Gesamtanlageneffektivität
Die Gesamtanlageneffektivität (oder englisch Overall Equipment Effectiveness, OEE; Overall Asset Effectiveness, OAE) ist eine betriebswirtschaftliche Kennzahl, mit welcher die Produktivität und etwaige Verluste von technischen Anlagen oder Maschinen gemessen werden kann.
Allgemeines
Die Kennzahl ist im Rahmen der Total Productive Maintenance von Bedeutung und wurde 1988 vom Japan Institute of Plant Maintenance entwickelt.[1] Je höher die erzielte Gesamtanlageneffektivität einer Anlage, desto größer ist das Leistungspotential, das dem Produktionsprozess zur Verfügung gestellt wird. Die Maximierung der Gesamtanlageneffektivität gehört damit zu den obersten formalen Zielen auch bei der Instandhaltung von Anlagen.[2]
Berechnung
Die Gesamtanlageneffektivität besteht aus den Faktoren Verfügbarkeit (englisch availability; ), Leistungsgrad (englisch performance rate;) und Qualitätsrate (englisch quality rate;):
- .
Die Verfügbarkeit setzt sich aus geplantem Maschinenstillstand, Produktionsplananpassungen, Funktionsstörungen und Prozessfehlern zusammen, bei der Qualitätsrate spielen Ausschuss und Nacharbeiten eine Rolle.
Der Wertebereich der Gesamtanlageneffektivität liegt zwischen 0 und 1 oder zwischen 0 % und 100 %.
Die Definition der Kennzahl kann in keiner Norm nachgelesen werden. Sie wird sehr individuell auf das anwendende Unternehmen zugeschnitten. Dabei handelt es sich im Regelfall um einen länger andauernden Prozess, da im Unternehmen erst Verständnis für die Art des Denkens in den Kategorien Wertschöpfung und Verschwendung aufgebaut werden muss. Weiterhin gestaltet sich abhängig von den Anlagen bzw. Produkten die Erfassung der nötigen Basisdaten zur Ermittlung der Kennzahl u. U. als schwierig. Viele Unternehmen setzen daher auf spezielle Software zur Datensammlung, Auswertung und Analyse. Die Gesamtanlageneffektivität ergibt gemeinsam mit der Gesamtserviceeffizienz (OSE oder englisch Overall Service Effectiveness) die Overall Administration Effectiveness (OAE) eines Unternehmens.
Kriterien der Gesamtanlageneffektivität
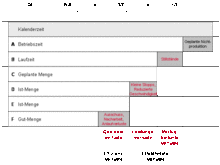
Die Gesamtanlageneffektivität ist eine Kennzahl für ungeplante Verluste einer Anlage. Daher werden im ersten Schritt von der Kalenderzeit (24 Stunden an 7 Tagen in der Woche) die geplanten Stillstände abgezogen. Geplante Stillstände können beispielsweise sein:
- keine Belegung/Besetzung,
- geplante Wartung,
- Arbeitspause,
- Streik,
- keine Produktion aus anderen Gründen.
Die verbleibende Betriebszeit (Nutzungszeit) ist die Basis für die Gesamtanlageneffektivität und wird damit als 100 % definiert. Von diesen 100 % werden die Leistungs-, Verfügbarkeits- und Qualitätsverluste abgezogen, so dass sich die Gesamtanlageneffektivität der Anlage ergibt.
Verfügbarkeitsfaktor
Der Verfügbarkeitsfaktor ist das Verhältnis aus der Zeit bis zum Auftreten eines Fehlers und der Zeit des Ausfalls der Funktion. Der Verfügbarkeitsfaktor ist wie folgt definiert:
- .
Dabei ist der Durchschnittswert der Zeit zwischen Ausfällen und der Durchschnittswert der Wiederherstellungszeit. Mit der Normänderung DIN EN 13306:2017 kann die Verfügbarkeit eindeutig beschrieben werden. Für die Laufzeit der Einheit wurde jetzt die Kennzahl MOTBF (englisch mean operating time between failures) in die Norm aufgenommen. Die Berechnung der Gesamtanlageneffektivität ist dadurch eindeutiger geworden.
Der Verfügbarkeitsfaktor reduziert sich durch die Wiederherstellungszeit wie beispielsweise folgende Ereignisse:
- Warten auf die Instandhaltung,
- Stromausfall,
- Fehler an der Anlage (Störung der Funktion).
Im Unternehmen muss eine Konvention vereinbart werden, ab wann ein ungeplanter Stillstand vorliegt. Jede Sekunde Anlagenausfall zu erfassen und auch zu begründen, bedeutet bei den meisten Unternehmen einen zu hohen Aufwand. In der betrieblichen Praxis hat sich eine Erfassungsgrenze von 1 Minute Anlagenausfall als pragmatischer Ansatz gezeigt. Alle Stillstände über einer Minute gehen damit in den Leistungsfaktor ein.
