Dickenmessverfahren
Dickenmessverfahren spielen in der Fertigung und Materialprüfung eine große Rolle, insbesondere wenn es sich um zerstörungsfreie Verfahren handelt.
Es gibt offline-Dickenmessverfahren, die manuell und nicht in der Produktionslinie angewendet werden. Die Dickenmessung einer Beschichtung, eines Drahtes, einer Folie oder eines Bandes kann offline berührend, aber zerstörungslos durch taktiles Messen (Messschraube, Messschieber, Ultraschall) oder zerstörend durch Untersuchung eines Querschliffes mit einem Messmikroskop (Objektmikrometer oder Messokular) geschehen.
Industrielle Dickenmessverfahren, also die automatische Messung direkt in der Produktionslinie, werden als inline-Messverfahren bezeichnet.
Eine Drahtdickenmessung kann optisch (Abschattung eines Lichtfächers auf einer CCD-Zeile), mikroskopisch oder mechanisch (Messschieber) erfolgen.
Oft ist die Bestimmung der Schichtdicke auf einem Draht (z. B. Isolierschicht auf Kupferlackdraht) nötig, sie kann kapazitiv erfolgen oder, indem eine durch den laufenden Draht abtransportierte Ladungsmenge bestimmt wird.
Verfahren zur Inlinemessung von Blechen und Bändern
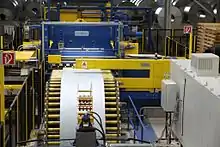
Bei der industriellen Produktion sollen mittels Dickenmessung Abweichungen von der Solldicke aussortiert und ausgeregelt werden. Kriterien sind Dicke in der Bandmitte in Längsrichtung und auch das Querprofil.
Bei der Herstellung von Metallband (Coils) unterscheidet man zwischen den Prozesslinien Querteilanlage (das Band wird quer in Blechtafeln zerschnitten) und Längsteilanlage (das Band wird längs in Streifen geschnitten).
Bei Längsteilanlagen werden die Querprofile der Bänder aus Platz- und Bandberuhigungsgründen auch bereits vor der Längsteilschere gemessen. Zur Kontrolle aller Bandstreifen muss die Blechdicke im kompletten Querprofil gemessen werden. Dabei können die Messwerte den späteren Streifen mit unterschiedlichsten Breiten zugeordnet werden. Die Querprofildickenmessung deckt Bandbreiten bis zu vier Meter quer zum Materialfluss ab. Während bei einer Bandmitten-Dickenmessung die Sensorik üblicherweise mit einem C-Rahmen im Messort gehalten wird, wird die verfahrbare Sensorik bei einer traversierenden Messspur z. B. aus Platzgründen von einem statischen O-Rahmen getragen. Die Dickenprofile längs und quer der Spaltbänder werden ermittelt und für jedes Coil einzeln dokumentiert. Somit ist auch die Längsposition von detektierten Toleranzverletzungen für jeden Streifen bekannt. Diese nahtlose Qualitätsdokumentation erlaubt es, die Produkte auftrags- und kundenspezifisch zu selektieren.
Motivation zur 100 %-Kontrolle der Banddicke ist den heutigen Qualitätsanforderungen von automobilen Endkunden sowie einer Messsystemanalyse (MSA) nach der ISO/TS 16949 zu genügen.
Taktile Dickenmessung
Die taktile Dickenmessung besteht aus zwei Messtastern, die senkrecht von der Ober- und der Unterseite kollinear das Messgut gleitend abtasten. Mit einer Referenzierung wird zuvor der Abstand der beiden Taster zueinander ermittelt.
Das Messverfahren ist rückführbar.
Zu den Nachteilen zählen die Beeinflussung empfindlichen Messguts und Verschleiß der Tasterköpfe. Diese führten zu Entwicklung berührungsloser Messverfahren.
