Highly Accelerated Life Test
Ein Highly Accelerated Life Test (abgekürzt HALT, englisch für stark beschleunigte Grenzlastprüfung) ist ein qualitatives Testverfahren mit dem Ziel, vorzugsweise elektronische und elektromechanische Baugruppen noch im Entwicklungsstadium einer beschleunigten Alterung auszusetzen, um Schwachstellen und Designfehler aufdecken zu können. Die dabei gewonnenen Erkenntnisse fließen in das Gerätedesign und den Produktionsprozess ein, wodurch die Robustheit und damit die Zuverlässigkeit des Produktes verbessert werden. Das Verfahren wird seit den 1980er Jahren angewandt.
Geschichte
Das HALT-Verfahren hat seinen Ursprung im Environmental Stress Screening (ESS) aus den 1960er-Jahren. Die Weiterentwicklung zu einem Testverfahren, bei dem mit Belastungen oberhalb der Produktspezifikation getestet wird, stieß anfangs auf Ablehnung und stellte einen Paradigmenwechsel dar. In der folgenden Zeit wurden verschiedene Testverfahren, die diesem Prinzip folgten, wie der Stress for Life (STRIFE) oder der Accelerated Stress Test (AST), beschrieben und angewandt. Um sich von anderen Verfahren zu differenzieren, kreierten Gregg K. Hobbs und seine Frau Virginia im Jahr 1988 den Begriff Highly Accelerated Life Test und dessen Akronym HALT.[1] Hobbs hatte zuvor über Jahre an der Entwicklung dieses Verfahrens und des dazu benötigten Equipments gearbeitet. Heute wird das HALT-Verfahren vorwiegend von amerikanischen Firmen dazu eingesetzt, die Zuverlässigkeit von Produkten zu verbessern.[2] Im Weiteren hat es sich in verschiedene Standards und Normen wie der IPC9592A[3][4] oder der DIN EN 62506:2014-03[5] etabliert.
Zielsetzung
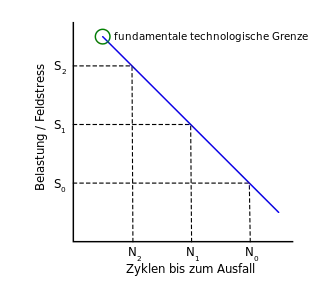
Die Zielsetzung eines HALT ist in erster Linie das Aufdecken von Schwachstellen im Gerätedesign und Herstellungsprozess innerhalb kürzester Zeit und mittels einer kleinen Anzahl von Prototypen. Dies wird mittels einer extremen Beschleunigung des Alterungs- und Schädigungsprozesses durch Belastung mit Temperatur, Vibration und schnellen Temperaturwechseln erreicht. Hierdurch treten Ausfälle frühzeitig auf. Jede so aufgedeckte Schwachstelle bietet die Möglichkeit, das Gerätedesign oder den Produktionsprozess zu verbessern. Infolge der Verbesserungsmaßnahmen wird die Robustheit des Produktes erhöht und somit dessen Zuverlässigkeit. Des Weiteren werden durch den HALT die Entwicklungszeit verkürzt und letztlich die Kosten gesenkt.[6]
Grundgedanke
Der Grundgedanke des HALT beruht auf der Annahme, dass die im HALT auftretenden Fehlerbilder und Ausfallarten die Gleichen sind, wie sie später in der erwarteten Lebensdauer des Produktes beobachtet werden. Zudem wird von der Voraussetzung ausgegangen, dass Belastungen zyklisch auftreten; zum Beispiel ist die Umgebungstemperatur im Freien tagsüber höher als nachts. Der dabei angenommene Zusammenhang von der Anzahl der Belastungszyklen bis zum Ausfall im Feld ist schematisch in der Abbildung 1 dargestellt. Die Zyklenzahl und die Belastung nehmen in der Darstellung vom Koordinatenursprung aus zu. Unter Einfluss des Feldstresses S0 fällt ein Produkt nach der Zyklenzahl N0 aus. Beim HALT wird die Belastung beispielsweise auf S2 erhöht, um die Anzahl der Zyklen bis zum Ausfall auf N2 zu senken und somit eine Beschleunigung der Alterung zu erreichen. Dieser Sachverhalt gilt für alle Komponenten eines Produktes, es gibt unter Umständen Unterschiede in der Steigung, zudem ist der Zusammenhang oft nichtlinear. Dies ändert jedoch nichts an dieser Grundannahme für das Produkt. Der Belastungsstress kann wiederum nicht ins Unendliche gesteigert werden, ohne den Fehlermechanismus zu ändern. Dieser Punkt wird fundamentale technologische Grenze genannt.[7]
