der Zinkenflanken einstellt. Die Zinkenflanken stellen die Klebeflächen dar.[3]
Universal-Keilzinkenverbindungen erlauben das Kleben hoch belasteter Anschlüsse in beliebigen Winkeln an Balken und Rahmenecken aus BSH. BSH-Bauteile lassen sich auch mit Eckstücken aus Furnierschichtholz und Baufurnier-Sperrholz (aus Nadel- oder Pappelholz) verkleben.[1]
Klebefehler sind im Nachhinein nur schwer nachweisbar und können schwerwiegendere Folgen haben als Fehler mit mechanischen Verbindungsmitteln. Bei tragenden Bauteilen im Sinne der DIN 1052 muss der Hersteller daher von einer unabhängigen Überwachungsstelle zertifiziert sein. Durch die Zertifizierung erwirbt der Hersteller eine „Bescheinigung für den Nachweis der Eignung zum Kleben von tragenden Holzbauteilen“.[43] Dadurch wird gewährleistet, dass der Betrieb über die technischen und organisatorischen Voraussetzungen verfügt, um fehlerfreie Klebungen herzustellen.
Nichttragende Bauteile
Im Bereich nichttragender Bauteile müssen keine Restriktionen hinsichtlich der Zinkengeometrie erfüllt werden. Dementsprechend existieren hier Zinkengeometrien und -anordnungen, bei denen andere Anforderungen an die Keilzinkenverbindung im Vordergrund stehen. Diese Anforderungen beziehen sich primär auf wirtschaftliche und ästhetische Aspekte des Produkts.
Formen der Keilzinkenverbindung
Sofern die zu verbindenden Werkstücke keinen quadratischen Querschnitt haben, ist ein grundsätzliches Unterscheidungsmerkmal die Richtung der Zinkenverbindung bezüglich der Querschnittsabmessung des Holzes.[44] Die Zinken können rechtwinklig oder parallel zur Breitseite des Holzes gefertigt werden.
Horizontale Keilzinkung
Das Zinkenprofil ist an der Schmalseite des Werkstücks sichtbar. Die horizontale Keilzinkung wird hauptsächlich bei Werkstücken im Sichtbereich angewendet, beispielsweise bei Möbelplatten und Parkett aus Vollholz.
Eine besondere Form der Horizontalzinkung ist die Kronenfuge, die im handwerklichen Bereich zum Einsatz kommt. Sie besitzt stets zwei Zinken.[45] Im Gegensatz zur Keilzinkenverbindung – bei der die Zinken auf der Hirnseite des Werkstücks angeordnet sind – ist die Kronenfuge eine Fugenverbindung. Die Zinken werden in die Längsseite des Werkstücks eingebracht.[46]
- Horizontal-Zinkung, Positiv-Negativ-Profil mit Randzinken
- Horizontal-Zinkung, Halbschulterprofil mit Randzinken
- Horizontal-Zinkung, Wechselschulterprofil mit Randzinken
- Horizontal-Zinkung, Trapezprofil ohne Randzinken
Vertikale Keilzinkung
Das Zinkenprofil ist über die gesamte Breitseite des Werkstücks sichtbar. Die vertikale Keilzinkung wird vor allem im konstruktiven Holzbau eingesetzt, beispielsweise für die Herstellung von Konstruktionsvollholz (KVH), Brettschichtholz und Brettsperrholz (BSP).
- Vertikale Zinkung
Randzinken
Ein weiteres Unterscheidungsmerkmal hinsichtlich der Form der Zinkenverbindung ist das Vorhandensein von Randzinken. Sie liegen vor, wenn den außen liegenden Zinken noch eine plane Fläche folgt, die den Abschluss an die Sichtfläche darstellt. Die Herstellung der Randzinken erfordert einen zusätzlichen Arbeitsschritt durch ein separates Werkzeug während der Keilzinkenherstellung. Durch Randzinken wird sichergestellt, dass die Stoßfuge der verbundenen Hölzer eine Gerade ist. Dadurch ergibt sich ein gefälligeres Erscheinungsbild der Sichtfläche. Bei tragenden Bauteilen sind Randzinken nicht zulässig. Die Stoßfuge kann abhängig von der Geometrie der Holzoberfläche dadurch ungleichmäßig verlaufen. Tragende Bauteile weisen im Allgemeinen keine Sichtflächen auf oder die ästhetischen Anforderungen treten gegenüber den Festigkeitseigenschaften in den Hintergrund.