Radiometrische Dickenmessung
Die radiometrische Dickenmessung erfolgt kontinuierlich und berührungslos. Es wird zwischen Messverfahren mit radioaktiven Isotopenstrahlern oder Röntgenstrahlern als Quelle unterschieden. Ferner wird zwischen radiometrischer Dickenmessung im Durchstrahlverfahren (Quelle und Detektor auf gegenüberliegenden Seiten des Messguts) und Rückstreuverfahren (Quelle und Detektor auf der gleichen Seite des Messguts) unterschieden.[1]
Die Messmethoden sind in der Industrie spätestens seit der Verfügbarkeit neuer Isotopenquellen in den 50er Jahren etabliert und verbreitet. Sie sind unempfindlich gegen äußere Temperaturveränderungen. Allerdings beeinflussen Änderungen des Materials oder der Legierung den Messwert ähnlich wie Dickenänderungen. Bei β- und γ-Strahlern weicht zudem die Absorption bei starken Dickenänderungen deutlich vom exponentiellen Gesetz ab.[2] Daher ist eine Kalibrierung speziell für das zu messende Target erforderlich (Legierung, Dicke). Die mit solchen Systemen erreichten Messgenauigkeiten liegen bei stabiler Legierung unter 1 Mikrometer Abweichung.
Die Anwendung der radiometrischen Dickenmessung bringt erhöhte Anforderung an den Strahlungsschutz mit sich.[3]
Optische Dickenmessung
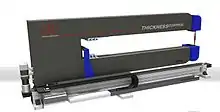
Die optische Dickenmessung erfolgt entsprechend der taktilen Dickenmessung mit zwei Abstands-Sensoren, die von der Ober- und der Unterseite – kollinear angeordnet – den Abstand zum Band-Material messen. Mit einer Referenzierung wird iterativ (z. B. jeweils zu Beginn einer Messung) der Abstand der beiden Sensoren zueinander ermittelt. Die industriell eingesetzten Abstandssensoren messen berührungslos häufig nach dem Prinzip der Lasertriangulation.[4]
Die Messung erfolgt zeitlich diskret mit Messraten von typischerweise einigen 10 kHz.
Andere physikalische Verfahren wie konfokale Sensorik kommen u. a. aufgrund steigender Anforderungen (spiegelnde Oberflächen, höhere Genauigkeiten etc.) zunehmend zum Einsatz.
Die bei der Dickenmessung zum Einsatz kommenden Triangulationssensoren sind, je nach Anwendungsschwerpunkt, mit Laserpunkt, optisch verlängertem Laserpunkt oder diskreter Laserlinie (mit vielen Lasermesspunkten gleichzeitig) ausgeführt. Die diskrete Laserlinie ermöglicht zusätzlich eine Messung von Verkippungswinkeln in Linienrichtung und deren vollständige Kompensation.
Allen Triangulationssensoren gemeinsam ist ein fest definierter Messbereich für den oberen und den unteren Sensor und die mit dem Messbereich proportional skalierende Messunsicherheit. Auch gibt es Triangulationssensoren (Laserlinie), welche durch selektive Deaktivierung von Pixel-Zeilen im Bildsensor, neben einem maximalen Messbereich, auch kleinere Messbereiche in einem Triangulationssensor beinhalten. Die Eingrenzung des genutzten Bildsensorbereichs erlaubt eine höhere Messfrequenz, die bei der Laserlinientechnik naturgemäß niedriger liegt, als bei Laserpunkt-Sensoren mit typischerweise nur einer genutzten Pixel-Zeile.
In die Messgenauigkeit eines Dickenmesssystems fließen die voneinander unabhängigen Messfehler beider Triangulationssensoren ein. Die Richtigkeit oder Linearität eines Lasertriangulationssensors auf einfache (matte) Oberflächen ist in der Praxis bei Punktlasern nicht besser, als 0,01 % des Messbereichs, bei Linienlasern nicht besser als 0,1 % (z. B. für ±2 mm Messbereich: ±2µm bei 2 Sigma). Allerdings erhält man bei Linienlasertechnik mehr als 1000 Messpunkte gleichzeitig. Sie ist daher unabhängiger von optisch schwierigen (glänzenden) Oberflächen oder Verkippungen, die erkannt, gemessen und kompensiert werden.
Durch gleitende Mittelung in Materialtransportrichtung (typ. wenige Millimeter) wird eine hohe Präzision der Dickenwerte erreicht. Die von vielen Herstellern angegebene Auflösung hingegen sagt praktisch nichts über die Messgenauigkeit aus.
