Elektrischer Stellantrieb (Stellventil)
Elektrische Stellantriebe für Regelarmaturen, auch Stellventile genannt, sind eine Variante der Stellantriebe für Regelarmaturen. Eine Versorgung mit Druckluft wird bei dieser Realisierung nicht vorausgesetzt.
Elektrische Stellantriebe
Elektrische Stellantriebe kommen nicht nur für Regelarmaturen, also für Stellventile, zum Einsatz. Sie sind bei Armaturen wie Ventile, Schieber und Klappen allgemein eine Art der Stellantriebe; je nach Art der Hilfsenergie können elektrische, pneumatische und hydraulische Stellantriebe und Kombinationen davon unterschieden werden. Elektrische Antriebe lassen sich nicht nur für Bewegungsvorgänge nutzen, sondern auch als Stellantriebe. Diese sind in einem technischen System nötig für die automatische Regelung und Steuerung des Zuflusses von Flüssigkeiten, Gasen oder Feststoffen. Die elektrischen Stellantriebe für Armaturen benutzen einen Elektromotor und ermöglichen zudem einen manuellen Antrieb über ein Handrad.
Elektrische Antriebe für Regelarmaturen
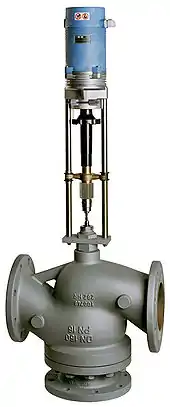
Kontinuierliche elektrische Antriebe für Regelarmaturen betätigen Stellventile elektrisch. Innerhalb einer Automatisierungskette haben Regelarmaturen (Stellventile) die Aufgabe, Stoffströme so zu konditionieren, dass ein optimaler Gesamt-Prozesswirkungsgrad erreicht wird. Ihre Betätigung kann durch pneumatische, hydraulische oder elektrische Antriebe erfolgen. Aufgrund der einfacheren Installation und der geringeren erforderlichen Geräteinfrastruktur erhalten elektrische Antriebe vielfach den Vorzug.
Die Anforderungen des zu regelnden Prozesses an das Stellglied sind vielfältig. Unterschiedliche Schwerpunkte sind für die Auswahl relevant. Diese können z. B. sein:
- Investitionskosten für die Geräte
- Prozessausfallkosten bei Defekt einer Komponente
- Regelgüte
- Standzeit
- Wartungsaufwand
Regelantriebe für geringe bis mittlere Anforderungen
Für diese Applikationen kommen häufig Antriebe zur Anwendung, welche im Aussetzbetrieb arbeiten. Im ausgeregelten Zustand ist der Motor abgeschaltet und das Stellglied wird entweder durch eine Bremse oder die Selbsthemmung von Antrieb und / oder Getriebe gegen die Prozesskraft in der aktuellen Position gehalten. Erfordert der Prozess eine Änderung des Volumen- oder Massenstroms startet der Motor mit maximalem Moment und bewegt das Stellglied. Sobald die Abweichung von gewünschtem Volumen- oder Massenstrom und gemessenem Volumen- oder Massenstrom ausreichend gering ist (der Regler ist dann in der „toten Zone“), schaltet der Motor ab.
Konstruktiv kann eine solche Antriebseinheit modular aus einem Drehantrieb mit einer Zusatzbaugruppe bestehen, welche die Mehrfach-Drehbewegung des Antriebs in lineare oder schwenkende (teil-rotatorische) Bewegung umsetzt.[1] Als Getriebekomponenten kommen häufig Schneckengetriebe vorwiegend mit Fett- aber auch mit Ölschmierung zur Anwendung. Auch kompakte Geräte mit integriertem Getriebe sind möglich, bei denen am Ausgang bereits die vom Stellglied vorgegebene Bewegungsrichtung (linear oder schwenkend) bereitgestellt wird. Zum Schutz von Antrieb und Armatur sind üblicherweise Schutz- oder Überwachungsbaugruppen wie Drehmoment-, Weg- oder Thermoschalter erforderlich. Sie schalten den Motor ab sobald sich ein unzulässiger Betriebszustand einstellt (z. B. Temperatur zu hoch; Stellglied blockiert).