Randzinken werden sowohl bei vertikalen wie auch bei horizontalen Keilzinkenverbindungen angewendet.
Anwendung
Die Keilzinkenverbindung wird in einer Vielzahl verschiedener Produkte aus Vollholz und Holzwerkstoffen eingesetzt. Im konstruktiven Holzleimbau werden Brettschichtholz, Konstruktionsvollholz, Brettsperrholz, Kreuzbalken, DUO- und TRIO-Balken vorrangig durch Keilzinkung hergestellt.[47] Auch Kanthölzer, Bohlen und Bretter sind oftmals keilgezinkt.[48] Bei der Fertigung von Schalungsträgern kommt die Keilzinkung mehrfach zur Anwendung. Gurte und Stege werden durch Keilzinken bis zur benötigten Länge verbunden. Das Fügen von Gurt und Steg kann ebenfalls durch Keilzinkung erfolgen.[49] Alle diese Vorprodukte werden vielfältig in Ingenieursbauten wie Häusern, Hallen, Brücken, Türmen und anderen Tragwerken eingesetzt. Im Innenausbau sind Fenster- und Türelemente, Leisten, Treppenstufen und -geländer sowie Massivholzfußböden typische Anwendungen.[50] Im Möbelbau finden sich Keilzinkenverbindungen in Arbeitsplatten und Möbelholzplatten zur Herstellung von Massivholzmöbeln.[51] Auch Bilderrahmen und Kleiderbügel werden durch Keilzinkung hergestellt.
Anmerkungen
- Der Begriff Schiftzinkung ist vermutlich in Anlehnung an die Schäftung gewählt worden, da die Geometrie des zugespitzten Holzes zweier aufeinanderliegender geschäfteter Hölzer entspricht.
- Abweichend hiervon wird in der DIN 68140-1 die erste Ausgabe auf den Juni 1960 datiert.
Literatur
- Vanessa Angst, Manfred Augustin u. a.: Handbuch 1 – Tragwerke aus Holz. (PDF; 7 MB) In: Lehrunterlagen für den Entwurf und Konstruktion von Holztragwerken – TEMTIS. Dezember 2008, abgerufen am 8. Juni 2012.
- Fördergesellschaft Holzbau und Ausbau mbH (Hrsg.): 100 Jahre Bund Deutscher Zimmermeister. 1. Auflage. Bruder, Karlsruhe 2003, ISBN 3-87104-143-2.
- Peter Glos, Dietger Grosser, Borimir Radovic, Wolfgang Rug: Holzbau Handbuch, Reihe 4 Baustoffe, Teil 1 Allgemeines, Folge 1 Holz als konstruktiver Baustoff. 2008, ISSN 0446-2114 (mh-massivholz.de (Memento vom 13. August 2012 im Internet Archive) [PDF; 7,0 MB; abgerufen am 25. Juni 2012]).
- Otto Graf, Karl Egner: Versuche mit geleimten Laschenverbindungen aus Holz. In: Holz als Roh- und Werkstoff. Band 1, Nr. 12, 1938, S. 460–464, doi:10.1007/BF02608801.
- Elmar Josten, Thomas Reiche, Bernd Wittchen: Holzfachkunde – Ein Lehr-, Lern- und Arbeitsbuch für Tischler/Schreiner, Holzmechaniker und Fachkräfte für Möbel-, Küchen- und Umzugsservice. 5. Auflage. Vieweg+Teubner, Wiesbaden 2009, ISBN 978-3-8348-0530-0.
