Stepper (Halbleitertechnik)
Ein Stepper (auch Wafer-Stepper) ist in der Halbleitertechnik ein Anlagentyp bzw. ein Funktionsprinzip zur fotolithografischen Strukturierung einer Fotolackschicht, einem der wichtigsten Teilprozesse der komplexen Herstellung von integrierten Schaltkreisen, auch Mikrochips genannt. Wichtigstes Merkmal von Steppern ist die Belichtung des Wafers in mehreren gleichen Schritten mit einer Maske. Wafer sind dünne Halbleiterscheiben, auf deren Oberfläche die integrierten Schaltkreise aufgebaut werden. Weitere Belichtungsverfahren sind die 1:1-Belichtung und die Belichtung mittels Scanner-Anlagen.

Hintergrund
Die in der Halbleitertechnik eingesetzten Belichtungsanlagen haben die Aufgabe, die Strukturen auf einer Fotomaske (engl. reticle) in eine aufgetragene Schicht aus Fotolack (engl. resist) zu übertragen. Diese strukturierte Fotolackschicht dient anschließend als Kontaktmaske für nachfolgende Prozesse, wie das Ätzen des darunterliegenden Materials oder eine selektive Beschichtung. Wichtige Kriterien bei dieser Übertragung sind eine möglichst hohe Strukturtreue, das heißt, wie genau die 2D-Geometrie der Maske übertragen wird, und eine hohe Positionierungspräzision relativ zu vorhergehenden Strukturierungsebenen, vgl. Overlay (Halbleitertechnik).
In der Anfangszeit der Mikroelektronik bis zum Ende der 1970er-Jahre wurde diese Strukturübertragung (die Belichtung des Fotolacks) in einer Ganzscheibenbelichtung durchgeführt. Dabei wurde die Fotolackschicht auf dem gesamten Wafer (damals mit einem Durchmesser von höchstens 100 mm) in einem Schritt belichtet. Die Fotomaske war so groß wie die Wafer, und die Strukturen auf der Maske waren so groß wie die gewünschten Strukturen auf dem Wafer (1:1-Projektionsbelichtung). Mit der stetigen Verkleinerung der Strukturen auf dem Wafer und dem Einsatz größerer Wafer ergaben sich zunehmend Probleme, beispielsweise die Herstellung der Strukturen auf der Maske und auch die Maskengröße.
Aus diesen Gründen wurden bereits Anfang der 1960er-Jahre neue Konzepte mit zwei Produktionsschritten von David W. Mann in Burlington (USA) entwickelt. GCA (Geophysical Corporation of America) kauft 1959 David Mann und 1965 wird in Kreuzlingen in der Schweiz aktiv. Das Stepper-Prinzip wurde nach 1961 (erster Verkauf an Clevite Corp. mit einer Nikon-Optik) dann ab 1969 industriell in Europa bei IBM, Valvo, Philips, Siemens, Mullard, SGS Ates, GI, Texas Instruments und anderen Halbleiterherstellern sowie in der Forschung der Uni Aachen eingesetzt. Eine typische Reduktion im Repeater von David Mann ist der Faktor zehn, bessere Ergebnisse erzielen nun die Zeiss-Objektve. Bevor ein Photorepeater zum Einsatz kommt, wird im Pattern Generator 3000 eine gezeichnete Maske auf einer 100-x-100-mm-Glasplatte auf die Emulsion belichtet. Die Genauigkeiten dieser frühen Anlagen basierte auf zwei Glasmaßstäben die übereinander von einer hochpräzisen Spindel bewegt wurden. Die durchscheinenden Lichtsignale erzeugten Interferenz Impulse und ermöglichten, mit einer DIGITAL PDP-8 ausgewertet und interpoliert, die Genauigkeit der Positionierung von 1µ mit den X- und Y-Stellmotoren zu erreichen. Spätere Modelle des Pattern Generators 3600 hatten einen größeren (150 × 150 mm) noch präziseren X-Y-Tisch und wurden mit zwei HP-Laser-Messeinrichtungen gesteuert, hier benötigte man schon eine DIGITAL PDP-11. Der GCA 4800 DSW (Direct Step on the Wafer) war ab 1979 in der Industrie in USA, Japan und Europa im Einsatz.