Solch eine Anordnung bietet für den Großteil von Prozessen und den eingangs definierten Anforderungen eine gute, zuverlässige und preiswerte Lösung. Ihre Grenzen erreicht sie jedoch wenn es aufgrund der Prozessdynamik (häufig und schnell wechselnder Prozess Ist- oder Sollwert bei gleichzeitig geforderter hoher Regelgüte) zu einer hohen Schaltspielzahl des Motors kommt. Diese kann bis zu 1200 c/h und mehr betragen. Hohe Schaltspielzahlen und die daraus resultierenden Lastspitzen können zur Beschädigung oder Zerstörung von Antriebskomponenten und damit zum Ausfall des Stellgliedes führen. Eine mögliche Reduzierung der Lastspielzahl durch Vergrößerung der toten Zone des Prozessreglers würde andererseits Einbußen in der Prozessperfomance mit sich bringen.
Kontinuierliche Regelantriebe für dynamische, hochgenaue Regelkreise
Um auch für hochdynamische Regelkreise eine hohe Regelgenauigkeit bei gleichzeitig hoher Standzeit zu gewährleisten, entwickelten renommierte Hersteller elektrische Regelantriebe für die kontinuierliche Positionierung.[2][3]
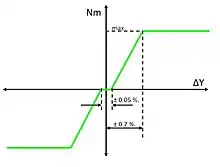
Deren wesentliches Alleinstellungsmerkmal ist die Betriebsart. Anders als bei den eingangs beschriebenen Arbeitsprinzipien ist der Motor permanent eingeschaltet (Einschaltdauer = 100 %). Das heißt jedoch nicht zwangsläufig, das er eine Drehbewegung erzeugt. Im ausgeregelten Zustand entwickelt er gerade soviel Drehmoment wie erforderlich ist um das Stellglied gegen die etwaig anstehende Prozesskraft in der Position zu halten. Antriebskräfte auf der einen Seite und Rückstellkräfte aus dem Prozess bilden dann ein sensibles Gleichgewicht. Erfordert der Prozess eine Änderung des Massen- oder Volumenstroms, erhöht oder reduziert der Motor sein Moment sanft und proportional zur gewachsenen Abweichung zwischen Positionssoll- und Istwert solange, bis sich im überlagerten Prozessregelkreis die gewünschte Prozessgröße eingestellt hat.
Dieses Verhalten, bei dem keine schlagartigen (Momenten) Lastspitzen auftreten, leistet so einen wesentlichen Beitrag zur Materialschonung und damit zur Verlängerung der Standzeit des Regelantriebs. Bezogen auf den gesamten Prozess arbeitet der Positionierregelkreis als ein dem Prozessregelkreis unterlagerter Regelkreis mit P-Verhalten.
Kontinuierliche Regelantriebe für Schwenkbewegung
Ein 3-Phasen Asynchronmotor wirkt über ein Differentialgetriebe auf das eigentliche Antriebsgetriebe. Dies ist in der Regel als kugelgelagertes Stirnradgetriebe ausgelegt, welches in einem Ölbad läuft und so ein hohes Maß an Leichtgängigkeit gewährleistet. Es wandelt die eingehende Mehrfachdrehbewegung des Motors unter Erhöhung des Drehmomentes in eine ausgangsseitige Schwenkbewegung. Ein Sensor auf der Rückseite der Antriebswelle erfasst die aktuelle Antriebsposition und überträgt diese als Strom- oder Spannungswert an die Ansteuerelektronik.
