Fiber Patch Placement
Fiber Patch Placement (kurz FPP) ist die additive Fertigungstechnik zur automatisierten Herstellung von geometrisch komplexen Faserverbundbauteilen aus Carbonfaser, Glasfaser und anderen technischen Fasern.
Funktionsweise
Definierte Stücke (Fiber Patches) werden vollautomatisch aus flachem trockenem oder vorimprägniertem Faserband geschnitten und mit Hilfe von zwei Robotern und einem flexiblen Greifer positionsgenau auf einem dreidimensionalen Formwerkzeug aufgebracht. Durch die Lastpfad-orientierte und annähernd verschnittfreie Ablage der einzelnen Inkremente direkt auf der finalen 3D-Geometrie entfallen zusätzliche Umformschritte. Der formflexible Greifer sowie eine der Oberflächengeometrie angepasste Patch-Größe verhindern ungewollte Drapiereffekte der Fasern bei der Ablage. Damit stellt FPP eine Innovation in der automatisierten Verfahrenstechnik für Faserverbundbauteile dar.[1] Da es für ein breites Bauteilspektrum die vorherrschende Handarbeit ersetzen kann, trägt es maßgeblich zur Industrialisierung der Faserverbundbauteil-Produktion bei.
Ein FPP-Gesamtprozess gliedert sich in zwei Abschnitte:
- Der digitale Entwicklungsprozess umfasst die Laminaterstellung und die Anlagenprogrammierung.
- Im eigentlichen Produktionsprozess wird das geometrisch komplexe Faserhalbzeug additiv gelegt.
Digitaler Entwicklungsprozess
Die Basis des FPP-Prozesses liegt in der Anpassung der Patchgröße an die lokal oder global vorherrschende Bauteilkomplexität, z. B. die Anpassung an eine Geometrie, oder an einen komplexen Lastpfad. Ein FPP-Laminat kann aus mehreren tausend Stücken bestehen. Eine rein händische Programmierung der Produktionsanlagen ist bei dieser Komplexität nicht mehr möglich. Dem eigentlichen Produktionsprozess ist deswegen eine virtuelle Produktentwicklung vorgeschaltet, die auf die FPP-spezifischen Laminat- und Platzierungsfunktionen abgestimmt ist.[2]
Die virtuelle Produktentwicklung besteht im Wesentlichen aus zwei Programmschritten
Im Rahmen des integrierten, digitalen Entwicklungsprozesses findet der gesamte Prozess des Laminatdesigns in einem CAD-Modul statt: Der Nutzer definiert mit Hilfe der Software Materialeigenschaften und Faserorientierungen, um dann Faserlaminate basierend auf importierten CAD-Daten zu erzeugen und bei Bedarf individuelle Anpassungen durchzuführen. Dabei werden die zu legenden Faser-Patches so gewählt, dass die automatisierte Verarbeitung sichergestellt ist.
Zur Programmierung der Roboter für die zahlreichen einzelnen Legevorgänge ist die automatisierte Maschinendatenerstellung über ein CAM-Modul integriert. Basierend auf dem zuvor erstellten Laminat und einem digitalen Zwilling des Produktionssystems werden die notwendigen Roboterkoordinaten vollautomatisch generiert. Die Software berechnet die besten Roboterbewegungen zur Platzierung der Patches und führt eine Kollisionskontrolle aus, um eine sichere Produktion zu gewährleisten. Zudem kann die Zykluszeit durch eine Reihenfolge-Optimierung verbessert werden.
Produktionsprozess
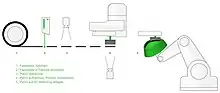
Zur Fertigung des Laminats im Produktionssystem sind im Wesentlichen 5 Prozessschritte nötig, wie in der Illustration bezeichnet.
- Faserband zuführen
- Faserband in Patches schneiden
- Patch überprüfen
- Patch aufnehmen und Position kontrollieren
- Patch auf 3D-Werkzeug ablegen
Eine Bandzuführungseinheit transportiert das Ausgangsmaterial – Trockenfaser-Tape oder Towpreg – in Form von Endlosfaserband zur Laser- oder Ultraschall-Schneideeinheit, die die Patches vom zugeführten Faserband abschneidet. Alternativ kann das Ausgangsmaterial auch direkt in Patchform z. B. auf einem Legetisch vorliegen und von dort aufgenommen werden.