Step-and-Repeat-Prinzip
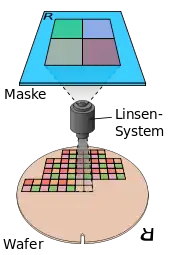
Anders als bei der zuvor genannten Ganzscheibenbelichtung werden beim Stepper die Strukturen der Fotomaske nicht in einem Schritt auf den gesamten Wafer übertragen. Stattdessen wird ein bestimmter Ausschnitt des vollständigen Layouts, beispielsweise die Strukturen eines einzelnen oder einiger weniger (2–8) Chips, nacheinander auf verschiedene Positionen des Wafers übertragen. Diese Übertragung in Schritten (engl. steps) gab dem Verfahren seinen Namen. Genau genommen handelt es sich dabei um das Step-and-Repeat-Prinzip.
Der Einsatz des Stepper-Prinzips hat einige Vorteile gegenüber der Ganzscheibenbelichtung: Es konnten nun Verkleinerungsoptiken (oft 5:1) genutzt werden, denn die Maximalgröße der noch handhabbaren Masken blieb gleich. Größere Strukturen auf den Masken bedeuteten zudem geringe Anforderungen an die Maske selbst, was sich unter anderem in niedrigeren Herstellungskosten äußert. Zudem wurden Defekte durch Partikel im optischen System oder auf der Maske weniger kritisch, da die meisten Partikel nicht im Fokus des Abbildungssystems sind und damit nicht scharf abgebildet werden und sie außerdem verkleinert werden. Der Einsatz von Lichtquellen immer kürzerer Wellenlängen (436 nm, 365 nm, 248 nm bis hin zu 193 nm im Jahr 2011) ermöglicht es in Kombination mit weiteren Verbesserungen der Belichtungsanlagen (z. B. Immersionslithografie) sowie auflösungverbessernden Techniken (RAT), Strukturbreiten bis hinunter auf 32 nm und weniger herzustellen.
Step-and-Scan-Prinzip
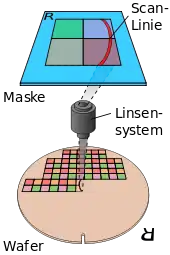
Belichtungsanlagen nach dem Step-and-Scan-Prinzip arbeiten ähnlich wie Anlagen mit Step-and-Repeat-Prinzip. Dabei wird in jedem Schritt nur ein Teil des gesamten Wafers belichtet und die Maske durch das optische System verkleinert abgebildet (in der Regel 4:1). Der Unterschied zwischen den beiden Verfahren liegt in der Belichtung des Teilstücks. Im Gegensatz zu Steppern mit Step-and-Repeat-Prinzip wird die Maske nur in einem schmalen Streifen beleuchtet und unter diesem Lichtstreifen durch gefahren, ähnlich wie es bei Zeilenscannern oder Fotokopierern geschieht. Anlagen, die dieses Prinzip nutzen, werden häufig auch nur als Scanner bezeichnet. Belichtungsanlagen mit einer 1:1-Projektionsbelichtung nach dem Scanner-Prinzip werden seit spätestens Mitte der 1980er-Jahre Front-End nicht mehr angewendet, finden aber seit einigen Jahren wieder im Back-End aufgrund der hohen Durchsätze im Auflösungsbereich 1 µm bis 3 µm ihre Anwendung. Das Step-and-Scan-Prinzip ist seit Mitte der 1990er-Jahre das bevorzugte Belichtungsprinzip bei der Herstellung von modernen integrierten Schaltkreisen.
Siehe auch
Literatur
- Chris Mack: Fundamental Principles of Optical Lithography: The Science of Microfabrication. 1. Auflage. John Wiley & Sons, 2007, ISBN 978-0-470-01893-4 (Hauptquelle).