Equipment
Parameter | Größe |
---|---|
Temperaturbereich | −100 … +200 °C |
Heizgeschwindigkeit | max. 70 K/min |
Kühlgeschwindigkeit | max. 70 K/min |
Tischabmessungen | 915 mm × 915 mm |
Vibrationsbandbreite (fest) | 5 … 10.000 Hz |
Vibrationsbandbreite | 2 … 60 Grms |
Kammerabmessung (B×H×T) | 122 cm × 106,5 cm × 129,5 cm |
Für einen HALT-Test werden spezielle HALT-Kammern verwendet, in denen der Prüfling auf einen Vibrationstisch fixiert werden kann. Der Prüftisch kann mittels druckluftbetriebener Hämmer in sechs Freiheitsgraden nach dem Zufallsprinzip angeregt werden. Die Belastungsenergie der so erzeugten Vibrationen wird in Grms angegeben.[9] Die Kammern haben einen Temperaturbereich von −100 °C bis +200 °C, mit möglichen Temperaturgradienten von bis zu 80 K/min. Dies wird mit starken elektrischen Heizelementen und einer Stickstoffkühlung erreicht. Damit die thermische Energie möglichst effektiv auf den Prüfling einwirken kann, wird sie mittels Luftleitschläuchen geleitet. In der Tabelle 1 sind typische technische Parameter einer HALT-Kammer angegeben.
Prüflinge
Die Prüflinge, die im HALT verwendet werden sollen, müssen vor dem Test so vorbereitet werden, dass deren Betrieb und Funktionsüberwachung von außerhalb der HALT-Kammer möglich ist. Zusätzlich können Temperatur- und Beschleunigungssensoren an den verwendeten Prototypen angebracht werden, um den einwirkenden Belastungsstress dokumentieren zu können. In den Prüflingen implementierte Schutzmechanismen müssen für den HALT ggf. außer Funktion gesetzt werden, weil sich ansonsten die Prüflinge selber schützen und Fehlerbilder nicht angeregt werden können.
Vorgehensweise
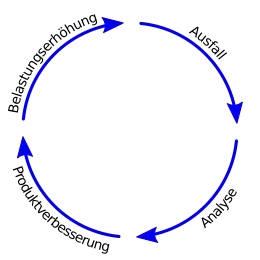
Im Folgenden wird das Vorgehen und die einzelnen Prüfungen beim HALT beschrieben. Die gesamte Vorgehensweise und auftretende Ereignisse während der Durchführung der einzelnen Prüfschritte müssen sorgfältig dokumentiert werden. Während der Tests auftretende Schäden am Prüfling müssen einer präzisen Fehleranalyse unterzogen werden und Verbesserungsmaßnahmen am Produkt zur Folge haben. Danach können die Beschädigungen behoben werden, so dass der Test mit dem entsprechenden Prüfling fortgeführt werden kann. Ein Defekt ist kein Beendigungskriterium, sondern stellt ein gewünschtes Zwischenergebnis dar. Ein HALT ist wie in Abbildung 2 dargestellt ein 360°-Prozess der im Idealfall bis zu den fundamentalen technologischen Grenzen durchgeführt wird.[10]
Kältestufenprüfung
Der HALT wird mit der Kältestufenprüfung begonnen, weil diese sich gewöhnlich am wenigsten zerstörend auf den Prüfling auswirkt. Begonnen wird bei einer Umgebungstemperatur von 20 °C, die in 10 K-Schritten herabgesetzt wird, bis die untere Betriebsbelastungsgrenze (Lower Operating Limit) für die Temperatur erreicht wird. Danach wird die untere Zerstörungsgrenze (Lower Destruct Limit) bestimmt, wenn dies möglich ist. Die jeweilige Verweilzeit in jeder Stufe beträgt ungefähr 10 Minuten. Diese Zeit wird benötigt, damit sich der Prüfling thermisch einschwingt und die Funktion überprüft werden kann.[11][12]
Wärmestufenprüfung