- Verena Krackler, Daniel Keunecke, Peter Niemz: Verarbeitung und Verwendungsmöglichkeiten von Laubholz und Laubholzresten. In: ETH Zürich, Institut für Baustoffe – Holzphysik (Hrsg.): Research Collection der ETH Zürich. 15. Juli 2010, doi:10.3929/ethz-a-006113078.
- Karin Lißner, Ansgar Felkel, Klaus Hemmer, Borimir Radovic, Wolfgang Rug, Dieter Steinmetz: DIN 1052 – Praxishandbuch Holzbau. 2. Auflage. Beuth Verlag, Berlin 2010, ISBN 978-3-410-17176-8 (eingeschränkte Vorschau in der Google-Buchsuche).
- Ulf Lohmann: Holz-Lexikon. 4. Auflage. Band 1: A–K. DRW-Verlag, Leinfelden-Echterdingen 2003, ISBN 3-87181-355-9.
- Joseph-Eric Marian: Ein neues Verfahren für die Keilzinkung von Holz und seine Grundlagen. In: Holz als Roh- und Werkstoff. Band 26, Nr. 2, 1968, S. 41–45, doi:10.1007/BF02615808 (diva-portal.org [PDF; 12,0 MB; abgerufen am 12. März 2012]).
- José Luis Moro: Baukonstruktion – vom Prinzip zum Detail. Band 3 Umsetzung. Springer, Berlin 2009, ISBN 978-3-540-85913-0, doi:10.1007/978-3-540-85914-7.
- Hans-Wolf Reinhardt: Zum Gedenken an Otto Graf, universeller Bauforscher in Stuttgart. Univ., Stuttgart 2006, ISBN 3-926269-71-5 (uni-stuttgart.de [PDF; 5,0 MB; abgerufen am 7. März 2012]).
- Wolfgang Rug: Innovationen im Holzbau – Die Hetzerbauweise (Teil 2). In: Bautechnik: Zeitschrift für den gesamten Ingenieurbau. Band 72, Nr. 4, 1995, ISSN 0932-8351, S. 231–241 (Seite nicht mehr abrufbar, Suche in Webarchiven: holzbau-statik.de [abgerufen am 7. März 2012]).
- Kurt Rügge: Stand der Technologie beim Keilzinken von Holz. In: Holz als Roh- und Werkstoff. Band 34, Nr. 11, 1976, S. 403–411, doi:10.1007/BF02608006.
- André Wagenführ, Frieder Scholz (Hrsg.): Taschenbuch der Holztechnik. Fachbuchverlag Leipzig im Carl Hanser Verlag, München 2008, ISBN 3-446-22852-7.
Normen
- Deutsches Institut für Normung e. V. (Hrsg.): DIN 68140-1 Keilzinkenverbindungen von Nadelholz für tragende Bauteile. Februar 1998 (zurückgezogen).
- Deutsches Institut für Normung e. V. (Hrsg.): DIN EN 385 Keilzinkenverbindungen im Bauholz – Leistungsanforderungen und Mindestanforderungen an die Herstellung; Deutsche Fassung EN 385:2001. November 2007.
- Deutsches Institut für Normung e. V. (Hrsg.): DIN EN 387 Universal-Keilzinkenverbindungen – Leistungsanforderungen und Mindestanforderungen an die Herstellung; Deutsche Fassung EN 387:2001. April 2002.
- Deutsches Institut für Normung e. V. (Hrsg.): DIN EN 15497 Keilzinkenverbindungen im Bauholz – Leistungsanforderungen und Mindestanforderungen an die Herstellung; Deutsche Fassung prEN 15497:2011. September 2011 (Normentwurf).
Weblinks
- Keilzinkenverbindung - Formen von Keilzinkenverbindungen. Höchsmann GmbH, abgerufen am 9. März 2012 (Informationen zu Normung, Einsatzgebieten und Formen von Keilzinkenverbindungen).