Die Dickenmessung mittels Lasertriangulation ist rückführbar. Der Bediener ist jederzeit in der Lage, einen Messmittelfähigkeitsnachweis durchzuführen (Audit).
Im Vergleich zur radiometrischen Dickenmessung besitzt die optische Dickenmessung eine hohe Ortsauflösung und im Verhältnis zu taktiler Dickenmessung ist eine schnelle Reaktion auf Dickenänderungen möglich. Die optische Dickenmessung ermöglicht mit diesen Vorteilen das Herangehen an spezielle Messaufgaben, die mit taktilen Messsystem, Isotopen und Radiometern nicht realisierbar sind. Dazu gehört z. B. die dynamische Walzenregelung, die Messung von Riffelblechen (Dicke des Grundbleches und die Riffelhöhe) oder Dicken von „Sandwichblechen“ aus inhomogenem Material (Strukturen aus Aluminium mit Luftanteil, Aufbau ähnlich Wellpappe).
Die optische Dickenmessung arbeitet unbeeinflusst von der Materiallegierung.
Der Wartungsaufwand der optischen Dickenmessung ist gering. Verschleiß gibt es bei dem Messprinzip praktisch nicht. Die Lebensdauer der verwendeten Laserdioden mit Leistungen im unteren Milliwatt-Bereich liegt bei typischerweise > 40.000 h.[5]
Bei höchsten Genauigkeitsanforderungen müssen Temperaturschwankungen der Messtechnik kompensiert oder verhindert werden. Ein Ansatz zur Kompensation von Fehlern (z. B. durch Temperaturänderungen) ist die regelmäßige (möglichst automatische) Referenzierung, sowohl vor Beginn als auch iterativ während der Messungen.
Andere physikalische Verfahren zur berührungslosen Dickenmessung
Generell sind auch kapazitive Sensoren möglich (hohe Genauigkeiten, aber empfindlich gegenüber Emulsion oder Öl). Hier ist jedoch der physikalische Messspalt nur in etwas so groß wie der Messbereich.
Wirbelstromsensoren können bei statischen Messungen eingesetzt werden, jedoch nicht auf ferritischem, vorbeilaufendem Material. Diese Sensoren sind stabiler gegen Umwelteinflüsse wie Öl oder Emulsion.
Eine zerstörungs- und verschleissfreie Dickenmessung einer isolierenden Schicht auf beliebigen Metallen oder CFK-Verbundwerkstoffen ist mittels Mikrowellenprüfung möglich.
Literatur
- Walter Wegener, Heinz Bechlenberg: Vergleichende Untersuchungen an Meßvorrichtungen zur fortlaufenden Ermittlung der Materialungleichmäßigkeit. Springer Fachmedien Wiesbaden GmbH, Wiesbaden 1970.
- Siegfried Methfessel: Dünne Schichten, ihre Herstellung und Messung. W. Knapp, 1953.
Siehe auch
Weblinks
- Patent EP0324896B1: Dickenmessverfahren. Angemeldet am 10. Oktober 1988, veröffentlicht am 30. Dezember 1992, Anmelder: Mitsubishi Denki Kabushiki Kaisha, Erfinder: Makoto Tokumaru et al.
- Bedampfen im Hochvakuum und Schichtdickenmessung (abgerufen am 15. Oktober 2015)
Einzelnachweise
- Werner Stolz: Radioaktivität – Springer. doi:10.1007/978-3-663-01497-3 (springer.com [abgerufen am 5. September 2016]).
- L. G. Erwall, H. G. Forsberg, K. Ljunggren: Radioaktive Isotope in der Technik – Springer. doi:10.1007/978-3-663-02872-7 (springer.com [abgerufen am 5. September 2016]).
- Strahlenschutzverordnung - StrlSchV
- Bela G. Liptak: Instrument Engineers’ Handbook Process Measurement and Analysis. 4th Edition Auflage. CRC Press, 2003, ISBN 978-0-8493-1083-6, S. 1049.
- Dirk Jansen: Optoelektronik – Springer. doi:10.1007/978-3-663-05975-2 (springer.com [abgerufen am 5. September 2016]).