Die Wärmestufenprüfung wird bei 20 °C Umgebungstemperatur begonnen, die in 10 K-Schritten erhöht wird, bis die obere Betriebsbelastungsgrenze (Upper Operating Limit) der Temperatur erreicht wird. Danach wird die obere Zerstörungsgrenze (Upper Destruct Limit) bestimmt, wenn dies möglich ist. Die jeweilige Verweilzeit in jeder Stufe beträgt ungefähr 10 Minuten. Diese Zeit wird benötigt, damit sich der Prüfling thermisch einschwingt und die Funktion überprüft werden kann.[11][12]
Temperaturwechselprüfung
Bei der Temperaturwechselprüfung wird zyklisch mit der maximal möglichen Heiz- und Kühlleistung zwischen zwei Ecktemperaturen hin- und hergefahren. Die Ecktemperaturen, die in dieser Prüfung verwendet werden, orientieren sich an den ermittelten Betriebsbelastungsgrenzen (Lower- and Upper Operating Limit) der Temperaturstufen-Prüfungen. Es werden mindestens fünf Zyklen durchfahren. Der Prüfling muss hierbei permanent überwacht und auf Funktion überprüft werden. Zusätzlich kann bei den Ecktemperaturen der Prüfling ab- und angeschaltet werden, um weiteren Stress zu erzeugen. Die Verweilzeit bei dieser Prüfung beträgt ebenfalls ungefähr 10 Minuten bei der jeweiligen Temperatur.[11][13]
Vibrationsprüfung
Die Vibrationsprüfung beginnt bei circa 5 Grms und wird pro Schritt um 5 Grms erhöht, bis die Betriebsbelastungs- und Zerstörungsgrenze erreicht wird. Die Funktion des Prüflings muss während der ganzen Prüfung überwacht werden, zusätzlich wird über einen Beschleunigungssensor der einwirkende Vibrationsstress festgehalten. Die Haltezeit beträgt in jeder Stufe circa 10 Minuten. Wird ein Vibrationslevel von 30 Grms und höher erreicht, ohne dass ein Fehlerbild aufgetreten ist, sollte die Funktion des Prüflings nochmals bei niedrigeren Stressleveln geprüft werden. Es besteht die Möglichkeit, dass Fehlerbilder, die durch hohe Vibrationslevel verursacht werden, nur bei geringeren Vibrationsleveln detektiert werden können.[11][14]
Kombinierte Stressprüfung
Nachdem die einzelnen Stressprüfungen abgeschlossen sind, kann die kombinierte Stressprüfung, die sich aus der Überlagerung der Temperaturwechsel- und Vibrationsprüfung zusammensetzt, durchgeführt werden. Bei diesem kombinierten Test wird das Temperaturprofil der Temperaturwechselprüfung verwendet. Für die Vibrationsstufen wird der Wert der Zerstörungsgrenze aus dem Vibrationstest geteilt durch fünf Zyklen angewandt. Die Wichtigkeit dieser kombinierten Stressprüfung liegt darin begründet, dass sich mit der Änderung der Temperatur das Vibrationsverhalten vieler Produkte ändert. Hierdurch treten bei dieser Stressprüfung andere Fehlerbilder als bei den Einzeltests auf.[11][15]
Testergebnis und Ende
Ein HALT liefert die folgenden Kenngrößen, bezogen auf die thermischen und mechanischen Belastungen in den einzelnen Prüfungen, für ein Produkt:
- Untere Betriebsbelastungsgrenze (Lower Operating Limit)
- Obere Betriebsbelastungsgrenze (Upper Operating Limit)
- Untere Zerstörungsgrenze (Lower Destruct Limit)
- Obere Zerstörungsgrenze (Upper Destruct Limit)
- Fundamentale technologische Grenzen (Fundamental Limit of Technology)
Die Betriebsbelastungs- und Zerstörungsgrenzen mit den dazugehörigen Margen auf die Entwurfspezifikation sind schematisch in der Abbildung 3 dargestellt. Es ist nicht immer möglich, alle Grenzen bei einer der Prüfung zu ermitteln. In so einem Fall muss die Prüfzeit so bemessen sein, dass eventuell vorhandene Schwachstellen hätten ersichtlich werden müssen.