- Verzeichnis anerkannter Leimbaubetriebe und Verzeichnis zugelassener Klebstoffe. Materialprüfungsanstalt Universität Stuttgart, abgerufen am 9. März 2012 (Verzeichnis der Betriebe, welche den Eignungsnachweis zum Kleben tragender Holzbauteile gemäß DIN 1052 erbracht haben; Verzeichnis geprüfter Klebstoffe im Anwendungsbereich der DIN 1052 und allgemeiner bauaufsichtlicher Zulassung; Verzeichnis der Klebstoffe, die zur Verklebung von Brettschichtholz nach DIN EN 14080:2005 geeignet sind).
Einzelnachweise
- Deutsches Institut für Normung e. V. (Hrsg.): DIN EN 387 Universal-Keilzinkenverbindungen – Leistungsanforderungen und Mindestanforderungen an die Herstellung; Deutsche Fassung EN 387:2001. 2002, S. 4.
- Elmar Josten, Thomas Reiche, Bernd Wittchen: Holzfachkunde – Ein Lehr-, Lern- und Arbeitsbuch für Tischler/Schreiner, Holzmechaniker und Fachkräfte für Möbel-, Küchen- und Umzugsservice. 2009, S. 318, S. 481.
- José Luis Moro: Baukonstruktion – vom Prinzip zum Detail. 2009, S. 262–263.
- Vanessa Angst, Manfred Augustin u. a.: Handbuch 1 – Tragwerke aus Holz. 2008, S. 150 f., S. 164.
- André Wagenführ, Frieder Scholz (Hrsg.): Taschenbuch der Holztechnik. 2008, S. 135.
- Gerd Habenicht: Kleben – Grundlagen, Technologien, Anwendungen. 6. Auflage. Springer-Verlag, Berlin 2009, ISBN 978-3-540-85264-3, S. 927 (eingeschränkte Vorschau in der Google-Buchsuche).
- Deutsches Institut für Normung e. V. (Hrsg.): DIN 68140-1 Keilzinkenverbindungen von Nadelholz für tragende Bauteile. 1998, S. 2.
- Deutsches Institut für Normung e. V. (Hrsg.): DIN EN 385 Keilzinkenverbindungen im Bauholz – Leistungsanforderungen und Mindestanforderungen an die Herstellung; Deutsche Fassung EN 385:2001. 2007, S. 4.
- Fördergesellschaft Holzbau und Ausbau mbH (Hrsg.): 100 Jahre Bund Deutscher Zimmermeister. 2003, S. 370.
- Otto Graf, Karl Egner: Versuche mit geleimten Laschenverbindungen aus Holz. 1938, S. 464.
- Hans-Wolf Reinhardt: Zum Gedenken an Otto Graf, universeller Bauforscher in Stuttgart. 2006, S. 30–32.
- Ulf Lohmann: Holz-Lexikon. 2003, S. 666–667.
- Hans-Wolf Reinhardt: Zum Gedenken an Otto Graf, universeller Bauforscher in Stuttgart. 2006, S. 35–37.
- Wolfgang Rug: Innovationen im Holzbau – Die Hetzerbauweise (Teil 2). 1995, S. 239.
- Fördergesellschaft Holzbau und Ausbau mbH (Hrsg.): 100 Jahre Bund Deutscher Zimmermeister. 2003, S. 371.
- Kurt Rügge: Stand der Technologie beim Keilzinken von Holz. 1976, S. 403.
- Hans-Wolf Reinhardt: Zum Gedenken an Otto Graf, universeller Bauforscher in Stuttgart. 2006, S. 36.
- Joseph-Eric Marian: Ein neues Verfahren für die Keilzinkung von Holz und seine Grundlagen. 1968, S. 43.
- José Luis Moro: Baukonstruktion – vom Prinzip zum Detail. 2009, S. 262.
- Peter Niemz, Fritz Bächle, Walter Sonderegger, Kristin Junghans, Yvonne Herbers: Grundlagen der Holzbe- und Verarbeitung. (PDF; 14 MB) In: Research Collection der ETH Zürich. ETH, Eidgenössische Technische Hochschule Zürich, Institut für Baustoffe IfB, 2007, S. 2–15, abgerufen am 10. August 2012 (doi:10.3929/ethz-a-005433202).
