Distortion Engineering
Als Distortion Engineering bezeichnet man eine methodische Vorgehensweise zur ingenieurmäßigen Beherrschung von Verzugsursachen.
Diese Vorgehensweise unterstützt einerseits eine verzugsgerechte Konstruktion und Fertigung von Bauteilen und andererseits eine Kompensation der Bauteilverzüge durch die gezielte Nutzung von vorhandenen Verzugspotenzialträgern (VP-Träger) in der Prozesskette. Wesentliches Merkmal des Distortion Engineering ist die Systembetrachtung und die Erkenntnis, dass nur die Betrachtung des Verzugs als eine Eigenschaft in der gesamten Fertigungskette erfolgreich sein kann. Dafür müssen auch die Wechselwirkungen der Einflussfaktoren aus den einzelnen Fertigungsschritten auf den Verzug identifiziert, hinsichtlich ihrer Wirkung verstanden und durch Zusammenarbeit der relevanten Fachdisziplinen in einen systemübergreifenden Lösungsansatz einbezogen werden.
Vorgehensweise
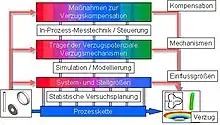
Die Vorgehensweise im Distortion Engineering besteht aus drei Schritten (Bild 1):
- System-, Stellgrößen ermitteln
- Träger der Verzugspotenziale bestimmen
- Maßnahmen zur Verzugskompensation einleiten
Schritt 1
Entlang einer Fertigungskette werden mögliche, signifikante Einflussgrößen in Form von System- und Stellgrößen (Systemgrößen: Maschine, Werkstück, Werkzeug, Kühlschmierung; Stellgröße: Schnittgeschwindigkeit, Vorschubgeschwindigkeit etc.) ermittelt. Eine mögliche Vorgehensweise ist die Anwendung der Methodik Design of Experiments (statistische Versuchsmethodik). Am Ende von Schritt 1 sind alle signifikanten Einflussgrößen ermittelt. Nun muss im nächsten Schritt eine Korrelation zwischen den Einflussgrößen und den VP-Trägern hergestellt werden.
Schritt 2
Die in Schritt 1 ermittelten Einflussgrößen werden für eine prozessübergreifende Beschreibung des Verzugspotenzials (VP) verwendet. Das Verzugspotenzial beinhaltet die Summe aller Einflussmöglichkeiten, Vorgänge auszulösen, die die Maße und Formen eines Bauteils ungünstig beeinflussen können und wird durch den Zustand verschiedener Träger des Verzugspotenzials quantifiziert. Die bisher erkannten Verzugspotenzialträger sind im Folgenden aufgelistet:
- Abmessungen (Geometrie);
- Chemische Zusammensetzung;
- Gefüge;
- (Eigen-)Spannungen;
- Temperatur;
- Mechanische Historie (Verfestigung).
Entscheidend für den Verzug sind jedoch nicht die angegebenen Größen an sich, sondern vielmehr ihre räumliche Verteilung im Werkstück. Die angegebenen VP-Träger wurden am Werkstoff Stahl ermittelt. In anderen Werkstoffen treten unter Umständen andere Träger auf.
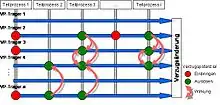
Jeder Teilprozess der Prozesskette kann den Zustand dieser VP-Träger entweder direkt über die Prozessgrößen oder indirekt durch Wechselwirkungen zwischen einzelnen VP-Trägern ändern. Bild 2 zeigt schematisch die Beeinflussung der VP-Träger in einer Prozesskette.
Welche VP-Träger schließlich den Verzug bestimmen, hängt vor allem von der Bauteilgeometrie und dem Herstellungsprozess ab.
Die komplexen Wechselwirkungen, die innerhalb der Werkstücke auftreten, können in der Regel nur durch den Einsatz von Prozesssimulationen erkannt werden (für das Beispiel Stahl beinhalten diese die Gießsimulation, Zerspansimulation, Umformsimulation und Simulation der Wärmebehandlung)
Schritt 3
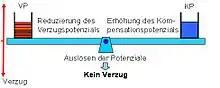
Mit den Erkenntnissen aus Schritt 1 und 2 kann der Fertigungsprozess zunächst verzugsgerecht gestaltet werden. Darüber hinaus kann durch gezielte Änderung ausgewählter VP-Träger ein Kompensationspotenzial erzeugt werden, das den Einfluss der übrigen VP-Träger ausgleicht (Bild 3).
Das Kompensationspotenzial ist definiert als die Summe aller Einflussmöglichkeiten, Vorgänge auszulösen, die die Maße und Formen eines Bauteils günstig beeinflussen können. Globale Kompensationsmaßnahmen werden bereits in der Prozessplanung vorgenommen. Ergänzend zur Qualitätsplanung wird durch das In-Prozess-Messen der Bauteilgeometrie und den Einsatz von entsprechenden Regelungsstrategien die Kompensation für individuelle Bauteile während der Herstellung optimiert.
Praxisbeispiel
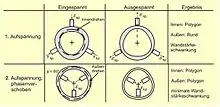

Eine verzugsgerechte Prozessgestaltung kann anhand der Herstellung dünnwandiger Werkstücke (z. B. Wälzlagerringe) erläutert werden. In diesem Fall werden Rundheits- und Wandstärkevariationen, die normalerweise durch aufwendiges Nachbearbeiten (Schleifen) beseitigt werden müssen, durch verschiedene Kompensationsmaßnahmen sukzessive in der Prozesskette minimiert.
Eine Reduzierung der Wandstärkevariationen erfolgt durch Zerspanen (Drehprozess, Bild 4). Während der Bearbeitung bewirkt die Spannkraft Fsp eine elastische Verformung des Werkstücks. Die dadurch bedingte inhomogene Spanabnahme führt normalerweise zu Wandstärkeschwankungen und Rundheitsabweichungen. Indem der Ring bei der zweiten Aufspannung jedoch um 60° gedreht wird und die Spannkraft entsprechend der verringerten Wandstärke (im Vergleich zu der ersten Aufspannung) angepasst wird, werden Wandstärkeschwankungen bereits größtenteils kompensiert.
Die verbleibenden Rundheitsabweichungen werden dann in der nachfolgenden Wärmebehandlung über gezielt asymmetrische Erwärm- und Abschreckbedingungen ausgeglichen.
Literatur
- F. Hoffmann, O. Keßler, Th. Lübben, P. Mayr: Distortion Engineering. Verzugsbeherrschung in der Fertigung. In: HTM. Nr. 57, 2002, S. 213–217.
- K.-D. Thoben, T. Lübben, B. Clausen, C. Prinz, A. Schulz, R. Rentsch, R. Kusmierz, L. Nowag, H. Surm, F. Frerichs, M. Hunkel, D. Klein, P. Mayr: Distortion Engineering. Eine systemorientierte Betrachtung des Bauteilverzugs. In: HTM. Nr. 57, 2002, S. 276–282.
- Th. Lübben, H.-W. Zoch: Distortion Engineering. A Systematic Strategy to Control Dimensional Changes. In: Heat Treatment and Metallography Study Group of AIM (Hrsg.): Innovation in Heat Treatment for Industrial Competitiveness. Verona 7. Mai 2008 (Tagungsband).