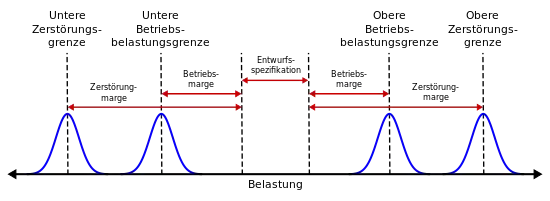
Die während des HALT aufgetretenen Fehlerbilder und Beschädigungen werden dokumentiert und analysiert. Die gewonnenen Erkenntnisse fließen als Verbesserungen in das Produktdesign und den Herstellungsprozess ein, so dass am Ende die Robustheit des Produktes verbessert, die Lebensdauer verlängert und die Ausfallrate gesenkt wird.
Kritik
Das HALT-Verfahren hat Nachteile und bietet aus diesem Grund Anlass für Kritik. Zum einen gibt es keine Übereinstimmung zwischen den Belastungen im Test und den später im Feld auftretenden realen Umgebungsbedingungen. Aus diesem Grund müssen im Test auftretende Fehler einer sorgfältigen und vorsichtigen Ursachenanalyse unterzogen werden. Dabei ist es wichtig zu klären, ob der aufgetretene Fehler später bei den Belastungen im Feld grundsätzlich auftreten kann oder nicht berücksichtigt werden muss. Um dies beurteilen zu können, ist Erfahrung und Fachwissen über physikalische und chemische Ausfallmechanismen und Ausfallmodelle erforderlich. Des Weiteren gibt es keine wissenschaftliche Grundlage dafür, über statistische Beschleunigungsmodelle und Testergebnisse auf die Lebensdauer des Produkts zu schließen.[16][17] Ein weiterer Nachteil ist, dass im Gegensatz zu anderen Prüfverfahren diese Prüftechnik nicht ausreichend normiert ist[18] und somit die Prüfbedingungen nicht unabhängig reproduzierbar sind.
Siehe auch
- Highly Accelerated Stress Screening (HASS) ist ein produktionsbegleitende und nichtzerstörende Zuverlässigkeitsprüfung aller gefertigten Einheiten (100 %).
Literatur
- Gregg K. Hobbs: HALT and HASS – Accelerated Reliability Engineering. Hobbs Engineering Corporation, Westminster, Colorado 2005, ISBN 0-615-12833-5.
- Harry W. McLean: HALT, HASS, and HASA Explained – Accelerated Reliability Techniques. Amer Society for Quality, 2009, ISBN 978-0-87389-766-2 (Revised Edition).
- Arno Meyna, Bernhard Pauli: Zuverlässigkeitstechnik – Quantitative Bewertungsverfahren. Carl Hanser Verlag, München 2010, ISBN 978-3-446-41966-7.
- Mark A. Levin, Ted T. Kalal: Improving Product Reliability: Strategies and Implementation. John Whiley & Sons, 2003, ISBN 0-470-85449-9.