- Karin Lißner, Ansgar Felkel, Klaus Hemmer, Borimir Radovic, Wolfgang Rug, Dieter Steinmetz: DIN 1052 – Praxishandbuch Holzbau. 2010, S. 62–64, S. 103.
- Walter Stampfli, Thomas Meyer: Berührungsloser Klebstoffauftrag auf Keilzinken. In: Adhäsion Kleben & Dichten. Nr. 10. Springer Vieweg, 2008, ISSN 0001-8198 (Seite nicht mehr abrufbar, Suche in Webarchiven: purbond.com [abgerufen am 20. August 2012]).
- Verena Krackler, Daniel Keunecke, Peter Niemz: Verarbeitung und Verwendungsmöglichkeiten von Laubholz und Laubholzresten. 2010, S. 64.
- Verena Krackler, Daniel Keunecke, Peter Niemz: Verarbeitung und Verwendungsmöglichkeiten von Laubholz und Laubholzresten. 2010, S. 22.
- Deutsches Institut für Normung e. V. (Hrsg.): DIN EN 15497 Keilzinkenverbindungen im Bauholz – Leistungsanforderungen und Mindestanforderungen an die Herstellung; Deutsche Fassung prEN 15497:2011. 2011, S. 9.
- Verena Krackler, Daniel Keunecke, Peter Niemz: Verarbeitung und Verwendungsmöglichkeiten von Laubholz und Laubholzresten. 2010, S. 23.
- Peter Glos, Dietger Grosser, Borimir Radovic, Wolfgang Rug: Holzbau Handbuch, Reihe 4 Baustoffe, Teil 1 Allgemeines, Folge 1 Holz als konstruktiver Baustoff. 2008, S. 45–48.
- Brettschichtholz. (Nicht mehr online verfügbar.) WECOBIS Ökologisches Baustoffinformationssystem, archiviert vom Original am 30. Dezember 2011; abgerufen am 20. Juni 2012.
- Verena Krackler, Daniel Keunecke, Peter Niemz: Verarbeitung und Verwendungsmöglichkeiten von Laubholz und Laubholzresten. 2010, S. 66.
- Holzmarktbericht 2010. (PDF; 1 MB) Bundesministerium für Ernährung, Landwirtschaft und Verbraucherschutz (BMELV), August 2011, S. 5, abgerufen am 19. Juni 2012.
- A. Frühwald, J. B. Ressel, A. Bernasconi: Hochwertiges Brettschichtholz aus Buchenholz. (PDF; 5 MB) Juli 2003, archiviert vom Original am 25. April 2012; abgerufen am 19. Juni 2012.
- Hans Joachim Blaß, J. Denzler, Matthias Frese, Peter Glos, P. Linsemann: Biegefestigkeit von Brettschichtholz aus Buche. Universitätsverlag Karlsruhe, Karlsruhe 2005, ISBN 3-937300-40-6, doi:10.5445/KSP/1000001371 (digbib.ubka.uni-karlsruhe.de [PDF; 12,0 MB; abgerufen am 19. Juni 2012]).
- Matthias Frese: Biegefestigkeit von Brettschichtholz aus Buche – Experimentelle und numerische Untersuchungen zum Laminierungseffekt. Universitätsverlag Karlsruhe, Karlsruhe 2006, ISBN 3-86644-043-X, doi:10.5445/KSP/1000004599 (digbib.ubka.uni-karlsruhe.de [PDF; 13,0 MB; abgerufen am 19. Juni 2012]).
- Hans Joachim Blaß, Matthias Frese: Biegefestigkeit von Brettschichtholz-Hybridträgern mit Randlamellen aus Buchenholz und Kernlamellen aus Nadelholz. Universitätsverlag Karlsruhe, Karlsruhe 2006, ISBN 3-86644-072-3, doi:10.5445/KSP/1000005148 (digbib.ubka.uni-karlsruhe.de [PDF; 7,0 MB; abgerufen am 20. Juni 2012]).