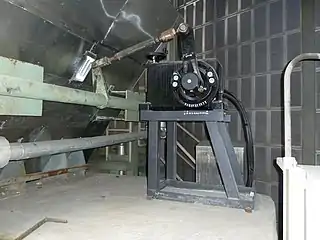
Das austretende Wellenende hat einen Arbeitsbereich von bis zu 120° (entsprechend 100 %) und kann, z. B. bei Verbindung mit Kugelhähnen, direkt mit dem Stellglied, z. B. über eine Buchsen–Paßfederverbindung, gekuppelt werden. Bei Klappenanwendungen ist es über einen Hebel und ein Anlenkgestänge mit dem Stellglied verbunden. Dieser Aufbau ermöglicht durch Wahl der geeigneten Winkel in der Gestängeverbindung eine positionabhängige Erhöhung des an der Klappe wirksamen Momentes. Darüber hinaus bewirkt es auch eine thermische Entkopplung von Antrieb und Stellglied.
Konstruktionsbedingt weisen diese Antriebe eine äußerst geringe, interne Reibung ohne jegliche Selbsthemmung auf. Die auf das Stellglied wirkenden Prozesskräfte würden demzufolge bei Ausfall der Spannungsversorgung für den Motor das Stellglied in eine Endlage bewegen. Um dem entgegen zu wirken sind die Motoren mit einer Bremse ausgerüstet, welche nach dem Ruhestromprinzip arbeitet. Im normalen Betrieb stehen Motor und Bremsmagnet unter Spannung. Der Magnet hält die Bremse gegen eine Feder mechanisch gelöst. Bei Wegfall der Versorgungsspannung ist der Magnet wirkungslos und die Feder lässt die Bremse mechanisch einfallen. Das Stellglied wird in der aktuellen Position gehalten. Da dieser Vorgang nur bei Ausfall oder gezieltem Abschalten der Spannung auftritt, ist ein wartungsrelevanter Reibverschleiß zu vernachlässigen.
Neben dem Motor wirkt eingangsseitig auch ein Handrad auf das Differentialgetriebe. Nach dessen Entriegelung und eingefallener Bremse kann hierüber der Antrieb im Bedarfsfall manuell bewegt werden.
Kontinuierliche Regelantriebe für Linearbewegung
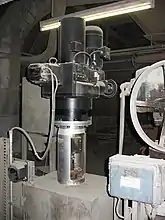
Während Schwenkantriebe vorwiegend bei Stellgliedern mit teil-rotatorischer Bewegung Verwendung finden, erfordern linear arbeitende Regelventile geeignete Linearantriebe. Da die Anforderungen hinsichtlich Ansprechempfindlichkeit, Standzeit, Leichtgängigkeit und Robustheit in hochdynamischen Regelkreisen auch für diese Bauart zutreffen, entsprechen sie in ihrer grundsätzlichen Arbeitsweise und ihren wesentlichen Konstruktionselementen den Ausführungen für Schwenkbewegung. Abweichend hiervon jedoch muss nun eine lineare Arbeitsbewegung erzeugt werden. Der 3-Phasen Asynchronmotor wirkt daher über das bekannte Differentialgetriebe auf einen im Ölbad laufenden Kugelgewindetrieb. Das Ausgangszahnrad dieses Differentialgetriebes wirkt dabei auf eine axial gefesselte Mutter, welche sich auf einer wiederum radial gefesselten Spindel bewegt. Dies erzeugt bei eingehender Motordrehbewegung eine lineare Bewegung der Gewindespindel. Deren ausgehendes Ende wird mit der Ventilspindel gekoppelt.
Bei kritischen Applikationen, z. B. Heissdampf-Regelventilen in Kraftwerken, kann es zu einer thermisch bedingten Längenänderung von Ventilspindel und Antriebsspindel kommen. Um diese zu kompensieren ist der gesamte Spindeltrieb bei Linearantrieben einiger Hersteller „schwimmend“ in einem Federpaket aufgehängt.
Ansteuerelektronik
Unabhängig von der Bewegungsrichtung des kontinuierlichen, elektrischen Regelantriebs sind die Anforderungen von kontinuierlichen Schwenk- oder Linearantrieben an die Ansteuerelektronik identisch. Leistungsseitig arbeitet die Elektronik als Frequenzumrichter mit Pulsweitenmodulation. Diese erlaubt eine weite Bandbreite in der Varianz von Antriebsgeschwindigkeit und / oder Antriebskraft /-moment ohne Notwendigkeit einer Hardwareänderung (Getriebeübersetzung).