Ob Rüsten die Gesamtanlageneffektivität (GAE) reduziert, ist eine Frage der unternehmensspezifischen Definition. Reduzieren Rüstaktivitäten die Gesamtanlageneffektivität, entsteht eine Motivation, die Rüstzeiten durch SMED (englisch Single Minute Exchange of Die) zu reduzieren. Andererseits führt dies aber auch dazu, dass eine GAE-Steigerung durch weniger Umbauten, also durch größere Losgrößen, erreicht werden kann. Dies steht den Prinzipien der Schlanken Produktion entgegen. Reduzieren Rüstaktivitäten die GAE nicht, besteht die Gefahr, dass Störungen unrichtigerweise als Rüstvorgang deklariert werden.
Die beste Möglichkeit im Umgang mit Rüstzeiten besteht darin, mit Rüstzeitvorgabewerten zu arbeiten. Die geplante Rüstzeit reduziert die GAE nicht, Rüstzeitüberschreitungen reduzieren sie jedoch. Dafür müssen jedoch Rüstzeitvorgabewerte, bei Bedarf unterschieden für unterschiedliche Rüstvarianten, vorhanden sein. Der Aufwand dafür ist u. U. jedoch sehr groß.
Der Verfügbarkeitsfaktor ist von den drei GAE-Faktoren häufig am leichtesten zu erfassen. Deshalb beginnen GAE-Initiativen in Unternehmen häufig mit der Erfassung des Verfügbarkeitsfaktors.
Leistungsfaktor
Der Leistungsfaktor ist ein Maß für Verluste durch Abweichung von der geplanten Stückzeit, kleineren Ausfällen (also die Stillstände, die nicht in die Verfügbarkeit eingehen) und Leerläufen.
- (zum Beispiel in Stück pro Stunde).
Zu berücksichtigen ist, dass der Leistungsfaktor nur bezogen auf die Laufzeit und nicht auf die Betriebszeit berechnet werden darf.
Während die Ist-Leistung messbar ist, ist es in der betrieblichen Praxis häufig schwierig, an eine Soll-Leistung als Vorgabewert zu kommen. Wenn keine technischen Daten des Maschinenherstellers verfügbar oder diese nicht realistisch sind, hat sich das Konzept der „bestdemonstrierten Stückzeit“ bewährt. Dabei werden die Produktionsgeschwindigkeiten der Produkte aus der Vergangenheit miteinander verglichen und die höchste Produktionsgeschwindigkeit als Soll-Leistung im Sinne von 100 % Leistungsfaktor definiert. Allerdings eignet sich der so gewonnene Leistungsfaktor nicht zur Produktionsprogrammplanung. Der Faktor 1 stelle einen Spitzenwert dar, der regelmäßig nicht erreicht würde.
Bei Anlagen, die nur ein oder wenige Produkte herstellen, ist die Berechnung des Leistungsfaktors einfach. Wird eine Vielzahl von unterschiedlichen Produkten auf einer Anlage gefahren (Mehrproduktunternehmen), ist der Aufwand für die Ermittlung einer Vorgabezeit unter Umständen hoch.
Qualitätsfaktor
Der Qualitätsfaktor ist ein Maß für den Verlust aufgrund defekter und zu überarbeitender Teile. Er ist wie folgt definiert:
- .
Dabei ist die Anzahl der produzierten Teile, die Anzahl der Nacharbeitsteile und die Anzahl der Ausschussteile.
Insbesondere bei der Erfassung des Qualitätsfaktors ist ein pragmatischer Ansatz sinnvoll: Häufig wird ungenügende Qualität nicht an der Anlage entdeckt, die sie verursacht hat. Hier hat es sich bewährt, das „Entdeckerprinzip“ einzusetzen, also die Anlage mit einer GAE-Reduktion zu belasten, an der der Fehler entdeckt wurde. So entfernt sich die GAE von einer reinen Anlagen- und wird zu einer Prozesskennzahl. Die Optimierung der GAE einer Anlage kann aber natürlich auch durch Optimierungen an anderen Anlagen stattfinden. Auch sollte die GAE eine möglichst zeitnahe Kennzahl sein. Insofern sollte die i.O.-Menge spätestens am Losende bestimmt und die GAE berechnet werden. Von nachträglichen Korrekturen der GAE z. B. durch spätere Sperrungen ist abzuraten.