- H. Anthony Chan: Accelerated Stress Testing Handbook: Guide for Achieving Quality Products. Whiley-IEEE Press, 2001, ISBN 0-7803-6025-7.
Weblinks
- Zuverlässigkeit erhöhen – Kosten reduzieren - In: productronic 12/2006 (deutsch) (PDF; 137 kB; abgerufen am 31. Juli 2014)
Einzelnachweise
- Gregg K. Hobbs: Editorial - The History of HALT and HASS. (PDF) In: Sound&Vibration. Oktober 2002, S. 5, abgerufen am 10. August 2014.
- Arno Meyna, Bernhard Pauli: Zuverlässigkeitstechnik - Quantitative Bewertungsverfahren. 2. Auflage. Carl Hanser Verlag, München 2010, ISBN 978-3-446-41966-7, S. 587.
- David Rahe: HALT and HASS in IPC9592A. (PDF) Qualmark & DLi Labs, abgerufen am 15. August 2014.
- IPC-9592A - Requirements for Power Conversion Devices for the Computer and Telecommunications Industries. IPC, Mai 2010, S. 25–28.
- DIN EN 62506:2013-03 - Verfahren für beschleunigte Produktprüfungen (IEC 62506:2013). Beuth Verlag GmbH, Berlin 2014, S. 15–21.
- Gregg K. Hobbs: HALT and HASS - Accelerated Reliability Engineering. Hobbs Engineering Corporation, Westminster (Colorado) 2005, S. 4.
- Mike Silvermann: How Reliable is Your Product? – 50 Ways to Improve Product Reliability. Super Star Press, Cupertino 2010, ISBN 978-1-60773-060-6, S. 177.
- HALT and HASS – Test Equipment For Highly Accelerated Life Test and Stress Screen Applications. (PDF) Weiss Umwelttechnik GmbH, 2. Juli 2011, S. 11, abgerufen am 30. Juli 2014.
- Neill Doertenbach: The Calculation of Grms. (PDF) QualMark Corp., abgerufen am 2. August 2014.
- Mike Silvermann: How Reliable is Your Product? – 50 Ways to Improve Product Reliability. Super Star Press, Cupertino 2010, ISBN 978-1-60773-060-6, S. 183.
- Mike Silverman: Summary of HALT and HASS Results at an Accelerated Reliability Test Center. In: IEEE – Reliability and Maintainability Symposium Proceedings. 1998, ISBN 0-7803-4362-X, S. 30–36.
- Harry W. McLean: HALT, HASS, and HASA Explained – Accelerated Reliability Techniques. Amer Society for Quality, 2009, ISBN 978-0-87389-766-2, S. 13–14 (Revised Edition).
- Harry W. McLean: HALT, HASS, and HASA Explained – Accelerated Reliability Techniques. Amer Society for Quality, 2009, ISBN 978-0-87389-766-2, S. 15 (Revised Edition).
- Harry W. McLean: HALT, HASS, and HASA Explained – Accelerated Reliability Techniques. Amer Society for Quality, 2009, ISBN 978-0-87389-766-2, S. 15–16 (Revised Edition).
- Harry W. McLean: HALT, HASS, and HASA Explained – Accelerated Reliability Techniques. Amer Society for Quality, 2009, ISBN 978-0-87389-766-2, S. 16–17 (Revised Edition).
- Luis A. Escobar, William Q. Meeker: A Review of Accelerated Test Models. Hrsg.: Institute of Mathematical Statistics. 2. August 2007, arxiv:0708.0369.
- Wayne B. Nelson: Accelerated Testing - Statistical Models, Test Plans, and Data Analysis. John Wiley & Sons, Inc., New York 2004, ISBN 0-471-69736-2, S. 37–39.
- Arno Meyna, Bernhard Pauli: Zuverlässigkeitstechnik - Quantitative Bewertungsverfahren. 2. Auflage. Carl Hanser Verlag, München 2010, ISBN 978-3-446-41966-7, S. 588.