Die Leistungsversorgung erfolgt aus dem 115V/230V 1-Phasen Netz. Eine jeweils antriebsspezifische Software in der Elektronik überwacht und begrenzt bei Bedarf die Stromaufnahme des Motors und gewährleistet so eine der Kernfunktionen: die Blockierfestigkeit des Antriebsmotors auch bei max. Drehmoment und Drehzahl „0“ ohne zeitliche Begrenzung. Eine gesonderte thermische oder drehomentabhängige Überwachung und demzufolge zusätzliche Bauelemente als mögliche Fehlerquellen sind nicht erforderlich.
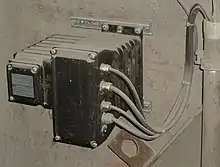
Die Elektronik erhält vom überlagerten Prozessregler eine Vorgabe für die aktuell optimale Stellgliedposition (Stellungs-Sollwert); abhängig von der technischen Ausführung entweder als Analogwert (4…20 mA) oder als Digitalwert bei Feldbus Kommunikation. Die Elektronik Software vergleicht diese permanent mit der momentanen Stellgliedposition (Stellungs-Istwert). Abhängig vom Ergebnis wird der Antrieb nun das Stellglied in die neue Position bewegen oder er hält es bei eingeschaltetem (aber nicht drehendem) Motor in der momentanen Position.
Zahlreiche weitere Softwarefunktionen ermöglichen eine individuelle Anpassung der Antriebsfunktionen an den Prozess. Der Umfang ist abhängig vom Hersteller unterschiedlich – daher nachfolgend eine allgemeine Übersicht:
- Reduzierung von Moment / Kraft und Geschwindigkeit
- Alarmmeldungen
- Fehlerprotokolle
- Signalsimulationen
- Individuelles Endlagenverhalten
- Verhalten im Fehlerfall
Darüber hinaus bieten die Geräte einiger Hersteller auch ein Wartungsmanagement. Hierbei werden die wartungs- und lebensdauerrelevanten Parameter wie z. B. Temperatur, Lastspitzen, Lastverteilung, Anzahl der Motor Drehrichtungswechsel etc. am Antrieb erfasst und in einem Algorithmus der Elektronik Software ausgewertet. Der Anlagenbetreiber erhält so die Möglichkeit eventuell erforderliche Wartungsarbeiten belastungsabhängig zu planen und einen unnötigen Anlagenstillstand aufgrund pauschaler Wartungsintervalle zu vermeiden.
Bestandteil der Elektronik ist in der Regel auch ein lokales Bedienfeld. Neben der Möglichkeit Grundfunktionen des Antriebs von dort über Tastbefehle aufzurufen kann es auch eine Kommunikationsschnittstelle mit üblichem Industriestandard umfassen. Hier lässt sich ein PC oder Notebook anschließen um mittels einer grafischen Bedienoberfläche Parameter darzustellen, auszulesen oder zu ändern.
Die Elektronik kann entweder Bestandteil des Regelantriebs sein (integriert) oder sie wird separat installiert. Die Auswahl der Installationsart ist applikationsabhängig. Erlauben integrierte Elektroniken in der Regel eine kompaktere Bauform und preislich günstigere Lösung, bietet die separate Installation Vorteile bei der Zugänglichkeit in engen und rauen Umgebungsbedingungen. Auch bei thermisch kritischen Bedingungen am Einbauort des Stellgliedes wirkt sich die hiervon abgesetzte Installation vorteilhaft auf die Lebensdauer der Elektronik aus.
Einzelnachweise
- Elektrische Stellantriebe – Automatisierung von Industriearmaturen
- ABB: Technische Beschreibung TD/ACTUATOR/001-DE (Intelligente elektrische Antriebe für die Prozessautomatisierung)
- ROTORK – Established Leaders in Valve actuation