Gesamtanlageneffizienz
Die Bezeichnung Gesamtanlageneffizienz wird in der deutschen Sprache häufig synonym zu Gesamtanlageneffektivität verwendet, auch wenn dies nicht korrekt ist (siehe Effektivität). Maßnahmen, die den Produktionsausstoß erhöhen, dabei aber überproportional hohe Kosten verursachen, können durchaus effektiv, aber gleichzeitig ineffizient und damit ökonomisch nicht sinnvoll sein.
Gesamtanlageneffektivität
Die GAE ist als Produkt von Verfügbarkeitsfaktor, Leistungsfaktor und Qualitätsfaktor definiert. Es ergibt sich ein Prozentwert, der angibt, zu welchem Anteil der geplanten Maschinenlaufzeit tatsächlich den Qualitätskriterien entsprechend produziert wurde.[3]
Dieser Wert liegt meist deutlich unter 100 %, da die einfließenden Faktoren 100 % nie völlig erreichen können. So werden die begrenzenden Faktoren deutlich, an denen gearbeitet werden muss.
Six Big Losses
Eines der Hauptziele der GAE ist es, die Ursachen der sechs höchst relevanten Effizienzverluste (Six Big Losses)[4] zu beeinflussen. GAE hat drei Kategorien: Verfügbarkeit, Leistung und Qualität. In jeder Kategorie gibt es zwei Arten von Verlusten.
Ursache | Kategorie | Bemerkung |
---|---|---|
Ausfall | Verluste bei der Verfügbarkeit | Dazu gehören Störungen und Ausfälle (z. B. Arbeitnehmer, die wegen Krankheit fehlen) |
Einstellung | Verluste bei der Verfügbarkeit | Dazu gehören Werkzeugwechsel und Werkzeugeinstellung |
Micro Stops | Verluste bei der Leistung | Dazu gehören normalerweise Stillstände von weniger als drei Minuten |
Geschwindigkeitsverlust | Verluste bei der Leistung | Alles, was den Prozessablauf mit (theoretischer) Höchstgeschwindigkeit nicht ermöglicht |
Ausschuss beim Anfahren | Verluste bei der Qualität | Ausschuss, der durch Erwärmung, Starten und andere frühe Herstellungsphasen verursacht wird |
Ausschuss bei der Herstellung | Verluste bei der Qualität | Ausschuss, der im Normalbetrieb erzeugt wird |
Die meisten der sechs Ursachen sind nicht auffällig (besonders Micro Stops), aber zusammen können sie zu großen Verlusten führen.
Nutzen der GAE
Der Nutzen der GAE liegt in der Transparenz des Wertschöpfungsanteils der Anlage und lässt das Management mit einem anderen Blick auf die Anlagen schauen. Die Kennzahl ist ideal geeignet, um z. B. an eine GAE-Steigerung einen Zielvereinbarungsprozess anzuknüpfen, weil die Kennzahl aufgrund ihrer Umfänglichkeit robust gegen strukturelle Änderungen der Produktion gestaltet werden kann.
Steigerung der GAE
Zur gezielten Steigerung der GAE müssen die Gründe für Abweichungen der GAE-Faktoren von 100 % erfasst werden. Die Frage ist also, warum wurde(n) nicht
- 100 % der Betriebszeit produziert?
- 100 % der geplanten Geschwindigkeit gefahren?
- 100 % der Produkte in der definierten Qualität produziert?
Durch eine manuelle oder systemgestützte Erfassung (z. B. mit Hilfe von Software zur Betriebsdatenerfassung bzw. Maschinendatenerfassung) der Abweichungen vom definierten Idealzustand kann eine Analyse der Pareto-Verteilung der größten Verlustquellen für eine Anlage erzeugt werden. Daraus lassen sich Maßnahmen zur gezielten Verbesserung der GAE einleiten, die dann auch gemessen werden können. Begonnen wird die Optimierung mit der Quelle des größten GAE-Verlustes.
Beispiel
Eine Maschine arbeitet an 5 Arbeitstagen im Zweischichtbetrieb zu je 7 Stunden und 12 Minuten, die Maschinenlaufzeit beträgt damit 4.320 Minuten.[5] Die Maschine fertigt während dieser Zeit 6.213 Teile, wovon 87 Teile als Ausschuss gelten und 312 Teile einer Nacharbeit zu unterziehen sind:
- .
Die Gesamtanlageneffektivität beträgt im Beispiel 67,29 %.
Praktische Erfahrungen
- Eine in der Praxis erzielte GAE von 85 % kann als „sehr gut“ eingestuft werden. Es gilt hier zu differenzieren, um welchen Anlagentypen/Produktionsmechanismus es sich handelt. So kann ein GAE von 90 % bei einer Vollkonti-Anlage auch als Untergrenze dienen, hingegen kann ein GAE von 60 % bei einem schwierig zu handhabenden Produktionsverfahren eine Obergrenze darstellen.