Die Bildverarbeitung analysiert die von einer hochauflösenden Kamera gemachten Patchbilder durch Algorithmen und prüft die Patches so auf Qualität und Maßhaltigkeit. Die prozessintegrierte Qualitätskontrolle erkennt Patches, die Defekte aufweisen oder außerhalb der Größentoleranzen liegen, und sortiert diese aus, ohne das laufende Legeprogramm zu beeinflussen.
Ein an einem Roboterarm montierter formadaptiver Greifer nimmt den einwandfreien Patch auf und transportiert ihn zum jeweiligen Ablageort. Auf dem Weg zum Ablageort erwärmen Heizvorrichtungen den Patch, um die jeweiligen Binder ausreichend haftend für die Ablage zu machen. Parallel identifiziert ein zweites Bildverarbeitungssystem die relative Position des Patches nach der Aufnahme durch den Greifer, misst eventuelle Abweichungen vom definierten Mittelpunkt und korrigiert entsprechend die Maschinendaten/Roboterkoordinaten, um die Abweichung bei der Ablage auf dem Werkzeug auszugleichen und dadurch eine hochpräzise Ablage gemäß definiertem Laminat zu gewährleisten. Auch dieser Kontrollvorgang wird für eine lückenlose Qualitätsüberwachung detailliert dokumentiert.
Abschließend legt der Patch-Greifer den Patch an der berechneten Position auf dem Werkzeug ab. Der Andruck erfolgt durch die passive Anpassungsfähigkeit des Greifers an die Oberfläche. Bei Bedarf unterstützt eine rollierende Bewegung der vorletzten Roboterachse um den Ablagepunkt die Ablage auf stark gekrümmten Oberflächen. So können Legefehler und ungewünschte Drapiereffekte zuverlässig vermieden werden.[3]
Anwendungsgebiete
Mit Hilfe von FPP können komplexe Faserbauteile, die bislang oft von Hand gefertigt werden mussten, automatisiert und in großen Stückzahlen hergestellt werden. Hierzu ist insbesondere die Fähigkeit, verschiedene Fasermaterialien mit einem System zu verarbeiten, sehr relevant. Das Verfahren eignet sich aber auch dazu, konventionell hergestellte Bauteile zu verstärken. In beiden Fällen bedingen der geringere Materialverbrauch und der signifikant reduzierte Verschnitt eine wesentliche Materialreduktion des fertigen Bauteils. Weitere Vorteile liegen in den Produktionskosten, die durch die Automatisierung häufig signifikant gesenkt werden können. Folglich kommt FPP-Technik überall da zum Einsatz, wo Hochleistungsbauteile aus Faserverbund mit gerichteter Faserorientierung in höheren Stückzahlen eingesetzt werden, z. B. in der Luftfahrt, in der Medizintechnik, im Automobilbau, und vielen weiteren Anwendungen.
Luft- und Raumfahrt
- Multimaterial-Bauteile
- Sandwichstrukturen, z. B. Verkleidungen, Gondelstrukturen, Radome, Steuerflächen, UAV-Strukturen
- Metall-Metall-Verbindungen mit Klebefilmen
- Komplexe Geometrien
- Fenstertrichter
- Luftkanäle
- Batteriekästen und -deckel
Wasserstoff-Tanks
- Verstärkung von Hochdrucktank-Kuppeln
Medizintechnik
Einzelnachweise
- vgl. Kalle Kind: Konfektionierte Halbzeuge Lehrstuhl für Carbon Composites, Technische Universität München, 2015/2016.
- vgl. Benjamin Fischer, Bernhard Horn, Christian Bartelt, Yannick Blößl: Method for an Automated Optimization of Fiber Patch Placement Layup Designs. In: International Journal of Composite Materials. Band 5, Nr. 2, 2015, S. 37–46.
- vgl. Oliver Meyer: Kurzfaser-Preform-Technologie zur kraftflussgerechten Herstellung von Faserverbundbauteilen. Dissertation, Institut für Flugzeugbau der Universität, Stuttgart, 2008. 2008, doi:10.18419/opus-3764.