- BS-Holz aus Buche und BS-Holz Buche-Hybridträger. (PDF; 2 MB) Deutsches Institut für Bautechnik, 7. Oktober 2009, abgerufen am 20. Juni 2012.
- Verena Krackler, Daniel Keunecke, Peter Niemz: Verarbeitung und Verwendungsmöglichkeiten von Laubholz und Laubholzresten. 2010, S. 67.
- Verena Krackler, Daniel Keunecke, Peter Niemz: Verarbeitung und Verwendungsmöglichkeiten von Laubholz und Laubholzresten. 2010, S. 65.
- Massivholzplatte (1-schicht / mehrschicht). (Nicht mehr online verfügbar.) WECOBIS Ökologisches Baustoffinformationssystem, archiviert vom Original am 21. Februar 2012; abgerufen am 20. Juni 2012.
- Karin Lißner, Ansgar Felkel, Klaus Hemmer, Borimir Radovic, Wolfgang Rug, Dieter Steinmetz: DIN 1052 – Praxishandbuch Holzbau. 2010, S. 103.
- Klebstoffliste I der MPA Universität Stuttgart betreffend geprüfter Klebstoffe im Geltungsbereich der DIN 1052 und allgemeiner bauaufsichtlicher Zulassungen. (PDF; 605 kB) Materialprüfungsanstalt Universität Stuttgart, 25. Juni 2021, abgerufen am 13. Februar 2022.
- André Wagenführ, Frieder Scholz (Hrsg.): Taschenbuch der Holztechnik. 2008, S. 135, S. 517–518.
- Deutsches Institut für Normung e. V. (Hrsg.): DIN 68140-1 Keilzinkenverbindungen von Nadelholz für tragende Bauteile. 1998, S. 3.
- Karin Lißner, Ansgar Felkel, Klaus Hemmer, Borimir Radovic, Wolfgang Rug, Dieter Steinmetz: DIN 1052 – Praxishandbuch Holzbau. 2010, S. 62–64, S. 102.
- Keilzinkenverbindung. Höchsmann GmbH, 2013, abgerufen am 13. Juli 2014.
- Elmar Josten, Thomas Reiche, Bernd Wittchen: Holzfachkunde – Ein Lehr-, Lern- und Arbeitsbuch für Tischler/Schreiner, Holzmechaniker und Fachkräfte für Möbel-, Küchen- und Umzugsservice. 2009, S. 296.
- Andreas Kalweit, Christof Paul, Sascha Peters, Reiner Wallbaum: Handbuch für Technisches Produktdesign – Material und Fertigung – Entscheidungsgrundlage für Designer und Ingenieure. 2. Auflage. Springer-Verlag, Berlin 2012, ISBN 978-3-642-02641-6, S. 177, doi:10.1007/978-3-642-02642-3 (eingeschränkte Vorschau in der Google-Buchsuche).
- Verena Krackler, Daniel Keunecke, Peter Niemz: Verarbeitung und Verwendungsmöglichkeiten von Laubholz und Laubholzresten. 2010, S. 67, S. 71, S. 74 f.
- Peter Glos, Dietger Grosser, Borimir Radovic, Wolfgang Rug: Holzbau Handbuch, Reihe 4 Baustoffe, Teil 1 Allgemeines, Folge 1 Holz als konstruktiver Baustoff. 2008, S. 71.
- Patent DE10121522C1: Schalungsträger. Angemeldet am 3. Mai 2001, veröffentlicht am 31. Oktober 2002, Anmelder: Doka Industrie GmbH, Amstetten, AT, Erfinder: Antrag auf Nichtnennung.
- Elmar Josten, Thomas Reiche, Bernd Wittchen: Holzfachkunde – Ein Lehr-, Lern- und Arbeitsbuch für Tischler/Schreiner, Holzmechaniker und Fachkräfte für Möbel-, Küchen- und Umzugsservice. 2009, S. 297, S. 481.
- Verena Krackler, Daniel Keunecke, Peter Niemz: Verarbeitung und Verwendungsmöglichkeiten von Laubholz und Laubholzresten. 2010, S. 65.