- Insbesondere bei mehreren ohne Pufferung verketteten Anlagen ist eine GAE des Gesamtsystems von z. B. 85 % schwierig zu erreichen, da die Berechnung durch eine Multiplikation der Einzel-GAEs erfolgt (Bsp.: 3 verkettete Anlagen mit jeweils einer GAE von 90 % führen zu einer OEE des Gesamtsystems von 0,9 × 0,9 × 0,9 = 0,73).
- Bei mehreren mit Pufferung verketteten Anlagen kann die korrekte GAE-Erfassung nur IT-technisch mit mehreren Messstellen durchgeführt werden. Jede einzelne Messstelle benötigt zusätzlich zu den Standardstörgründen noch die Störkategorien "Stau" und "Abriss", um vor- bzw. nachgelagerte Störungen von Produktionsanlagen identifizieren zu können.
- Die Ermittlung der GAE verursacht gerade in der Anfangszeit einen hohen Aufwand einerseits durch die Schulung der Mitarbeiter und andererseits in der Gewinnung von unverfälschten Daten.
- Die GAE kann nicht dazu dienen, die Leistung der Mitarbeiter zu messen. Sie dient zur Ermittlung und Messung von Anlagenverlusten, die anschließend durch entsprechende Ursachenanalysen und Maßnahmen beseitigt werden können.
Wirtschaftliche Aspekte
Insbesondere Produktionsunternehmen mit hoher Anlagenintensität bei technischen Anlagen müssen ihre Anlagenverfügbarkeit genau beobachten. Für Mehrproduktunternehmen, Serienfertigung und Verfahrenstechnik gilt die Gesamtanlageneffektivität als existenziell.[6] Dabei sind ungeplante Stillstände, die Erhöhung des Qualitätsgrades und die Reduzierung von Rüstzeiten von besonderer Bedeutung.
Abgrenzungen
Die GAE ist nicht gleichzusetzen mit anderen Kennzahlen, die üblicherweise in der Produktion oder Instandhaltung erfasst werden wie z. B. der technischen Verfügbarkeit. Der Grund dafür ist, dass bei einer GAE-Kennzahl die Rüstzeit nicht berücksichtigt werden darf (nur die Planbelegzeit). Bei dieser Vorgehensweise fehlt der Blick auf notwendige Optimierungen beim Rüstvorgang.
Siehe auch
Literatur
Eigenständige OEE-Literatur:
- Koch, Arno: OEE für das Produktionsteam. Das vollständige OEE-Benutzerhandbuch – oder wie Sie die verborgene Maschine entdecken. Ansbach: CETPM Publishing, 2008, ISBN 978-3940775047.
- May, Constantin; Koch, Arno: Overall Equipment Effectiveness (OEE) – Werkzeug zur Produktivitätssteigerung, erschienen in: Zeitschrift der Unternehmensberatung (ZUB), H. 6/2008, S. 245–250. zum Herunterladen beim Centre of Excellence for TPM (CETPM) (PDF-Datei; 190 kB)
- Oee for Operators: Overall Equipment Effectiveness, Productivity Development Team, Productivity Press, 1999
In TPM-Literatur:
- TPM – Effiziente Instandhaltung und Maschinenmanagement, Edward Hartmann, Landsberg, Verlag Moderne Industrie, 2000 [S. 77ff.]
- Introduction to TPM, Seiichi Nakajima, Productivity Press Cambridge Massachusetts, 1988 [S. 27ff.]
- Total Productive Maintenance, Al-Radhi, Carl-Hanser-Verlag München, 1995 [S. 30ff.]
- Total Productive Maintenance – The Western Way, Peter Willmott, Butterworth-Heinemann Ltd., 1994 [S. 25ff.]
Einzelnachweise
- Seiichi Nakajima, Introduction to Total Productive Maintenance, 1988, 21 ff.
- Alejandro Alcalde Rasch, Erfolgspotential Instandhaltung, 2000, S. 229
- Jürgen Kletti/Jochen Schumacher, Die perfekte Produktion - Manufacturing Excellence durch Short Interval Technology (SIT), 2010, ISBN 978-3-642-13845-4, S. 80 ff.
- Six Big Losses - Die wichtigsten Verlustursachen der OEE. Symestic, abgerufen am 16. Oktober 2020.
- Holger Regber/Klaus Zimmermann, Change-Management in der Produktion, 2007, S. 129
- Holger Regber/Klaus Zimmermann, Change-Management in der Produktion, 2007, S. 285 f.